Đề tài Thiết kế Đồ án Chi tiết máy - Đào Xuân Hòa
1. Chọn động cơ điện
1.1. Chọn loại và kiểu động cơ
Động cơ điện có nhiều kiểu loại, nhưng dùng trong hộp giảm tốc thì ta phải
tính toán và chọn lựa sao cho phù hợp nhất để vừa thỏa mãn cả hai yếu tố kinh tế
và kỹ thuật. Dưới đây sẽ trình bày về một số loại động cơ và cách chọn.
a. Động cơ điện một chiều
Dùng dòng điện 1 chiều để làm việc (kích từ mắc song song, nối tiếp hoặc
hỗn hợp), hoặc dùng dòng điện một chiều điều chỉnh được (Hệ thống máy phát –
động cơ). Ưu điểm của loại này là cho phép thay đổi trị số của moomen và vận
tốc góc trong một phạm vi rộng. Ngoài ra dùng động cơ điện một chiều khi khởi
động êm, hãm và đảo chiều dễ dàng, do đó thích hợp dùng trong các thiết bị vận
chuyển bằng điện, thang máy, máy trục, các thiết bị thí nghiệm. Nhược điểm của
chúng là đắt, riêng loại động cơ điện một chiều lại khó kiếm và phải tăng thêm
chi phí đầu tư để lắp các thiết bị chỉnh lưu.
b. Động cơ điện không đồng bộ 1 pha
Thường dùng cho các thiết bị máy móc phục vụ cho các sinh hoạt hằng ngày
vì công suất của các loại động cơ này không lớn lắm. Do vậy không thích hợp để
làm việc trong điều kiện cần công suất lớn như hộp giảm tốc.
c. Động cơ điện xoay chiều ba pha
Trong công nghiệp sử dụng rộng rãi động cơ ba pha. Chúng gồm hai loại là:
Động cơ ba pha đồng bộ và không đồng bộ.
- Động cơ ba pha đồng bộ có vận tốc góc không đổi, không phụ thuộc vào trị
số của tải trọng và thực tế không điều chỉnh được. So với động cơ ba pha không
đồng bộ, động cơ ba pha đồng bộ có ưu diểm là hiệu suất và hệ số công suất cosφ
cao, hệ số quá tải lớn nhưng có nhược điểm: thiết bị tương đối phức tạp, giá thành
tương đối cao vì phải có thiết bị phụ để khởi động động cơ. Vì vậy động cơ ba
pha đồng bộ được sử dụng trong những trường hợp hiệu suất động cơ và trị số3
cosφ có vai trò quyết định (như trong các trường hợp yêu cầu công suất lớn trên
100kW, không cần điều chỉnh vận tốc, lại ít phải mở máy và dừng máy).
- Động cơ ba pha không đồng bộ gồm hai kiểu: Rôto dây cuốn và Rôto lồng
sóc.
Động cơ ba pha không đồng bộ rôto dây cuốn cho phép điều chỉnh vận tốc
