Cực tiểu hóa sai lệch kích thước theo phương pháp Taguchi khi phay trên trung tâm gia công CNC
Tiến sỹ G.Taguchi (Nhật Bản) đã phát triển
phương pháp thiết kế các thực nghiệm, để nghiên
cứu biện pháp xác định các thông số khác nhau ảnh
hưởng đến giá trị trung bình và phương sai (average
value and variances) của đặc tính hiệu suất quá
trình, xác định xem quá trình này hoạt động tốt như
thế nào. Thiết kế thực nghiệm bởi Taguchi đề xuất
liên quan đến việc sử dụng các ma trận trực giao để
tổ chức các thông số ảnh hưởng đến quá trình và các
mức, mà tại đó chúng sẽ được thay đổi, nó cho phép
để thu thập các dữ liệu cần thiết để xác định các yếu
tố ảnh hưởng đến hầu hết chất lượng sản phẩm với
một số lượng tối thiểu của thí nghiệm, do đó tiết
kiệm thời gian và nguồn lực. Phân tích phương sai
trên các dữ liệu thu thập được từ các thiết kế thực
nghiệm Taguchi, có thể được sử dụng để chọn các
giá trị thông số mới nhằm tối ưu hóa các đặc tính
hiệu suất.
Việc lựa chọn ma trận trực giao được thực
hiện theo phương pháp Taguchi, được lựa chọn phụ
thuộc vào số thông số nghiên cứu, các mức ảnh
hưởng của chúng và được trình bày trong Bảng 1.
Từ hàm tổn thất Taguchi, để cực tiểu hóa
hàm mục tiêu và xác định ảnh hưởng cho từng biến
ở đầu ra, giá trị tỷ lệ tín hiệu nhiễu S/N, cần phải
tính toán cho mỗi thí nghiệm theo biểu thức (4).
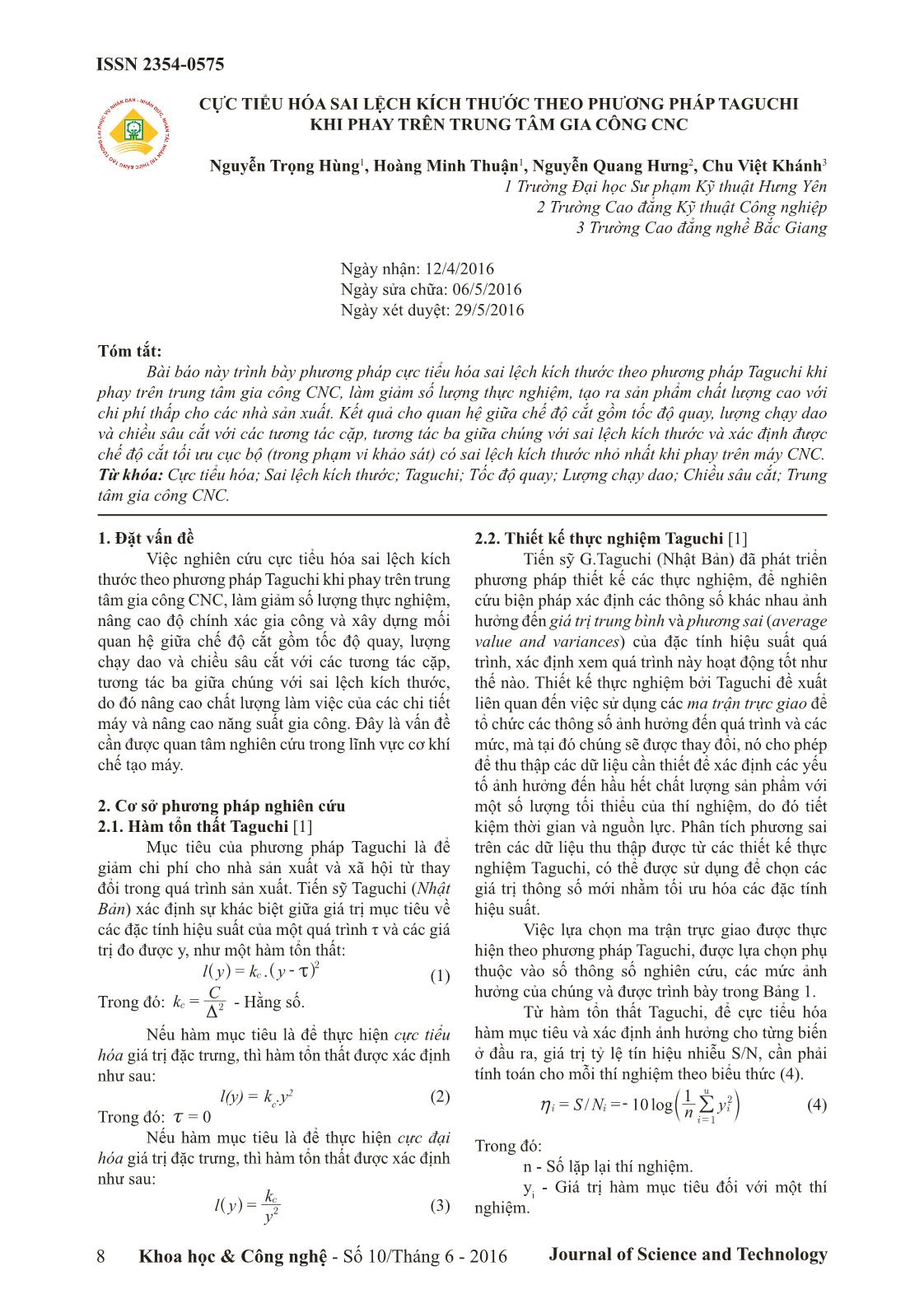
Trang 1
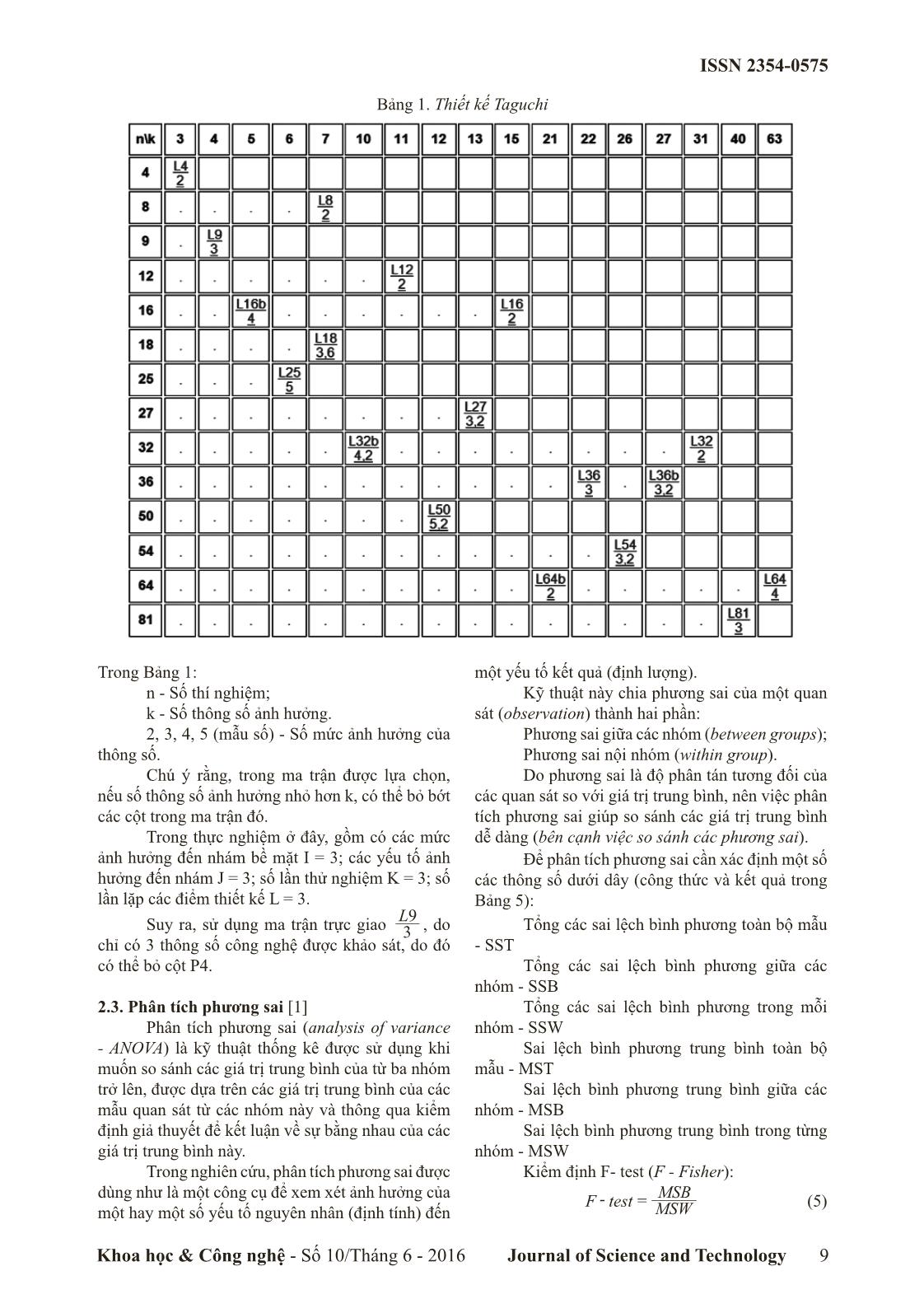
Trang 2
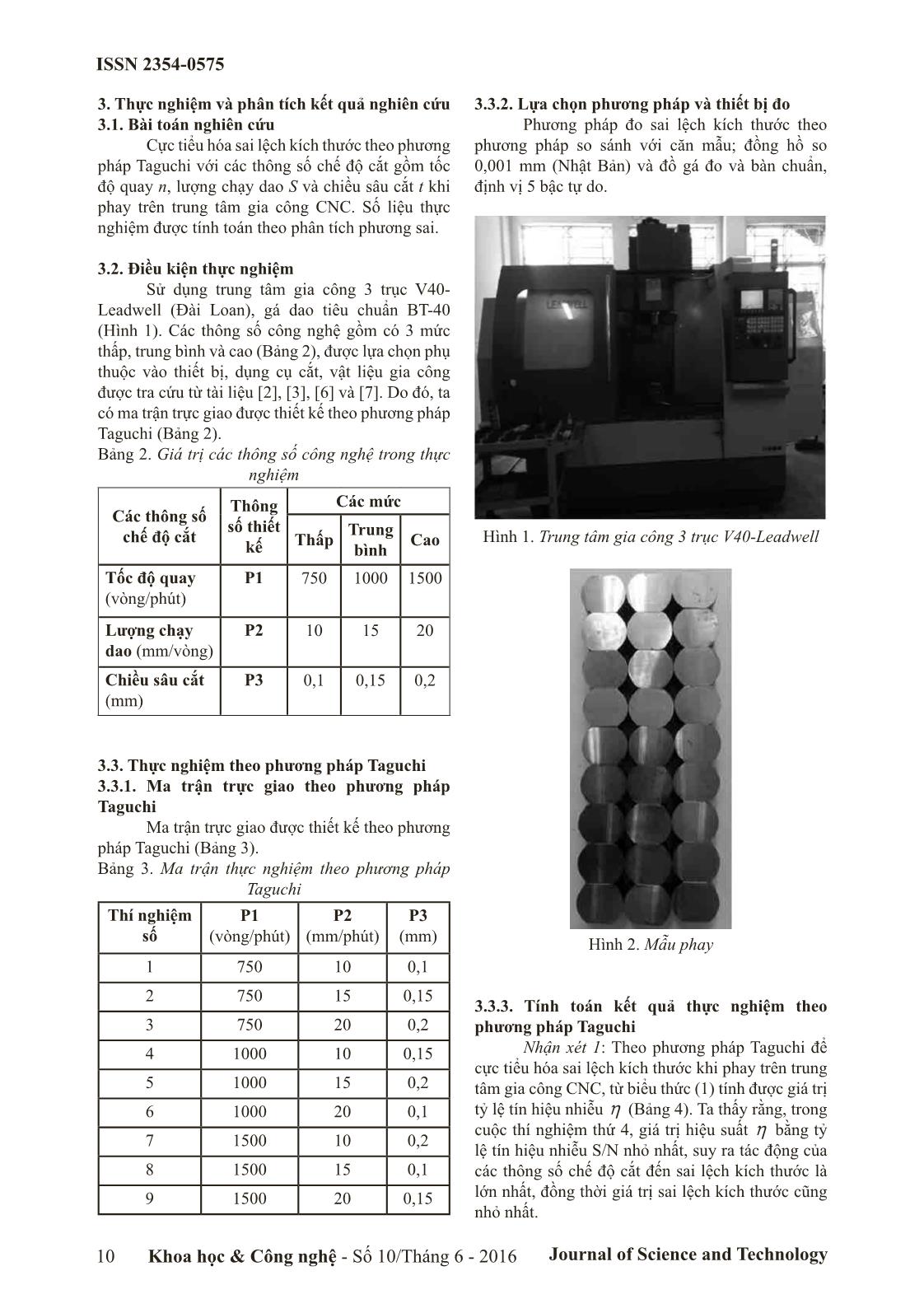
Trang 3
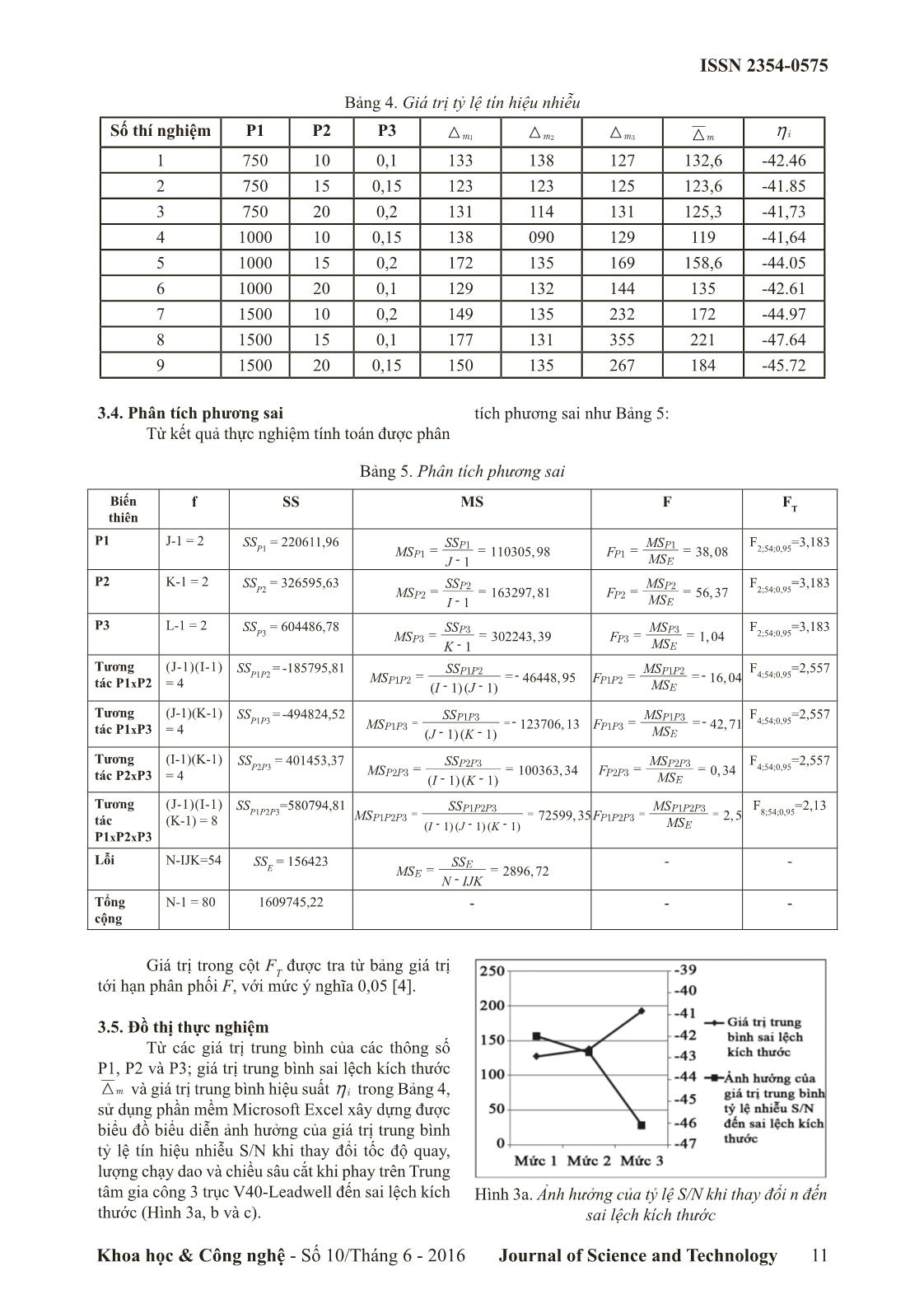
Trang 4
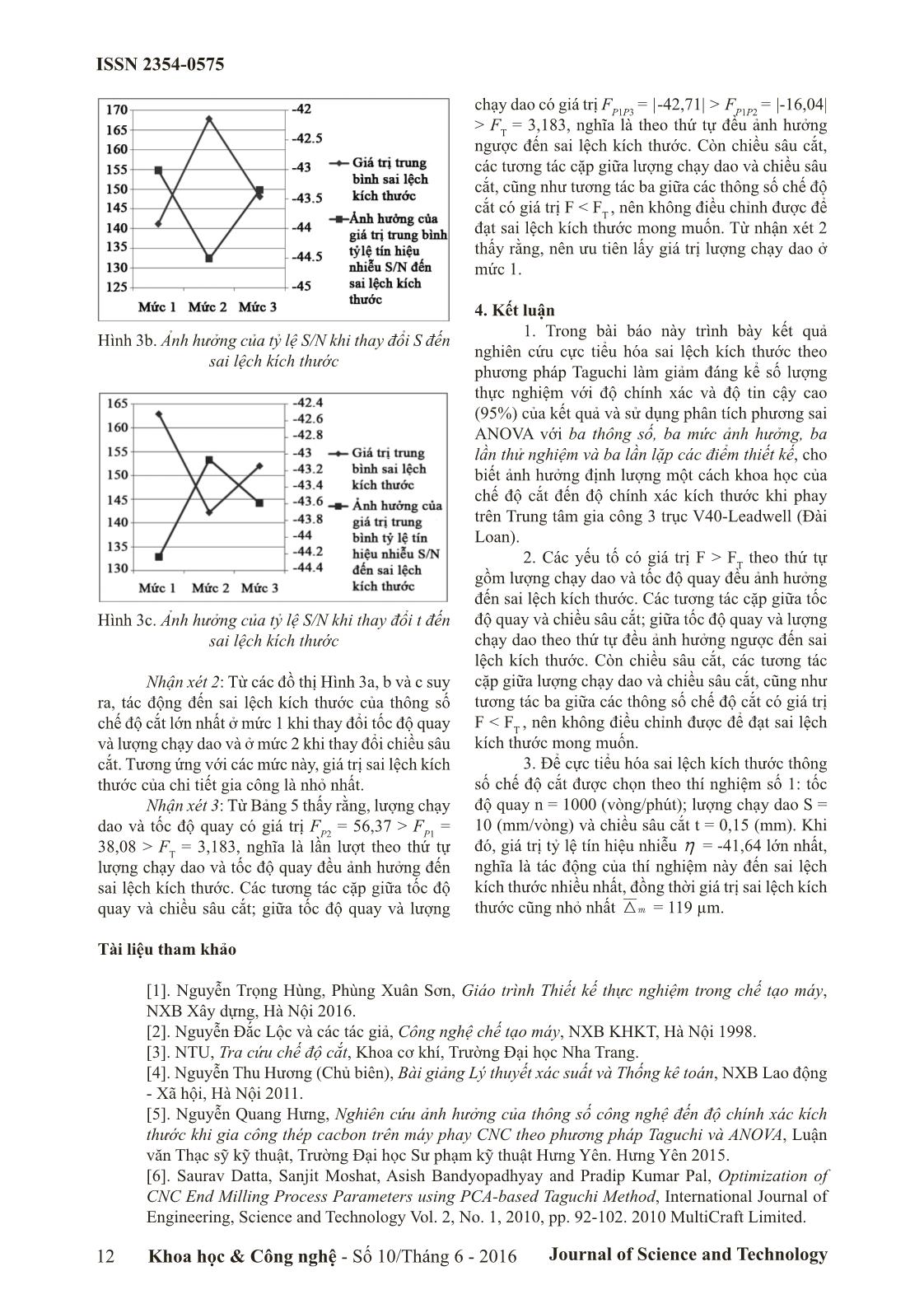
Trang 5
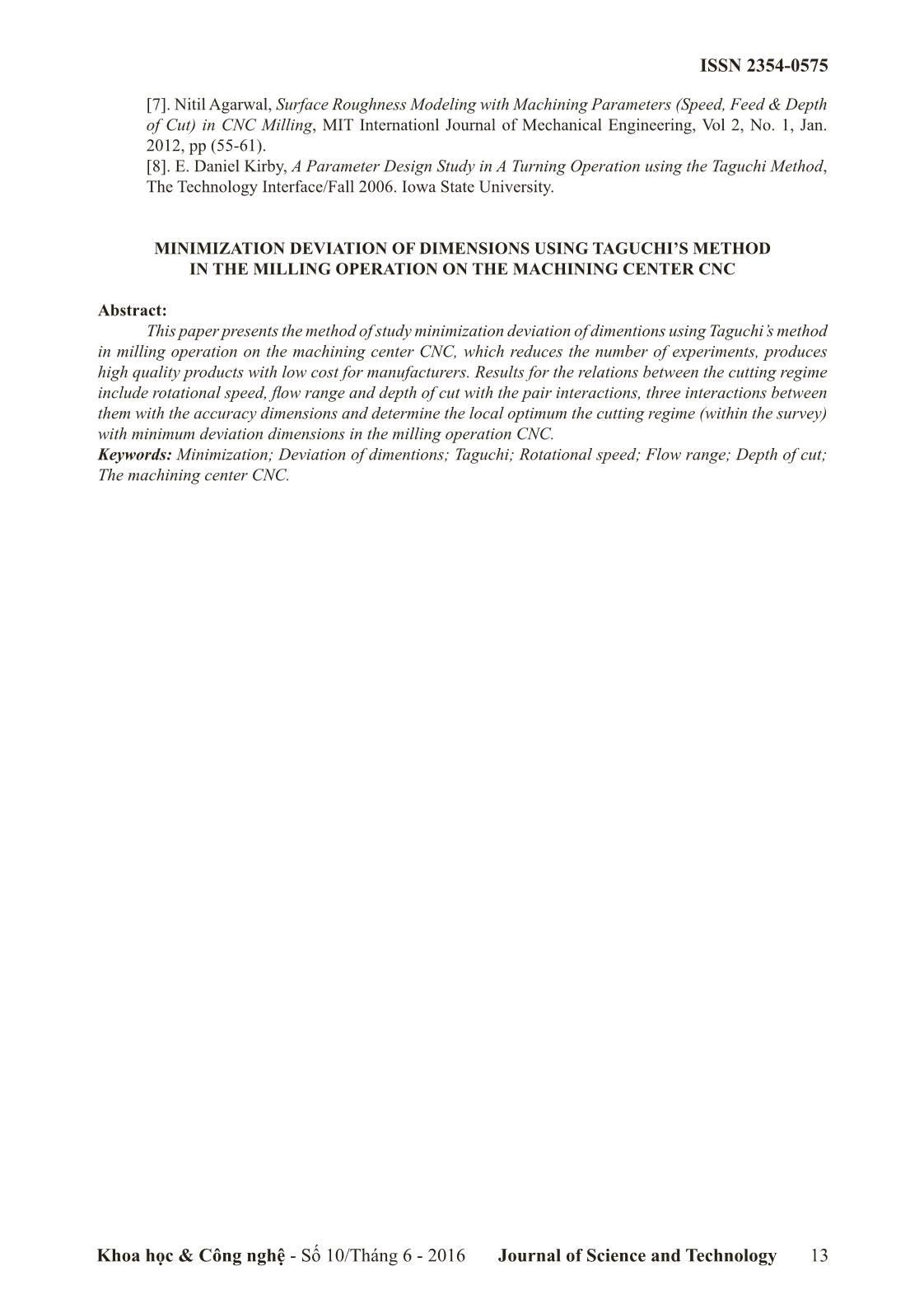
Trang 6
Tóm tắt nội dung tài liệu: Cực tiểu hóa sai lệch kích thước theo phương pháp Taguchi khi phay trên trung tâm gia công CNC
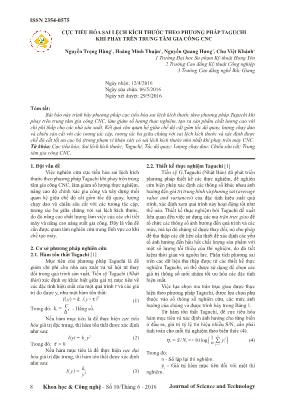
