Requirements of human resource in Vietnam mechanical industry in the context of industry 4.0
Abstract
The fourth industrial revolution is different from other industrial revolutions in speed,
scope and influence to many aspects of life. It brings mass difference in manufacturing
process and requires the mechanical industry change in human resource. Industry 4.0 is
expected to lift people from the production lines, also creates a breaking by supplying chance
for the development of each individual with support of information, knowledge and new
technology. Mechanical human resource in Vietnam with low quality, weak soft skills and
low flexibility is hindering the development and integration of the mechanical industry in the
new stage. New requirement of knowledge and skills for Vietnamese mechanical engineers in
an age of smart manufacturing is to improve the efficiency, quality, and utilization of
operation in modern mechanical factories.
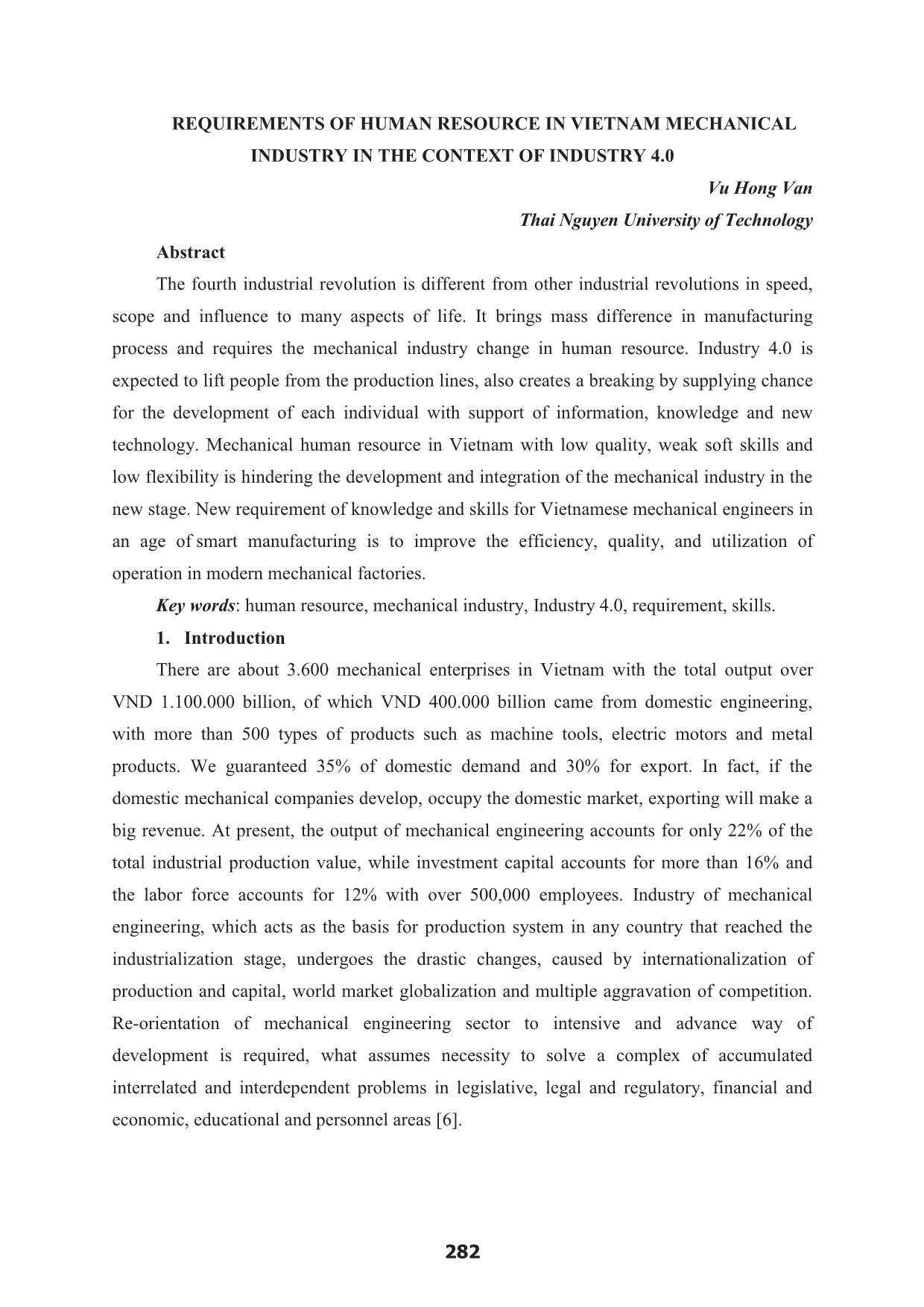
Trang 1
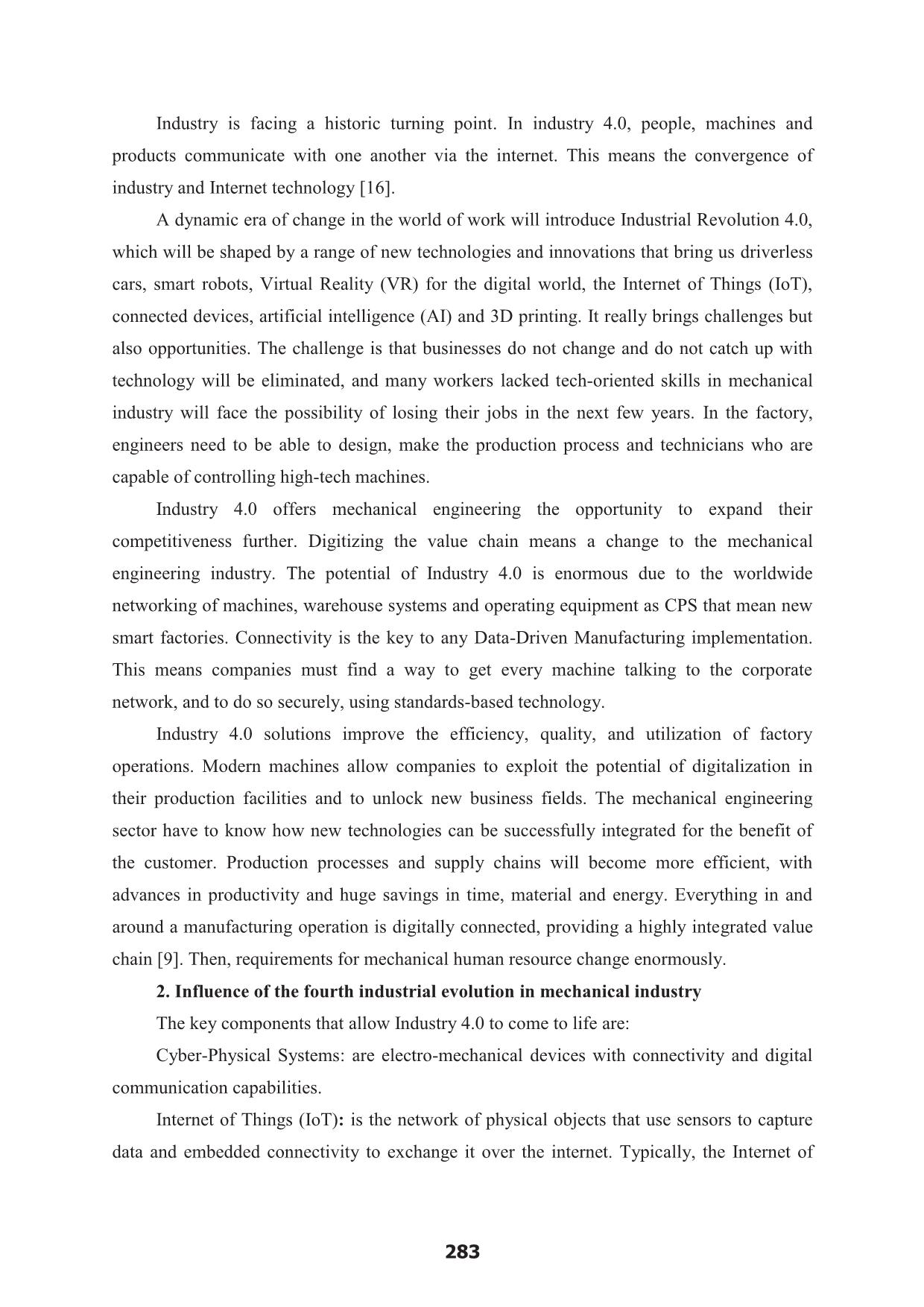
Trang 2
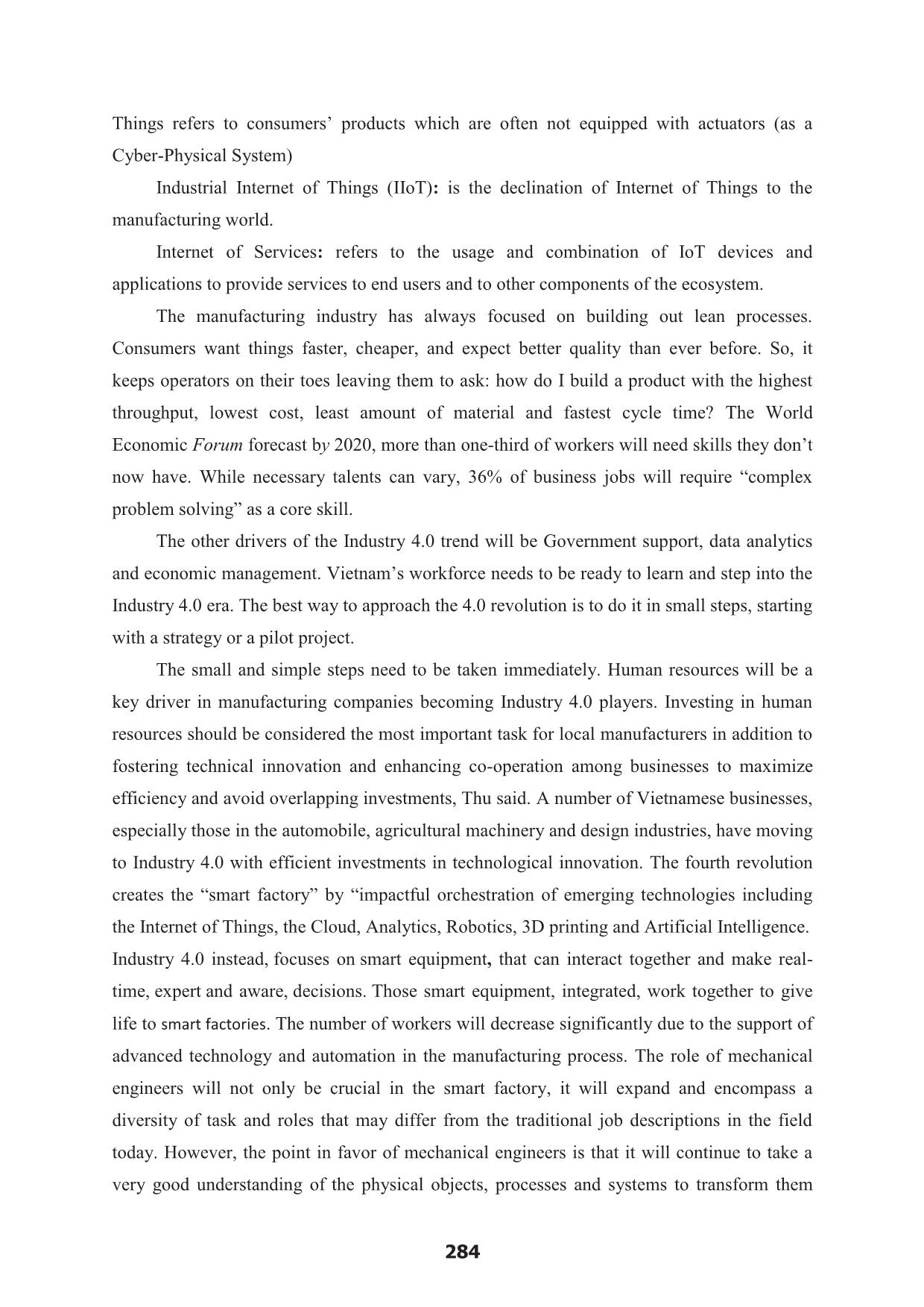
Trang 3
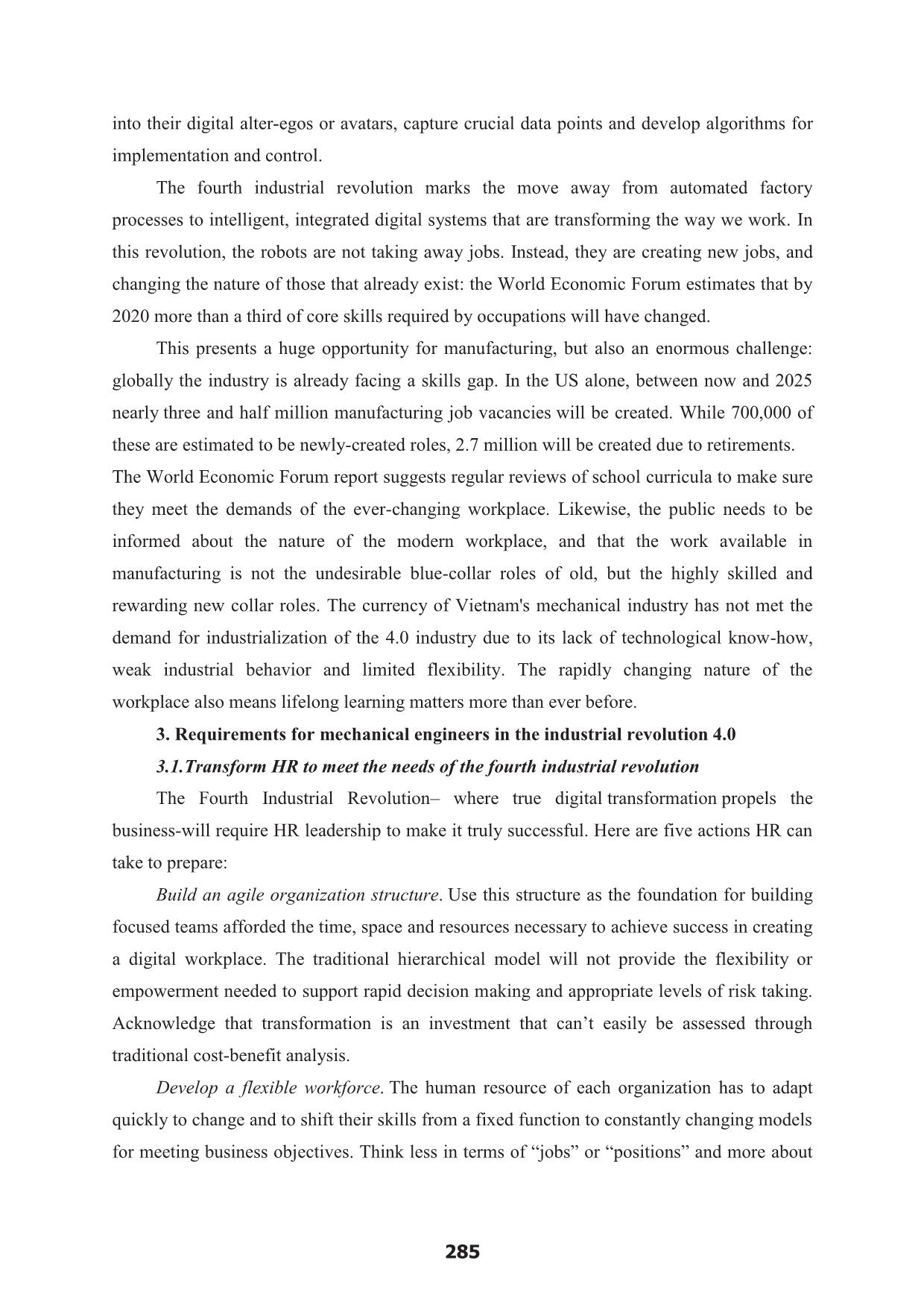
Trang 4
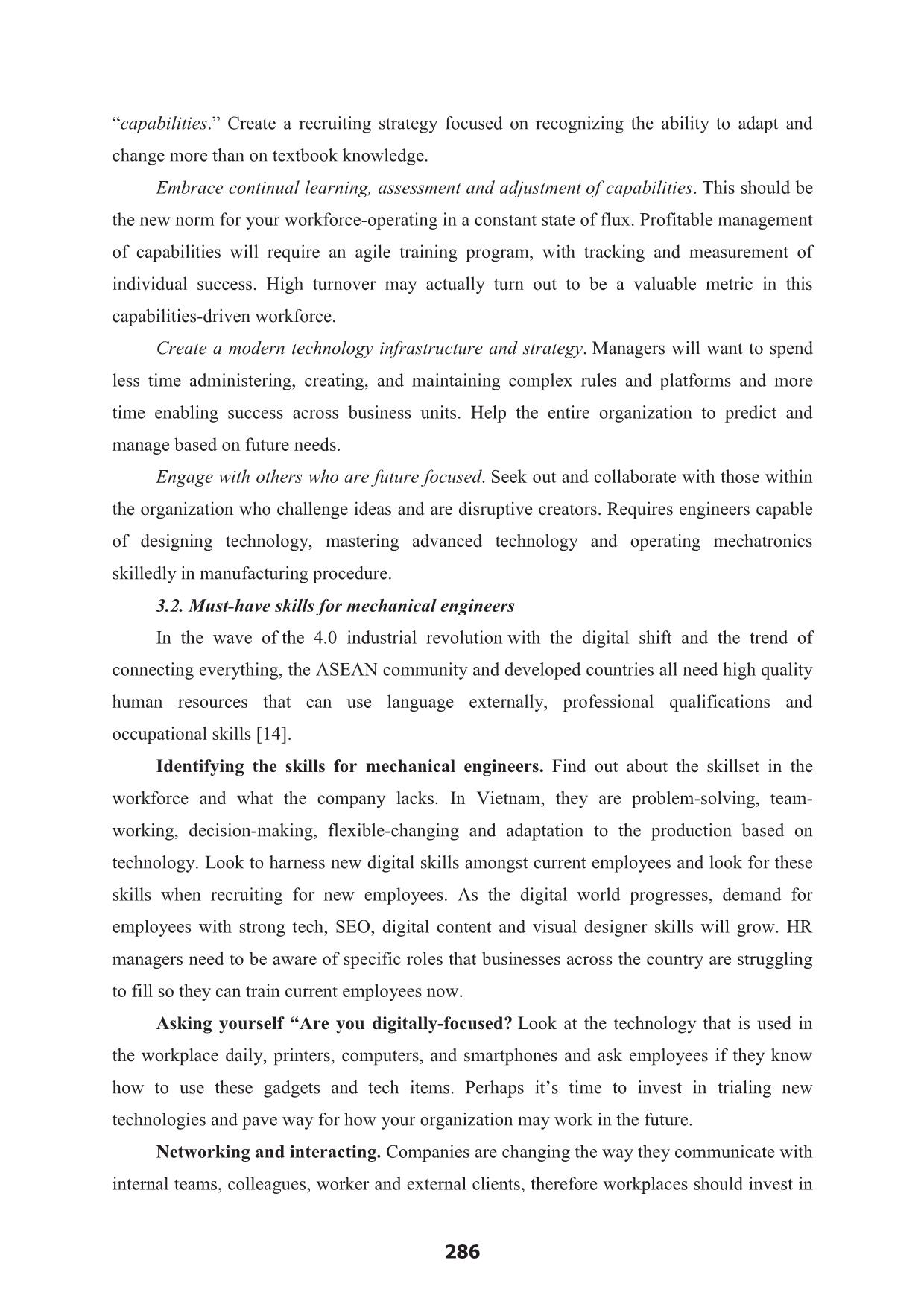
Trang 5
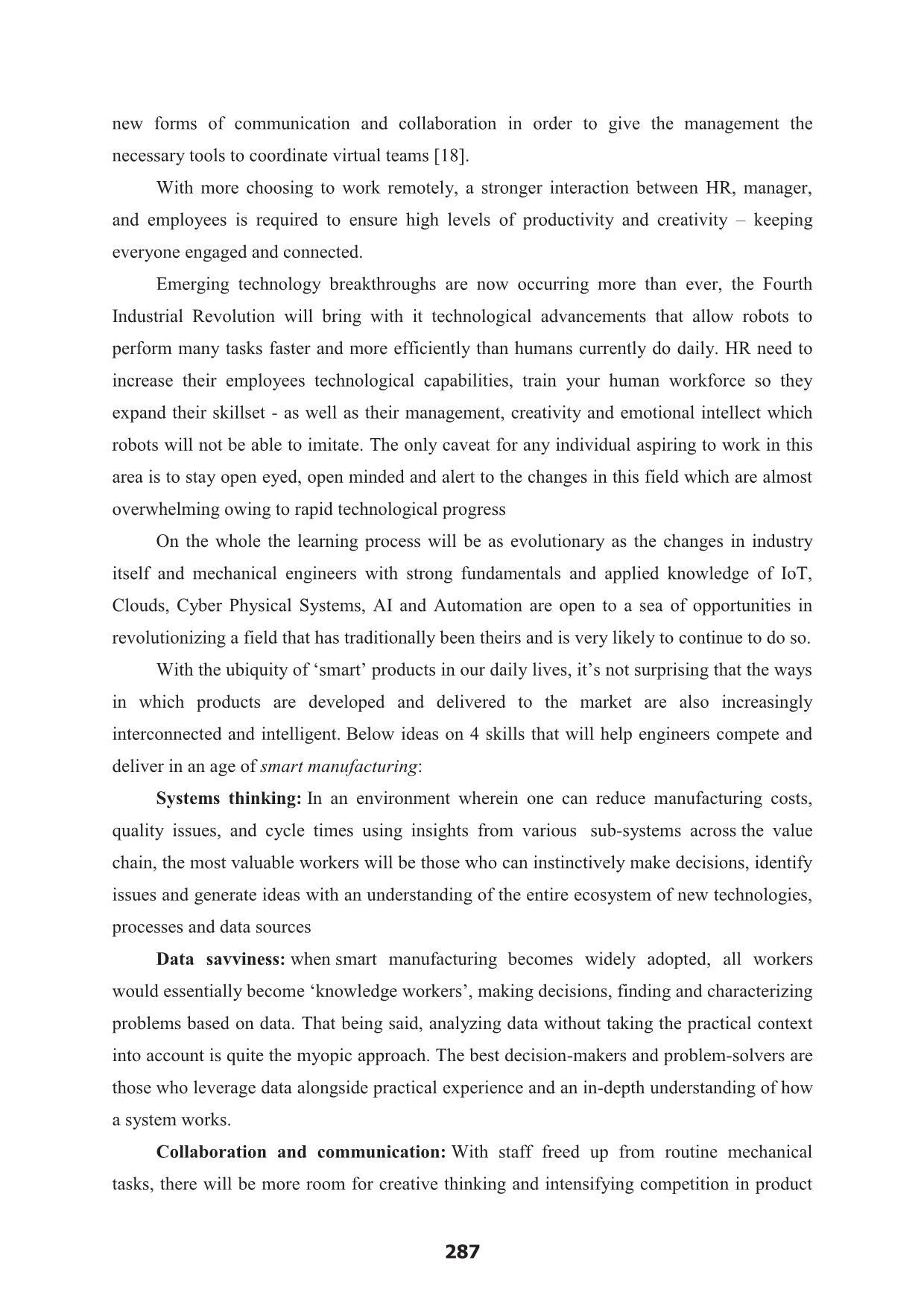
Trang 6
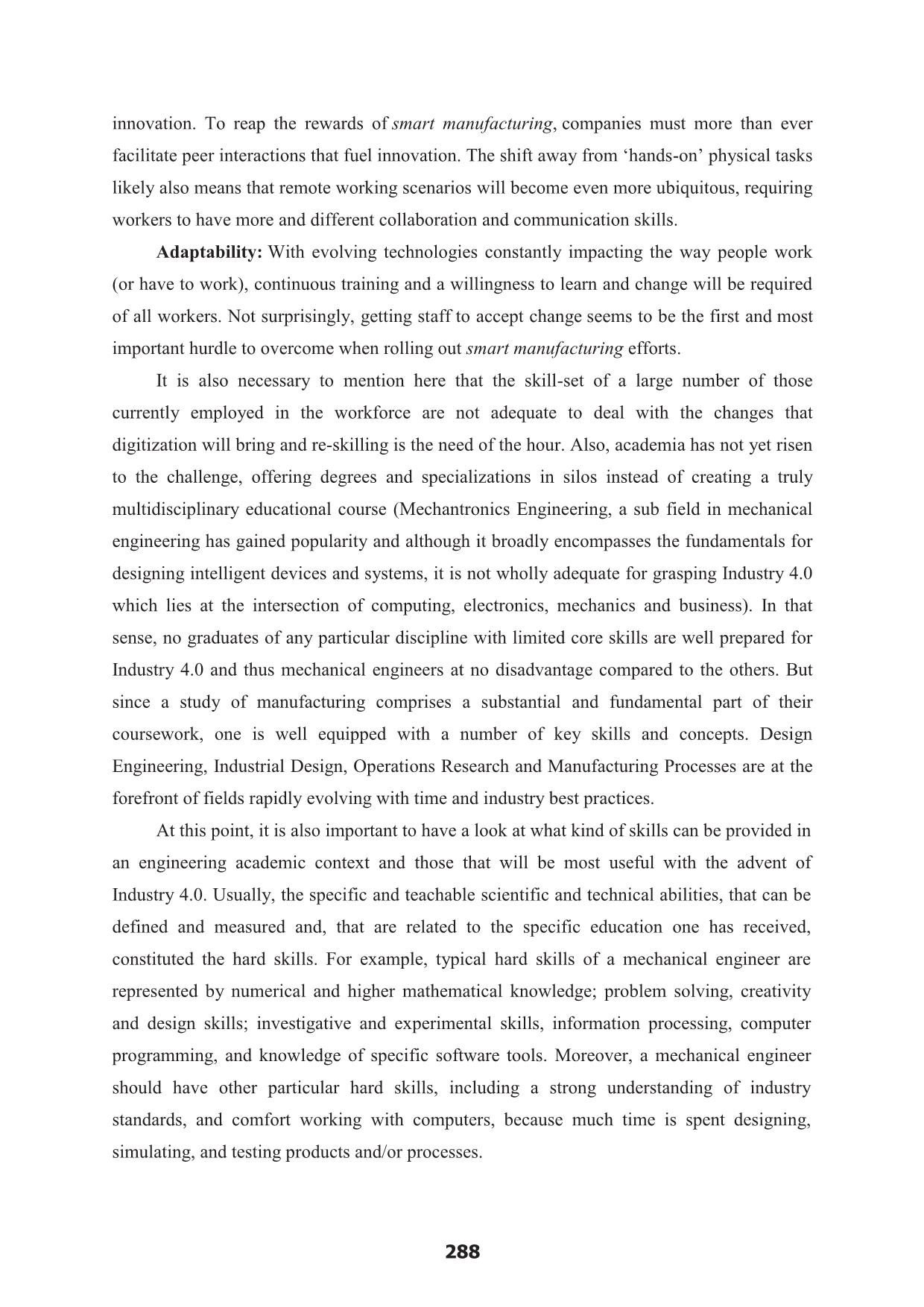
Trang 7
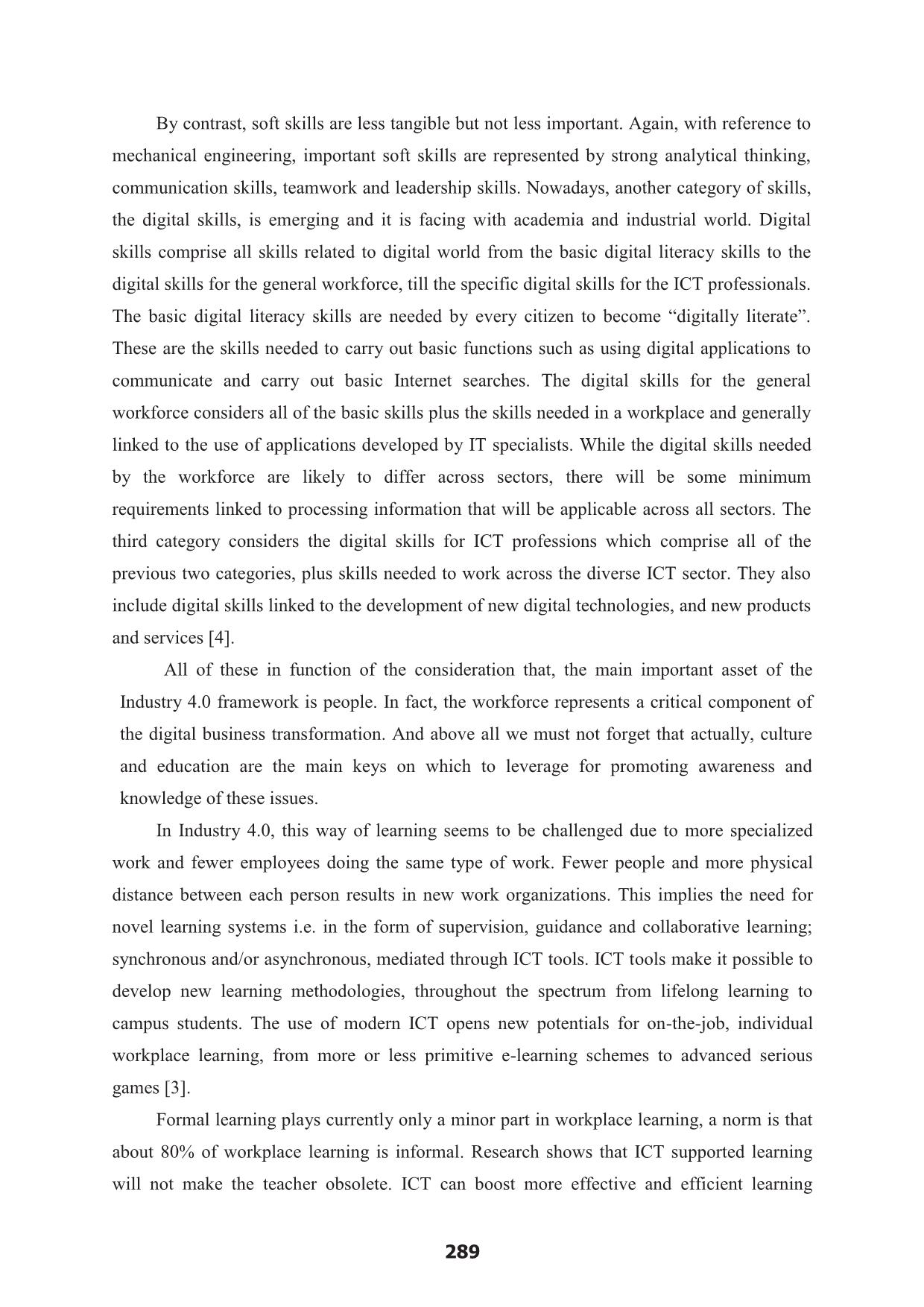
Trang 8
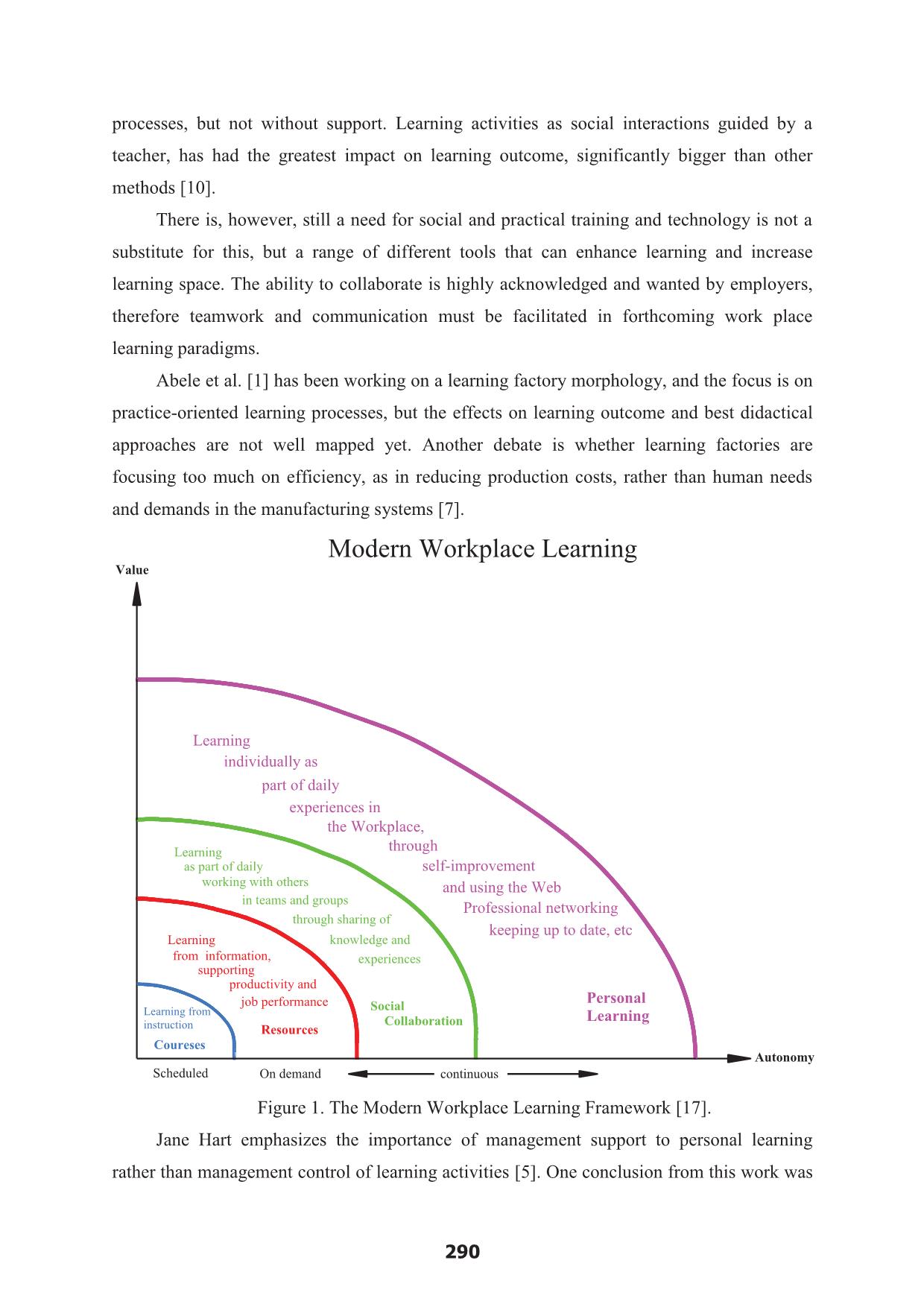
Trang 9
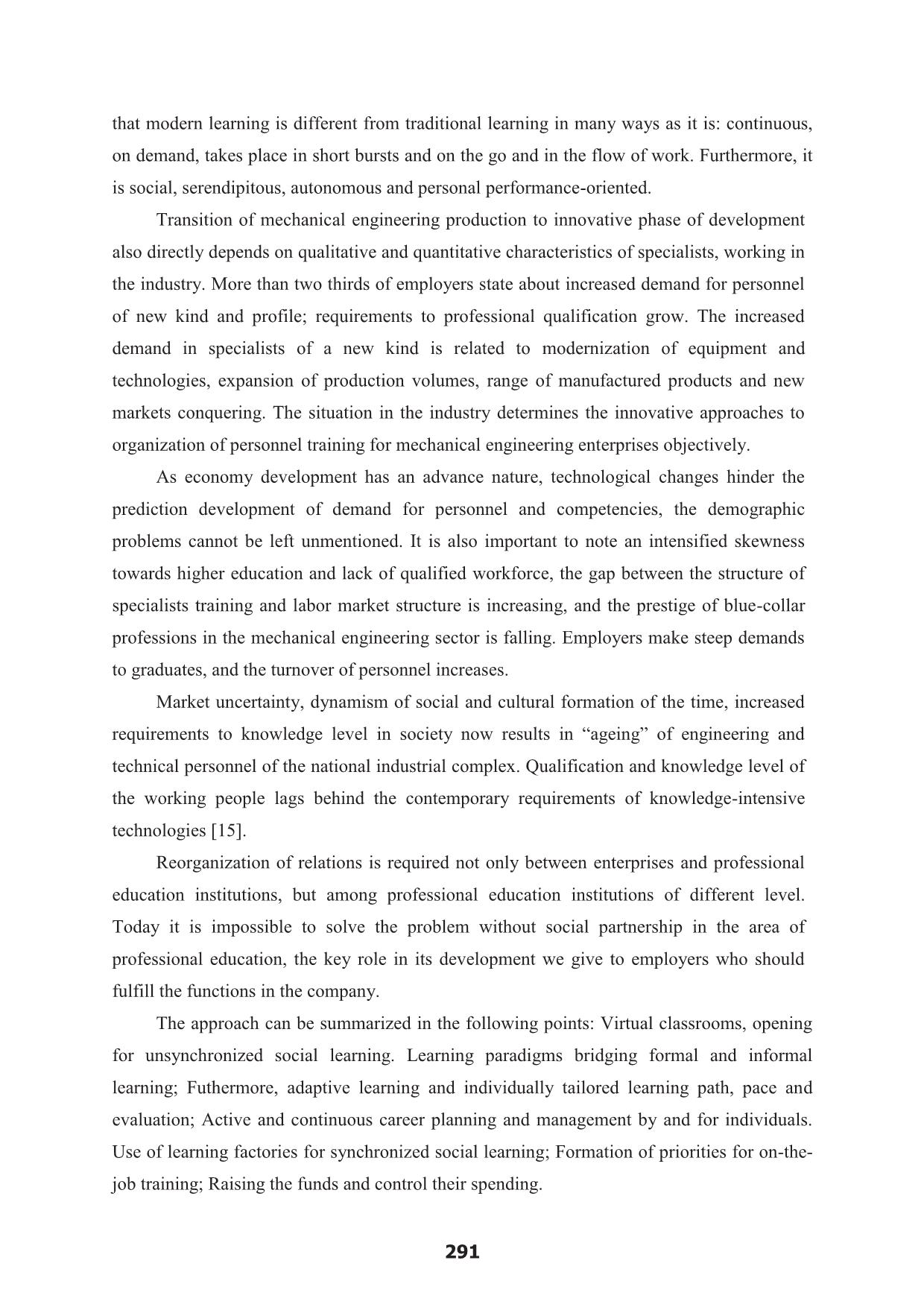
Trang 10
Tải về để xem bản đầy đủ
Tóm tắt nội dung tài liệu: Requirements of human resource in Vietnam mechanical industry in the context of industry 4.0
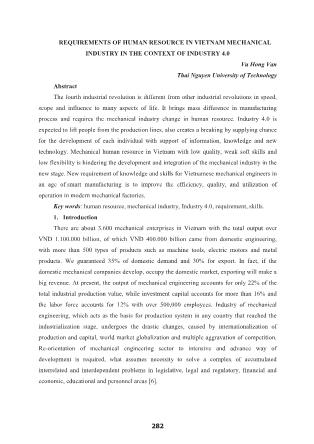