trong một phạm vi nhỏ (khoảng 5%), có dòng điện mở máy nhỏ nhưng cosφ thấp,
giá thành cao, kích thước lớn và vận hành phức tạp, dùng khi cần điều chỉnh trong
một phạm vi hẹp để tìm ra vận tốc thích hợp của máy
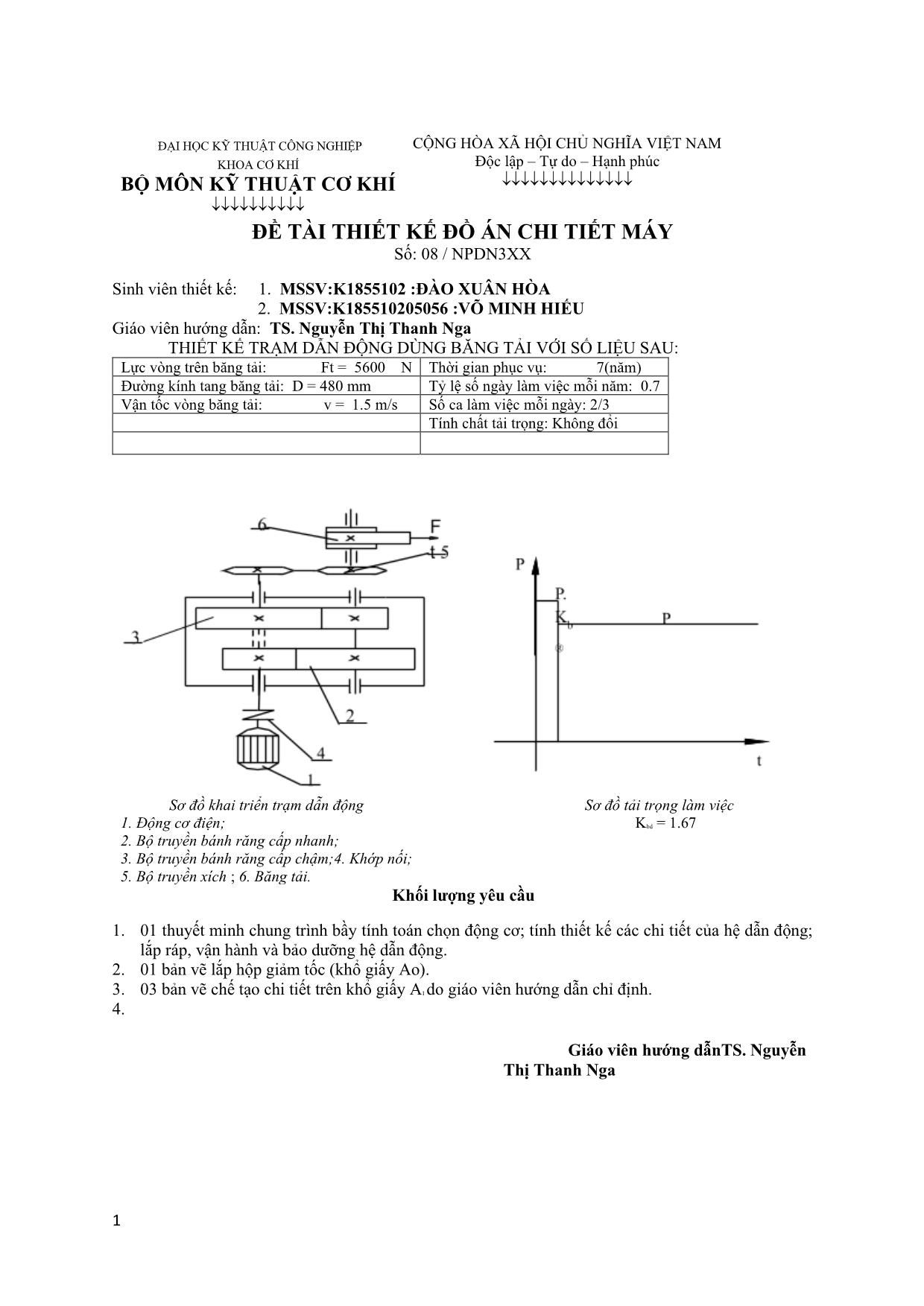
Trang 1
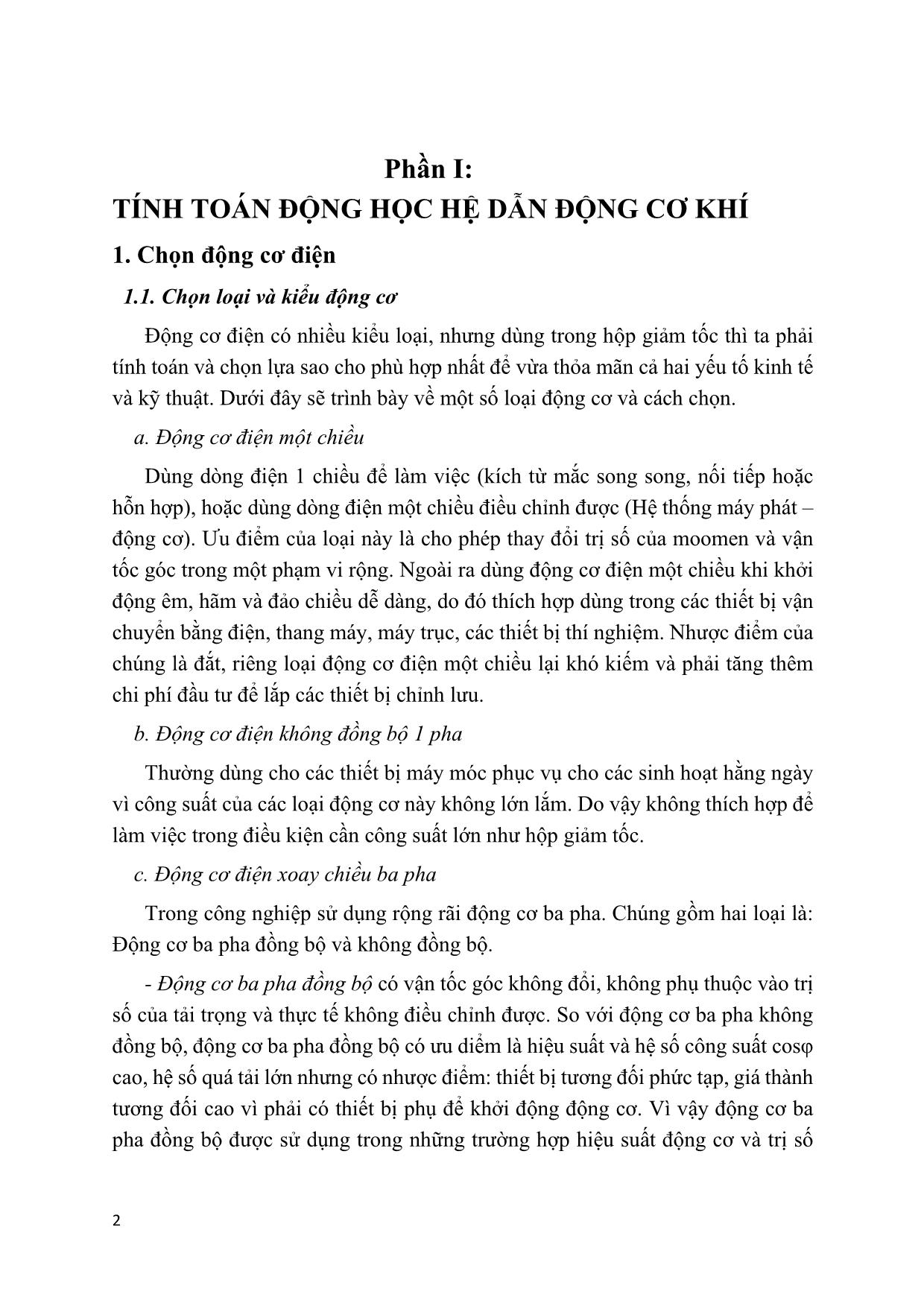
Trang 2

Trang 3
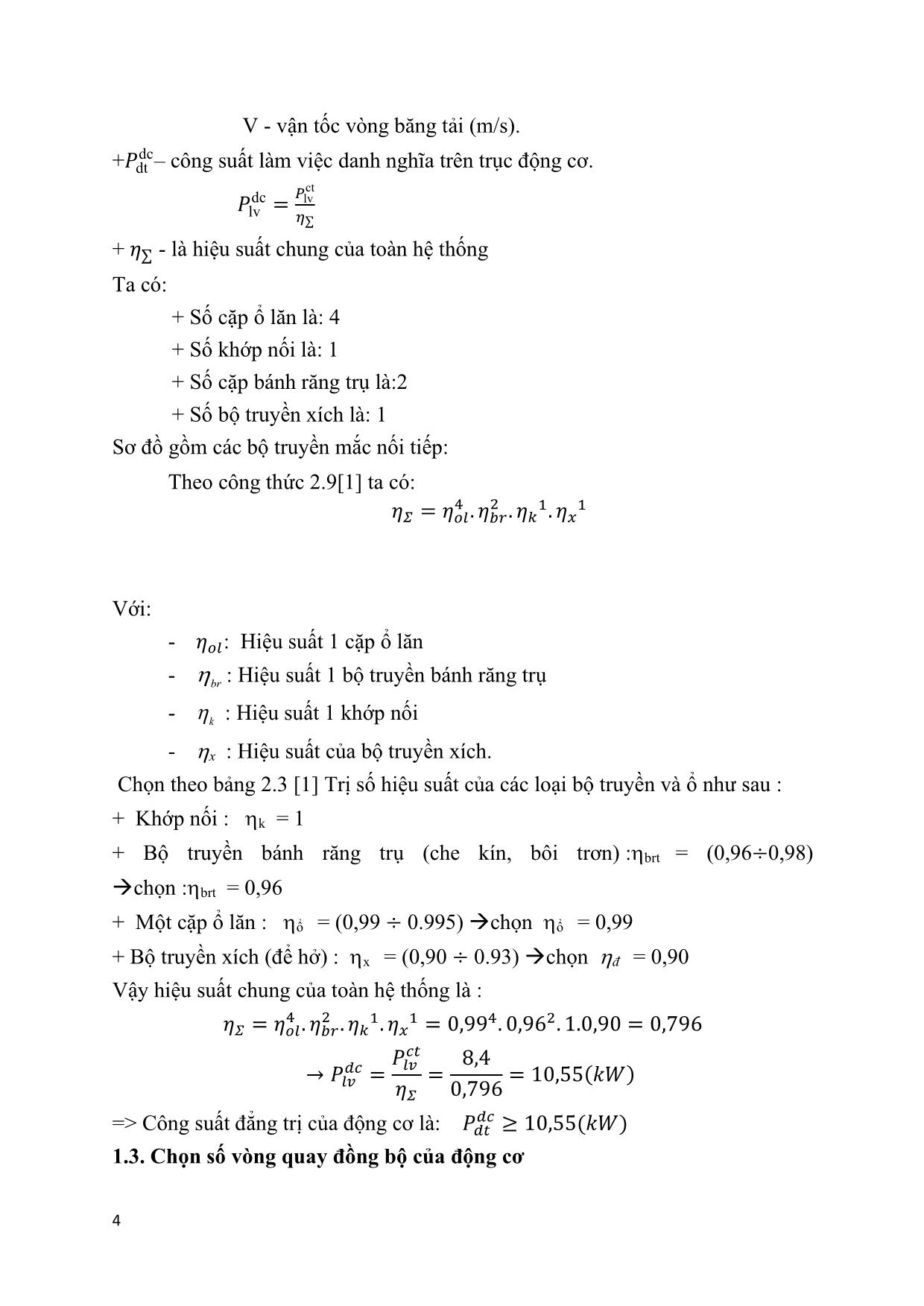
Trang 4
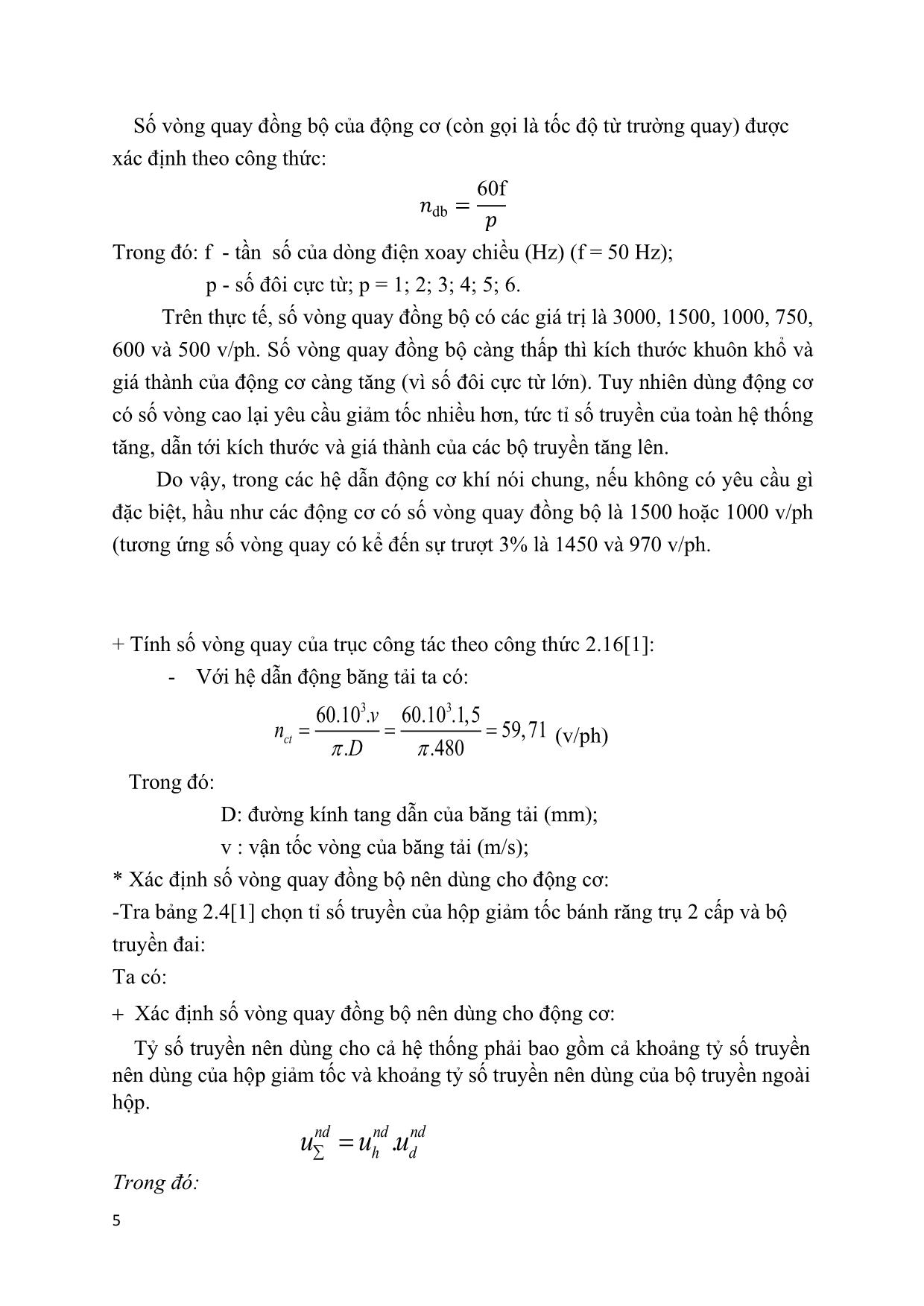
Trang 5
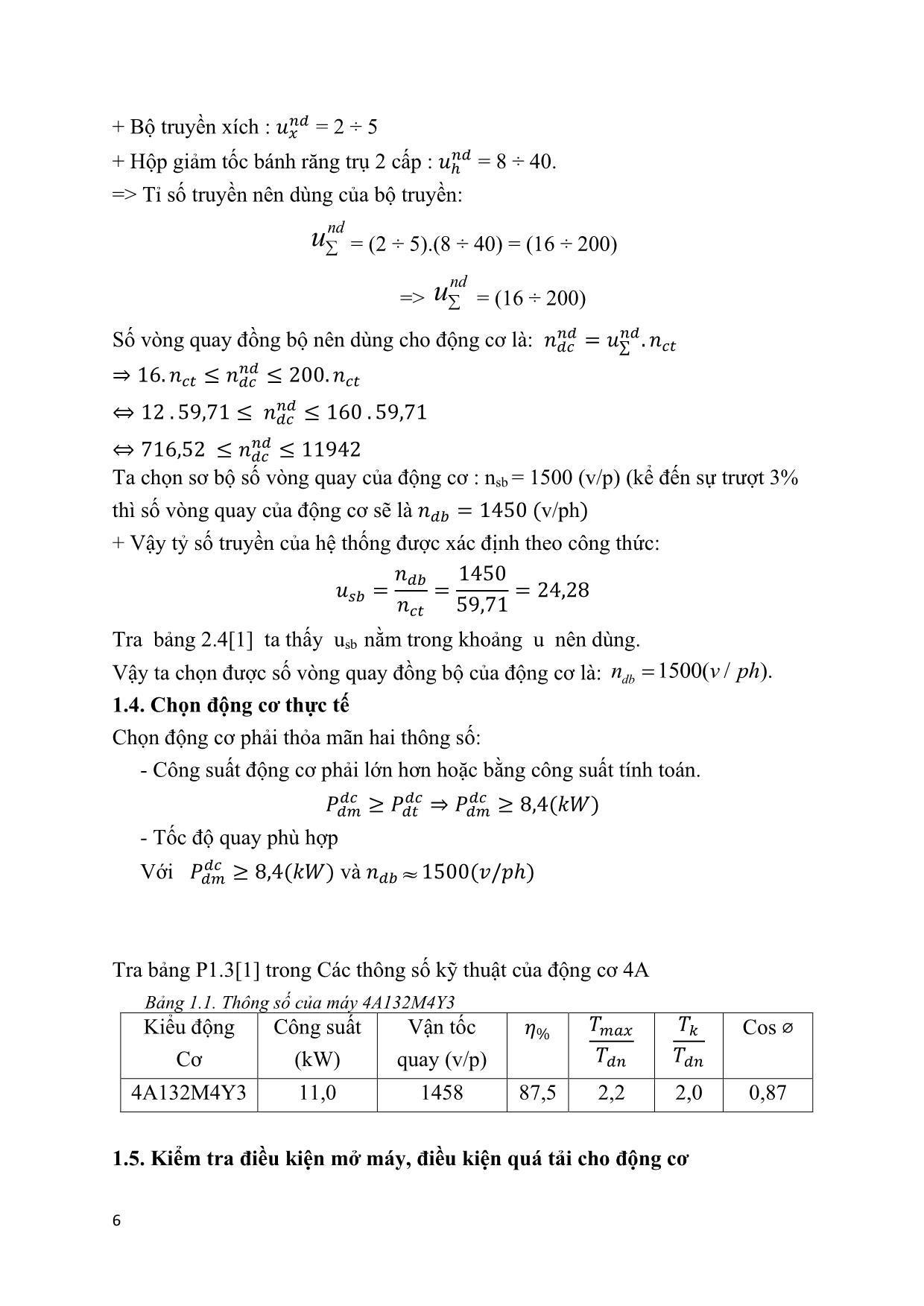
Trang 6
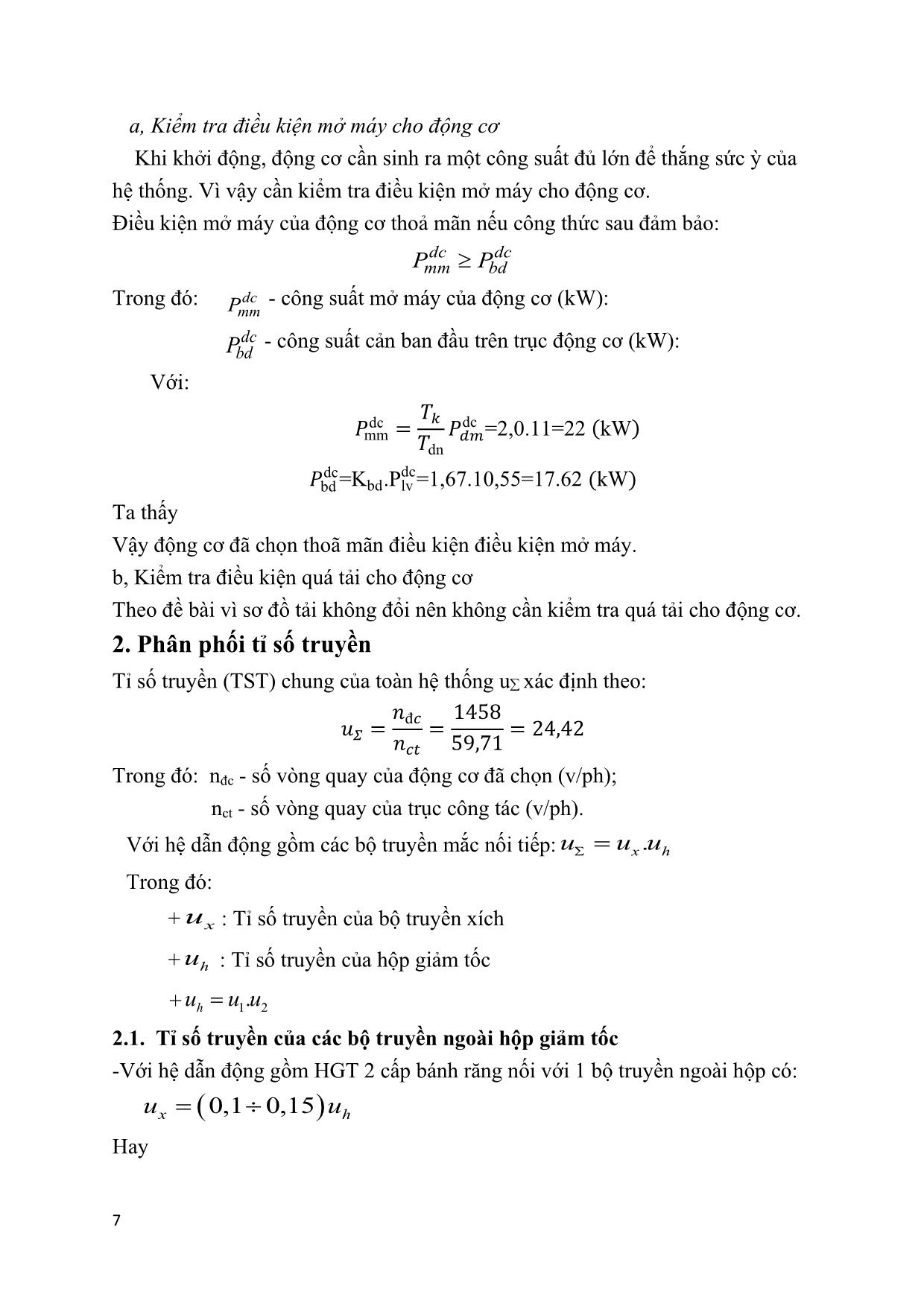
Trang 7
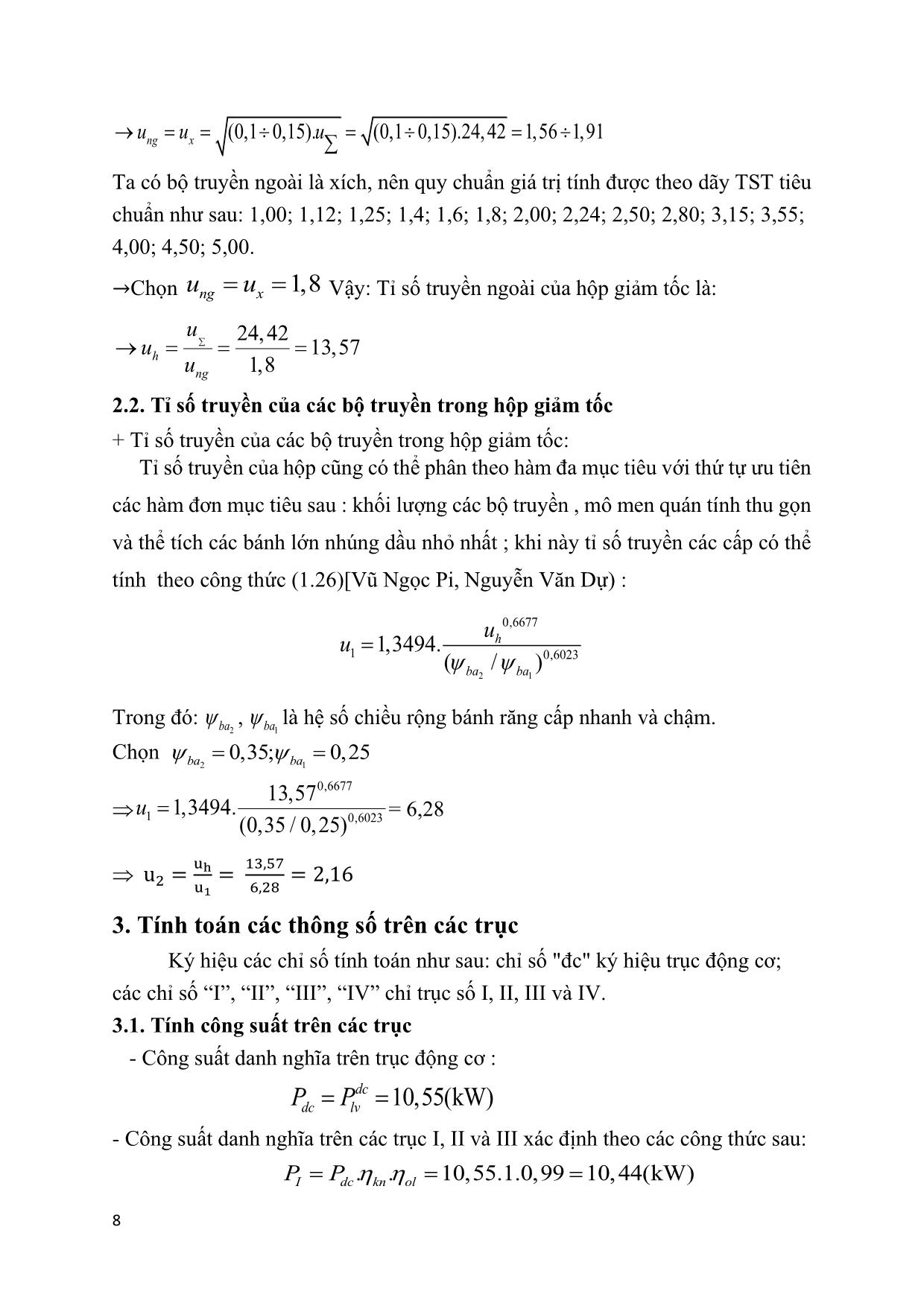
Trang 8
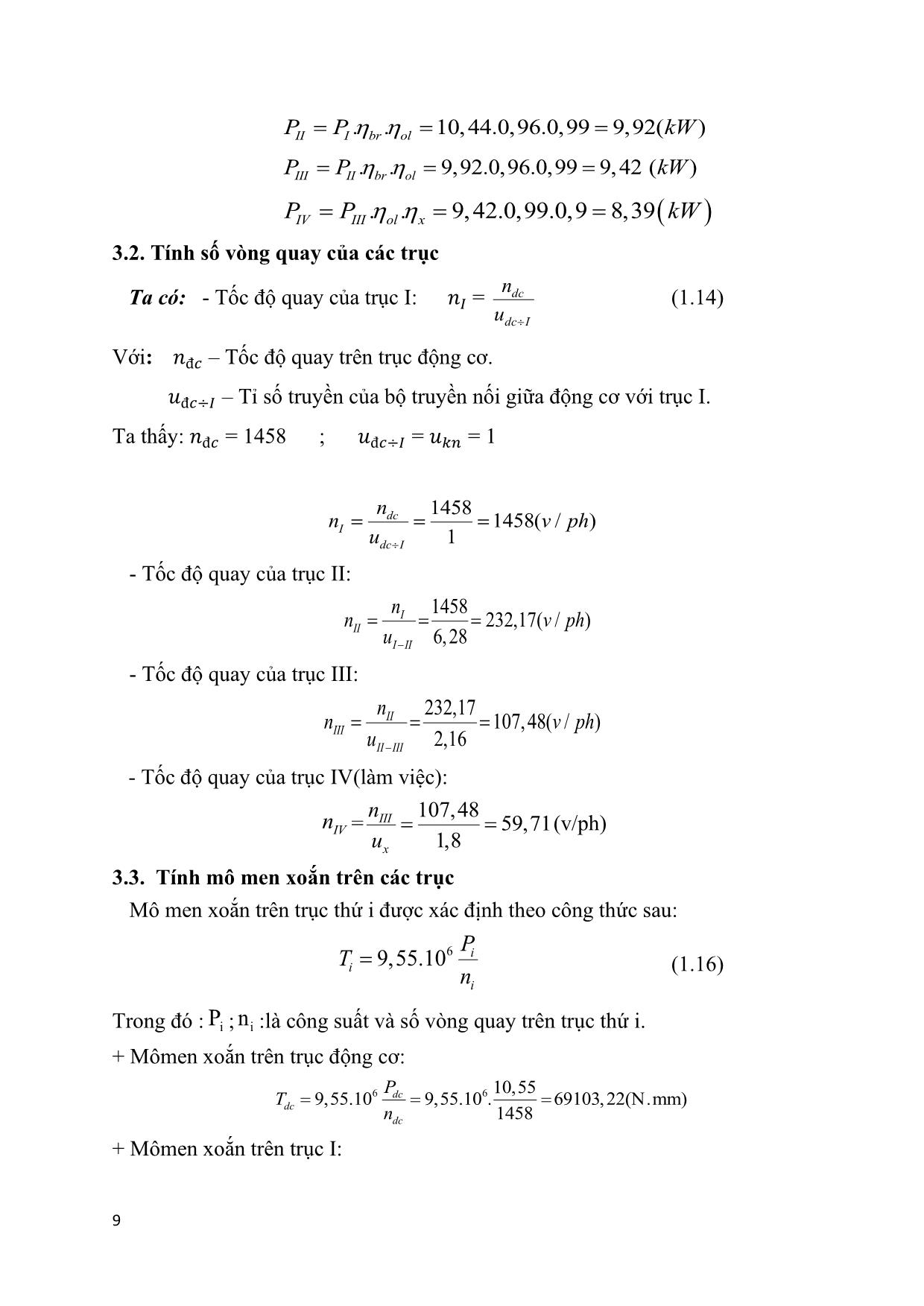
Trang 9
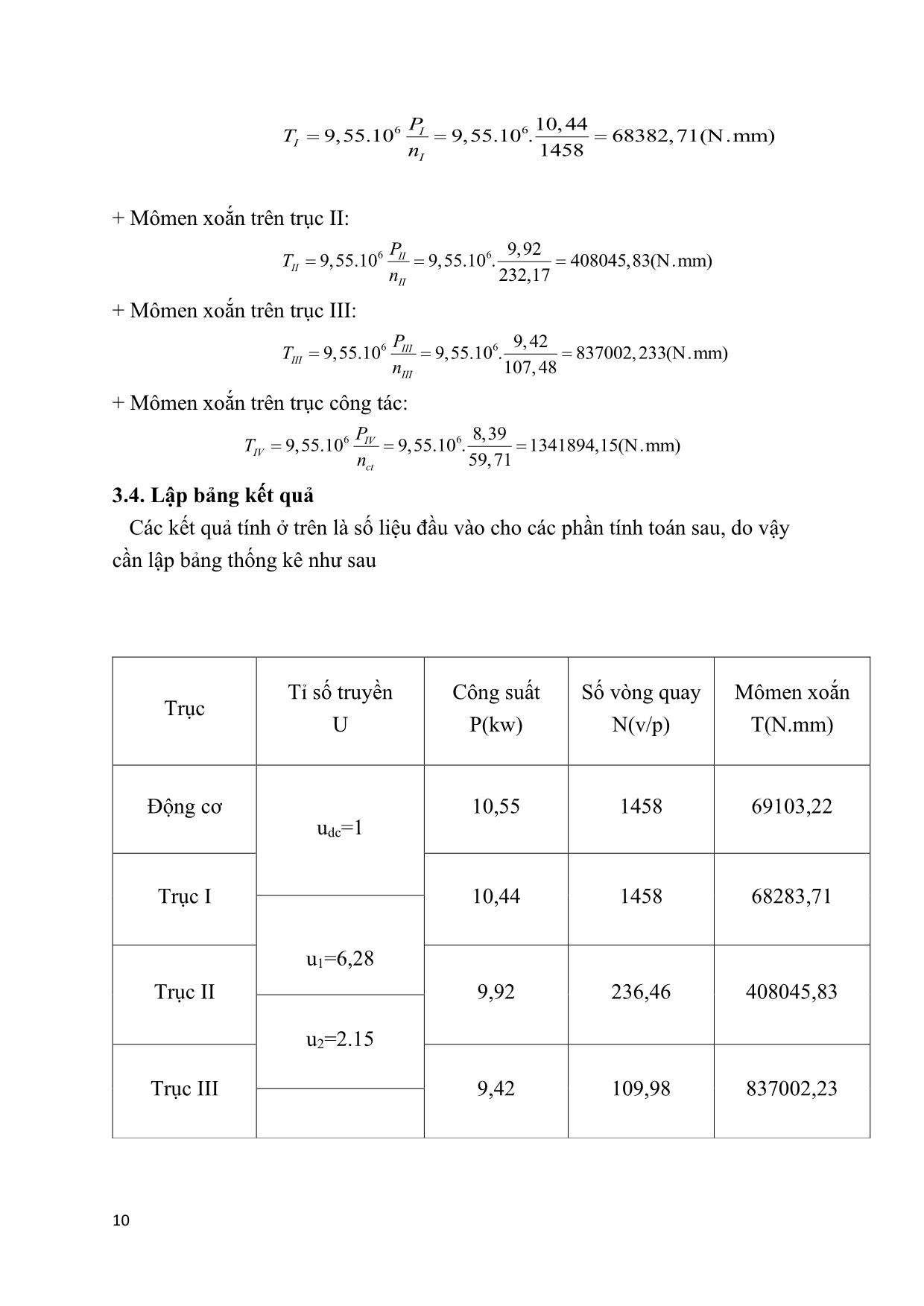
Trang 10
Tải về để xem bản đầy đủ
Tóm tắt nội dung tài liệu: Đề tài Thiết kế Đồ án Chi tiết máy - Đào Xuân Hòa
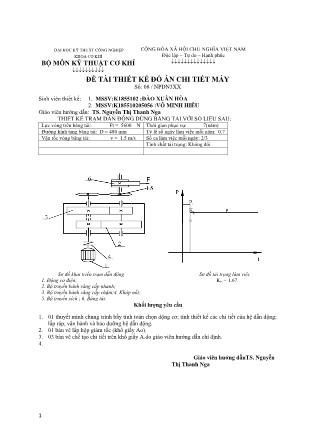
ng thép 45 => [τc] = 60 ÷ 90 (Mpa). Chọn [τc] = 60 (Mpa). + T là momen xoắn trên trục. + d là đường kính trục tại tiết diện đang xét + Llv là chiều dài làm việc của then + b là chiều dày của then 96 => ( ) 2.408045,83 35,98 MPa 45.36.14 c == Ta thấy τc then đảm bảo điều kiện bền cắt. Then đã chọn thỏa mãn điều kiện bền b. Tại chỗ lắp bánh răng Z3. Kích thước then. Đường kính trục tại chỗ lắp bánh răng Z3 là d = 52 (mm). Ta chọn then bằng Tra bảng 9.1b[1] ta có: + Kích thước tiết diên then: b = 16 (mm) ; h = 10(mm) + Chiều sâu rãnh then trên trục và lỗ: t1 = 6 (mm) ; t2 = 4,3 (mm) + Chiều dài mayơ : Lm23 = 80 (mm) + Chiều dài then : Lt = ( 0,8÷0,9).Lm23 = ( 0,8÷0,9).80 = 64÷ 72(mm) Chọn Lt = 70 (mm). => Chiều dài then làm việc : Llv = Lt – b = 70– 16 = 54 (mm) Kiểm nghiệm sức bền dập cho then. Điều kiện bền dập. 1 2. . .( ) d d t T d L h t = − Trong đó: + [σd] là ứng suất dập cho phép. Tra bảng 9.5[1] ta có : [σd] = 150 ( Mpa) + T là momen xoắn trên trục. + d là đường kính trục tại tiết diện đang xét + Llv là chiều dài làm việc của then + h là chiều cao của then + t1 là chiếu sâu rãnh then trên trục. => 2.408045,83 52.54.