Giáo trình Nghề Tiện
1. Tiện trục trơn ngắn.
1.1. Khái niệm về những chi tiết có mặt trụ ngoài.
- Các chi tiết máy như trục, bánh răng, chốt, píttông đều có mặt ngoài
là mặt trụ.
- Mặt ngoài được tạo bởi một đường thẳng quay quanh một đường tâm
cố định song song với nó. Vì vậy, muốn tiện được chi tiết mặt trụ ngoài
chi tiết phải quay tròn, dao chuyển động tịnh tiến song song với đường
tâm chi tiết.
- Công việc tiện ngoài là tiến hành bóc đi những lớp kim loại ở xung
quanh vật gia công để đạt được những kích thước, hình dáng theo đúng
yêu cầu bản vẽ.
Hình 2.1.1: Các bề mặt trụ ngoài
1.2. Yêu cầu đối với mặt trụ ngoài.
- Độ thẳng của đường sinh.
- Độ hình trụ : Mọi tiết diện cắt vuông góc với đường tâm phải bằng nhau (không có
hình côn, tang trống hay yên ngựa).
- Độ tròn : Các tiết diện cắt vuông góc với đường tâm phải có độ tròn xoay (không
bị ô van, không có cạnh).
- Độ đồng tâm : Trục của tất cả các bậc của chi tiết bậc nằm trong một đường thẳng
chung.
Hình 2.1.2: Các dạng bề mặt sai hỏng của bề mặt trụ ngoài
a. Hình trụ b. Trục trơn c. Trục bậc
D d
a. Mặt côn
D d
b. Mặt yên ngựa
d D
c. Mặt tang trống
d. Hình ô van
d. Hình nhiều cạnh
a- Trong thực tế, không thể có những chi tiết mặt ngoài là hình trụ tuyệt đối vì trong
quá trình gia công sẽ có những sai lệch xảy ra. Sai lệch cho phép về hình dáng hình
học, vị trí tương quan giữa các bề mặt chi tiết được ghi trên bản vẽ bằng ký hiệu hoặc
ghi chú.
Ví dụ : Độ côn cho phép trên chiều dài 100 mm là 0,05.
1.3. Phương pháp tiện trục trơn ngắn.
1.3.1. Dao tiện trụ ngoài.
- Dao tiện thô có thể là dao đầu thẳng và dao đầu cong, các dao này không chỉ để
tiện ngoài mà còn dùng để khoả mặt đầu của chi tiết.
- Dao tiện thô có góc = 30 60o, 1 = 10 30o.
Góc nhỏ dùng để gia công vật có độ cứng vững cao L/D 5.
- Dao vai có góc = 90o được dùng để gia công phôi kém cứng vững L/D > 12. Vì
dao này có lực uốn phôi nhỏ, chiều dài tham gia cắt gọt ít, nhiệt tập trung ở mũi dao,
tuổi thọ của dao kém hơn dao có góc = 60o.
- Để gia công thô, mũi dao mài bán kính R = 0,5 - 1 mm
Gia công bán tinh R = 1,5 - 2 mm
Gia công tinh R = 3 - 5 mm
R càng lớn, độ bóng càng cao, dao hợp kim cứng để gia công gang, lưỡi cắt được mài
