Giáo trình mô đun Mài mặt phẳng
Giới thiệu:
Là bài học đầu tiên của công nghệ mài, các kiến thức trong bài này sẽ đề cập đến
quá trình cắt và các phương pháp mài để áp dụng cho tất cả các loại máy mài
phẳng, máy mài tròn, máy mài vô tâm.làm cơ sở cho các mô đun mài tiếp theo của
chương trình
Mục tiêu thực hiện:
- Giải thích rõ các đặc điểm khác nhau giữa gia công mài và gia công tiện, phay
bào.
- Trình bày được nguyên tắc chung của mài, nguyên lý áp dụng cho nguyên công
mài bất kỳ như: mài tiến dọc, ngang, quay tròn, phối hợp
- Nhận dạng chính xác sơ đồ nguyên lý mài, phân tích rõ lực cắt và công suất khi
mài
1.Những đặc điểm khác nhau giữa mài và tiện, phay, bào
- Quá trình mài kim loại là quá trình cắt gọt chi tiết bằng dụng cụ cắt là đá mài, tạo
ra rất nhiều phoi vụn do sự ma sát cắt và cà miết của các hạt mài vào vật gia công.
- Mài có những đặc điểm khác với các phương pháp gia công cắt gọt khác như tiện,
phay bào như sau:
+ Đá mài là dụng cụ cắt có nhiều lưỡi cắt với góc cắt khác nhau
+ Hình dáng hình học của mỗi hạt mài khác nhau, bán kính góc lượn ở đỉnh của hạt
mài, hướng của góc cắt sắp xếp hỗn loạn, không thuận lợi cho việc thoát phoi
+ Tốc độ cắt khi mài rất cao, cùng một lúc trong một thời gian ngắn có nhiều hạt
mài tham gia cắt gọt và tạo ra nhiều phoi vụn
+ Độ cứng của hạt mài cao do đó có thể cắt gọt được những vật liệu cứng mà các
loại dụng cụ cắt khác không cắt được như thép đã tôi, hợp kim cứng.
+ Hạt mài có độ giòn cao nên dễ thay đổi hình dạng, lưỡi cắt bị dễ bị vỡ vụn tạo
thành những hạt mới hoặc bật ra khỏi chất dính kết.4
+ Do có nhiều hạt cùng tham gia cắt gọt và hướng góc cắt của các hạt không phù
hợp nhau tạo ra ma sát làm cho chi tiết gia công bị nung nóng rất nhanh và nhiệt độ
vùng cắt rất lớn
+ Hạt mài có nhiều cạnh cắt và có bán kính tròn p ở đỉnh (hình 1.1)
Quá trình tách phoi của hạt có thể chia làm 3 giai đoạn (hình 1.2)
a/ Giai đoạn 1(trượt): Gọi bán kính cong của mũi hạt mài là p, chiều dày của lớp
kim loại bóc đi là a. Ở giai đoạn đầu này mũi hạt mài bắt đầu va đập vào bề mặt gia
công (hình1.2.a), lực va đập này phụ thuộc vào tốc độ mài và lượng tiến của đá vào
vật gia công, bán kính cong p của mũi hạt mài hợp lý thì việc cắt gọt thuận tiện,