(10- 2,6 6) 7 5d = = ( Mpa) Ta thấy σd then đảm bảo điều kiện bền dập. 97 Kiểm nghiệm sức bền cắt cho then. c lv c bLd T = .. .2 Trong đó: + [τ] là ứng suất cắt cho phép. Với then bằng thép 45 => [τc] = 60 ÷ 90 (Mpa). Chọn [τc] = 60 (Mpa). + T là momen xoắn trên trục. + d là đường kính trục tại tiết diện đang xét + Llv là chiều dài làm việc của then + b là chiều dày của then => 2.408045,83 52.54.1 1 , 6 6 8 1c = = (Mpa). Ta thấy τc then đảm bảo điều kiện bền cắt. Then đã chọn thỏa mãn điều kiện bền. 5.2. Tính then cho trục III. Tại chỗ lắp bánh răng Z4 Kích thước then. Đường kính trục tại chỗ lắp bánh răng Z4 là d = 60 (mm). Ta chọn then bằng Tra bảng 9.1a[1] ta có: + Kích thước tiết diên then: b = 18 (mm) ; h = 11 (mm) + Chiều sâu rãnh then trên trục và lỗ: t1 = 7 (mm) ; t2 = 4,4 (mm) + Chiều dài mayơ : Lm32 =74 (mm) + Chiều dài then : Lt = ( 0,8÷0,9).Lm32 = ( 0,8÷0,9).74 = 59,2 ÷ 66,6 (mm) Chọn Lt = 63 mm. => Chiều dài then làm việc : Llv = Lt – b = 63 – 18 = 45 (mm) Kiểm nghiệm sức bền dập cho then. Điều kiện bền dập. 98 1 2. . .( ) d d lv T d L h t = − Trong đó: + [σd] là ứng suất dập cho phép. Tra bảng 9.5[1] ta có : [σd] = 150 ( Mpa) + T là momen xoắn trên trục. + d là đường kính trục tại tiết diện đang xét + Llv là chiều dài làm việc của then + h là chiều cao của then + t1 là chiếu sâu rãnh then trên trục. Ta sử dụng 2 then đặt cách nhau 180 => 2.0,75.837002, 23 116, 25 60.45.(11 7) d = = − ( Mpa) Ta thấy σd then đảm bảo điều kiện bền dập. Kiểm nghiệm sức bền cắt cho then. c lv c bLd T = .. .2 Trong đó: + [τ] là ứng suất cắt cho phép. Với then bằng thép 45 => [τc] = 60 ÷ 90 (Mpa). Chọn [τc] = 60 (Mpa). + T là momen xoắn trên trục. + d là đường kính trục tại tiết diện đang xét + Llv là chiều dài làm việc của then + b là chiều dày của then => 2.837002,23 34,44 60.45.18 c = = (Mpa). Ta thấy τc then đảm bảo điều kiện bền cắt. Then đã chọn thỏa mãn điều kiện bền Tại chỗ lắp với bộ truyền xích Kích thước then. 99 Đường kính trục tại chỗ lắp khớp nối là d = 55 (mm). Ta chọn then bằng Tra bảng 9.1a[1] ta có: + Kích thước tiết diên then: b = 16 (mm) ; h = 10 (mm) + Chiều sâu rãnh then trên trục và lỗ: t1 = 6 (mm) ; t2 = 4,3 (mm) + Chiều dài mayơ : Lm33 =70 (mm) + Chiều dài then : Lt = ( 0,8÷0,9).Lm32 = ( 0,8÷0,9).70 = 80 ÷ 90 (mm) Chọn Lt = 80 mm. => Chiều dài then làm việc : Llv = Lt – b = 80 – 16 = 64 (mm) Kiểm nghiệm sức bền dập cho then. Điều kiện bền dập. 1 2. . .