tate peer interactions that fuel innovation. The shift away from ‘hands-on’ physical tasks likely also means that remote working scenarios will become even more ubiquitous, requiring workers to have more and different collaboration and communication skills. Adaptability: With evolving technologies constantly impacting the way people work (or have to work), continuous training and a willingness to learn and change will be required of all workers. Not surprisingly, getting staff to accept change seems to be the first and most important hurdle to overcome when rolling out smart manufacturing efforts. It is also necessary to mention here that the skill-set of a large number of those currently employed in the workforce are not adequate to deal with the changes that digitization will bring and re-skilling is the need of the hour. Also, academia has not yet risen to the challenge, offering degrees and specializations in silos instead of creating a truly multidisciplinary educational course (Mechantronics Engineering, a sub field in mechanical engineering has gained popularity and although it broadly encompasses the fundamentals for designing intelligent devices and systems, it is not wholly adequate for grasping Industry 4.0 which lies at the intersection of computing, electronics, mechanics and business). In that sense, no graduates of any particular discipline with limited core skills are well prepared for Industry 4.0 and thus mechanical engineers at no disadvantage compared to the others. But since a study of manufacturing comprises a substantial and fundamental part of their coursework, one is well equipped with a number of key skills and concepts. Design Engineering, Industrial Design, Operations Research and Manufacturing Processes are at the forefront of fields rapidly evolving with time and industry best practices. At this point, it is also important to have a look at what kind of skills can be provided in an engineering academic context and those that will be most useful with the advent of Industry 4.0. Usually, the specific and teachable scientific and technical abilities, that can be defined and measured and, that are related to the specific education one has received, constituted the hard skills. For example, typical hard skills of a mechanical engineer are represented by numerical and higher mathematical knowledge; problem solving, creativity and design skills; investigative and experimental skills, information processing, computer programming, and knowledge of specific software tools. Moreover, a mechanical engineer should have other particular hard skills, including a strong understanding of industry standards, and comfort working with computers, because much time is spent designing, simulating, and testing products and/or processes. 288 By contrast, soft skills are less tangible but not less important. Again, with reference to mechanical engineering, important soft skills are represented by strong analytical thinking, communication skills, teamwork and leadership skills. Nowadays, another category of skills, the digital skills, is emerging and it is facing with academia and industrial world. Digital skills comprise all skills related to digital world from the basic digital literacy skills to the digital skills for the general workforce, till the specific digital skills