nếu bán kính p quá nhỏ hoặc quá lớn so với chiều dày cắt a thì hạt mài sẽ trượt trên
bề mặt vật mài làm cho vật mài nung nóng với nhiệt cắt rất lớn
b/ Giai đoạn 2 (nén): Áp lực mài tăng lên, nhiệt cắt tăng lên làm tăng biến dạng
dẻo của kim loại, lúc này bắt đầu xẩy ra quá trình cắt phoi (hình 1.2b)
Trong quá trình làm việc bán kính này tăng lên
đến một trị số nhất định, lực cắt tác dụng vào hạt mài
tăng lên đến trị số đủ lớn, có thể phá hạt mài thành
những hạt khác nhau tạo ra những lưỡi cắt mới, hoặc
làm bật các hạt mài ra khỏi chất dính kết. Vì vậy quá
trình mài, sự tách phoi phụ thuộc vào hình dạng của
các hạt mài.
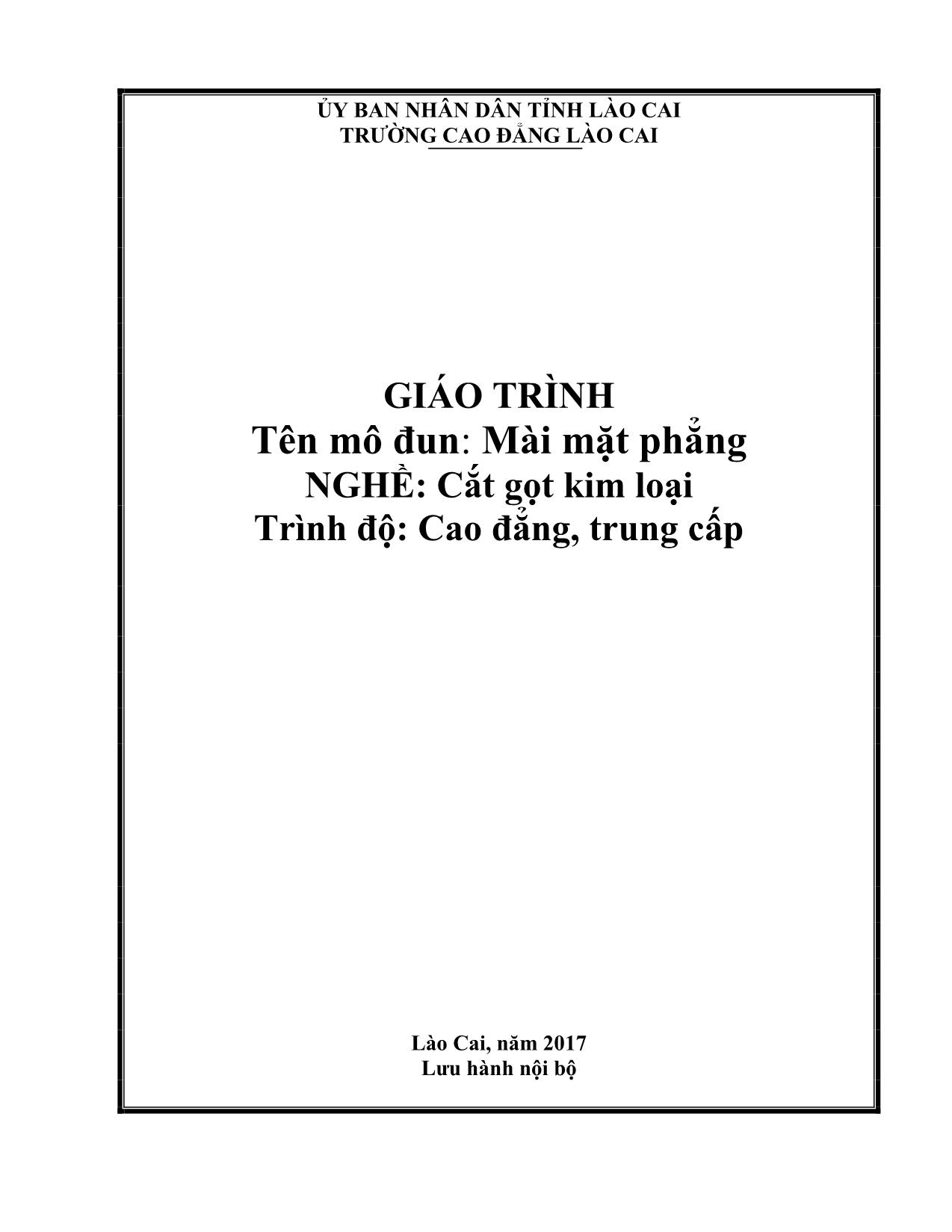
Trang 1
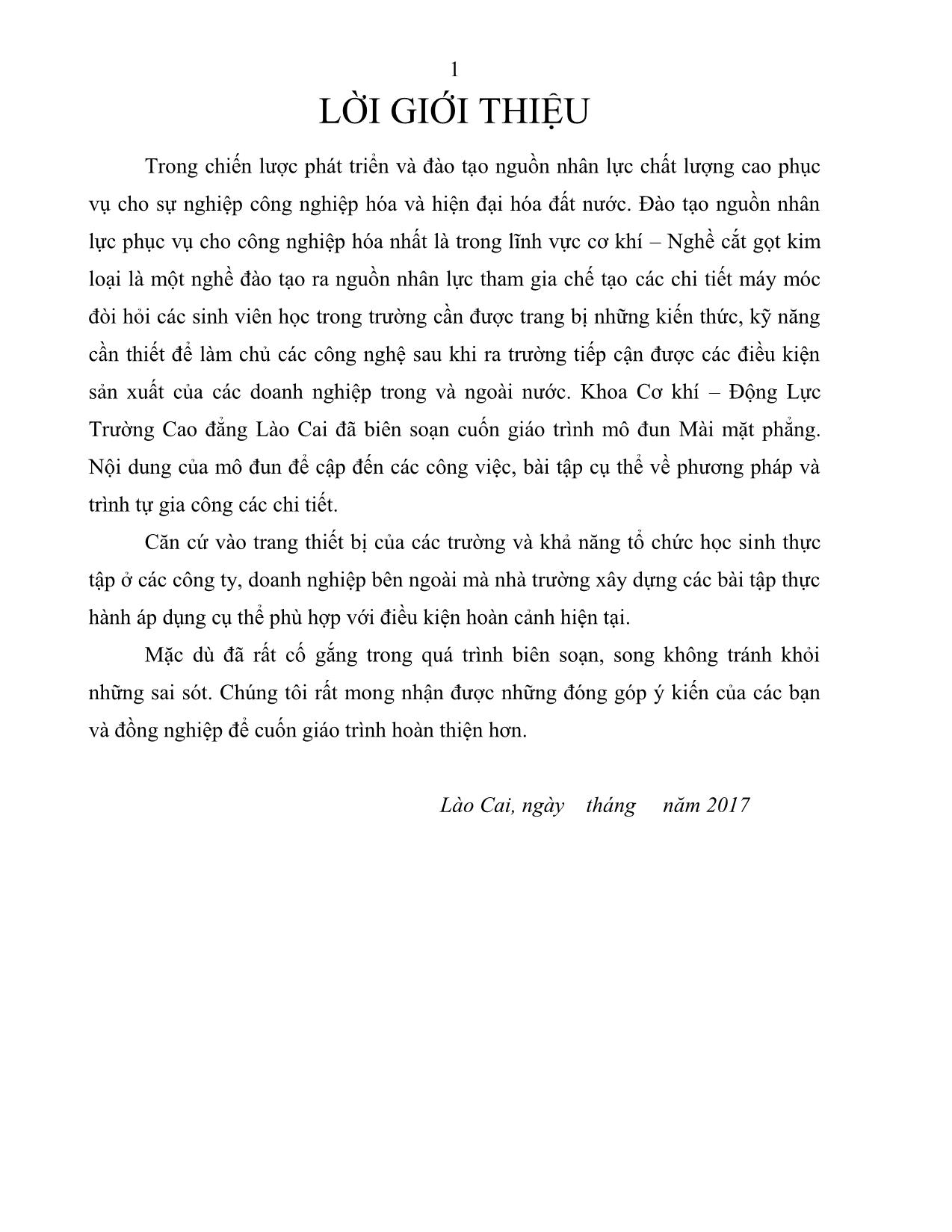
Trang 2
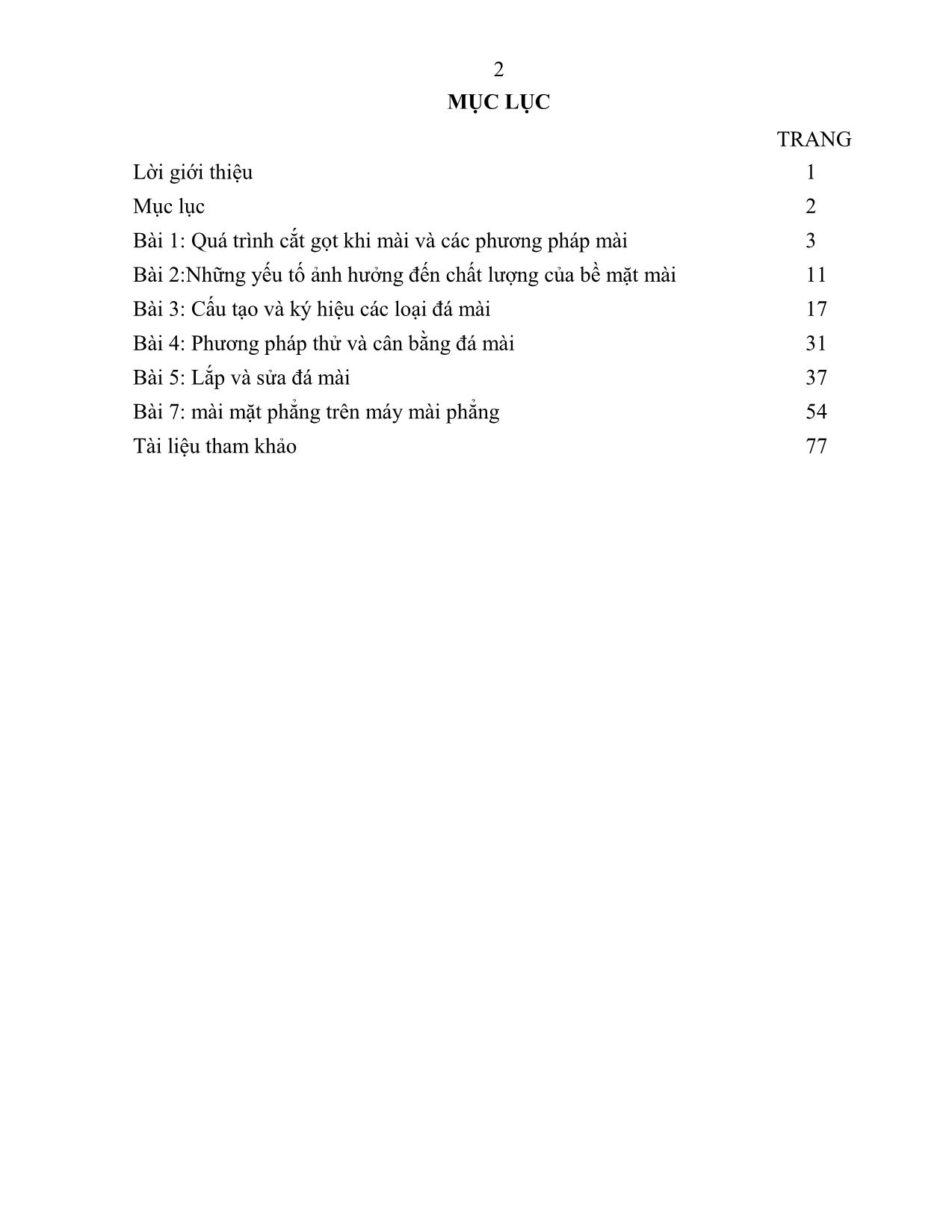
Trang 3
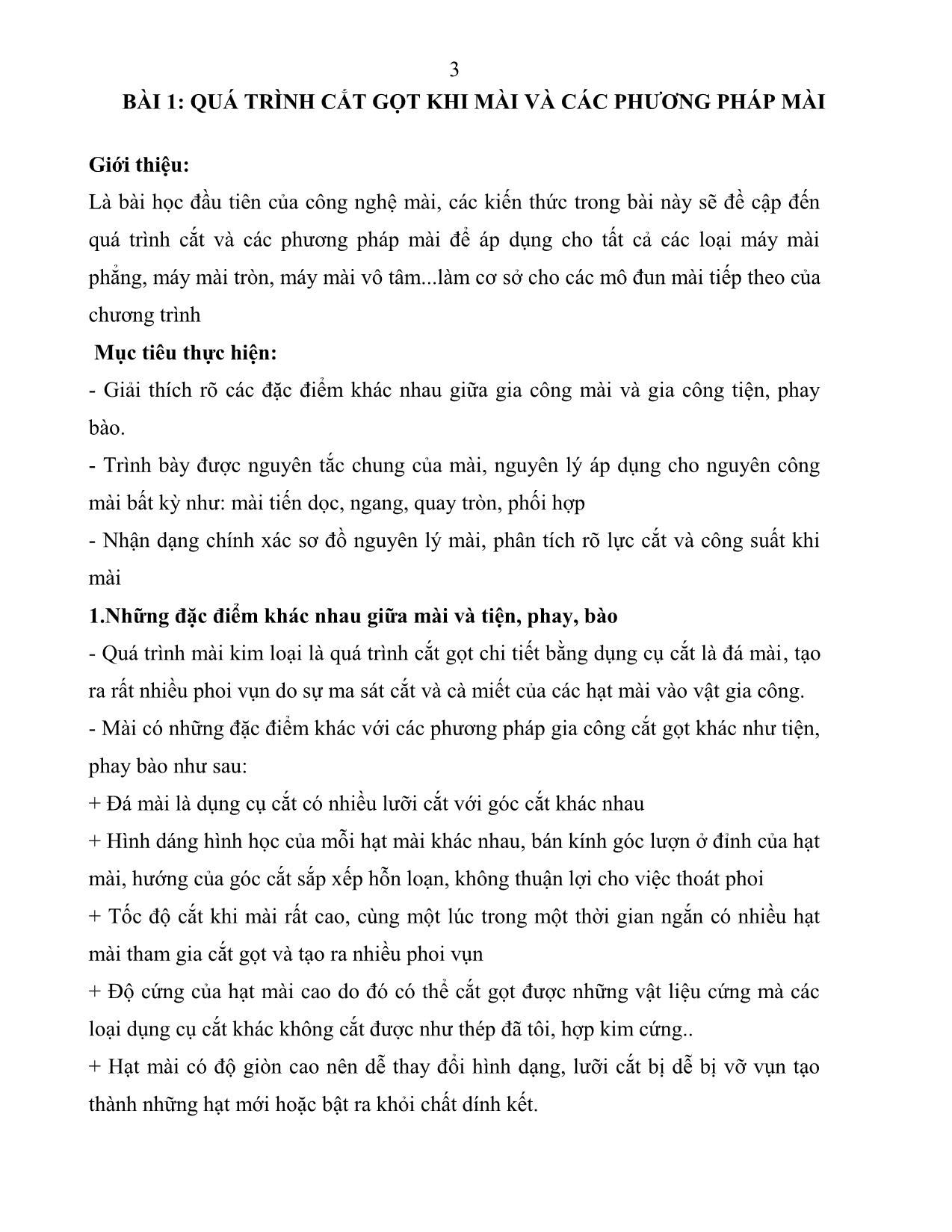
Trang 4
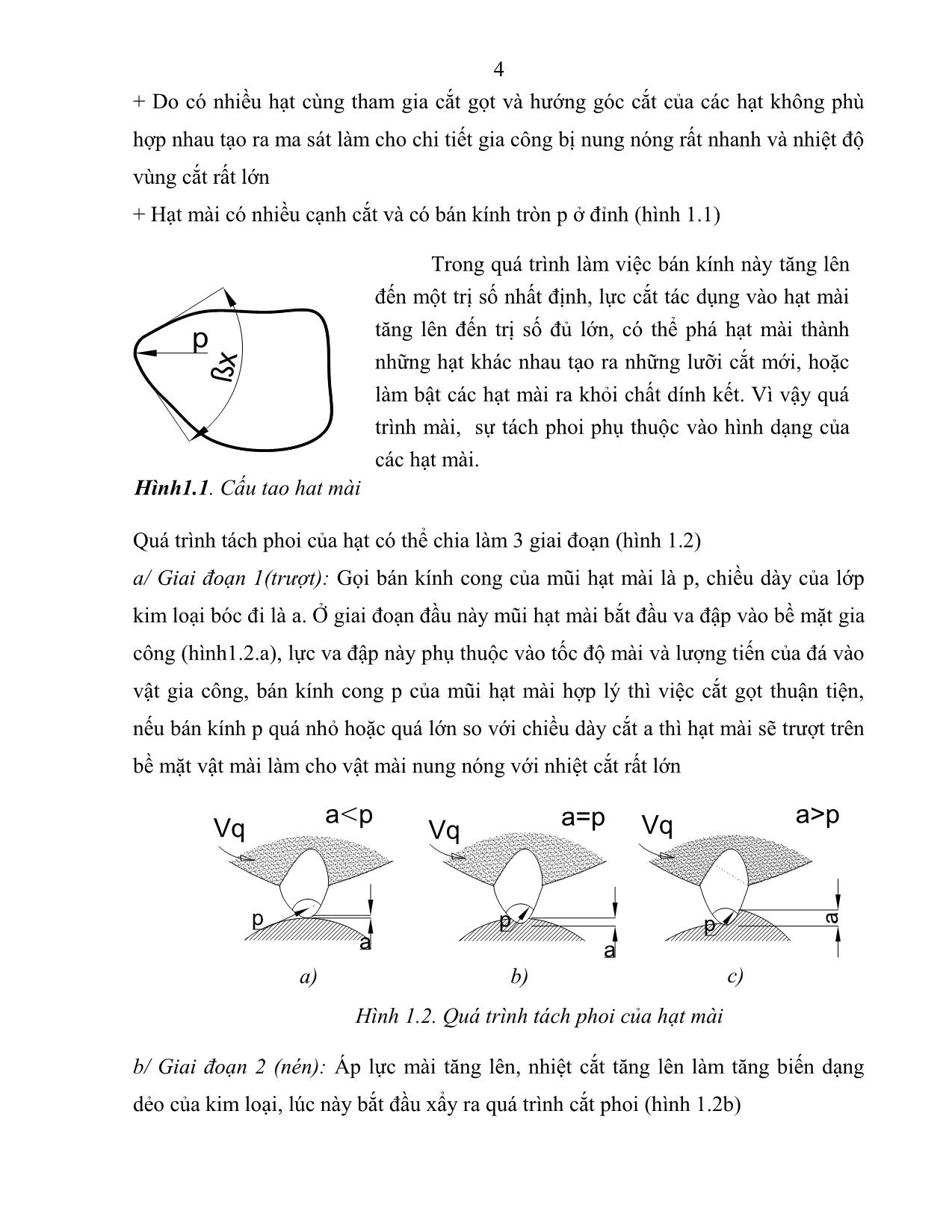
Trang 5
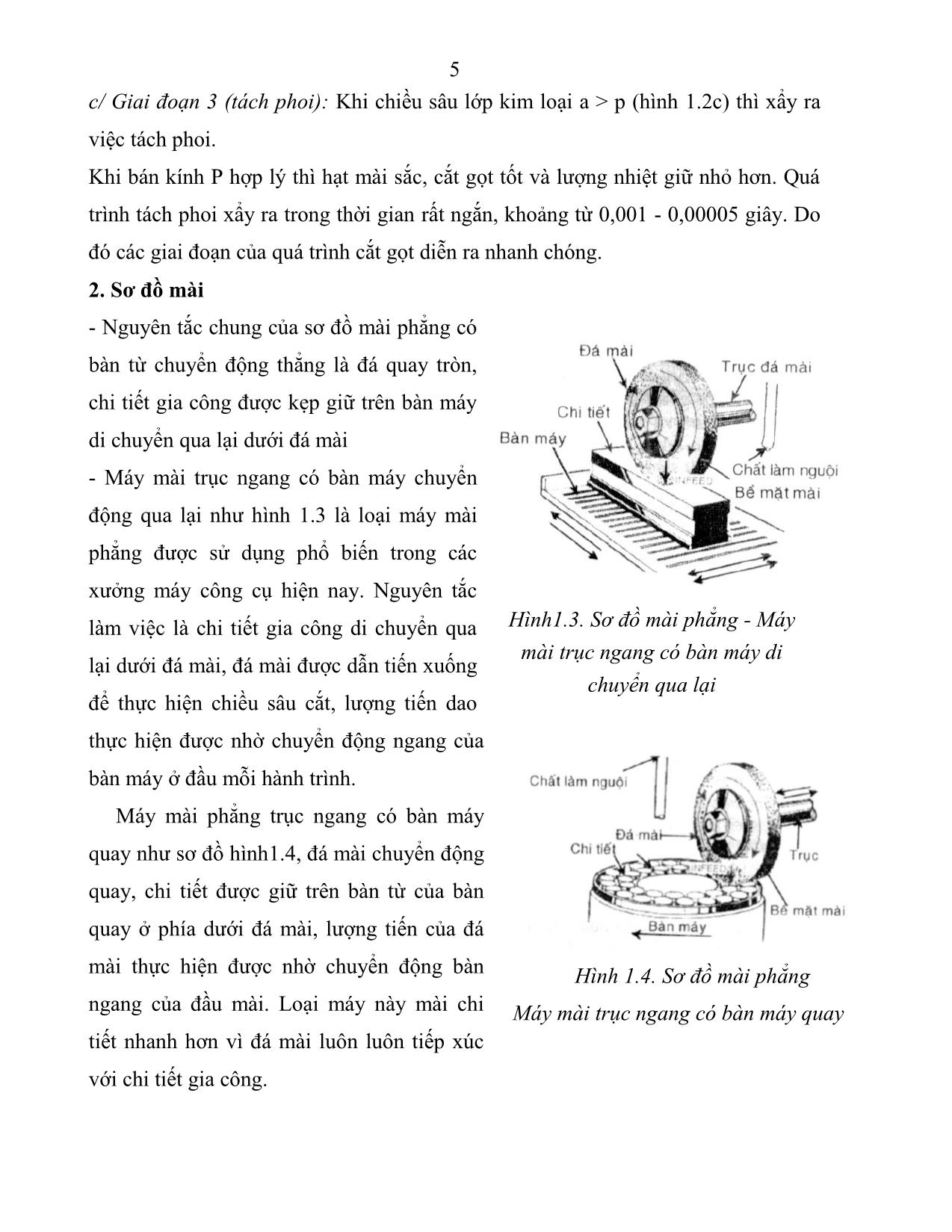
Trang 6
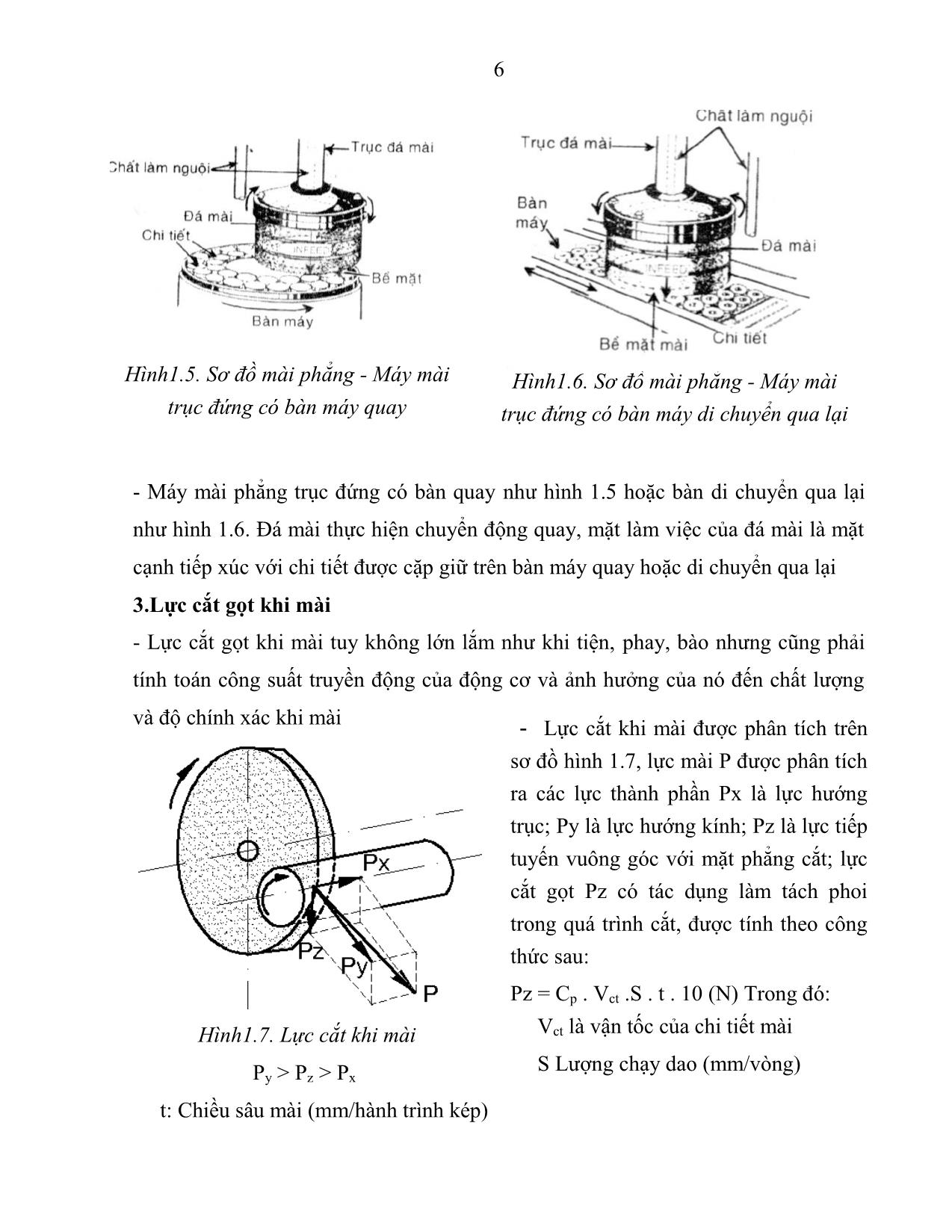
Trang 7
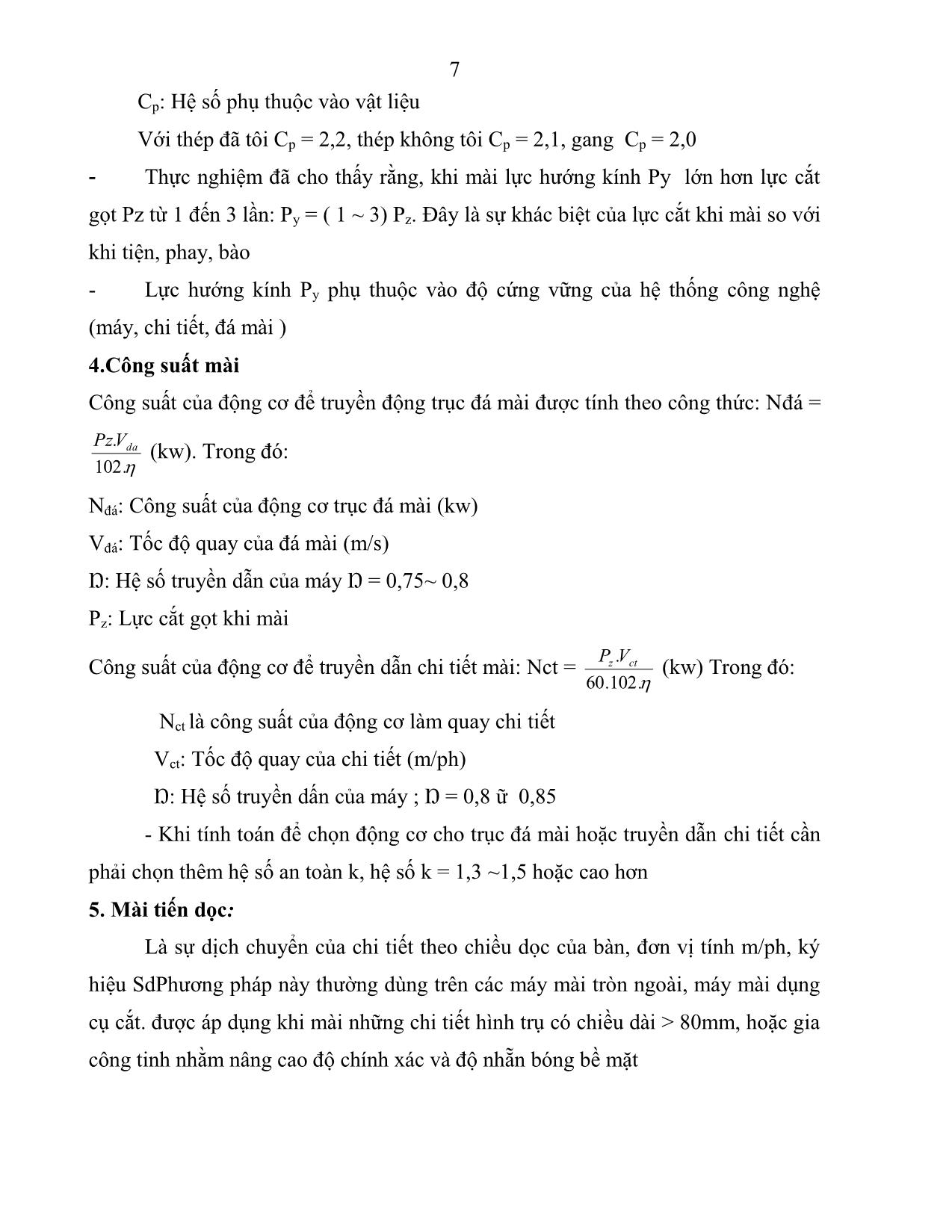
Trang 8
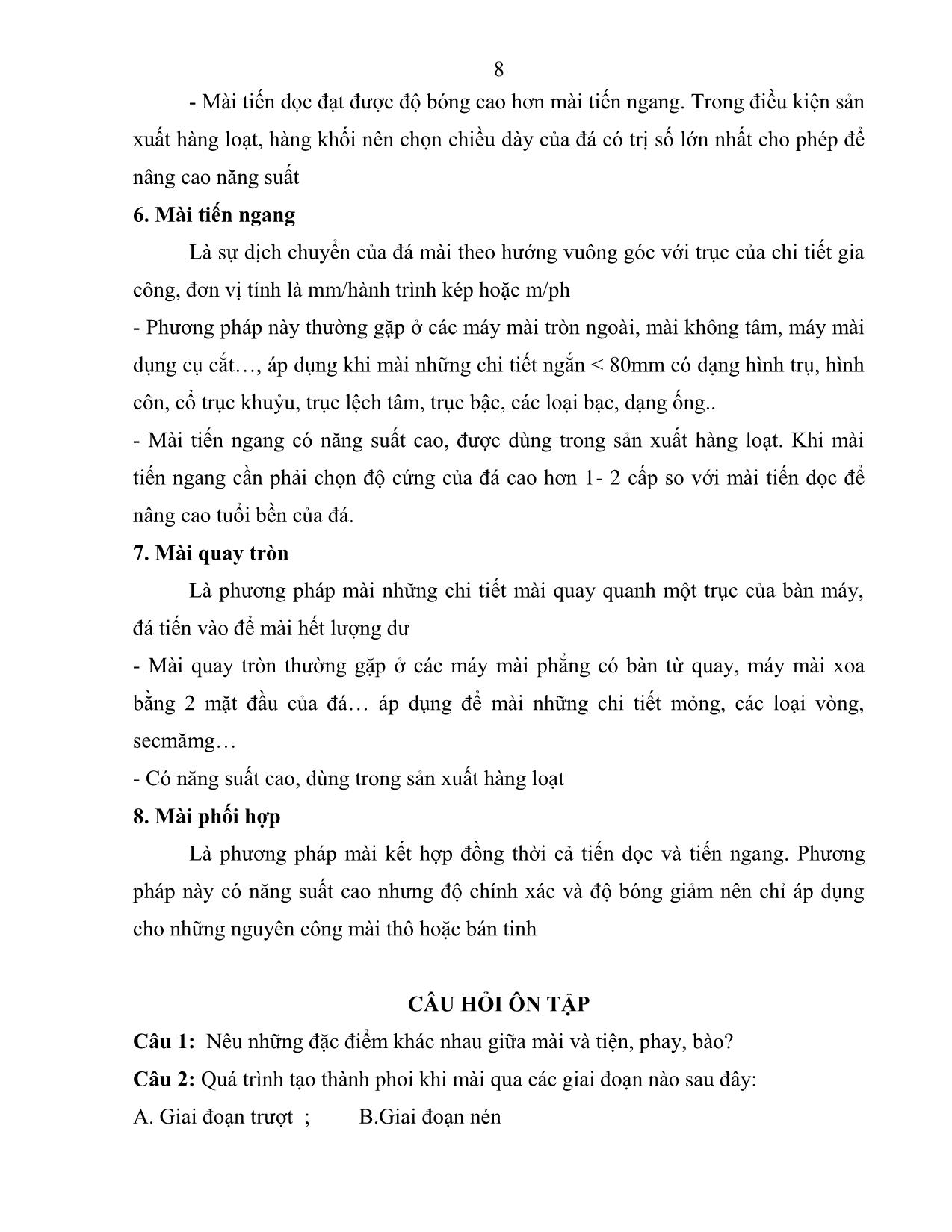
Trang 9
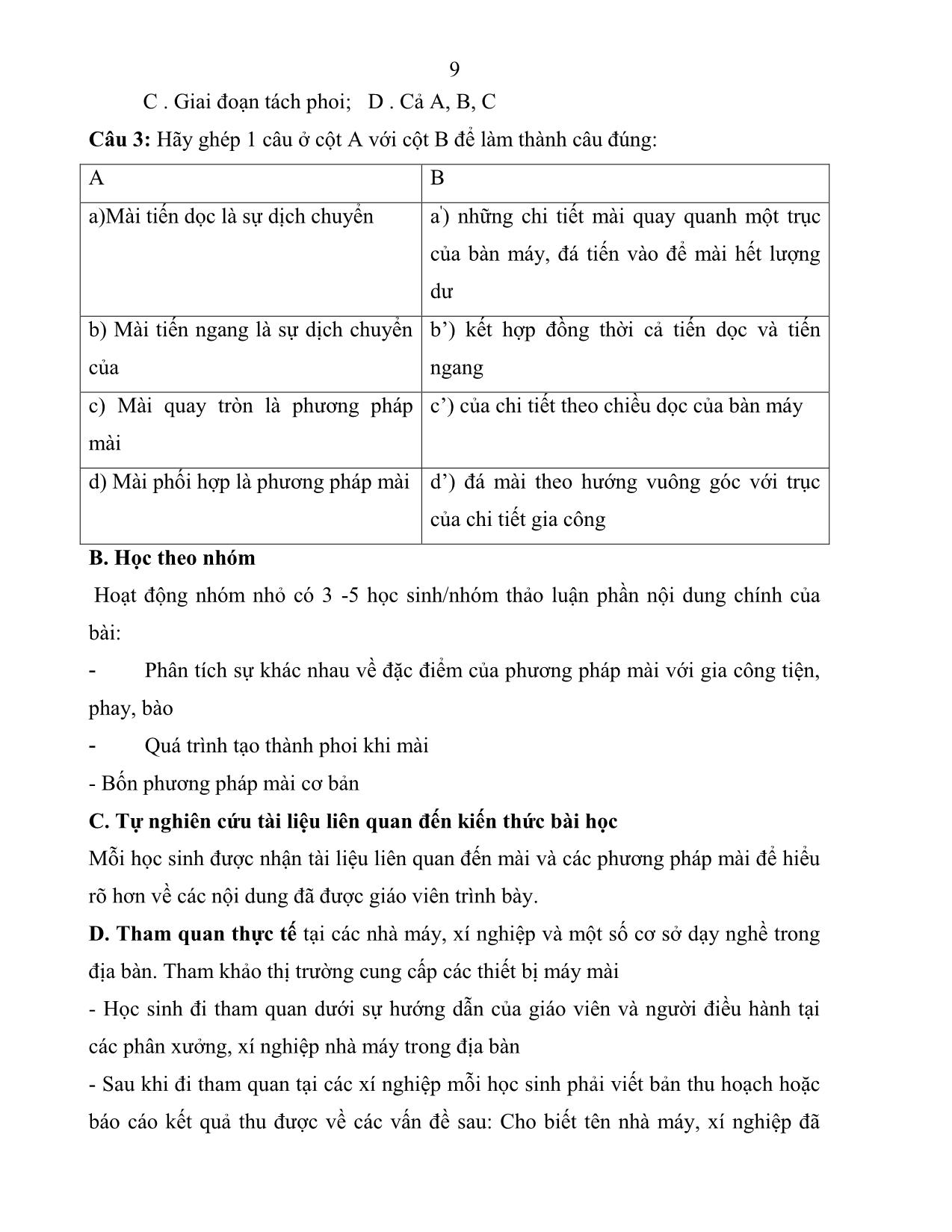
Trang 10
Tải về để xem bản đầy đủ
Tóm tắt nội dung tài liệu: Giáo trình mô đun Mài mặt phẳng
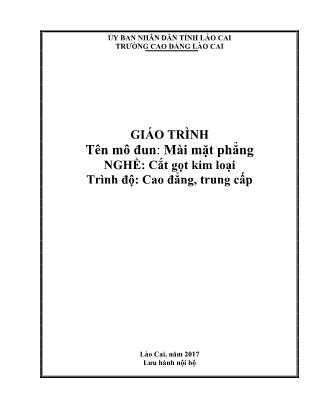
gia công phụ thuộc rất nhiều vào độ chính xác của bàn từ và trình độ tay nghề của người thợ. Vì vậy bàn từ cần được giữ gìn và bảo quản rất chu đáo . Phải kiểm tra thật chu đáo các thiết bị điện để đảm bảo lực kẹp tốt nhất Không để bàn từ bị xước hoặc lồi lõm không bằng phẳng. Nếu đã bị xước hoặc không bằng phẳng thì có thể mài lại mặt bàn từ bằng đá của máy mài mà không cần làm nguội Những chi tiết mỏng hoặc có tính nhiễm từ cao thì sau khi mài phải khử từ Khi mài những vật liệu không nhiễm từ thì phải có đồ gá kẹp bằng vật liệu nhiễm từ cao Lực hút của bàn từ thường ổn định và không được lớn lắm nên khi gia công cần tuân theo chế độ cắt gọt đã cho của mỗi máy, tránh lực cắt gọt quá lớn sẽ gây ra tai nạn lao động. 3.1.Các bước tiến hành gá chi tiết gia công lên bàn từ 60 a/ Chuẩn bị: Kiểm tra từng bộ phận của máy và tra dầu bôi trơn, chuẩn bị đá mài và dụng cụ cần thiết b/ Gá lắp bàn từ lên bàn máy: Làm sạch mặt trên của bàn máy hoặc dưới của bàn từ Lắp chặt sơ bộ bàn từ bằng bu lông hình chữ T, cho đầu đo của đồng hồ so tiếp xúc với mặt sau của bàn từ và dịch chuyển bàn máy sang phải hoặc trái Kiểm tra độ dịch chuyển chỉ trên đồng hồ so và hiệu chỉnh độ song song của bàn từ Xiết chặt các bu lông của bàn từ và dùng đồng hồ so kiểm tra lại độ song song lần cuối (hình 7.3) Hình 7.3. Điều chỉnh độ song song của bàn từ c/ Gá lắp chi tiết có diện tích lớn như hình khối vuông hay chữ nhật Làm sạch các bề mặt của chi tiết( Hình 7.4) Đặt chi tiết lên bàn từ Bật công tắc bàn từ về vị trí cấp từ Dùng tay kiểm tra độ vững của chi tiết gá lắp Tắt công tắc bàn từ và lấy chi tiết ra một cách nhẹ nhàng Hình 7.4. Chiều gá lắp chi tiết gia công 61 d/ Gá lắp chi tiết có mặt đáy nhỏ và cao Lau sạch mặt trên của bàn từ và các bề mặt của chi tiết gia công Đặt chi tiết lên bàn từ Chặn xung quanh chi tiết bằng các khối tỳ Bật công tắc bàn từ về vị trí cấp từ và dùng búa cao su gõ nhẹ vào các khối tỳ cho chúng tỳ sát vào chi tiết để Hình 7.5. Sử dụng các khối tỳ đảm bảo vững chắc(hình 7.5) e/ Dùng êtô kẹp chính xác để gá lắp chi tiết gia công Đối với các chi tiết gia công làm bằng vật liệu phi từ tính như phi kim loại hay kim loại màu như nhôm, đồng hoặc những chi tiết có hình dạng không chuẩn thì có thể sử dụng êtô chính xác để làm tăng độ cứng vững khi gia công(hình 7.6). Hình 7.6. Dùng êtô kẹp chính xác f/ Dùng ke và bàn kẹp chữ C để gá lắp chi tiết Hình 7.7: Gá phôi bằng ke gá 62 g/ Dùng khối tỳ chữ V để gá lắp chi tiết Hình 7.8: Gá phôi bằng khối V có gắn nam châm h/ Tháo chi tiết gia công Tắt công tắc bàn từ Xoay công tắc bàn từ theo chiều kim đồng hồ từng nấc một để khử hết từ dư Tháo chi tiết ra nhẹ nhàng không làm xước bề mặt bàn từ và chi tiết 3.2. Các bước tiến hành mài mặt phẳng trên khối lập phương a/ Đọc bản vẽ: Yêu cầu kỹ thuật: - Độ không song, độ không vuông góc giữa các mặt <0,01 - Độ nhám toàn bộ cấp 7 63 b/ Chuẩn bị Kiểm tra tình trạng máy và chọn đá mài phù hợp với điều kiện gia công Kiểm tra độ an toàn của đá mài, cân bằng và rà sửa đá Làm sạch mặt trên của bàn từ bằng vải hoặc cao su, nếu mặt bàn từ bị xước thì phải mài lại hết hoặc dũa sạch