( ) d d lv T d L h t = − Trong đó: + [σd] là ứng suất dập cho phép. Tra bảng 9.5[1] ta có : [σd] = 150 ( Mpa) + T là momen xoắn trên trục. + d là đường kính trục tại tiết diện đang xét + Llv là chiều dài làm việc của then + h là chiều cao của then + t1 là chiếu sâu rãnh then trên trục. => 2.837002,23 118,89 55.64.(10 6) d = = − ( Mpa) Ta thấy σd then đảm bảo điều kiện bền dập. Kiểm nghiệm sức bền cắt cho then. c lv c bLd T = .. .2 Trong đó: + [τ] là ứng suất cắt cho phép. Với then bằng thép 45 => [τc] = 60 ÷ 90 (Mpa). Chọn [τc] = 60 (Mpa). 100 + T là momen xoắn trên trục. + d là đường kính trục tại tiết diện đang xét + Llv là chiều dài làm việc của then + b là chiều dày của then => 2.837002,23 29,72 55.64.16 c = = (Mpa). Ta thấy τc then đảm bảo điều kiện bền cắt. Then đã chọn thỏa mãn điều kiện bền IV. TÍNH CHỌN KHỚP NỐI D Do d dm l1 l2 l B L l l3 h D2 d1 dc Hình 4.8: Khớp nối đàn hồi Khớp nối là chi tiết tiêu chuẩn vì vậy trong thiết kế thường dựa vào đường kính trục động cơ để tính. Ở đây ta chọn khớp nối trục đàn hồi hai nửa nối trục với nhau bằng bộ phận đàn hồi có thể là kim loại hoặc không phải kim loại(cao su), vật liệu làm nối trục là gang xám GX21-40. Vật liệu chế tạo chốt là thép 45 thường hoá. 1.Tính chọn khớp nối cho trục I Kích thước cơ bản của nối trục đàn hồi được tính dựa theo: Tt = k.T T -Trong đó: 101 T: mômen xoắn danh nghĩa TI = 68283,71(N.mm) =68,28371 (N.m) k : chế độ làm việc , phụ thuộc vào loại máy công tác ,trị số được tra trong bảng 16.1 [2] ,k = 1,2 ÷1,5 chọn kbd = 1,5 Tt = 68,28 .1,5 = 102,42(N.m) Dựa vào mômen xoắn Tt = 102,42 (N.m) và đường kính d = 20 (mm), tra bảng 16.10a [2], ta được kích thước nối trục vòng đàn hồi như bảng sau: T (Nm) D dm L l d1 D0 Z nmax B B1 l1 D3 l2 102,42 100 36 104 50 40 71 6 5700 4 28 21 20 20 Tra bảng 16.10b[3] ta có kích thước cơ bản của vòng đàn hồi: Bảng 6.2. Kích thước cơ bản của vòng đàn hổi . dc d1 D2 l l1 l2 l3 h 14 M10 20 62 34 15 28 2 * Kiểm nghiệm điều kiện bền của vòng đàn hồi và chốt. - Điều kiện sức bền dập của vòng đàn hồi d = d c ldDZ Tk 30 ... ..2 - Điều kiện sức bền uốn của chốt u = 0 3 0 . . 