Nghiên cứu xác định lượng tiến dao tối ưu khi mài phẳng hợp kim titan bằng đá mài cBN
Hợp kim Ti-6Al-4V (Ti64) là loại hợp kim titan được sử dụng phổ biến nhất
trong công nghiệp. Tuy nhiên, hợp kim này bị coi là khó gia công do nó có tỉ số độ
bền trên khối lượng riêng cao, dễ bị bám dính và phân tán nhiệt cắt kém. Trong
khi đó, đá mài cBN hay được lựa chọn để gia công các kim loại khó cắt gọt do có
năng suất cao, độ tin cậy cao, tuổi bền tốt và giảm được các khuyết tật do nhiệt.
Nghiên cứu này đánh giá về tính gia công của hợp kim Ti64 khi mài phẳng bằng
đá mài cBN kết dính nhựa độ hạt #120. Kết quả cho thấy khi tăng lượng tiến dao
hoặc chiều sâu cắt (DOC) thì độ nhám bề mặt tăng và DOC có ảnh hưởng đến
nhám nhiều hơn bước tiến dao. Nghiên cứu thực nghiệm cũng chỉ ra lượng tiến
dao tối ưu ở khoảng 3000mm/ph sẽ cho độ nhám bề mặt có giá trị nhỏ nhất
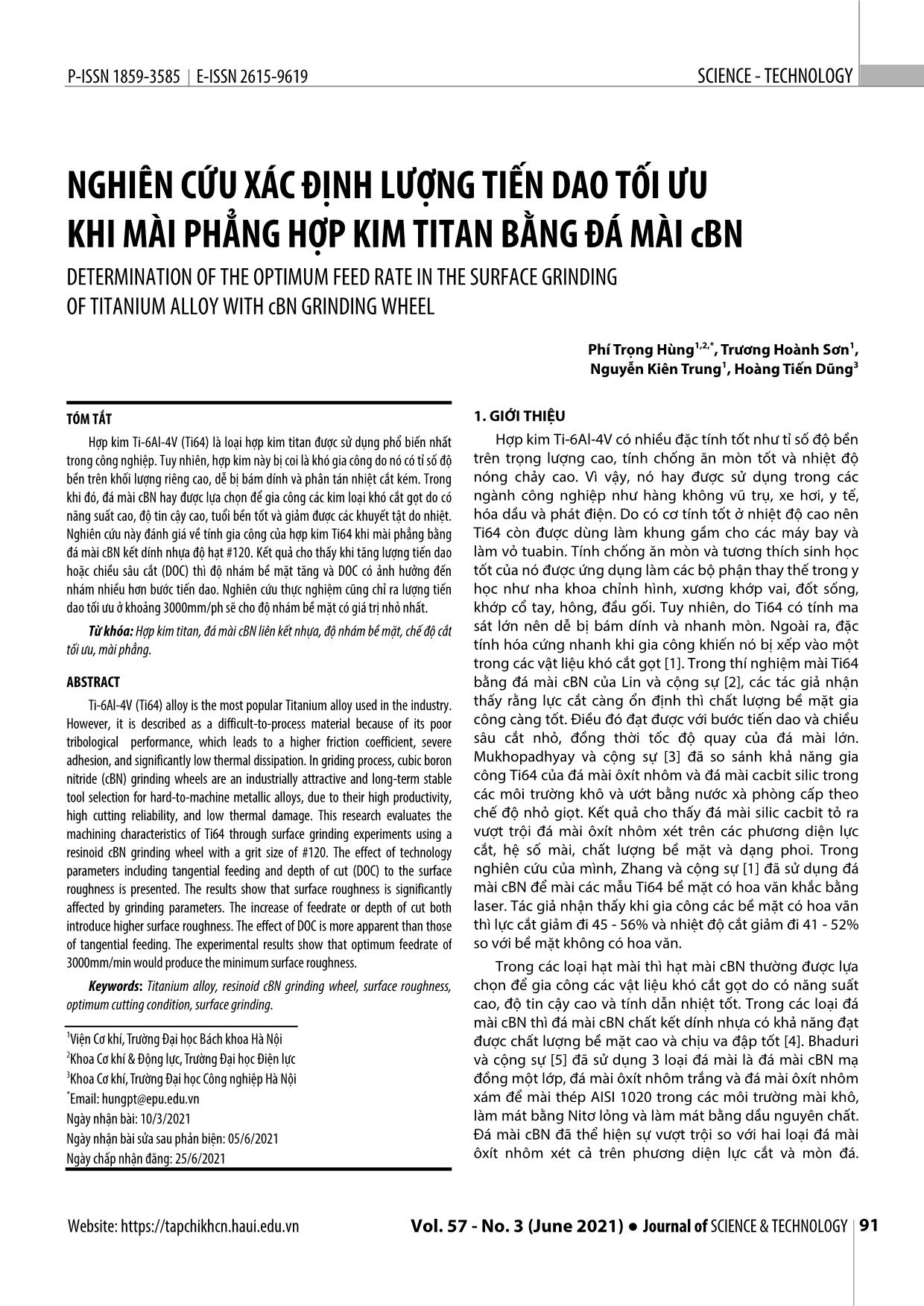
Trang 1
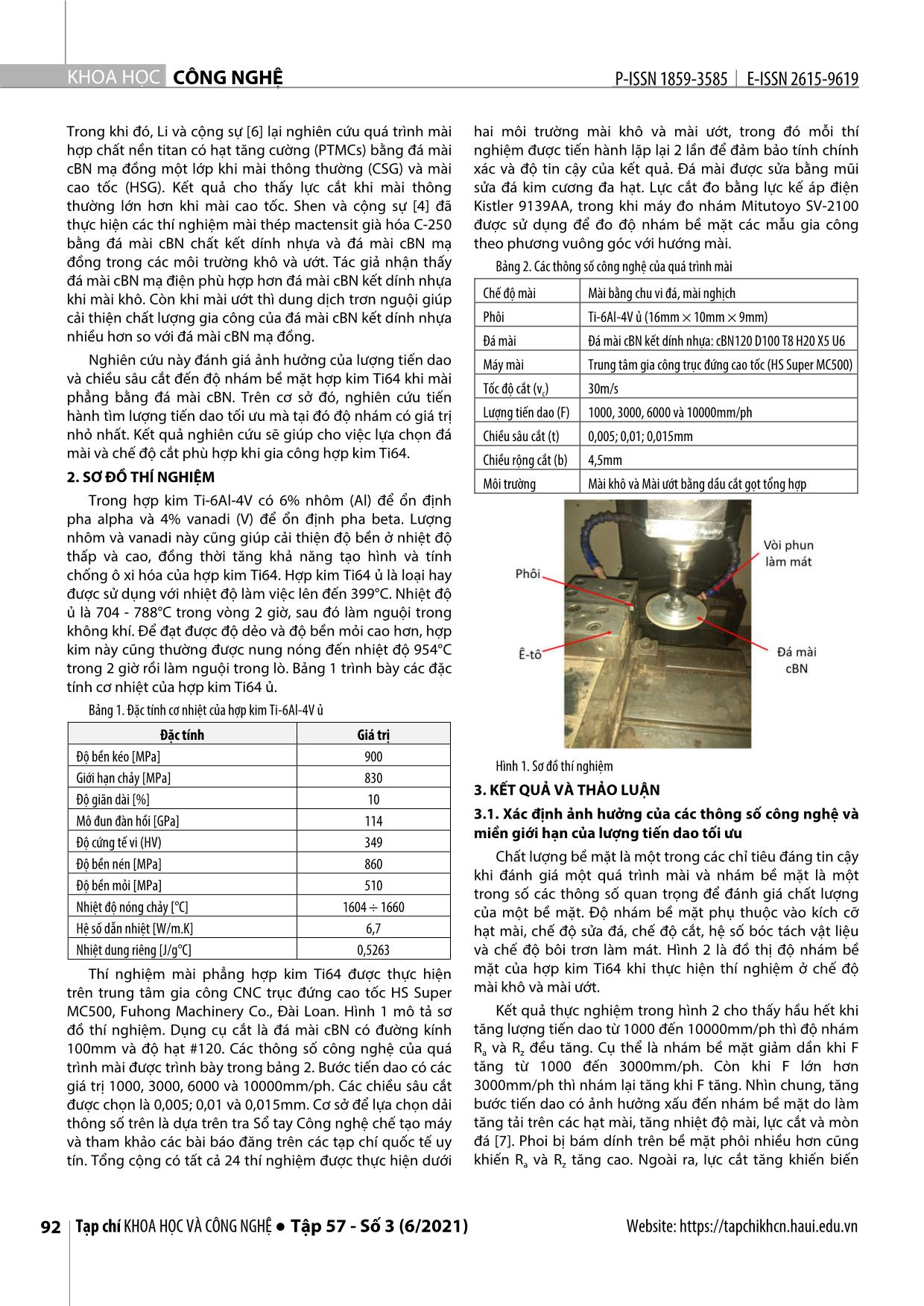
Trang 2
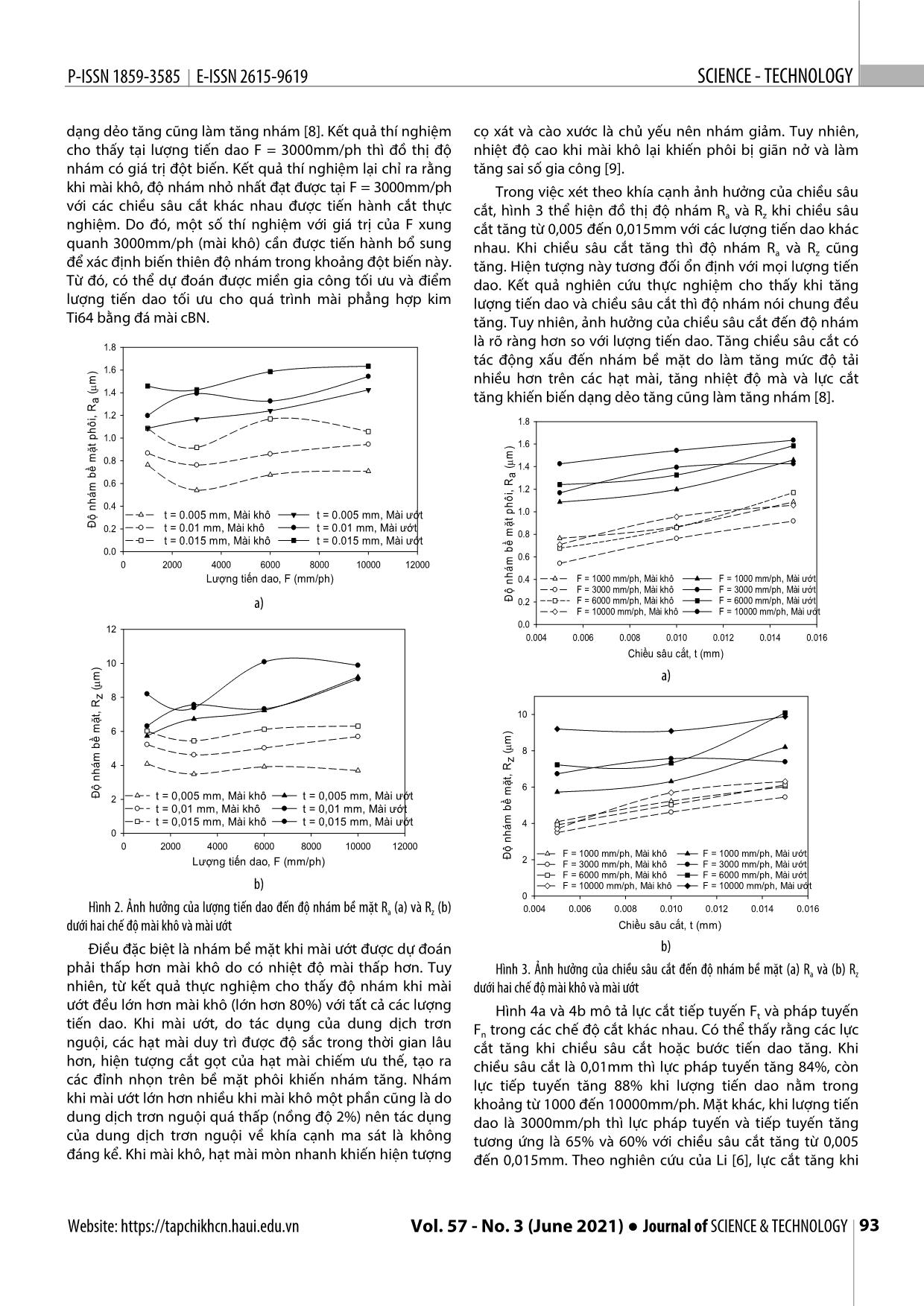
Trang 3
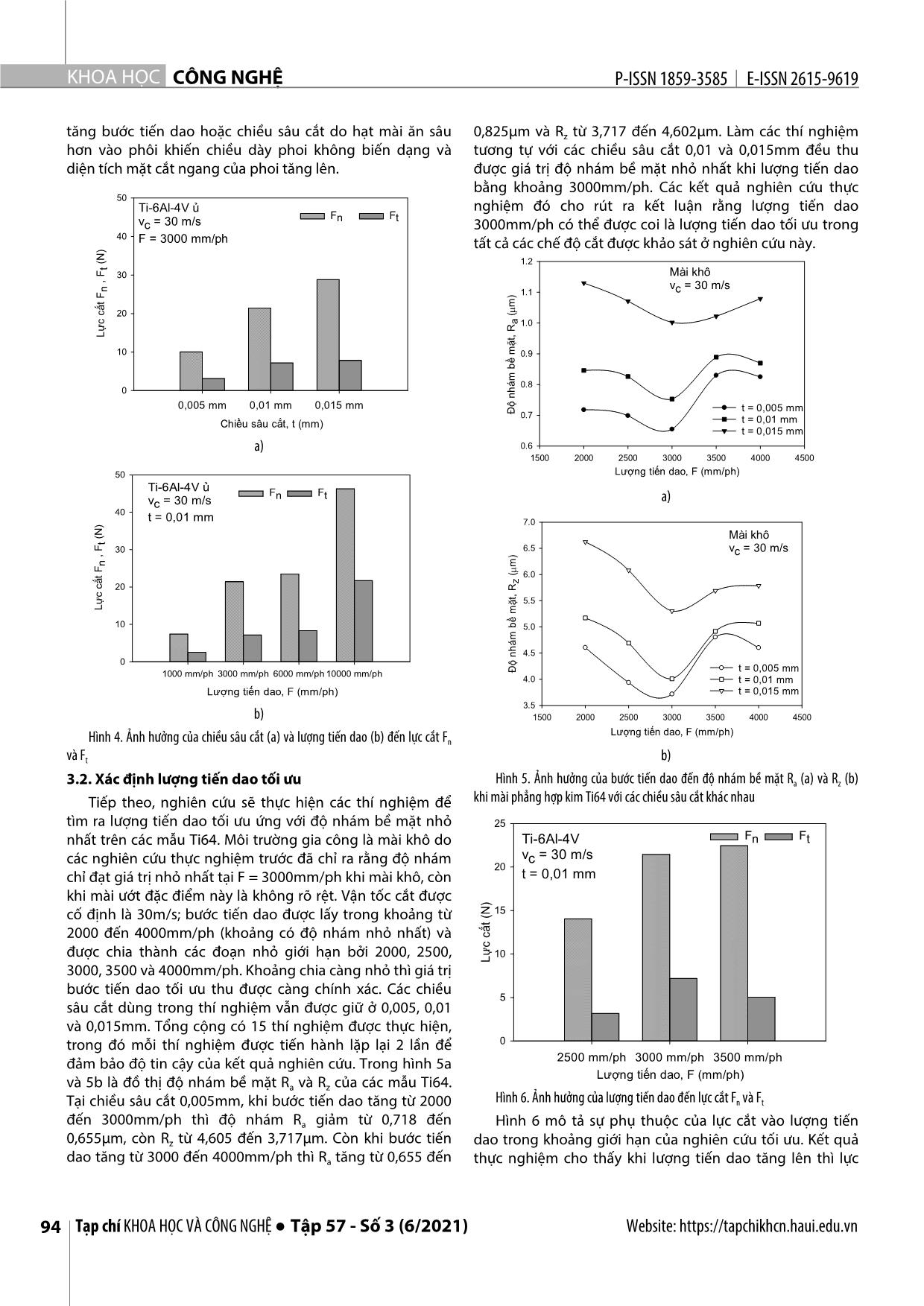
Trang 4
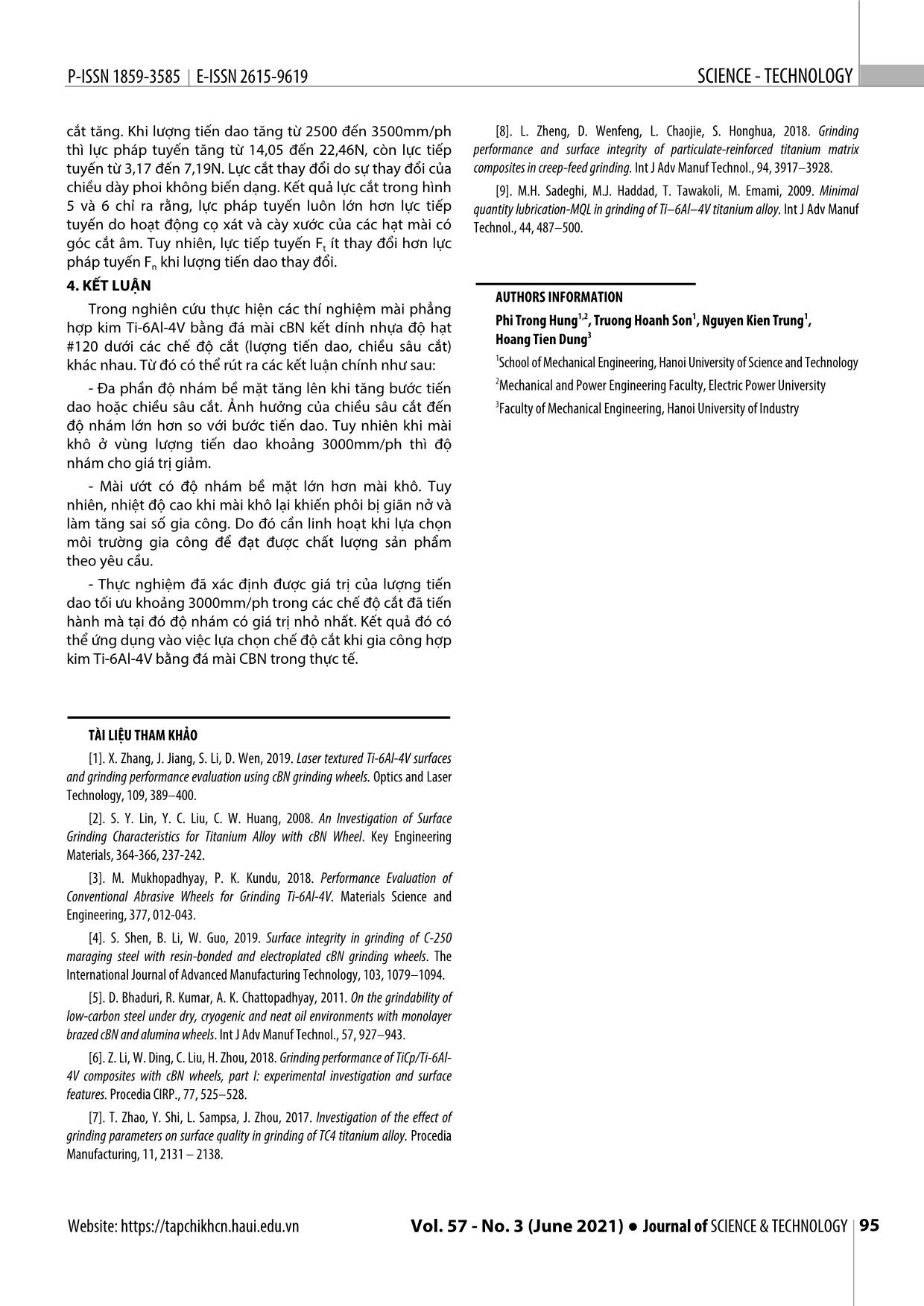
Trang 5
Tóm tắt nội dung tài liệu: Nghiên cứu xác định lượng tiến dao tối ưu khi mài phẳng hợp kim titan bằng đá mài cBN
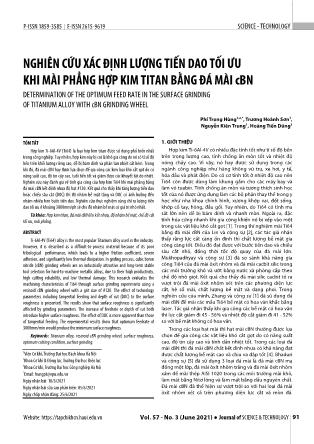
mài nghịch cải thiện chất lượng gia công của đá mài cBN kết dính nhựa Phôi Ti-6Al-4V ủ (16mm × 10mm × 9mm) nhiều hơn so với đá mài cBN mạ đồng. Đá mài Đá mài cBN kết dính nhựa: cBN120 D100 T8 H20 X5 U6 Nghiên cứu này đánh giá ảnh hưởng của lượng tiến dao Máy mài Trung tâm gia công trục đứng cao tốc (HS Super MC500) và chiều sâu cắt đến độ nhám bề mặt hợp kim Ti64 khi mài Tốc độ cắt (v ) 30m/s phẳng bằng đá mài cBN. Trên cơ sở đó, nghiên cứu tiến c hành tìm lượng tiến dao tối ưu mà tại đó độ nhám có giá trị Lượng tiến dao (F) 1000, 3000, 6000 và 10000mm/ph nhỏ nhất. Kết quả nghiên cứu sẽ giúp cho việc lựa chọn đá Chiều sâu cắt (t) 0,005; 0,01; 0,015mm mài và chế độ cắt phù hợp khi gia công