cắt gồm tốc độ quay, lượng chạy dao và chiều sâu cắt với các tương tác cặp, tương tác ba giữa chúng với sai lệch kích thước và xác định được chế độ cắt tối ưu cục bộ (trong phạm vi khảo sát) có sai lệch kích thước nhỏ nhất khi phay trên máy CNC. Từ khóa: Cực tiểu hóa; Sai lệch kích thước; Taguchi; Tốc độ quay; Lượng chạy dao; Chiều sâu cắt; Trung tâm gia công CNC. 1. Đặt vấn đề Việc nghiên cứu cực tiểu hóa sai lệch kích thước theo phương pháp Taguchi khi phay trên trung tâm gia công CNC, làm giảm số lượng thực nghiệm, nâng cao độ chính xác gia công và xây dựng mối quan hệ giữa chế độ cắt gồm tốc độ quay, lượng chạy dao và chiều sâu cắt với các tương tác cặp, tương tác ba giữa chúng với sai lệch kích thước, do đó nâng cao chất lượng làm việc của các chi tiết máy và nâng cao năng suất gia công. Đây là vấn đề cần được quan tâm nghiên cứu trong lĩnh vực cơ khí chế tạo máy. 2. Cơ sở phương pháp nghiên cứu 2.1. Hàm tổn thất Taguchi [1] Mục tiêu của phương pháp Taguchi là để giảm chi phí cho nhà sản xuất và xã hội từ thay đổi trong quá trình sản xuất. Tiến sỹ Taguchi (Nhật Bản) xác định sự khác biệt giữa giá trị mục tiêu về các đặc tính hiệu suất của một quá trình τ và các giá trị đo được y, như một hàm tổn thất: .l y k yc 2x= -^ ^h h (1) Trong đó: k Cc 2D= - Hằng số. Nếu hàm mục tiêu là để thực hiện cực tiểu hóa giá trị đặc trưng, thì hàm tổn thất được xác định như sau: l(y) = k c .y2 (2) Trong đó: 0x = Nếu hàm mục tiêu là để thực hiện cực đại hóa giá trị đặc trưng, thì hàm tổn thất được xác định như sau: l y y kc 2=^ h (3) 2.2. Thiết kế thực nghiệm Taguchi [1] Tiến sỹ G.Taguchi (Nhật Bản) đã phát triển phương pháp thiết kế các thực nghiệm, để nghiên cứu biện pháp xác định các thông số khác nhau ảnh hưởng đến giá trị trung bình và phương sai (average value and variances) của đặc tính hiệu suất quá trình, xác định xem quá trình này hoạt động tốt như thế nào. Thiết kế thực nghiệm bởi Taguchi đề xuất liên quan đến việc sử dụng các ma trận trực giao để tổ chức các thông số ảnh hưởng đến quá trình và các mức, mà tại đó chúng sẽ được thay đổi, nó cho phép để thu thập các dữ liệu cần thiết để xác định các yếu tố ảnh hưởng đến hầu hết chất lượng sản phẩm với một số lượng tối thiểu của thí nghiệm, do đó tiết kiệm thời gian