0,1. . . u c k T l D d Z -Trong đó: d = có thể lấy (2 4) MPa ứng suất dập cho phép của vòng cao su. u = (60 80) MPa ứng suất dập cho phép của chốt. Z, D0, dc, l đã cho trong bảng 4.5 và bảng 4.6 102 2 0 1 15 34 41,5 2 2 l l l= + = + = k = 1,5 hệ số phụ thuộc vào chế độ làm việc của máy +) Điều kiện sức bền dập của vòng đàn hồi : 2.1,5.68283,71 1,2 4 6.71.14.28 d d MPa = = = thỏa mãn điều kiện bền dập +) Điều kiện sức bền của chốt : 3 41,5.1,5.68283,71 36,36 80 0,1.71.14 .6 u u MPa = = = thỏa mãn điều kiện bền chốt Kết luận: Vậy khớp nối trục đảm bảo yêu cầu làm việc PHẦN IV CẤU TẠO VỎ HỘP, CÁC CHI TIẾT VÀ CÁC CHẾ ĐỘ LẮP TRONG HỘP 4.1. Tính thiết kế vỏ hộp giảm tốc. - Vỏ hộp giảm tốc có nhiệm vụ đảm bảo vị trí tương đối giữa các chi tiết và bộ phận máy, tiếp nhận tải trọng do các chi tiết lắp trên vỏ hộp truyền đến, đựng dầu bôi trơn, và bảo vệ các chi tiết máy tránh bụi bẩn. 4.1.1 : Tính kết cấu của vỏ hộp. - Chỉ tiêu của hộp giảm tốc là độ cứng cao và khối lượng nhỏ. Chọn vật liệu để đúc hộp giảm tốc là gang xám GX15-32. - Chọn bề mặt ghép của vỏ hộp đi qua tâm trục. 4.1.2: Kết cấu bánh răng. Chọn phương pháp rèn hoặc dập để chế tạo phôi bánh răng. 4.1.3 : Các kích thước cơ bản của vỏ hộp. - Dùng phương pháp đúc để chế tạo lắp ổ, vật liệu GX15-32. Dựa vào bảng 18.1[2], và 18.2[2] ta xác định được kích thước của hộp như sau. 103 Tên gọi Biểu thức tính toán Chiều dày. + Thân hộp + Nắp hộp 1 0,03. 3 0,03.193 3 8,79wa = + = + = (mm) Chọn = 9 mm 1 0,9. 0,9. 8,19 == = (mm) Chọn 1 = 8(mm) Gân tăng cứng: + Chiều dày gân e + Chiều cao gân h + Độ dốc (0,8 1). (0,8 1).9 7,2 9e = = = Chọn e = 9(mm) h 58 ( mm); Khoảng 20 Đường kính : + Bulông nền, d1 + Bulông cạnh ổ,d2 + Bulông ghép bích nắp và thân,d3 + Vít ghép nắp ổ, d4 1 0,04. 