hợp kim Ti64. Chiều rộng cắt (b) 4,5mm 2. SƠ ĐỒ THÍ NGHIỆM Môi trường Mài khô và Mài ướt bằng dầu cắt gọt tổng hợp Trong hợp kim Ti-6Al-4V có 6% nhôm (Al) để ổn định pha alpha và 4% vanadi (V) để ổn định pha beta. Lượng nhôm và vanadi này cũng giúp cải thiện độ bền ở nhiệt độ thấp và cao, đồng thời tăng khả năng tạo hình và tính chống ô xi hóa của hợp kim Ti64. Hợp kim Ti64 ủ là loại hay được sử dụng với nhiệt độ làm việc lên đến 399°C. Nhiệt độ ủ là 704 - 788°C trong vòng 2 giờ, sau đó làm nguội trong không khí. Để đạt được độ dẻo và độ bền mỏi cao hơn, hợp kim này cũng thường được nung nóng đến nhiệt độ 954°C trong 2 giờ rồi làm nguội trong lò. Bảng 1 trình bày các đặc tính cơ nhiệt của hợp kim Ti64 ủ. Bảng 1. Đặc tính cơ nhiệt của hợp kim Ti-6Al-4V ủ Đặc tính Giá trị Độ bền kéo [MPa] 900 Hình 1. Sơ đồ thí nghiệm Giới hạn chảy [MPa] 830 3. KẾT QUẢ VÀ THẢO LUẬN Độ giãn dài [%] 10 Mô đun đàn hồi [GPa] 114 3.1. Xác định ảnh hưởng của các thông số công nghệ và miền giới hạn của lượng tiến dao tối ưu Độ cứng tế vi (HV) 349 Độ bền nén [MPa] 860 Chất lượng bề mặt là một trong các chỉ tiêu đáng tin cậy khi đánh giá một quá trình mài và nhám bề mặt là một Độ bền mỏi [MPa] 510 trong số các thông số quan trọng để đánh giá chất lượng Nhiệt độ nóng chảy [°C] 1604 ÷ 1660 của một bề mặt. Độ nhám bề mặt phụ thuộc vào kích cỡ Hệ số dẫn nhiệt [W/m.K] 6,7 hạt mài, chế độ sửa đá, chế độ cắt, hệ số bóc tách vật liệu Nhiệt dung riêng [J/g°C] 0,5263 và chế độ bôi trơn làm mát. Hình 2 là đồ thị độ nhám bề Thí nghiệm mài phẳng hợp kim Ti64 được thực hiện mặt của hợp kim Ti64 khi thực hiện thí nghiệm ở chế độ trên trung tâm gia công CNC trục đứng cao tốc HS Super mài khô và mài ướt. MC500, Fuhong Machinery Co., Đài Loan. Hình 1 mô tả sơ Kết quả thực nghiệm trong hình 2 cho thấy hầu hết khi đồ thí nghiệm. Dụng cụ cắt là đá mài cBN có đường kính tăng lượng tiến dao từ 1000 đến 10000mm/ph thì độ nhám 100mm và độ hạt #120. Các thông số công nghệ của quá