và nguồn lực. Phân tích phương sai trên các dữ liệu thu thập được từ các thiết kế thực nghiệm Taguchi, có thể được sử dụng để chọn các giá trị thông số mới nhằm tối ưu hóa các đặc tính hiệu suất. Việc lựa chọn ma trận trực giao được thực hiện theo phương pháp Taguchi, được lựa chọn phụ thuộc vào số thông số nghiên cứu, các mức ảnh hưởng của chúng và được trình bày trong Bảng 1. Từ hàm tổn thất Taguchi, để cực tiểu hóa hàm mục tiêu và xác định ảnh hưởng cho từng biến ở đầu ra, giá trị tỷ lệ tín hiệu nhiễu S/N, cần phải tính toán cho mỗi thí nghiệm theo biểu thức (4). / logS N n y10 1 i i i i u 2 1 h = =- = c m/ (4) Trong đó: n - Số lặp lại thí nghiệm. yi - Giá trị hàm mục tiêu đối với một thí nghiệm. ISSN 2354-0575 Khoa học & Công nghệ - Số 10/Tháng 6 - 2016 Journal of Science and Technology 9 Bảng 1. Thiết kế Taguchi Trong Bảng 1: n - Số thí nghiệm; k - Số thông số ảnh hưởng. 2, 3, 4, 5 (mẫu số) - Số mức ảnh hưởng của thông số. Chú ý rằng, trong ma trận được lựa chọn, nếu số thông số ảnh hưởng nhỏ hơn k, có thể bỏ bớt các cột trong ma trận đó. Trong thực nghiệm ở đây, gồm có các mức ảnh hưởng đến nhám bề mặt I = 3; các yếu tố ảnh hưởng đến nhám J = 3; số lần thử nghiệm K = 3; số lần lặp các điểm thiết kế L = 3. Suy ra, sử dụng ma trận trực giao L3 9 , do chỉ có 3 thông số công nghệ được khảo sát, do đó có thể bỏ cột P4. 2.3. Phân tích phương sai [1] Phân tích phương sai (analysis of variance - ANOVA) là kỹ thuật thống kê được sử dụng khi muốn so sánh các giá trị trung bình của từ ba nhóm trở lên, được dựa trên các giá trị trung bình của các mẫu quan sát từ các nhóm này và thông qua kiểm định giả thuyết để kết luận về sự bằng nhau của các giá trị trung bình này. Trong nghiên cứu, phân tích phương sai được dùng như là một công cụ để xem xét ảnh hưởng của một hay một số yếu tố nguyên nhân (định tính) đến một yếu tố kết quả (định lượng). Kỹ thuật này chia phương sai của một quan sát (observation) thành hai phần: Phương sai giữa các nhóm (between groups); Phương sai nội nhóm (within