10 0,04.193 10 17,72wd a + = + = (mm) Chọn d1 =18 (mm) chọn bulông M18. d2 = (0,70,8). d1 = (0,70,8).18 = 12,614.4 ( mm) Chọn d2 = 14mm và chọn bulông M14 d3 = (0,8 0,9).d2 = (0,8 0,9).14 = 11,2 12,6(mm) Chọn d3 = 12 mm và chọn bulông M12 d4 = (0,6 0,7).d2 = (0,6 0,7).12 = 7,2 8.4 ( mm) Chọn d4 = 8 mm và chọn vít M8 d5 = (0,5 0,6).d2 = (0,5 0,6).14 104 + Vít ghép nắp cửa thăm, d5 = 7 8,4 ( mm) Chọn d5 = 8 mm và chọn vít M8 Mặt bích ghép nắp và thân: + Chiều dày bích thân hộp,S3 + Chiều dày bích nắp hộp, S4 + Bề rộng bích nắp và thân, K3 S3 =(1,4 1,8).d3 = (1,4 1,8).12 = 16,8 21,6 (mm) Chọn S3 = 20 mm S4 = (0,9 1).S3 = (0,9 1).20 = 18 20 ( mm), Chọn S4 =20 mm 2 21,6. 1,6.14 22,4E d mm= = = ; 2 21,3. 1,3.14 18,2R d mm= = = ( ) ( ) ( ) 2 2 2 3 5 22,4 18,2 3 5 42,6 44,6 K E R = + + = + + = Chọn 2 42K mm ( ) ( )3 2 3 5 42 3 5 (39 37)K K mm − = − = , nên chọn 3 37K mm= Mặt đế: + Chiều dày đế ( có phần lồi ) + Bề rộng mặt đế hộp, K1 và q S1 = (1,41,7).d1= (1,41,7).18 = = 25,230,6( mm) Chọn S1 = 30 mm S2 = (1 ÷ 1,1).d1 = (1÷1,1).18 = 18÷19,8 Chọn S2 = 18 mm K1 3.d1 3.18 = 54 ( mm) q K1 + 2. = 54 + 2.9= 73 ( mm) 105 Khe hở giữa các chi tiết + Giữa bánh răng và thành trong hộp + Giữa đỉnh bánh răng lớn với đáy hộp ( 11,2). = (11,2).9 = 9 10,8 ( mm) Chọn = 11( mm) 1 = (35). = (35).9= 27 45 ( mm) Chọn 1 = 45 ( mm) + Giữa mặt bên các bánh răng với nhau 2 > = 9 lấy 2 =13 ( mm) Số lượng bu lông nền Z 542,05 357 2,99 4,49 (200 300) (200 300) L B Z + + = = = Chọn Z = 4 L = 2 + 2 + 2 42 aa dd + + a 337,07 267,04 2.9 2.10 193 533 2 + = + + + = Ta chọn L=533 21 2 12B l b k= + + 310 27 2.10 357= + + = Ta chọn B=357 ( L,B: chiều dài và rộng của hộp). 4.2.2. gối trục. Gối trục phải đảm bảo độ cứng để không ảnh hưởng đến sự làm việc của ổ. Dựa vào kích thước các trục đã tính toán trong phần thiết kế trục và bảng 18.2[2] ta có kích thước gối trục. Trục D D2 D3 h d4 Z I 62 75 90 8 M6 4 II 90 110 135 12 M8 6 III 100 120 150 12 M10 6 106 Bảng 5.2: Thông số kích thước gối trục. Dùng phương pháp đúc để chế tạo nắp ổ, vật liệu là GX15-32.l Nắp ổ- vòng phớt 4.2.3. Vòng phớt. Để nhằm bảo vệ ổ khỏi bụi bặm, chất bẩn, hạt cứng và các tạp chất khác xâm nhập vào ổ. Những chất này làm ổ chóng bị mài mòn và bị han rỉ. Ngoài ra còn đề phòng dầu chảy ra ngoài ta dùng vòng