Ra và Rz đều tăng. Cụ thể là nhám bề mặt giảm dần khi F trình mài được trình bày trong bảng 2. Bước tiến dao có các tăng từ 1000 đến 3000mm/ph. Còn khi F lớn hơn giá trị 1000, 3000, 6000 và 10000mm/ph. Các chiều sâu cắt 3000mm/ph thì nhám lại tăng khi F tăng. Nhìn chung, tăng được chọn là 0,005; 0,01 và 0,015mm. Cơ sở để lựa chọn dải bước tiến dao có ảnh hưởng xấu đến nhám bề mặt do làm thông số trên là dựa trên tra Sổ tay Công nghệ chế tạo máy tăng tải trên các hạt mài, tăng nhiệt độ mài, lực cắt và mòn và tham khảo các bài báo đăng trên các tạp chí quốc tế uy đá [7]. Phoi bị bám dính trên bề mặt phôi nhiều hơn cũng tín. Tổng cộng có tất cả 24 thí nghiệm được thực hiện dưới khiến Ra và Rz tăng cao. Ngoài ra, lực cắt tăng khiến biến 92 Tạp chí KHOA HỌC VÀ CÔNG NGHỆ ● Tập 57 - Số 3 (6/2021) Website: https://tapchikhcn.haui.edu.vn P-ISSN 1859-3585 E-ISSN 2615-9619 SCIENCE - TECHNOLOGY dạng dẻo tăng cũng làm tăng nhám [8]. Kết quả thí nghiệm cọ xát và cào xước là chủ yếu nên nhám giảm. Tuy nhiên, cho thấy tại lượng tiến dao F = 3000mm/ph thì đồ thị độ nhiệt độ cao khi mài khô lại khiến phôi bị giãn nở và làm nhám có giá trị đột biến. Kết quả thí nghiệm lại chỉ ra rằng tăng sai số gia công [9]. khi mài khô, độ nhám nhỏ nhất đạt được tại F = 3000mm/ph Trong việc xét theo khía cạnh ảnh hưởng của chiều sâu với các chiều sâu cắt khác nhau được tiến hành cắt thực cắt, hình 3 thể hiện đồ thị độ nhám Ra và Rz khi chiều sâu nghiệm. Do đó, một số thí nghiệm với giá trị của F xung cắt tăng từ 0,005 đến 0,015mm với các lượng tiến dao khác quanh 3000mm/ph (mài khô) cần được tiến hành bổ sung nhau. Khi chiều sâu cắt tăng thì độ nhám Ra và Rz cũng để xác định biến thiên độ nhám trong khoảng đột biến này. tăng. Hiện tượng này tương đối ổn định với mọi lượng tiến Từ đó, có thể dự đoán được miền gia công tối ưu và điểm dao. Kết quả nghiên cứu thực nghiệm cho thấy khi tăng lượng tiến dao tối ưu cho quá trình mài phẳng hợp kim lượng tiến dao và chiều