cho nhẵn bóng c/ Gá lắp chi tiết gia công lên bàn từ: Làm sạch bề mặt chi tiết gia công Đặt mặt 2(mặt 2//mặt 1) lên gần tâm bàn từ, để chiều dọc của chi tiết // với chiều chuyển động qua lại (trái – phải) của bàn máy (hình7.9) Bật công tắc bàn từ và kiểm tra độ vững chắc của chi tiết được gá (dùng tay lắc) ChiÒu s©u c¾t TiÕn vµ lï i theo chiÒu ngang Bµn m¸ y qua l¹ i Hình7.9. Sơ đồ tiến dao khi cắt gọt d/ Xác định khoảng chạy của bàn máy theo chiều dài chi tiết Điều chỉnh khoảng chạy bàn máy sao cho tại điểm đầu và điểm cuối hành trình tâm của đá mài cách mặt đầu chi tiết 30 – 50mm Gá và điều chỉnh chi tiết gia công ở dưới đá mài bằng cách quay bàn máy bằng tay sang phải – trái, ra – vào theo chiều ngang và di chuyển cho đá xuống chạm vào chi tiết mài 64 Gá đặt chi tiết gia công ở ngay dưới vị trí của đá mài để tâm của đá thẳng tâm chi tiết mài (hình 7.10a), điều chỉnh sao cho đá gần sát với bề mặt gia công (khe hở 1 mm) và để 1/3 bề rộng của đá ăn vào bề mặt chi tiết (hình7.10b) 1/3 bÒ réng ®¸ mµi § ¸ mµi 1 Chi tiÕt gia c«ng Bµn tõ a) b) Hình7.10. Điều chỉnh máy trước khi lấy chiều sâu cắt e/ Mài mặt 1 của chi tiết gia công: Khởi động đá mài quay, thận trọng hạ thấp đá mài xuống cho tiếp xúc nhẹ nhàng với chi tiết gia công khi có tia lửa phát ra Ngừng hạ đá mài và dịch chuyển bàn ngang ra tách rời đá khỏi chi tiết, lấy chiều sâu cắt 0.1mm, lượng ăn dao tiến lùi = 2,5 – 3mm Khởi động dung dịch làm mát và hút bụi Cho bàn máy di chuyển sang trái – phải (hình 7.11)đồng thời thực hiện lượng chạy dao tiến – lùi bằng bàn ngang cho đến khi mài hết chiều rộng của chi tiết (hình 7.12) Đưa chi tiết về vị trí ban đầu, đưa đá mài vào vị trí cắt, kiểm tra để lại 1/2 tổng lượng dư Mài tinh: đặt chiều sâu cắt 0,05mm, lượng ăn dao 1-2mm Kiểm tra độ nhẵn bóng và kích thước thật cẩn thận. Dừng máy, tháo chi tiết ra 65 § ¸ mµi ®i qua hÕt bÒ réng chi tiÕt gia c«ng § ¸ mµi Chi tiÕt gia c«ng Bµn tõ Hình 7.11. Vị trí chạy dao lùi Hình7.12. Vị trí mút hành và tiến trình chạy dao lùi và tiến f/ Mài mặt 2 của chi tiết gia công: Lau sạch bề mặt bàn từ và mặt 1 đã mài xong, đặt mặt 1 tiếp xúc với mặt bàn từ (hình7.13) Mài thô mặt 2: đặt chiều sâu cắt 0,1, để lượng dư mài