sắc, còn gia công thép được mài vát 1 giải hẹp. Tiện tinh người ta có thể dùng dao có
lưỡi rộng (chiều rộng lưỡi cắt lớn hơn bước tiến của dao).
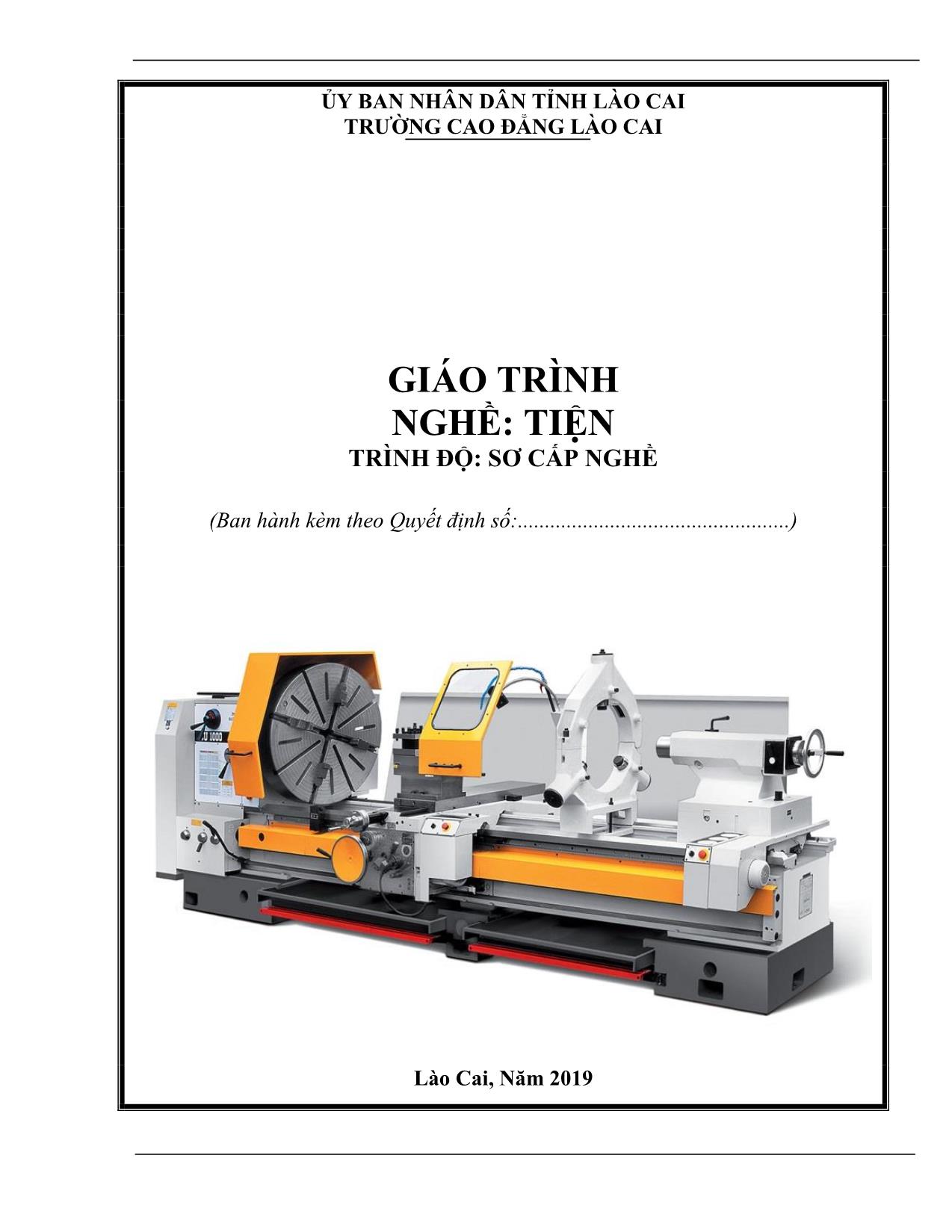
Trang 1
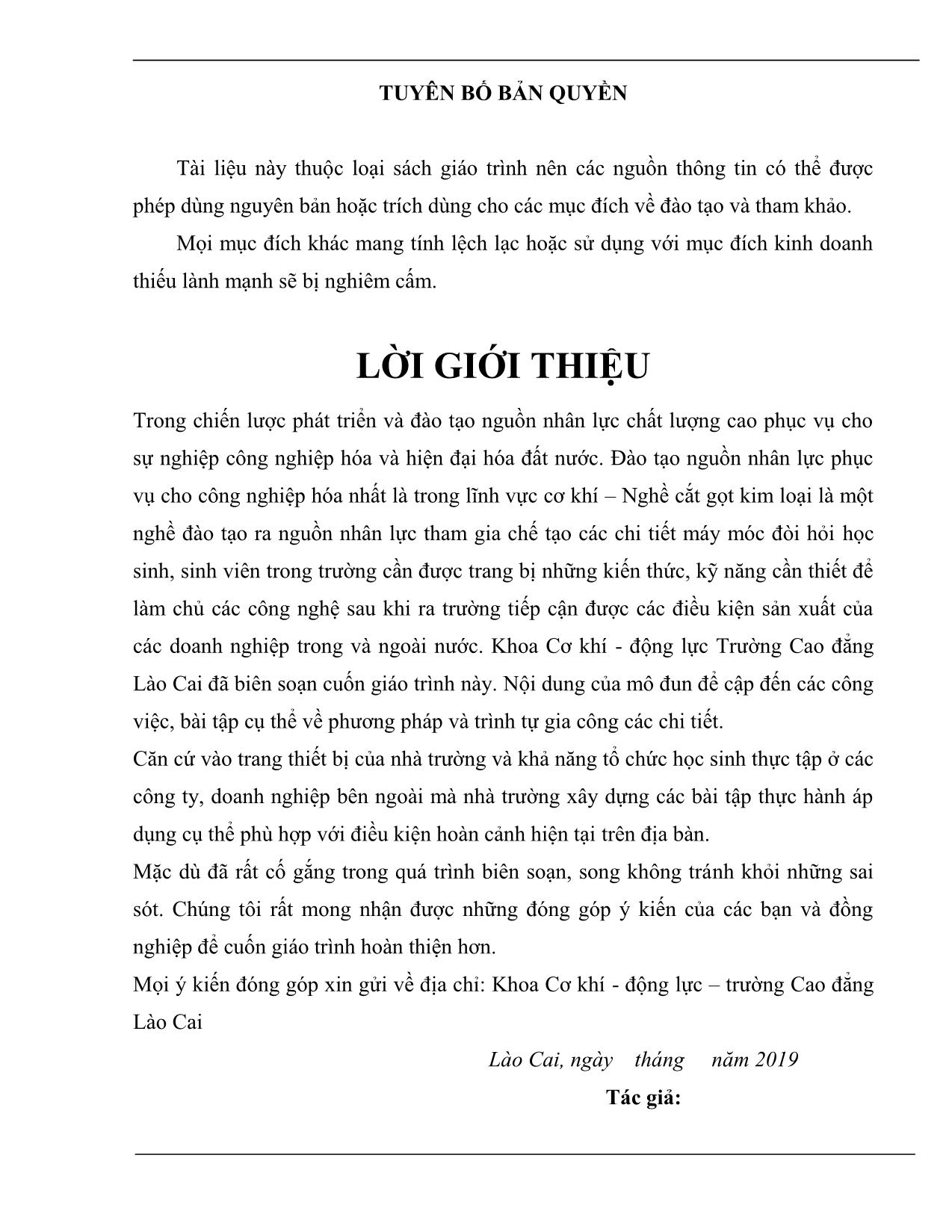
Trang 2
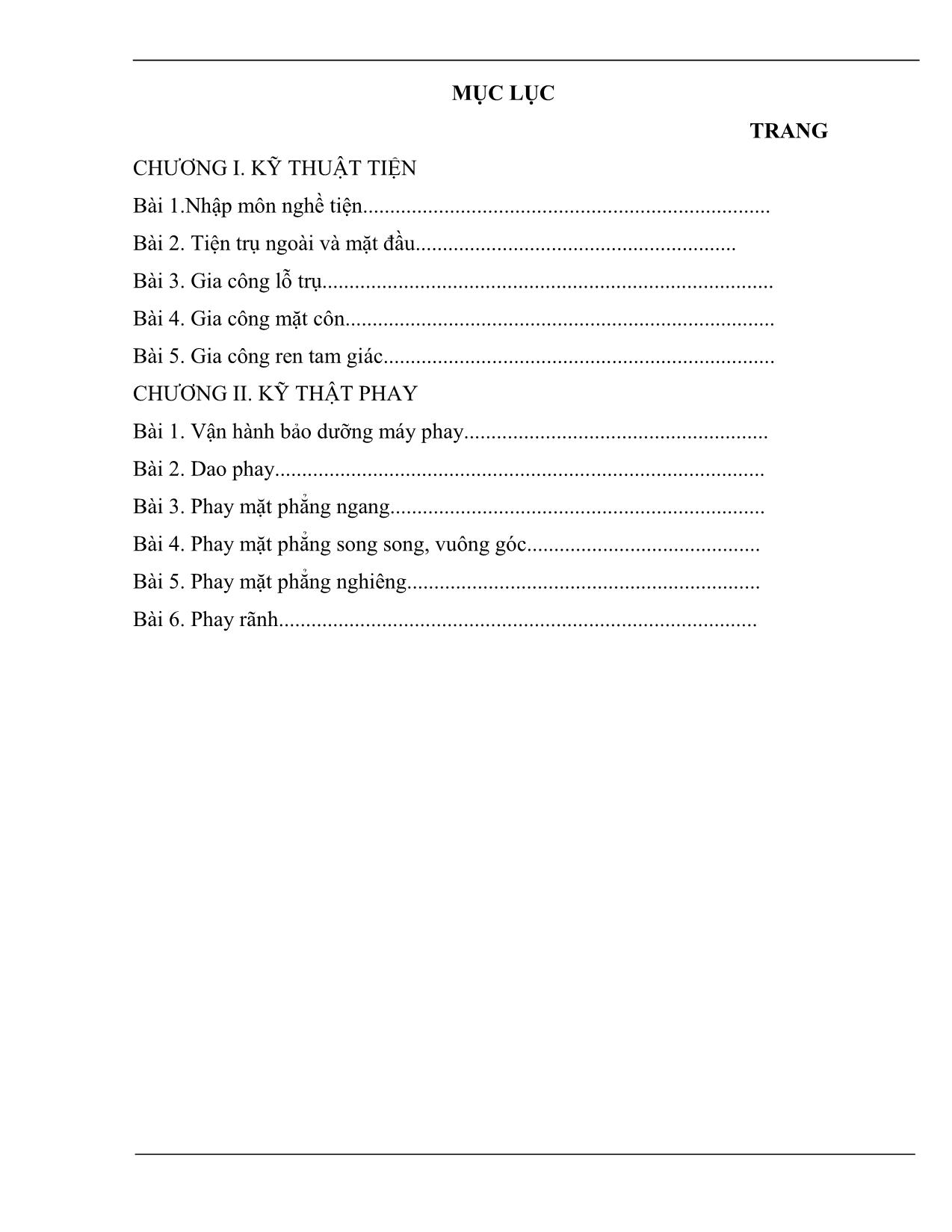
Trang 3
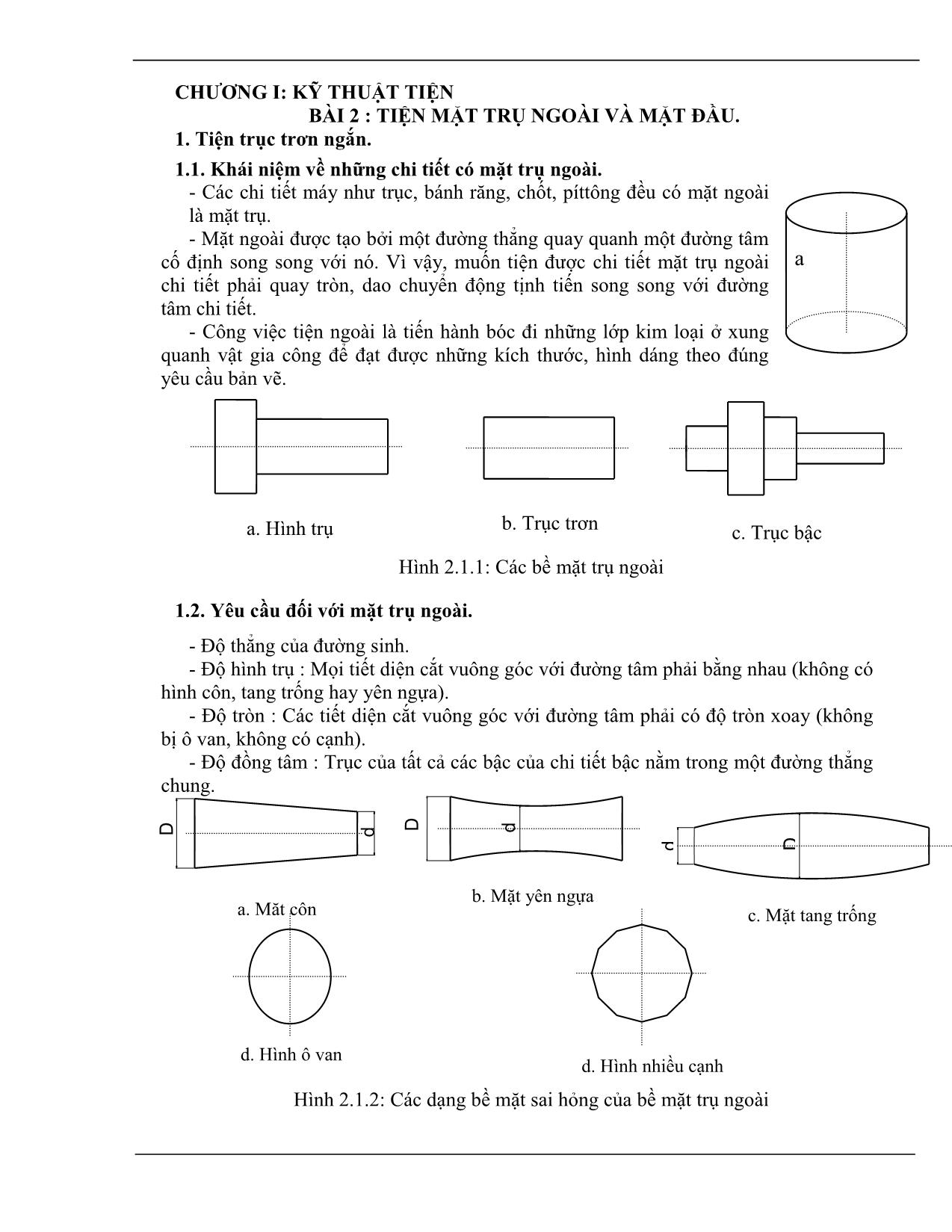
Trang 4
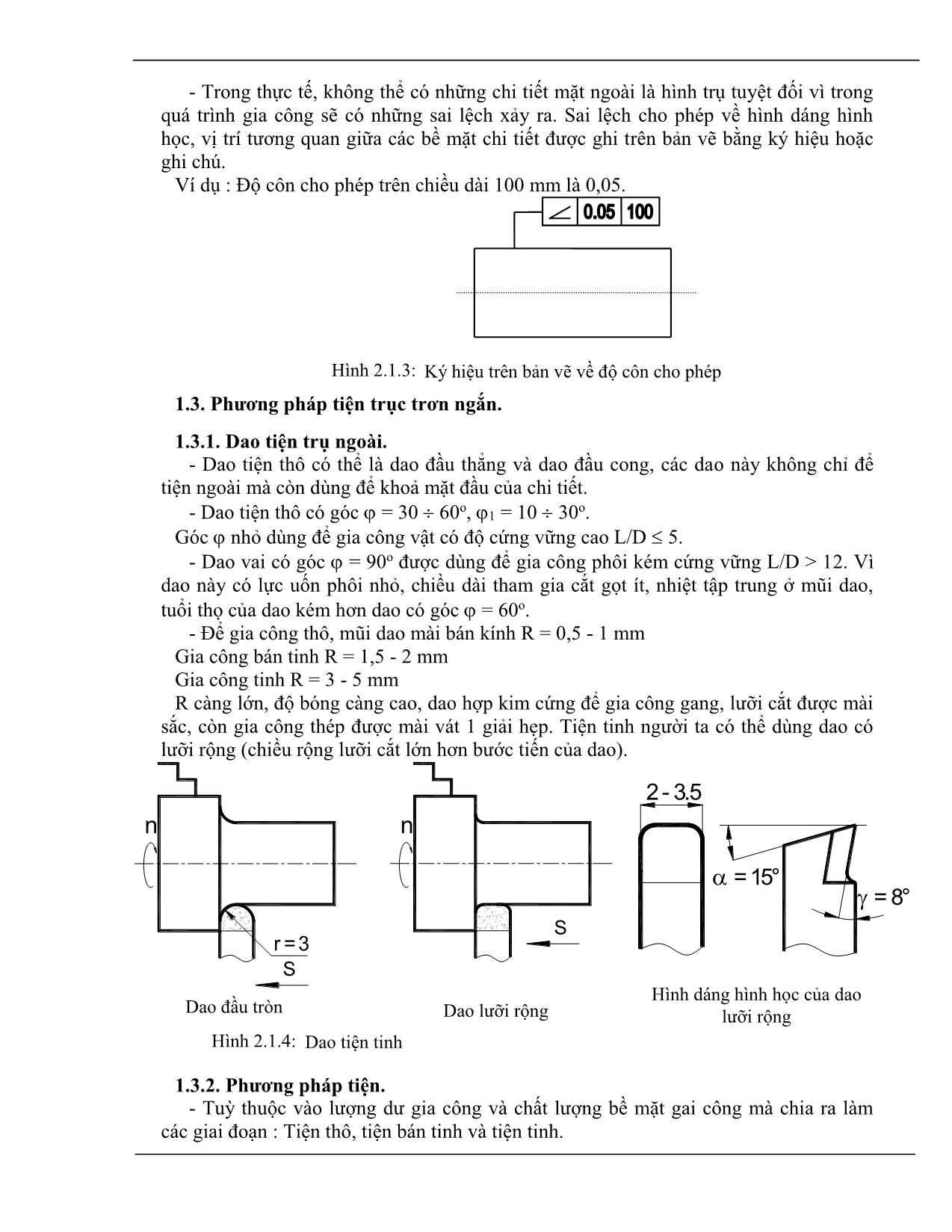
Trang 5
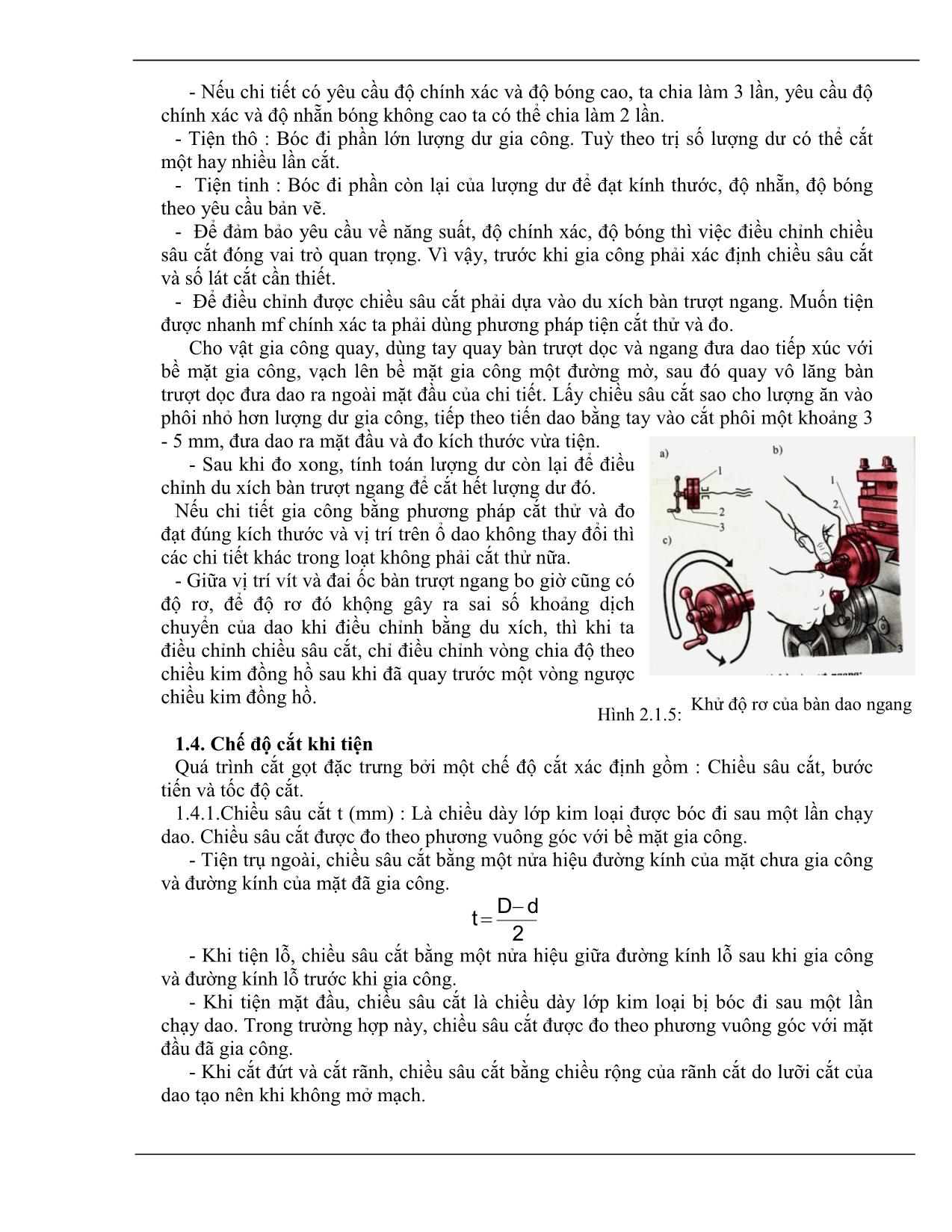
Trang 6
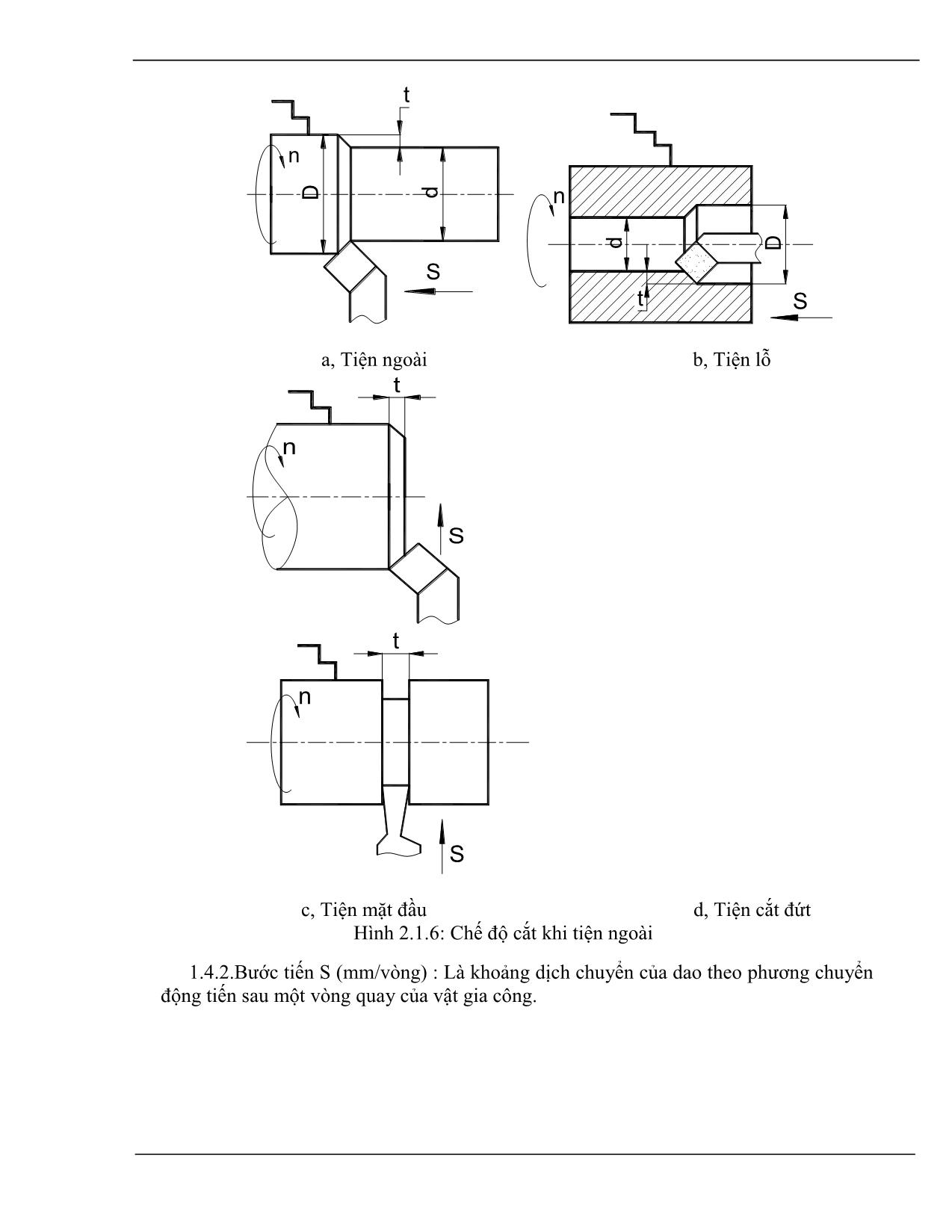
Trang 7
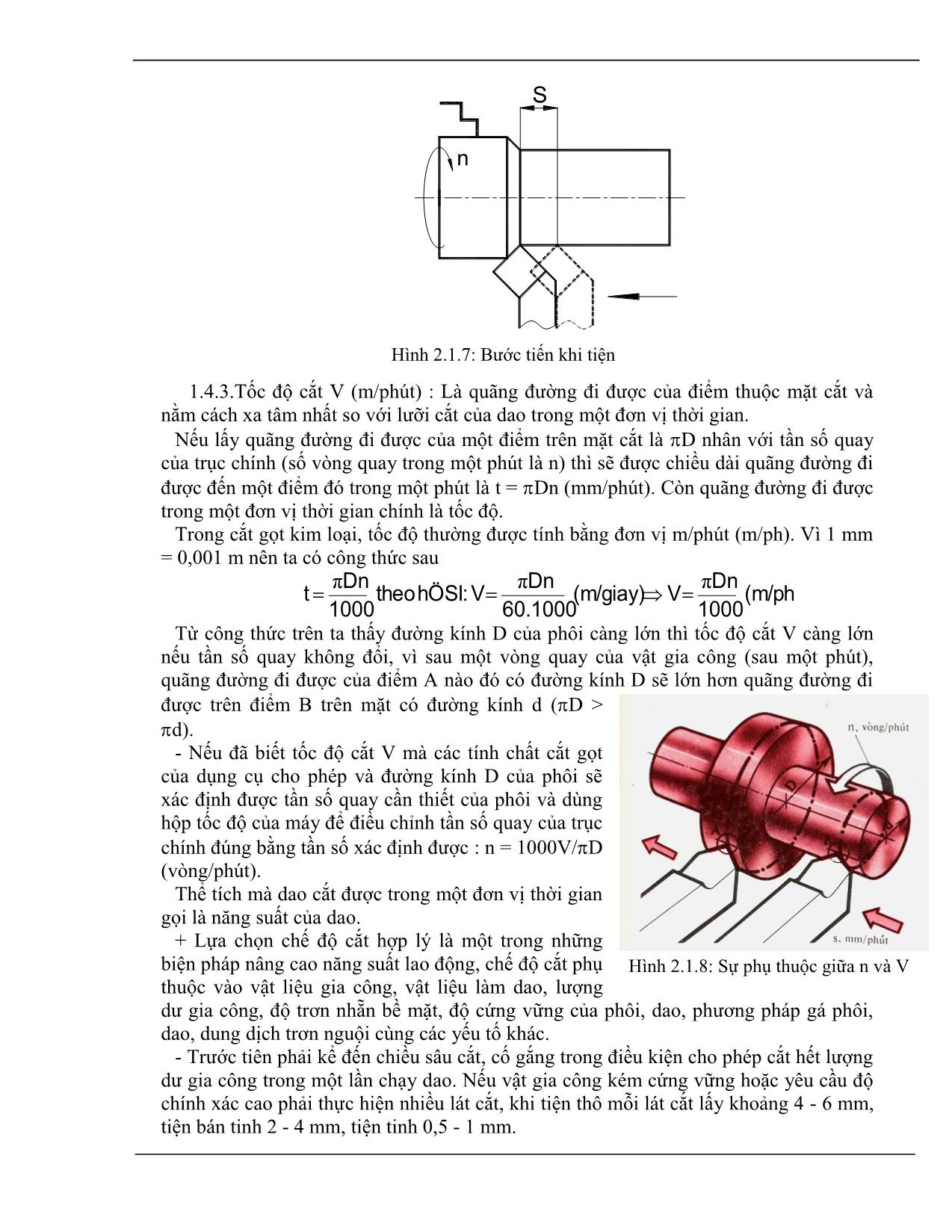
Trang 8
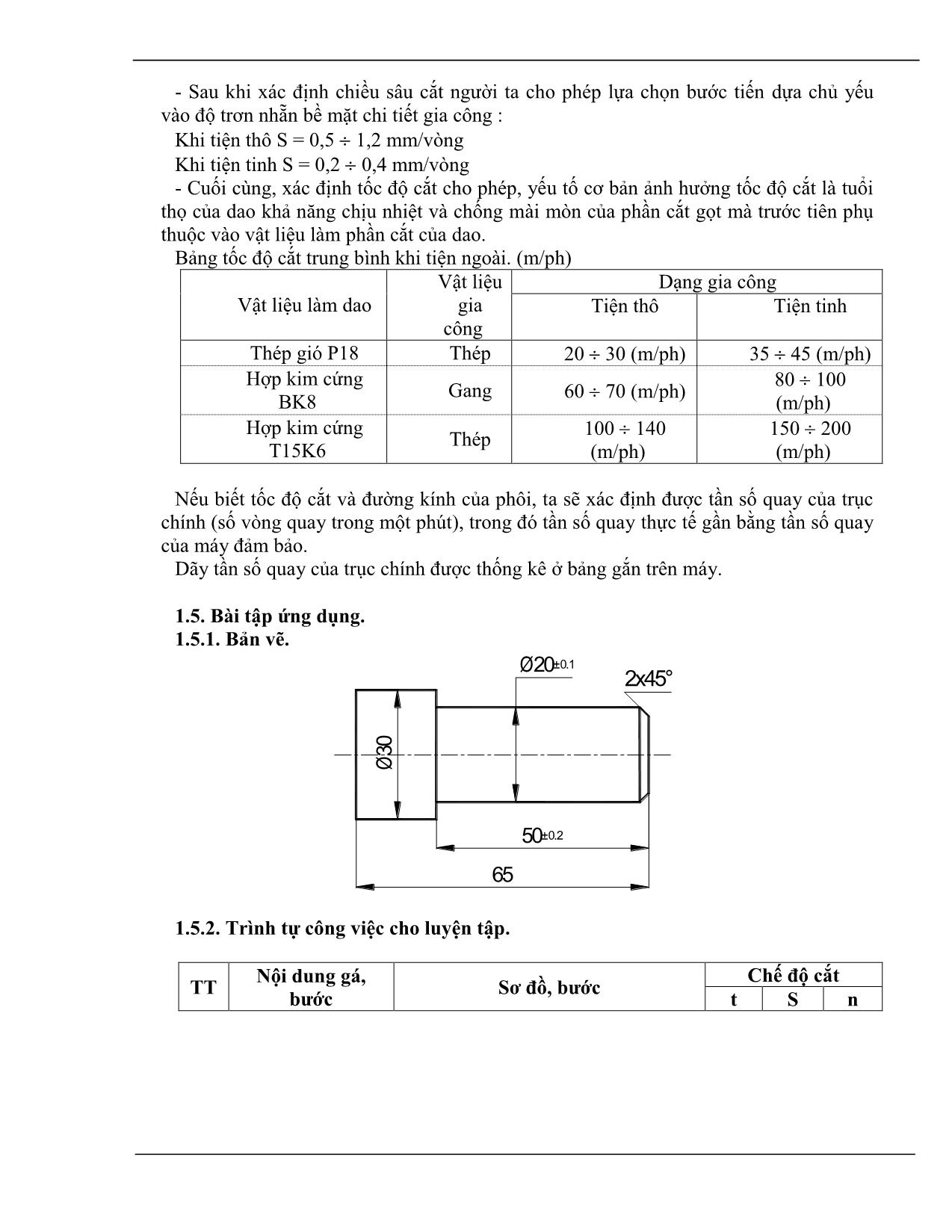
Trang 9
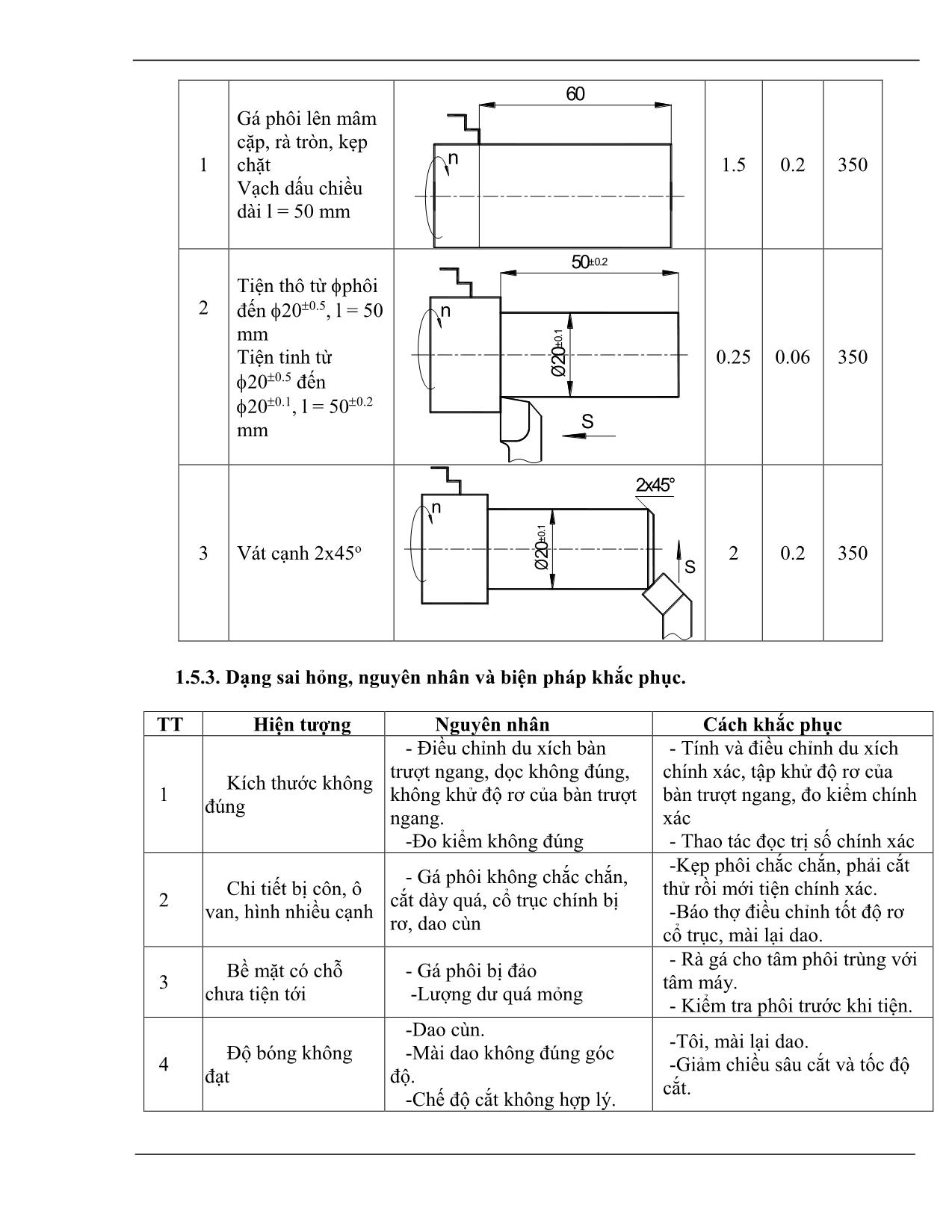
Trang 10
Tải về để xem bản đầy đủ
Tóm tắt nội dung tài liệu: Giáo trình Nghề Tiện
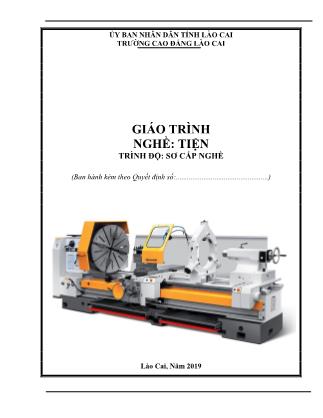
ng hợp phôi có vỏ cứng, nên tăng chiều sâu cắt t cho vượt qua lớp vỏ cứng, nhưng đồng thời phải giảm tốc độ cắt 2.6.2. Phay mặt phẳng nghiêng bằng dao phay mặt đầu. Sau khi gá phôi, gá dao, điều chỉnh máy và điều chỉnh vị trí dao phôi ,ta tiến hành gia công (Hình 6.13). Hình 6.13: Phay mặt phẳng nghiêng bằng dao phay mặt đầu - Đóng điện cho trục chính máy quay. Quay tay điều khiển bàn tiến dọc từ từ tiến đến dao để dao cắt gọt. Khi dao cách phôi được một khoảng 5 10 mm thì gạt tự động cho bàn máy chạy. - Dao cắt hết chiều dài phôi, tắt chuyển động trục chính ( hoặc hạ bàn máy xuống 0,51 mm ) lùi dao về vị trí ban đầu . Kiểm tra kích thước , độ phẳng điều chỉnh tiếp chiều sâu để cắt lát 2,3 cho đến đạt kích thước theo bản vẽ. - Chế độ cắt khi phay mặt phẳng : với vật liệu gia công là gang, thép thì tốc độ cắt V cho dao thép gió 50 m/phút ; dao hợp kim cứng:V=70 150 m/phút ( trong đó tốc độ cắt cho dao trụ nhỏ hơn dao mặt đầu , dao nhiều răng tốc độ cắt chọn nhỏ hơn dao ít răng. Trường hợp vật liệu gia công mềm dẻo như nhôm, đồng, duy ra tốc độ cắt V có thể lấy gấp 2.54 lần so với tốc độ cắt khi phay gang, thép ). - Chiều sâu cắt t: khi phay thô thép lấy t = 3 5mm, phay thô gang t = 57mm (Dao mặt đầu có một răng lấy t bằng một nửa giới hạn trên). Khi phay tinh bằng dao trụ lấy t = 10.5 mm, dao mặt đầu t = 0.50.1mm. Tốc độ chạy dao Sz phay thô: Sz = 0.10 0.4mm/răng.Phay