group). Do phương sai là độ phân tán tương đối của các quan sát so với giá trị trung bình, nên việc phân tích phương sai giúp so sánh các giá trị trung bình dễ dàng (bên cạnh việc so sánh các phương sai). Để phân tích phương sai cần xác định một số các thông số dưới dây (công thức và kết quả trong Bảng 5): Tổng các sai lệch bình phương toàn bộ mẫu - SST Tổng các sai lệch bình phương giữa các nhóm - SSB Tổng các sai lệch bình phương trong mỗi nhóm - SSW Sai lệch bình phương trung bình toàn bộ mẫu - MST Sai lệch bình phương trung bình giữa các nhóm - MSB Sai lệch bình phương trung bình trong từng nhóm - MSW Kiểm định F- test (F - Fisher): F test MSW MSB- = (5) ISSN 2354-0575 Journal of Science and Technology10 Khoa học & Công nghệ - Số 10/Tháng 6 - 2016 3. Thực nghiệm và phân tích kết quả nghiên cứu 3.1. Bài toán nghiên cứu Cực tiểu hóa sai lệch kích thước theo phương pháp Taguchi với các thông số chế độ cắt gồm tốc độ quay n, lượng chạy dao S và chiều sâu cắt t khi phay trên trung tâm gia công CNC. Số liệu thực nghiệm được tính toán theo phân tích phương sai. 3.2. Điều kiện thực nghiệm Sử dụng trung tâm gia công 3 trục V40- Leadwell (Đài Loan), gá dao tiêu chuẩn BT-40 (Hình 1). Các thông số công nghệ gồm có 3 mức thấp, trung bình và cao (Bảng 2), được lựa chọn phụ thuộc vào thiết bị, dụng cụ cắt, vật liệu gia công được tra cứu từ tài liệu [2], [3], [6] và [7]. Do đó, ta có ma trận trực giao được thiết kế theo phương pháp Taguchi (Bảng 2). Bảng 2. Giá trị các thông số công nghệ trong thực nghiệm Các thông số chế độ cắt Thông số thiết kế Các mức Thấp Trung bình Cao Tốc độ quay (vòng/phút) P1 750 1000 1500 Lượng chạy dao (mm/vòng) P2 10 15 20 Chiều sâu cắt (mm) P3 0,1 0,15 0,2 3.3. Thực nghiệm theo phương pháp Taguchi 3.3.1. Ma trận trực giao theo phương pháp Taguchi Ma trận trực giao được thiết kế theo phương pháp Taguchi (Bảng 3). Bảng 3. Ma trận thực nghiệm theo phương pháp Taguchi Thí nghiệm số P1 (vòng/phút) P2 (mm/phút) P3 (mm) 1 750 10 0,1 2 750 15 0,15 3 750 20 0,2 4 1000 10 0,15 5 