tinh. Cách thực hiện như mài mặt 1 Hình 7.13. Sơ đồ mài thô mặt 2 g/ Mài mặt 3 của chi tiết gia công: Dùng mặt 1 và 2 làm chuẩn để gá mài mặt 3 vuông góc với mặt 1 và 2 Đặt chi tiết gia công lên bàn từ cho mặt 4 tỳ lên chốt tròn, tỳ mặt 1 va 2 vào 2 khối tỳ có các góc vuông chính xác (hình 7.14a), dùng búa gỗ gõ nhẹ vào 2 khối tỳ để cho tiếp xúc hết với chi tiết 66 Mài thô và mài tinh mặt 3 như mặt 2, kiểm tra độ vuông góc giữa mặt 3 với mặt 1 và 2 bằng ke vuông a) b) Hình 7.14: Sơ đồ gá đặt mài mặt phẳng song song và vuông góc h/ Mài mặt 4 của chi tiết gia công: Gá cho mặt 3 xuống tiếp xúc với bàn từ, mài thô và mài tinh mặt 4 như mặt 3 Kiểm tra độ song song giữa mặt 4 và 3,độ vuông góc giữa mặt 4 với mặt 1 và mặt số 2 i/ Mài mặt 5 của chi tiết gia công: Dùng mặt 1 và 2 làm chuẩn để gá mài mặt 5 vuông góc với mặt 1 và 2 Đặt chi tiết gia công lên bàn từ cho mặt 6 tỳ lên chốt tròn, tỳ mặt 1 và 2 vào 2 khối tỳ có các góc vuông chính xác như hình (hình 7.14b),,, dùng búa gỗ gõ nhẹ vào 2 khối tỳ để cho tiếp xúc hết với chi tiết. Mài thô và mài tinh mặt 5 như mặt 4, kiểm tra độ vuông góc giữa mặt 5 với mặt 1 và 2 và mặt 3, 4 bằng ke vuông j/ Mài mặt 6 của chi tiết gia công: Gá mặt 5 xuống bàn từ, mài thô và mài tinh thực hiện như các mặt trên (hình 7.15) 67 Hình 7.15: Gá đặt gia công mặt 6 k/ Tháo chi tiết, khử hết từ và làm sạch các bề mặt mài 4. Kiểm tra hoàn chỉnh Kiểm tra kích thước bằng panme đo ngoài, thước cặp hiện số Khi kiểm tra phải đặt dụng cụ đo đều tại các điểm trên bề mặt của chi tiết, không nên đo tại 1 điểm duy nhất Kiểm tra độ vuông góc bằng ke vuông. Đặt 1 cạnh của ke lên bàn từ, để cạnh thứ 2 của ke áp sát vào mặt bên của chi tiết, quan sát khe hở giữa giữa cạnh của ke và bề mặt của chi tiết để đánh giá được độ vuông góc ( hình 7.17) Hình 7.17. Kiểm tra vuông góc 5. Vệ sinh công nghiệp: Ngắt nguồn điện vào máy Dịch chuyển các thiết bị chạy dao về đúng vị trí, các cần điều khiển về vị trí an toàn Lau sạch bàn từ, máy, chi tiết và dụng cụ đo, tra dầu bôi trơn Vệ sinh nơi làm việc 68 6. Trình tự thực hiện khi mài 6 mặt phẳng song song vuông góc: TT Nội dung Phương pháp Nghiên cứu bản vẽ và chuẩn bị gia công - Kiểm tra tình trạng máy và chọn