sâu cắt thì độ nhám nói chung đều Ti64 bằng đá mài cBN. tăng. Tuy nhiên, ảnh hưởng của chiều sâu cắt đến độ nhám 1.8 là rõ ràng hơn so với lượng tiến dao. Tăng chiều sâu cắt có tác động xấu đến nhám bề mặt do làm tăng mức độ tải 1.6 m) nhiều hơn trên các hạt mài, tăng nhiệt độ mà và lực cắt m ( 1.4 a tăng khiến biến dạng dẻo tăng cũng làm tăng nhám [8]. 1.2 1.8 1.0 1.6 m ) 0.8 m 1.4 ( a 0.6 1.2 0.4 t = 0.005 mm, Mài khô t = 0.005 mm, Mài ướt 1.0 Độ nhám bề mặt 0.2phôi, R t = 0.01 mm, Mài khô t = 0.01 mm, Mài ướt 0.8 t = 0.015 mm, Mài khô t = 0.015 mm, Mài ướt 0.0 0.6 0 2000 4000 6000 8000 10000 12000 Lượng tiến dao, F (mm/ph) 0.4 F = 1000 mm/ph, Mài khô F = 1000 mm/ph, Mài ướt F = 3000 mm/ph, Mài khô F = 3000 mm/ph, Mài ướt a) Độ nhám0.2 bề mặt phôi, R F = 6000 mm/ph, Mài khô F = 6000 mm/ph, Mài ướt F = 10000 mm/ph, Mài khô F = 10000 mm/ph, Mài ướt 12 0.0 0.004 0.006 0.008 0.010 0.012 0.014 0.016 Chiều sâu cắt, t (mm) 10 m) a) m ( z 8 10 6 m) m 8 ( 4 z 6 Độ nhám bề mặt, R 2 t = 0,005 mm, Mài khô t = 0,005 mm, Mài ướt t = 0,01 mm, Mài khô t = 0,01 mm, Mài ướt t = 0,015 mm, Mài khô t = 0,015 mm, Mài ướt 4 0 0 2000 4000 6000 8000 10000 12000 F = 1000 mm/ph, Mài khô F = 1000 mm/ph, Mài ướt Độ nhám bề mặt, R Lượng tiến dao, F (mm/ph) 2 F = 3000 mm/ph, Mài khô F = 3000 mm/ph, Mài ướt F = 6000 mm/ph, Mài khô F = 6000 mm/ph, Mài ướt b) F = 10000 mm/ph, Mài khô F = 10000 mm/ph, Mài ướt 0 Hình 2. Ảnh hưởng của lượng tiến dao đến độ nhám bề mặt Ra (a) và Rz (b) 0.004 0.006 0.008 0.010 0.012 0.014 0.016 dưới hai chế độ mài khô và mài ướt Chiều sâu cắt, t (mm) Điều đặc biệt là nhám bề mặt khi mài ướt được dự đoán b) phải thấp hơn mài khô do có nhiệt độ mài thấp hơn. Tuy Hình 3. Ảnh hưởng của chiều sâu cắt đến độ nhám bề mặt (a) Ra và (b) Rz nhiên, từ kết quả thực nghiệm cho thấy độ nhám khi mài dưới hai chế độ mài khô và mài ướt ướt đều lớn hơn mài khô (lớn hơn 80%) với tất cả các lượng Hình 4a và 4b mô tả lực cắt tiếp tuyến Ft và pháp