1000 15 0,2 6 1000 20 0,1 7 1500 10 0,2 8 1500 15 0,1 9 1500 20 0,15 3.3.2. Lựa chọn phương pháp và thiết bị đo Phương pháp đo sai lệch kích thước theo phương pháp so sánh với căn mẫu; đồng hồ so 0,001 mm (Nhật Bản) và đồ gá đo và bàn chuẩn, định vị 5 bậc tự do. Hình 1. Trung tâm gia công 3 trục V40-Leadwell Hình 2. Mẫu phay 3.3.3. Tính toán kết quả thực nghiệm theo phương pháp Taguchi Nhận xét 1: Theo phương pháp Taguchi để cực tiểu hóa sai lệch kích thước khi phay trên trung tâm gia công CNC, từ biểu thức (1) tính được giá trị tỷ lệ tín hiệu nhiễu h (Bảng 4). Ta thấy rằng, trong cuộc thí nghiệm thứ 4, giá trị hiệu suất h bằng tỷ lệ tín hiệu nhiễu S/N nhỏ nhất, suy ra tác động của các thông số chế độ cắt đến sai lệch kích thước là lớn nhất, đồng thời giá trị sai lệch kích thước cũng nhỏ nhất. ISSN 2354-0575 Khoa học & Công nghệ - Số 10/Tháng 6 - 2016 Journal of Science and Technology 11 Bảng 4. Giá trị tỷ lệ tín hiệu nhiễu Số thí nghiệm P1 P2 P3 m13 m23 m33 m3 ih 1 750 10 0,1 133 138 127 132,6 -42.46 2 750 15 0,15 123 123 125 123,6 -41.85 3 750 20 0,2 131 114 131 125,3 -41,73 4 1000 10 0,15 138 090 129 119 -41,64 5 1000 15 0,2 172 135 169 158,6 -44.05 6 1000 20 0,1 129 132 144 135 -42.61 7 1500 10 0,2 149 135 232 172 -44.97 8 1500 15 0,1 177 131 355 221 -47.64 9 1500 20 0,15 150 135 267 184 -45.72 3.4. Phân tích phương sai Từ kết quả thực nghiệm tính toán được phân tích phương sai như Bảng 5: Bảng 5. Phân tích phương sai Biến thiên f SS MS F F T P1 J-1 = 2 SSP1 = 220611,96 ,MS J SS 1 110305 98P P 1 1= - = ,F MS MS 38 08P E P 1 1= = F2;54;0,95=3,183 P2 K-1 = 2 SSP2 = 326595,63 ,MS I SS 1 163297 81P P 2 2= - = ,F MS MS 56 37P E P 2 2= = F2;54;0,95=3,183 P3 L-1 = 2 SSP3 = 604486,78 ,MS K SS 1 302243 39P P 3 3= - = ,F MS MS 1 04P E P 3 3= = F2;54;0,95=3,183 Tương tác P1xP2 (J-1)(I-1) = 4 SSP1P2 = -185795,81 ( ) ( ) ,MS I J SS 1 1 46448 95P P P P 1 2 1 2= - - = - ,F MS MS 16 04P P E P P 1 2 1 2= =- F4;54;0,95=2,557 Tương tác P1xP3 (J-1)(K-1) = 4 SSP1P3 = -494824,52 ( ) ( ) ,MS J K SS 1 1 