đá mài phù hợp với điều kiện gia công - Kiểm tra độ an toàn của đá mài, 1 cân bằng và rà sửa đá - Làm sạch mặt trên của bàn từ bằng vải hoặc cao su, nếu mặt bàn từ bị xước thì phải mài lại hết hoặc dũa sạch cho nhẵn bóng Gá phôi, điều chỉnh hành trình máy - Làm sạch bề mặt chi tiết gia công - Đặt mặt 1 lên gần tâm bàn từ, để § ¸ mµichiều ®i qua dọc hÕt của bÒ réng chi tiết // với chiều chi tiÕt gia c«ng § ¸ mµi chuyển động qua lại (trái – phải) Chi tiÕtcủa gia bàn c«ng máy 2 - Bật công tắc bàn từ và kiểm tra độ vững chắcBµn củatõ chi tiết được gá (dùng tay lắc) § ¸ mµi ®i qua hÕt bÒ réng chi tiÕt gia c«ng - Điều chỉnh khoảng chạy bàn § ¸ mµi máy sao cho tại điểm đầu và điểm Chi tiÕt gia c«ng cuối hành trình tâm của đá mài Bµn tõ cách mặt đầu chi tiết 30 – 50mm - Bật hệ thống thuỷ lực để bàn Cắt gọt. 3 máy và trục mang đá chuyển động. 69 - Điều chỉnh ụ đá đi xuống để lấy tiếp xúc bề mặt và tiến hành lấy chiều sâu mài. - Mài mặt 2 lấy mặt 1 làm chuẩn để mài mặt 2 - Mài mặt 3: Đặt chi tiết gia công lên bàn từ cho mặt 4 tỳ lên chốt tròn, tỳ mặt 1 va 2 vào 2 khối tỳ có các góc vuông chính xác, dùng búa gỗ gõ nhẹ vào 2 khối tỳ để cho tiếp xúc hết với chi tiết. - Mài mặt 4: Tương tự mài mặt 2 - Mài mặt 5: Đặt chi tiết gia công lên bàn từ cho mặt 6 tỳ lên chốt tròn, tỳ mặt 1 và 2 vào 2 khối tỳ có các góc vuông chính xác, dùng búa gỗ gõ nhẹ vào 2 khối tỳ để cho tiếp xúc hết với chi tiết. Mài mặt 6: Gá mặt 5 xuống bàn từ, mài thô và mài tinh thực hiện như các mặt trên như hình - Kiểm tra kích thước bằng panme đo ngoài, thước cặp hiện số Kiểm tra 4 - Khi kiểm tra phải đặt dụng cụ đo đều tại các điểm trên bề mặt của chi tiết, không nên đo tại 1 điểm 70 duy nhất - Kiểm tra độ vuông góc bằng ke vuông. Đặt 1 cạnh của ke lên bàn từ, để cạnh thứ 2 của ke áp sát vào mặt bên của chi tiết, quan sát khe hở giữa giữa cạnh của ke và bề mặt của chi tiết để đánh giá được độ vuông góc 71 Đánh giá kết quả học tập Kết quả Cách thức và thực hiện Điểm TT Tiêu chí đánh giá phương pháp đánh của tối đa giá người học I Kiến thức 1 Trình bày đầy đủ các yêu cầu Làm bài tự luận, đối khi mài mặt phẳng chiếu với nội dung 2 bài học 2 Trình bày được phương pháp Làm bài tự luận, đối mài