tuyến tiến dao. Khi mài ướt, do tác dụng của dung dịch trơn Fn trong các chế độ cắt khác nhau. Có thể thấy rằng các lực nguội, các hạt mài duy trì được độ sắc trong thời gian lâu cắt tăng khi chiều sâu cắt hoặc bước tiến dao tăng. Khi hơn, hiện tượng cắt gọt của hạt mài chiếm ưu thế, tạo ra chiều sâu cắt là 0,01mm thì lực pháp tuyến tăng 84%, còn các đỉnh nhọn trên bề mặt phôi khiến nhám tăng. Nhám lực tiếp tuyến tăng 88% khi lượng tiến dao nằm trong khi mài ướt lớn hơn nhiều khi mài khô một phần cũng là do khoảng từ 1000 đến 10000mm/ph. Mặt khác, khi lượng tiến dung dịch trơn nguội quá thấp (nồng độ 2%) nên tác dụng dao là 3000mm/ph thì lực pháp tuyến và tiếp tuyến tăng của dung dịch trơn nguội về khía cạnh ma sát là không tương ứng là 65% và 60% với chiều sâu cắt tăng từ 0,005 đáng kể. Khi mài khô, hạt mài mòn nhanh khiến hiện tượng đến 0,015mm. Theo nghiên cứu của Li [6], lực cắt tăng khi Website: https://tapchikhcn.haui.edu.vn Vol. 57 - No. 3 (June 2021) ● Journal of SCIENCE & TECHNOLOGY 93 KHOA H ỌC CÔNG NGHỆ P-ISSN 1859-3585 E-ISSN 2615-9619 tăng bước tiến dao hoặc chiều sâu cắt do hạt mài ăn sâu 0,825µm và Rz từ 3,717 đến 4,602µm. Làm các thí nghiệm hơn vào phôi khiến chiều dày phoi không biến dạng và tương tự với các chiều sâu cắt 0,01 và 0,015mm đều thu diện tích mặt cắt ngang của phoi tăng lên. được giá trị độ nhám bề mặt nhỏ nhất khi lượng tiến dao bằng khoảng 3000mm/ph. Các kết quả nghiên cứu thực 50 Ti-6Al-4V ủ nghiệm đó cho rút ra kết luận rằng lượng tiến dao Fn Ft vc = 30 m/s 3000mm/ph có thể được coi là lượng tiến dao tối ưu trong 40 F = 3000 mm/ph tất cả các chế độ cắt được khảo sát ở nghiên cứu này. 1.2 (N) t 30 Mài khô , F v = 30 m/s n 1.1 c m) 20 m ( a 1.0 Lực cắt F 10 0.9 0.8 0 0,005 mm 0,01 mm 0,015 mm t = 0,005 mm Độ nhámĐộ bề mặt, R 0.7 Chiều sâu cắt, t (mm) t = 0,01 mm t = 0,015 mm a) 0.6 1500 2000 2500 3000 3500 4000 4500 50 Lượng tiến dao, F (mm/ph) Ti-6Al-4V ủ Fn Ft vc = 30 m/s a) 40 t = 0,01 mm 7.0 