thô gang Sz = 0.20.50 . Khi phay tinh lấy Sz = 0.050.12 mm/răng .Tuỳ theo vật liệu gia công và độ nhẵn cần đạt của bề mặt gia công mà ta chọn cho phù hợp. - Trường hợp phôi có vỏ cứng, nên tăng chiều sâu cắt t cho vượt qua lớp vỏ cứng, nhưng đồng thời phải giảm tốc độ cắt 2.6.3. Phay mặt phẳng nghiêng bằng dao phay góc. - Các loại dao phay góc thường dùng Cách này chỉ áp dụng trong trường hợp bề rộng của mặt phẳng nghiêng rất nhỏ (khoảng 25 - 30mm trở lại) và chỉ phay một lần là đủ chiều rộng đó. Ví dụ: Trường hợp phay vát góc, phay rãnh chữ V với kích thước nhỏ. Phôi được gá bình thường (không xoay nghiêng) trên bàn máy phay. Dùng dao phay góc đơn, hoặc kép (hình 29.7.5) cắt gọt bằng lưỡi cắt có góc xiên thích hợp với độ nghiêng cần có. Dao phay góc đơn thường có góc độ tiêu chuẩn: 550; 600; 700; 750; 850. Dao phay góc kép lệch thường có góc ở một bên là 150; 200 và 250. Tốc độ cắt và lượng chạy dao khi dùng dao phay góc phải chọn trị số nhỏ hơn so với dao mặt trụ vì điều kiện cắt khó hơn. 2.6.3.1. Phay mặt phẳng nghiêng bằng dao phay góc đơn. Măt phẳng nghiêng phay bằng dao phay góc có thể thực hiện trên máy phay ngang, máy phay đứng Phôi gá trên Ê tô hoặc gá trực tiếp bàn máy, khi gá phải rà chỉnh cho các mặt chuẩn trên (hoặc dưới) phôi song song với mặt bàn máy, mặt cạnh phôi song song phương chạy dao khi cắt gọt (Hình6.15). Chế độ cắt đối với dao phay góc răng liền thép gió chọn bằng 3 1 2 1 so với dao phay trụ, dao phay ngón cùng loại vật liệu (vì dao phay góc có nhiều răng, cỡ răng nhỏ, mảnh, dễ gẫy, mẻ) Hình 6.14: Dao phay góc a)Dao phay góc đơn. b)Dao phay góc kép trụ nằm. c)Dao phay góc lệch. d)Dao phay góc đơn trụ đứng 2.6.3.2. Phay mặt phẳng nghiêng bằng dao phay góc kép. Phương pháp gia công mặt phảng nghiêng bằng dao phay góc kép tương tự như gia công mặt nghiêng bằng dao phay góc đơn. Tuy nhiên khi dùng dao phay góc kép chiều sâu mỗi lớp cắt thường nhỏ hơn dao phay mặt đầu hoặc dao phay mặt trụ(hình 6.16). BÀI 6: PHAY RÃNH 1. Yêu cầu kỹ thuật khi phay rãnh. 1.1. Phân loại rãnh Hình 6.15: Phay mặt nghiêng bằng dao phay góc đơn Hình 6.16: Phay mặt nghiêng bằng dao phay góc kép Rãnh là cái vết được tạo bởi