for the ICT professionals. The basic digital literacy skills are needed by every citizen to become “digitally literate”. These are the skills needed to carry out basic functions such as using digital applications to communicate and carry out basic Internet searches. The digital skills for the general workforce considers all of the basic skills plus the skills needed in a workplace and generally linked to the use of applications developed by IT specialists. While the digital skills needed by the workforce are likely to differ across sectors, there will be some minimum requirements linked to processing information that will be applicable across all sectors. The third category considers the digital skills for ICT professions which comprise all of the previous two categories, plus skills needed to work across the diverse ICT sector. They also include digital skills linked to the development of new digital technologies, and new products and services [4]. All of these in function of the consideration that, the main important asset of the Industry 4.0 framework is people. In fact, the workforce represents a critical component of the digital business transformation. And above all we must not forget that actually, culture and education are the main keys on which to leverage for promoting awareness and knowledge of these issues. In Industry 4.0, this way of learning seems to be challenged due to more specialized work and fewer employees doing the same type of work. Fewer people and more physical distance between each person results in new work organizations. This implies the need for novel learning systems i.e. in the form of supervision, guidance and collaborative learning; synchronous and/or asynchronous, mediated through ICT tools. ICT tools make it possible to develop new learning methodologies, throughout the spectrum from lifelong learning to campus students. The use of modern ICT opens new potentials for on-the-job, individual workplace learning, from more or less primitive e-learning schemes to advanced serious games [3]. Formal learning plays currently only a minor part in workplace learning, a norm is that about 80% of workplace learning is informal. Research shows that ICT supported learning will not make the teacher obsolete. ICT can boost more effective and efficient learning 289 processes, but not without support. Learning activities as social interactions guided by a teacher, has had the greatest impact on learning outcome, significantly bigger than other methods [10]. There is, however, still a need for social and practical training and technology is not a substitute for this, but a range of different tools that can enhance learning and increase learning space. The ability to collaborate is highly acknowledged and wanted by employers, therefore teamwork and communication must be facilitated in forthcoming work place learning paradigms. Abele et al. [1] has been working on a learning factory morphology, and the focus is on practice-oriented learning processes, but the effects on learning outcome and best didactical approaches are not well mapped yet. Another debate is whether learning factories are focusing too much on efficiency, as in reducing production costs, rather than human needs and demands in the manufacturing systems [7]. Figure 1. The