Mài khô (N) t 30 6.5 vc = 30 m/s , F n m) m ( 6.0 20 z 5.5 Lực cắt F cắt Lực 10 5.0 4.5 0 Độ nhám bề mặt, R t = 0,005 mm 1000 mm/ph 3000 mm/ph 6000 mm/ph 10000 mm/ph 4.0 t = 0,01 mm Lượng tiến dao, F (mm/ph) t = 0,015 mm 3.5 b) 1500 2000 2500 3000 3500 4000 4500 Lượng tiến dao, F (mm/ph) Hình 4. Ảnh hưởng của chiều sâu cắt (a) và lượng tiến dao (b) đến lực cắt Fn và Ft b) 3.2. Xác định lượng tiến dao tối ưu Hình 5. Ảnh hưởng của bước tiến dao đến độ nhám bề mặt Ra (a) và Rz (b) Tiếp theo, nghiên cứu sẽ thực hiện các thí nghiệm để khi mài phẳng hợp kim Ti64 với các chiều sâu cắt khác nhau tìm ra lượng tiến dao tối ưu ứng với độ nhám bề mặt nhỏ 25 nhất trên các mẫu Ti64. Môi trường gia công là mài khô do Ti-6Al-4V Fn Ft các nghiên cứu thực nghiệm trước đã chỉ ra rằng độ nhám vc = 30 m/s 20 chỉ đạt giá trị nhỏ nhất tại F = 3000mm/ph khi mài khô, còn t = 0,01 mm khi mài ướt đặc điểm này là không rõ rệt. Vận tốc cắt được cố định là 30m/s; bước tiến dao được lấy trong khoảng từ 15 2000 đến 4000mm/ph (khoảng có độ nhám nhỏ nhất) và được chia thành các đoạn nhỏ giới hạn bởi 2000, 2500, 10 Lực (N) cắt 3000, 3500 và 4000mm/ph. Khoảng chia càng nhỏ thì giá trị bước tiến dao tối ưu thu được càng chính xác. Các chiều 5 sâu cắt dùng trong thí nghiệm vẫn được giữ ở 0,005, 0,01 và 0,015mm. Tổng cộng có 15 thí nghiệm được thực hiện, trong đó mỗi thí nghiệm được tiến hành lặp lại 2 lần để 0 đảm bảo độ tin cậy của kết quả nghiên cứu. Trong hình 5a 2500 mm/ph 3000 mm/ph 3500 mm/ph Lượng tiến dao, F (mm/ph) và 5b là đồ thị độ nhám bề mặt Ra và Rz của các mẫu Ti64. Tại chiều sâu cắt 0,005mm, khi bước tiến dao tăng từ 2000 Hình 6. Ảnh hưởng của lượng tiến dao đến lực cắt Fn và Ft đến 3000mm/ph thì độ nhám Ra giảm từ 0,718 đến Hình 6 mô tả sự phụ thuộc của lực cắt vào lượng tiến 0,655µm, còn Rz từ 4,605 đến 3,717µm. Còn khi bước tiến dao trong khoảng giới hạn của nghiên cứu tối ưu. Kết quả dao tăng từ 3000 đến 4000mm/ph thì Ra tăng từ 0,655 đến thực