nhiều mặt phẳng hoặc mặt định hình. Dựa theo hình dạng người ta chia rãnh ra các loại rãnh (hình 3.1 a, b, c, d, đ, e) và các dạng rãnh: Rãnh suốt, rãnh kín một đầu, rãnh kín hai đầu. Việc gia công rãnh là một trong những nguyên công được thực hiện trên máy phay. Với các loại rãnh có những yêu cầu kỹ thuật khác nhau và các yêu cầu kỹ thuật này phụ thuộc vào công dụng của chi tiết, dạng sản xuất, độ chính xác về kích thước, về vị trí tương quan và độ bóng bề mặt. Những yêu cầu kỹ thuật này ảnh hưởng đến cách chọn phương pháp gia công. 1.2. Yêu cầu kỹ thuật của rãnh. - Đúng kích thước: Kích thước thực tế với kích thước được ghi trên bản vẽ như: Chiều rộng, chiều sâu,. - Sai lệch hình dạng hình học: Sai lệch về biên dạng, mặt phẳng không vượt quá phạm vi cho phép bởi độ không phẳng, độ không thẳng, hoặc không nhẵn. - Sai lệch về vị trí tương quan: Là sai lệch giữa rãnh so với các mặt hoặc các kích thước khác như rãnh được đối xứng và song song với đường trục của chi tiết hình trụ,.. - Độ nhám đạt yêu cầu. 2. Phương pháp gia công 2.1.Gá lắp, điều chỉnh êtô. Gá ê tô lên bàn máy, gá phiến đo lên hàm êtô, dùng đồng hồ so gá như hình vẽ rà chỉnh sao cho phiến đo song song với phương trượt dọc(Mục đích điều chỉnh gián tiếp hàm êtô song song với phương trượt dọc) Trường hợp yêu cầu gá hàm êtô song song phương trượt ngang bàn máy nếu có ke gá thì kẹp ke gá trực tiếp hàm êtô và điều chỉnh cho ke gá (1) tiếp xúc đều với băng trượt đứng của máy phay (2) như hình vẽ hoặc gá phiến đo rà tương tự như trường hợp gá hàm êtô song song với phương trượt dọc bàn máy. Sau đó kẹp chặt êtô với bàn máy bằng bulông hoặc bu lông bích kẹp(hình 3.2). 2.2.Gá lắp, điều chỉnh phôi. Dùng đôi căn phẳng có chiều cao như nhau đặt lên đáy ê tô, đặt phôi lên đôi căn phẳng, dung tay quay siết nhẹ cho 2 hàm ê tô tiếp xúc vào 2 mặt bên phôi, lấy búa nhựa gõ nhẹ vào mặt trên phôi sao cho đôi căn phẳng chắc và tiến hành siết chặt rồi kiểm tra lần cuối xem đôi căn phẳng có bị rơ lỏng không (hình 3.3). 