mặt phẳng chiếu với nội dung 3 bài học 3 Trình bày cách gá lắp và điều Vấn đáp, đối chiếu chỉnh đá mài khi mài mặt 3 với nội dung bài học phẳng 4 Trình bày các dạng sai hỏng Làm bài tự luận, đối khi khi mài mặt phẳng và chiếu với nội dung 2 cách khắc phục bài học Cộng: 10 đ II Kỹ năng 1 Chuẩn bị đầy đủ dụng cụ, Kiểm tra công tác thiết bị đúng theo yêu cầu của chuẩn bị, đối chiếu 1 bài thực tập. với kế hoạch đã lập 2 Vận hành thành thạo máy mài Quan sát các thao tác, thành thạo đối chiếu với quy 1 trình vận hành 3 Chọn đúng chế độ cắt khi mài Kiểm tra các yêu cầu, đối chiếu với tiêu 1 chuẩn. 4 Sự thành thạo và chuẩn xác Quan sát các thao tác các thao tác khi vận hành máy đối chiếu với quy 2 mài trình thao tác. 5 Kiểm tra Theo dõi việc thực 5 72 hiện, đối chiếu với 5.1 Độ phẳng 2 quy trình kiểm tra 5.2 Độ song song và vuông góc 2 5.3 Kích thước 1 Cộng: 10 đ III Thái độ 1 Tác phong công nghiệp 5 1.1 Đi học đầy đủ, đúng giờ Theo dõi việc thực 1 1.2 Không vi phạm nội quy lớp hiện, đối chiếu với 1 học nội quy của trường. 1.3 Bố trí hợp lý vị trí làm việc Theo dõi quá trình làm việc, đối chiếu 1 với tính chất, yêu cầu của công việc. 1.4 Tính cẩn thận, chính xác Quan sát việc thực hiện bài tập 1 1.5 Ý thức hợp tác làm việc theo Quan sát quá trình tổ, nhóm thực hiện bài tập 1 theo tổ, nhóm 2 Đảm bảo thời gian thực hiện Theo dõi thời gian bài tập thực hiện bài tập, đối 2 chiếu với thời gian quy định. 3 Đảm bảo an toàn lao động và 3 vệ sinh công nghiệp 3.1 Tuân thủ quy định về an toàn Theo dõi việc thực 1 khi sử dụng khí cháy hiện, đối chiếu với quy định về an toàn 3.2 Đầy đủ bảo hộ lao động( quần và vệ sinh công 1 áo bảo hộ, giày, kính,) nghiệp 3.3 Vệ sinh xưởng thực tập đúng 1 quy định Cộng: 10 đ KẾT QUẢ HỌC TẬP 73 Kết quả Kết quả Tiêu chí đánh giá Hệ số thực hiện học tập Kiến thức 0,3 Kỹ năng 0,5 Thái độ 0,2 Cộng: 74 CÂU HỎI A. CÂU HỎI PHẦN LÝ THUYẾT. Câu 1: Trình bày ưu nhược điểm của phương pháp mài phẳng bằng mặt đầu của đá? Câu 2: Hãy hoàn thành câu trả lời đúng vào chỗ trống: a/Khi mài phẳng, thực hiện gá kẹp chi tiết gia công bằng ..........(n)............., dòng điện của bàn từ tính là .........(m)........... b/ Phía trên của bàn từ là ...........