phớt. Tra bảng 15-17[2]. Trục d d1 d2 D a b S0 I 25 26 24 38 6 4,3 9 III 55 56,5 54 74 9 6,5 12 4.2.4. Vòng chắn dầu. Vòng gồm 3 rãnh tiết diện tam giác có góc ở đỉnh là 60 0 . Khoảng cách giữa các đỉnh là 3 mm. Vòng cách mép trong thành hộp 2 mm. Khe hở giữa vỏ với mặt ngoài của vòng ren là 0.4 mm. 107 Vòng chắn dầu 4.2.5. Nút thông hơi. Khi làm việc, nhiệt độ trong hộp tăng lên. Để giảm áp suất và điều hoà không khí bên trong và bên ngoài hộp người ta dùng nút thông hơi. Nút thông hơi được lắp trên nắp cửa thăm hoặc ở vị trí cao nhất của nắp hộp. Tra bảng 18.6 [2] A B C D E G H I K L M N O P Q R S M27x2 15 30 15 45 36 32 6 4 10 8 22 6 32 18 36 32 108 Hình dạng và kích thước nút thông hơi 4.2.6. Que thăm dầu. Kết cấu đã được tiêu chuẩn hoá và được cho như hình vẽ : Hình dạng và kích thước que thăm dầu 4.2.7. Nút tháo dầu. Sau một thời gian làm việc, dầu bôi trơn chứa trong hộp bị bẩn (do bụi bặm và do hạt mài), hoặc dị biến chất do đó cần phải thay dầu mới. Để tháo dầu cũ, ở đáy hộp có lỗ tháo dầu. Lúc làm việc, lỗ được bịt kín bằng nút tháo dầu. Kết cấu và kích thước của nút tháo dầu tra trong bảng 18.7[2]. P O R NC Q ØG ØQ Ø 3 6 l ç H ØA M I L ØA B K 109 d b m f L c q D S Do M16x1,5 12 8 3 23 2 13,8 26 17 19,6 Hình dạng và kích thước nút tháo dầu 4.2.7.Cửa thăm. Để kiểm tra, quan sát các tiết máy trong hộp khi lắp ghép và để đổ dầu vào hộp, trên đỉnh hộp có nắp cửa thăm. Dựa vào bảng 18-5[2] ta chọn kích thước của cửa thăm như hình vẽ: K A1 C1 A B R B 1 110 Kích thước nắp quan sát A B A1 B1 C C1 K R Vít Số lượng 100 75 150 100 125 87 12 M8 x 22 4 4.2.9. Chốt định vị Mặt ghép giữa nắp và thân nằm trong mặt phẳng chứa đường tâm các trục. Lỗ trụ lắp ở trên nắp và thân hộp được gia công đồng thời, để đảm bảo vị trí tương đối của nắp và thân trước và sau khi gia công cũng như khi lắp ghép, ta dùng 2 chốt định vị, nhờ có chốt định vị khi xiết bulông không làm biến dạng vòng ngoài của ổ. Tra bảng 18.4b[1] d c l 4 0,6 16 ÷ 70 Kích thước chốt định vị 4.3. Chọn dầu mỡ bôi trơn hộp giảm tốc. Phương pháp bôi trơn : vì vận tốc vòng v <12 m/s ta dùng phương pháp bôi trơn ngâm