21 Hình 3.2: Rà song song hàm ê tô trên bàn máy Sau khi gá phôi lên ê tô để đảm bảo mặt trên song song với mặt dưới ta tiến hành rà phẳng. Dùng đồng hồ so rà chỉn cho mặt chuẩn trên hoặc dưới của phôi song song với mặt bàn máy tương tự khi gá để gia công mặt phẳng. Có thể dùng búa gõ chỉnh để mặt chuẩn dưới tiếp xúc đều với mặt căn phẳng(hình 3.4). 2.3 .G á lắp, điều chỉnh dao. 2.3.1.Gá lắp, điều chỉnh dao phay trụ. - Gá trục dao lên trục chính máy và gá dao lên trục dao: Hình 3.3: Gá phôi lên ê tô 0 90 8 0 7 0 60 50 40 3 0 2 0 10 0 90 8 0 7 0 60 50 40 3 0 2 0 10 Hình 3.4: Rà song song khi gá phôi Tương tự như gá dao phay mặt đầu(hình 3.5). Trục gá dao (3) được gá lên trục chính máy sau đó dùng các bạc chặn(5) để xác định vị trí dao trên trục dao(4) sao đó gá giá đỡ trục gá dao lên đầu máy siết đai ốc (2) cố định giá đỡ. Để đảm bảo trục quay đồng tâm ta dùng bạc đồng (8)sau đó dùng đai ốc văn chắc cố định dao. - Điều chỉnh dao phay trụ: Để đảm bảo dao cắt đạt kích thước bề rộng rãnh (A) và chiều cao (h) ta tiến hành điều chỉnh bàn trượt ngang và bàn trượt đứng để sao cho vị trí dao phôi đạt kích thước A và h. Sau khi điều chỉnh xong ta khóa chặt bàn trượt ngang đảm bảo không xê dịch trong quá trình cắt gọt (hình 3.6). 2.3.2.Gá lắp, điều chỉnh dao phay mặt đầu. - Gá dao phay mặt đầu lên trục chính máy: Phương pháp gá tương tự như khi gá dao phay mặt phẳng. A h n Hình 3.7: Sơ đồ điều chỉnh dao phay rãnh Hình 3.5: Sơ đồ gá dao lên trục chính máy B A h Hình 3.6: Sơ đồ điều chỉnh vị trí dao phôi để phay rãnh - Điều chỉnh dao phay mặt đầu : Để gia công rãnh bằng dao phay mặt đầu ta tiến hành điều chỉnh vị trí dao phôi. Căn cứ vào vị trí rãnh, ta tiến hành điều chỉnh như sau: Điều chỉnh dao tiếp xúc thành bên của phôi đánh dấu du xích, căn cứ vào du xích để điều chỉnh máy sao cho vị trí dụng cụ cắt trùng với vị trí rãnh theo yêu cầu bản vẽ. 2.4. Điều chỉnh máy 2.4.1. Điều chỉnh máy bằng tay. 2.4.1.1. Điều chỉnh máy phay: - Điều chỉnh tốc độ trục chính (n) : căn cứ tốc độ cắt cho phép ( V) tính ra tốc độ cho phép (n) : D V n . 1000 vòng /phút. Sau đó căn cứ tốc độ thực tế hiện có của trục chính trên máy để điều chỉnh máy lấy tốc độ n thực theo nguyên tắc : nthực n -Điều chỉnh tốc độ bàn máy (Sp) : căn cứ tốc độ chạy dao răng cho phép Sz , số răng dao z , tốc độ trục chính vừa điều chỉnh (nthực) - xác định tốc độ chạy dao cho phép SzSp . z . nthực mm/phút. Từ Sp , căn cứ tốc độ thực tế hiện có của bàn máy để điều chỉnh lấy Spthực Sp . 