(p)..........xen kẽ giữa những lớp vật liệu ........(q)........, ......(h).....có thể chuyển dời để đóng mở chi tiết gia công. Câu 3: Nêu rõ cách giữ gìn và bảo quản bàn từ tính? Câu 4: Hãy đánh dấu (x) vào các ô trống để xác định nguyên nhân gây ra các dạng sai hỏng khi mài phẳng trong bảng dưới đây: Các dạng sai hỏng Kích Bề mặt Các bề Bề Bề Độ bóng Bề mặt thước chi tiết mặt mài mặt mặt không mài lớn mài bị không mài mài đạt( quá không Nguyên nhân hơn lồi lõm, song bị bị thô, đồng yêu không song cháy nứt nhiều đều, cầu phẳng vết không xước) phẳng Do đầu đá mài bị rơ, bị xê dịch khi cắt Đá mài quá mềm Chi tiết bị nung nóng nhiều do chiều sâu cắt quá lớn, Không đủ dung dịch 75 làm nguội Do đá mài quá cứng Chiều sâu cắt quá lớn Do bàn từ bị lồi lõm, bụi bẩn, không bằng phẳng Sống trượt băng máy bị rơ, mòn ổ bi trục chính bị mòn, đồ gá không chính xác, gá chi tiết sai Phôi không bằng phẳng, quá thô Chọn đá không phù hợp, hạt đá không đồng đều, sửa đá chưa đúng Dung dịch làm mát bẩn, bụi phoi nhiều Chế độ mài quá lớn Cấu trúc vật liệu gia công không đồng nhất Đá mòn không đều Độ cứng vững của máy kém, rung động 76 nhiều Chuyển động của bàn máy bị gián đoạn Dây đai bị mòn, trượt B. Học theo nhóm: Hoạt động nhóm nhỏ có 3 -5 học sinh/nhóm thảo luận về: - Kết cấu và cách bảo quản bàn từ tính -Phương pháp gá lắp chi tiết có nhiều dạng khác nhau lên bàn từ -Lập trình tự các bước tiến hành mài mặt phẳng theo bản vẽ chi tiết C. Xem trình diễn mẫu về: -Các thao tác thực hiện trên máy mài phẳng như: Cách gá phôi trên bàn từ, các loại đồ gá thông dụng kèm theo máy, thiết bị rà, sửa đá.. - Trình tự mài mặt phẳng song song, vuông góc D. Thực tập tại xưởng trường: -Thực hành từng bước về thao tác vận hành máy mài phẳng, chọn thử đá mài, gá phôi trên bàn từ, cân bằng đá và mài chi tiết theo yêu cầu của bản vẽ -Thực hành có hướng dẫn -Thực hành độc lập E. Tự nghiên cứu tài liệu liên quan đến kiến thức bài học 77 TÀI LIỆU THAM KHẢO [1]. Kỹ thuật mài -Trường công nhân kỹ thuật I - Hà nội-Tác giả: Nguyễn Văn Tính [2]. Thực hành cơ khí - Tiện phay bào mài-Nhà XB Đà Nẵng-2000- Tác giả Trần Thế San- Hoàng Trí - Nguyễn Thế Hùng
File đính kèm:
giao_trinh_mo_dun_mai_mat_phang.pdf