123706 13P P P P 1 3 1 3= = - - - ,F MS MS 42 71P P E P P 1 3 1 3= =- F4;54;0,95=2,557 Tương tác P2xP3 (I-1)(K-1) = 4 SSP2P3 = 401453,37 ( ) ( ) ,MS I K SS 1 1 100363 34P P P P 2 3 2 3= - - = ,F MS MS 0 34P P E P P 2 3 2 3= = F4;54;0,95=2,557 Tương tác P1xP2xP3 (J-1)(I-1) (K-1) = 8 SSP1P2P3=580794,81 ( ) ( ) ( ) , I J K MS SS 1 1 1 72599 35P P P P P P 1 2 3 1 2 3= = - - - ,F MS MS 2 5P P P E P P P 1 2 3 1 2 3= = F 8;54;0,95 =2,13 Lỗi N-IJK=54 SSE = 156423 ,MS N IJK SS 2896 72E E= - = - - Tổng cộng N-1 = 80 1609745,22 - - - Giá trị trong cột FT được tra từ bảng giá trị tới hạn phân phối F, với mức ý nghĩa 0,05 [4]. 3.5. Đồ thị thực nghiệm Từ các giá trị trung bình của các thông số P1, P2 và P3; giá trị trung bình sai lệch kích thước m3 và giá trị trung bình hiệu suất ih trong Bảng 4, sử dụng phần mềm Microsoft Excel xây dựng được biểu đồ biểu diễn ảnh hưởng của giá trị trung bình tỷ lệ tín hiệu nhiễu S/N khi thay đổi tốc độ quay, lượng chạy dao và chiều sâu cắt khi phay trên Trung tâm gia công 3 trục V40-Leadwell đến sai lệch kích thước (Hình 3a, b và c). Hình 3a. Ảnh hưởng của tỷ lệ S/N khi thay đổi n đến sai lệch kích thước ISSN 2354-0575 Journal of Science and Technology12 Khoa học & Công nghệ - Số 10/Tháng 6 - 2016 Hình 3b. Ảnh hưởng của tỷ lệ S/N khi thay đổi S đến sai lệch kích thước Hình 3c. Ảnh hưởng của tỷ lệ S/N khi thay đổi t đến sai lệch kích thước Nhận xét 2: Từ các đồ thị Hình 3a, b và c suy ra, tác động đến sai lệch kích thước của thông số chế độ cắt lớn nhất ở mức 1 khi thay đổi tốc độ quay và lượng chạy dao và ở mức 2 khi thay đổi chiều sâu cắt. Tương ứng với các mức này, giá trị sai lệch kích thước của chi tiết gia công là nhỏ nhất. Nhận xét 3: Từ Bảng 5 thấy rằng, lượng chạy dao và tốc độ quay có giá trị FP2 = 56,37 > FP1 = 38,08 > F T = 3,183, nghĩa là lần lượt theo thứ tự lượng chạy dao và tốc độ quay đều ảnh hưởng đến sai lệch kích thước. Các tương tác cặp giữa tốc độ quay và chiều sâu cắt; giữa tốc độ quay và lượng chạy dao có giá trị FP1P3 = |-42,71| > FP1P2 = |-16,04| > F T = 3,183, nghĩa là theo thứ tự đều ảnh hưởng ngược đến sai lệch kích thước. Còn chiều sâu cắt, các tương tác cặp giữa lượng chạy dao và chiều sâu cắt, cũng như tương tác ba giữa các thông số chế độ cắt có giá trị F < F T , nên không điều chỉnh được để đạt sai lệch kích thước mong muốn. Từ nhận xét 2 thấy rằng, nên ưu tiên lấy giá trị lượng chạy dao ở mức 1. 4. Kết luận 1. Trong bài báo này trình bày kết quả nghiên cứu cực tiểu hóa sai lệch kích thước theo phương pháp Taguchi làm giảm đáng kể số lượng thực nghiệm với độ chính xác và độ tin cậy cao (95%) của kết quả và sử dụng phân tích phương sai ANOVA với ba thông số, ba mức ảnh hưởng, ba lần thử nghiệm và ba lần lặp các điểm thiết kế, cho biết ảnh hưởng định lượng một cách khoa học của chế độ cắt đến độ chính xác kích thước khi phay trên Trung tâm gia công 3 trục V40-Leadwell (Đài Loan). 2. Các yếu tố có giá trị F > F T theo thứ tự gồm lượng chạy dao và tốc độ quay đều ảnh hưởng đến sai lệch kích thước. Các tương tác cặp giữa tốc độ quay và chiều sâu cắt; giữa tốc độ quay và lượng chạy dao theo thứ tự đều ảnh hưởng ngược đến sai lệch kích thước. Còn chiều sâu cắt, các tương tác cặp giữa lượng chạy dao và chiều sâu cắt, cũng như tương tác ba giữa các thông số chế độ cắt có giá trị F < F T , nên không điều chỉnh được để đạt sai lệch kích thước mong muốn. 3. Để cực tiểu hóa sai lệch kích thước thông số chế độ cắt được chọn theo thí nghiệm số 1: tốc độ quay n = 1000 (vòng/phút); lượng chạy dao S = 10 (mm/vòng) và chiều sâu cắt t = 0,15 (mm). Khi đó, giá trị tỷ lệ tín hiệu nhiễu h = -41,64 lớn nhất, nghĩa là tác động của thí nghiệm này đến sai lệch kích thước nhiều nhất, đồng thời giá trị sai lệch kích thước cũng nhỏ nhất m3 = 119 µm. Tài liệu tham khảo [1]. Nguyễn Trọng Hùng, Phùng Xuân Sơn, Giáo trình Thiết kế thực nghiệm trong chế tạo máy, NXB Xây dựng, Hà Nội 2016. [2]. Nguyễn Đắc Lộc và các tác giả, Công nghệ chế tạo máy, NXB KHKT, Hà Nội 1998. [3]. NTU, Tra cứu chế độ cắt, Khoa cơ khí, Trường Đại học Nha Trang. [4]. Nguyễn