2.4.1.1. Điều chỉnh máy bào: Điều chỉnh tốc độ đầu bào theo tốc độ hành trình kép dựa trên cơ sở hai tay gạt và bảng điều khiển tốc độ. Điều chỉnh bước tiến bàn máy dựa trên bánh cóc của bàn trượt ngang để chúng ta điều chỉnh. 2.4.2. Điều chỉnh máy tự động. 2.4.2.1. Điều chỉnh máy phay: Để máy chạy tự động ta tiến hành điều chỉnh hộp tốc độ bàn máy. Căn cứ vào bàng tốc độ và các tay gạt hoặc núm xoay ta tiến hành điều chỉnh. Sau khi điều chỉnh xong tốc độ bàn máy ta tiến hành điều chỉnh cữ không chế hành trình của bàn máy để đảm bảo an toàn khi thực hiện cắt gọt. 2.4.2.2. Điều chỉnh máy bào: Đối với máy bào hệ thống tự động của bàn trượt ngang sử dụng đĩa cóc. Do đó để điều chỉnh tự động ta điều chỉnh khoảng mở của cóc để được khoảng dịch chuyển của bàn máy. 2.5. Cắt thử và đo. Sau khi điều chỉnh vị trí dao phôi ta tiến hành cắt thử lát đầu tiên(thường chiều sâu cắt t=0.2mm) dùng thước cặp kiểm tra kích thước bề rộng rãnh(A) chiều sâu (h) để xác định lượng dư còn lại. 2.6.Tiến hành gia công. 2.6.1.Phay rãnh thông suốt 2.6.1.1.Phay rãnh suốt bằng dao phay trụ nằm. Sau khi gá phôi, gá dao, điều chỉnh máy và điều chỉnh vị trí dao phôi ,ta tiến hành gia công. A h n t=0.2 Hình 3.8: Sơ đồ cắt thử rãnh - Đóng điện cho trục chính máy quay. Quay tay điều khiển bàn tiến dọc từ từ tiến đến dao để dao cắt gọt. Khi dao cách phôi được một khoảng 5 10 mm thì gạt tự động cho bàn máy chạy. - Dao cắt hết chiều dài phôi, tắt chuyển động trục chính ( hoặc hạ bàn máy xuống 0,51 mm ) lùi dao về vị trí ban đầu . Kiểm tra kích thước , sau đó điều chỉnh tiếp chiều sâu để cắt lát 2,3 cho đến đạt kích thước theo bản vẽ(hình 3.9). - Chế độ cắt khi phay: với vật liệu gia công là gang, thép thì tốc độ cắt V cho dao thép gió 50 m/phút ; dao hợp kim cứng:V=70 150 m/phút , cần chú ý dao nhiều răng tốc độ cắt chọn nhỏ hơn dao ít răng. Trường hợp vật liệu gia công mềm dẻo như nhôm, đồng, duy ra tốc độ cắt V có thể lấy gấp 2.5 4 lần so với tốc độ cắt khi phay gang, thép ). - Chiều sâu cắt t: Khi phay thô thép t = 