dầu chứa trong hộp. Dầu bôi trơn : Tra bảng 18.11[1] chọn độ nhớt để bôi trơn là: l c x45° 1:50 3,2 d 111 Độ nhớt Centistoc Độ nhớt Engle Bộ truyền cấp nhanh 80 11 Bộ truyền cấp chậm 160(20) 16(3) Tra bảng 18.13[1]. Loại dầu bôi trơn Bộ truyền cấp nhanh Dầu ô tô máy kéo AK-15 Bộ truyền cấp chậm Dầu ô tô máy kéo AK-15 Chọn dầu mỡ bôi trơn cho ổ lăn Khi ổ lăn được bôi trơn đúng kỹ thuật nó sẽ không bị mài mòn vì chất bôi trơn sẽ giúp tránh không để các chi tiết kim loại tiếp xúc trực tiếp với nhau. Ma sát trong ổ lăn sẽ giảm, khả năng chống mài mòn của ổ tăng lên, khả năng tản nhiệt tốt hơn, giảm được tiếng ồn, bảo vệ bề mặt không bị han rỉ. Chất bôi trơn được lựa chọn dựa trên nhiệt độ làm việc và số vòng quay của ổ. Mỡ bôi trơn có nhiều ưu điểm hơn dầu như được giữ trong ổ dễ hơn, làm việc được lâu hơn, độ nhớt ít bị thay đổi vì nhiệt, tránh cho ổ khỏi tạp chất và độ ẩm. Chính vì vậy ta chọn mỡ để bôi trơn ổ lăn. Tra bảng 15.15.a[1] chọn loại mỡ CLGMT2.Loại này đặc biệt thích hợp cho các loại ổ cỡ nhỏ hoặc trung bình, ngay cả ở điều kiện làm việc cao hơn, CLGMT2 có tính năng chịu nước rất tốt cũng như chống gỉ cao. Để bôi trơn, mỡ được cho vào chiếm 2/3 khoảng trống của bộ phận ổ. Mỡ được đưa vào nhờ 1 vít trên lắp ổ. e 112 TÀI LIỆU THAM KHẢO [1] Trịnh chất, Lê văn uyển , tính toán hệ dẫn động cơ khí tập 1, NXB giáo dục ,1999. [2] Vu Ngoc Pi, A method for optimal calculation of total transmission ratio of two step helical gearboxes, Proceedings of The National conference on Engineering Mechnics, Volume 1, Hanoi, October 12-13, 2001, pp. 133-136. [3] Vũ Ngọc Pi, Vũ Quý Đạc, Phân phối tỉ số truyền cho hộp giảm tốc trục vít hai cấp theo chỉ tiêu kết cấu của hộp hợp lý nhất, Tạp chí Khoa học và Công nghệ, Đại học Thái nguyên, Số 1 (41) 2007, Trang 65-69. [4] Vu Ngoc Pi, Nguyen Dang Binh, Vu Quy Dac, Phan Quang The, Phương pháp phân tách tối ưu Tổng tỷ số truyền của hộp số xoắn đồng trục, Trường Khoa học và Kỹ thuật Tính toán: Lý thuyết và Ứng dụng, Tháng 3 3-5, 2005, Thành phố Hồ Chí Minh, trang 96-99.
File đính kèm:
de_tai_thiet_ke_do_an_chi_tiet_may_dao_xuan_hoa.pdf