nghiệm cho thấy khi lượng tiến dao tăng lên thì lực 94 Tạp chí KHOA HỌC VÀ CÔNG NGHỆ ● Tập 57 - Số 3 (6/2021) Website: https://tapchikhcn.haui.edu.vn P-ISSN 1859-3585 E-ISSN 2615-9619 SCIENCE - TECHNOLOGY cắt tăng. Khi lượng tiến dao tăng từ 2500 đến 3500mm/ph [8]. L. Zheng, D. Wenfeng, L. Chaojie, S. Honghua, 2018. Grinding thì lực pháp tuyến tăng từ 14,05 đến 22,46N, còn lực tiếp performance and surface integrity of particulate-reinforced titanium matrix tuyến từ 3,17 đến 7,19N. Lực cắt thay đổi do sự thay đổi của composites in creep-feed grinding. Int J Adv Manuf Technol., 94, 3917–3928. chiều dày phoi không biến dạng. Kết quả lực cắt trong hình [9]. M.H. Sadeghi, M.J. Haddad, T. Tawakoli, M. Emami, 2009. Minimal 5 và 6 chỉ ra rằng, lực pháp tuyến luôn lớn hơn lực tiếp quantity lubrication-MQL in grinding of Ti–6Al–4V titanium alloy. Int J Adv Manuf tuyến do hoạt động cọ xát và cày xước của các hạt mài có Technol., 44, 487–500. góc cắt âm. Tuy nhiên, lực tiếp tuyến Ft ít thay đổi hơn lực pháp tuyến F khi lượng tiến dao thay đổi. n 4. KẾT LUẬN AUTHORS INFORMATION Trong nghiên cứu thực hiện các thí nghiệm mài phẳng Phi Trong Hung1,2, Truong Hoanh Son1, Nguyen Kien Trung1, hợp kim Ti-6Al-4V bằng đá mài cBN kết dính nhựa độ hạt 3 #120 dưới các chế độ cắt (lượng tiến dao, chiều sâu cắt) Hoang Tien Dung khác nhau. Từ đó có thể rút ra các kết luận chính như sau: 1School of Mechanical Engineering, Hanoi University of Science and Technology 2 - Đa phần độ nhám bề mặt tăng lên khi tăng bước tiến Mechanical and Power Engineering Faculty, Electric Power University dao hoặc chiều sâu cắt. Ảnh hưởng của chiều sâu cắt đến 3Faculty of Mechanical Engineering, Hanoi University of Industry độ nhám lớn hơn so với bước tiến dao. Tuy nhiên khi mài khô ở vùng lượng tiến dao khoảng 3000mm/ph thì độ nhám cho giá trị giảm. - Mài ướt có độ nhám bề mặt lớn hơn mài khô. Tuy nhiên, nhiệt độ cao khi mài khô lại khiến phôi bị giãn nở và làm tăng sai số gia