35mm, phay thô gang t = 57mm Khi phay tinh bằng dao trụ t = 10.5 mm Hình 3.9: Phay rãnh bằng dao phay trụ nằm B A h Hình 10.10: Phay rãnh bằng dao phay mặt đầu Tốc độ chạy dao Sz phay thô: Sz = 0.100.4mm/răng.Phay thô gang Sz = 0.20.50 . Khi phay tinh lấy Sz = 0.050.12 mm/răng .Tuỳ theo vật liệu gia công và độ nhẵn cần đạt của bề mặt gia công mà ta chọn cho phù hợp. - Trường hợp phôi có vỏ cứng, nên tăng chiều sâu cắt t cho vượt qua lớp vỏ cứng, nhưng đồng thời phải giảm tốc độ cắt 2.6.1.2.Phay rãnh suốt bằng dao phay mặt đầu. - Đóng điện cho trục chính máy quay. Quay tay điều khiển bàn tiến dọc từ từ tiến đến dao để dao cắt gọt. Khi dao cách phôi được một khoảng 5 10 mm thì gạt tự động cho bàn máy chạy. - Dao cắt hết chiều dài phôi, tắt chuyển động trục chính ( hoặc hạ bàn máy xuống 0,51 mm ) lùi dao về vị trí ban đầu . Kiểm tra kích thước , sau đó điều chỉnh tiếp chiều sâu để cắt lát 2,3 cho đến đạt kích thước theo bản vẽ(hình 3.10). - Chế độ cắt khi phay: với vật liệu gia công là gang, thép thì tốc độ cắt V cho dao thép gió 50 m/phút ; dao hợp kim cứng:V=70 150 m/phút , cần chú ý dao nhiều răng tốc độ cắt chọn nhỏ hơn dao ít răng. Trường hợp vật liệu gia công mềm dẻo như nhôm, đồng, duy ra tốc độ cắt V có thể lấy gấp 2.5 4 lần so với tốc độ cắt khi phay gang, thép ).` A h n - Chiều sâu cắt t: Khi phay thô thép t = 35mm, phay thô gang t = 57mm Khi phay tinh bằng dao trụ t = 10.5 mm Tốc độ chạy dao Sz phay thô: Sz = 0.10 0.4mm/răng.Phay thô gang Sz = 0.20.50 . Khi phay tinh lấy Sz = 0.050.12 mm/răng .Tuỳ theo vật liệu gia công và độ nhẵn cần đạt của bề mặt gia công mà ta chọn cho phù hợp. Trường hợp phôi có vỏ cứng, nên tăng chiều sâu cắt t cho vượt qua lớp vỏ cứng, nhưng đồng thời phải giảm tốc độ cắt 2.6.1.3.Phay rãnh bằng dao phay ngón. - Đóng điện cho trục chính máy quay. Quay tay điều khiển bàn tiến dọc từ từ tiến đến dao để dao cắt gọt. Khi dao cách phôi được một khoảng 5 10 mm thì gạt tự động cho bàn máy chạy. - Dao cắt hết chiều dài phôi, tắt chuyển động trục chính ( hoặc hạ bàn máy xuống 0,51 mm ) lùi dao về vị trí ban đầu . Kiểm tra kích thước , sau đó điều chỉnh tiếp chiều sâu để cắt lát 2,3 cho đến đạt kích thước