Thu Hương (Chủ biên), Bài giảng Lý thuyết xác suất và Thống kê toán, NXB Lao động - Xã hội, Hà Nội 2011. [5]. Nguyễn Quang Hưng, Nghiên cứu ảnh hưởng của thông số công nghệ đến độ chính xác kích thước khi gia công thép cacbon trên máy phay CNC theo phương pháp Taguchi và ANOVA, Luận văn Thạc sỹ kỹ thuật, Trường Đại học Sư phạm kỹ thuật Hưng Yên. Hưng Yên 2015. [6]. Saurav Datta, Sanjit Moshat, Asish Bandyopadhyay and Pradip Kumar Pal, Optimization of CNC End Milling Process Parameters using PCA-based Taguchi Method, International Journal of Engineering, Science and Technology Vol. 2, No. 1, 2010, pp. 92-102. 2010 MultiCraft Limited. ISSN 2354-0575 Khoa học & Công nghệ - Số 10/Tháng 6 - 2016 Journal of Science and Technology 13 [7]. Nitil Agarwal, Surface Roughness Modeling with Machining Parameters (Speed, Feed & Depth of Cut) in CNC Milling, MIT Internationl Journal of Mechanical Engineering, Vol 2, No. 1, Jan. 2012, pp (55-61). [8]. E. Daniel Kirby, A Parameter Design Study in A Turning Operation using the Taguchi Method, The Technology Interface/Fall 2006. Iowa State University. MINIMIZATION DEVIATION OF DIMENSIONS USING TAGUCHI’S METHOD IN THE MILLING OPERATION ON THE MACHINING CENTER CNC Abstract: This paper presents the method of study minimization deviation of dimentions using Taguchi’s method in milling operation on the machining center CNC, which reduces the number of experiments, produces high quality products with low cost for manufacturers. Results for the relations between the cutting regime include rotational speed, flow range and depth of cut with the pair interactions, three interactions between them with the accuracy dimensions and determine the local optimum the cutting regime (within the survey) with minimum deviation dimensions in the milling operation CNC. Keywords: Minimization; Deviation of dimentions; Taguchi; Rotational speed; Flow range; Depth of cut; The machining center CNC.
File đính kèm:
cuc_tieu_hoa_sai_lech_kich_thuoc_theo_phuong_phap_taguchi_kh.pdf