công. Do đó cần linh hoạt khi lựa chọn môi trường gia công để đạt được chất lượng sản phẩm theo yêu cầu. - Thực nghiệm đã xác định được giá trị của lượng tiến dao tối ưu khoảng 3000mm/ph trong các chế độ cắt đã tiến hành mà tại đó độ nhám có giá trị nhỏ nhất. Kết quả đó có thể ứng dụng vào việc lựa chọn chế độ cắt khi gia công hợp kim Ti-6Al-4V bằng đá mài CBN trong thực tế. TÀI LIỆU THAM KHẢO [1]. X. Zhang, J. Jiang, S. Li, D. Wen, 2019. Laser textured Ti-6Al-4V surfaces and grinding performance evaluation using cBN grinding wheels. Optics and Laser Technology, 109, 389–400. [2]. S. Y. Lin, Y. C. Liu, C. W. Huang, 2008. An Investigation of Surface Grinding Characteristics for Titanium Alloy with cBN Wheel. Key Engineering Materials, 364-366, 237-242. [3]. M. Mukhopadhyay, P. K. Kundu, 2018. Performance Evaluation of Conventional Abrasive Wheels for Grinding Ti-6Al-4V. Materials Science and Engineering, 377, 012-043. [4]. S. Shen, B. Li, W. Guo, 2019. Surface integrity in grinding of C-250 maraging steel with resin-bonded and electroplated cBN grinding wheels. The International Journal of Advanced Manufacturing Technology, 103, 1079–1094. [5]. D. Bhaduri, R. Kumar, A. K. Chattopadhyay, 2011. On the grindability of low-carbon steel under dry, cryogenic and neat oil environments with monolayer brazed cBN and alumina wheels. Int J Adv Manuf Technol., 57, 927–943. [6]. Z. Li, W. Ding, C. Liu, H. Zhou, 2018. Grinding performance of TiCp/Ti-6Al- 4V composites with cBN wheels, part I: experimental investigation and surface features. Procedia CIRP., 77, 525–528. [7]. T. Zhao, Y. Shi, L. Sampsa, J. Zhou, 2017. Investigation of the effect of grinding parameters on surface quality in grinding of TC4 titanium alloy. Procedia Manufacturing, 11, 2131 – 2138. Website: https://tapchikhcn.haui.edu.vn Vol. 57 - No. 3 (June 2021) ● Journal of SCIENCE & TECHNOLOGY 95
File đính kèm:
nghien_cuu_xac_dinh_luong_tien_dao_toi_uu_khi_mai_phang_hop.pdf