theo bản vẽ(hình 3.11). Hình 3.11: Phay rãnh bằng dao phay ngón A h n - Chế độ cắt khi phay: với vật liệu gia công là gang, thép thì tốc độ cắt V cho dao thép gió 50 m/phút ; dao hợp kim cứng:V=70 150 m/phút , cần chú ý dao nhiều răng tốc độ cắt chọn nhỏ hơn dao ít răng. Trường hợp vật liệu gia công mềm dẻo như nhôm, đồng, duy ra tốc độ cắt V có thể lấy gấp 2.5 4 lần so với tốc độ cắt khi phay gang, thép ). - Chiều sâu cắt t: Khi phay thô thép t = 35mm, phay thô gang t = 57mm Khi phay tinh bằng dao trụ t = 10.5 mm Tốc độ chạy dao Sz phay thô: Sz = 0.10 0.4mm/răng.Phay thô gang Sz = 0.20.50 . Khi phay tinh lấy Sz = 0.050.12 mm/răng . Tuỳ theo vật liệu gia công và độ nhẵn cần đạt của bề mặt gia công mà ta chọn cho phù hợp. - Trường hợp phôi có vỏ cứng, nên tăng chiều sâu cắt t cho vượt qua lớp vỏ cứng, nhưng đồng thời phải giảm tốc độ cắt 2.6.4.Phay rãnh bằng dao phay đĩa. - Đóng điện cho trục chính máy quay. Quay tay điều khiển bàn tiến dọc từ từ tiến đến dao để dao cắt gọt. Khi dao cách phôi được một khoảng 5 10 mm thì gạt tự động cho bàn máy chạy(hình 3.12). - Dao cắt hết chiều dài phôi, tắt chuyển động trục chính ( hoặc hạ bàn máy xuống 0,51 mm ) lùi dao về vị trí ban đầu . Kiểm tra kích thước , sau đó điều chỉnh tiếp chiều sâu để cắt lát 2,3 cho đến đạt kích thước theo bản vẽ. - Chế độ cắt khi phay: với vật liệu gia công là gang, thép thì tốc độ cắt V cho dao thép gió 50 m/phút ; dao hợp kim cứng:V=70 150 m/phút , cần chú ý dao nhiều răng tốc độ cắt chọn nhỏ hơn dao ít răng. Trường hợp vật liệu gia công mềm dẻo như nhôm, đồng, duy ra tốc độ cắt V có thể lấy gấp 2.5 4 lần so với tốc độ cắt khi phay gang, thép). - Chiều sâu cắt t: Khi phay thô thép t = 35mm, phay thô gang t = 57mm Khi phay tinh bằng dao trụ t = 10.5 mm Tốc độ chạy dao Sz phay thô: Sz = 0.100.4mm/răng.Phay thô gang Sz = 0.20.50 . Khi phay tinh lấy Sz = 0.050.12 mm/răng .Tuỳ theo vật liệu gia công và độ nhẵn cần đạt của bề mặt gia công mà ta chọn cho phù hợp. - Trường hợp phôi có vỏ cứng, nên tăng chiều sâu cắt t cho vượt qua lớp vỏ cứng, nhưng đồng thời phải giảm tốc độ cắt h a Hình 3.12: Phay rãnh bằng dao phay đĩa
File đính kèm:
giao_trinh_nghe_tien.pdf