Modern Workplace Learning Framework [17]. Jane Hart emphasizes the importance of management support to personal learning rather than management control of learning activities [5]. One conclusion from this work was Modern Workplace Learning Value Learning Learning from information, Resources Learning supporting productivity and job performance as part of daily working with others in teams and groups through sharing of knowledge and experiences Social Collaboration Personal Learning individually as experiences in and using the Web Professional networking keeping up to date, etc through the Workplace, part of daily self-improvement Coureses Learning from instruction Scheduled On demand continuous Autonomy 290 that modern learning is different from traditional learning in many ways as it is: continuous, on demand, takes place in short bursts and on the go and in the flow of work. Furthermore, it is social, serendipitous, autonomous and personal performance-oriented. Transition of mechanical engineering production to innovative phase of development also directly depends on qualitative and quantitative characteristics of specialists, working in the industry. More than two thirds of employers state about increased demand for personnel of new kind and profile; requirements to professional qualification grow. The increased demand in specialists of a new kind is related to modernization of equipment and technologies, expansion of production volumes, range of manufactured products and new markets conquering. The situation in the industry determines the innovative approaches to organization of personnel training for mechanical engineering enterprises objectively. As economy development has an advance nature, technological changes hinder the prediction development of demand for personnel and competencies, the demographic problems cannot be left unmentioned. It is also important to note an intensified skewness towards higher education and lack of qualified workforce, the gap between the structure of specialists training and labor market structure is increasing, and the prestige of blue-collar professions in the mechanical engineering sector is falling. Employers make steep demands to graduates, and the turnover of personnel increases. Market uncertainty, dynamism of social and cultural formation of the time, increased requirements to knowledge level in society now results in “ageing” of engineering and technical personnel of the national industrial complex. Qualification and knowledge level of the working people lags behind the contemporary requirements of knowledge-intensive technologies [15]. Reorganization of relations is required not only between enterprises and professional education institutions, but among professional education institutions of different level. Today it is impossible to solve the problem without social partnership in the area of professional education, the key role in its development we give to employers who should fulfill the functions in the company. The approach can be summarized in the following points: Virtual classrooms, opening for unsynchronized social learning. Learning paradigms bridging formal and informal learning; Futhermore, adaptive learning and individually tailored learning path, pace and evaluation; Active and continuous career planning and management by and for individuals. Use of learning factories for synchronized social learning; Formation of priorities for on-the- job training; Raising the funds and control their spending. 291 4. Conclusion Knowledge is the key for adding value as a result of fundamental research and education knowledge will drive technologies towards technical innovations and produce complex products with efficient processes. The qualification of workforce for mechanical manufacturing depends on the education system and facilities for manufacturing. In view of changes in the fourth industrial revolution, mechanical engineers in Vietnam need to be well trained, highly and multi skilled. Innovation is an extremely important issue for success in mechanical engineering. It often supports clear market position and differentiation among competitors. The article emphasizes the role of informal learning for mechanical engineers and workers in the organization with modern workplace learning to get knowledge and skills. It helps them adapt to drastic changes in Industrial 4.0 and be suitable with conditions in Vietnamese mechanical factories. REFERENCES 1.Abele et al. 2017, Learning factories for future oriented research and education in manufacturing. CIRP Annals, Volume 66, Issue 2, 2017, Pages 803-826. 2.Barbara Motyl, Gabriele Baronio, Stefano Uberti, Domenico Speranza, Stefano Filippi (2017), How will change the future engineers' skills in the Industry 4.0 framework? A questionnaire survey; 27th International Conference on Flexible Automation and Intelligent Manufacturing, FAIM2017, 27-30 June 2017, Modena, Italy. 3. Borzoo Pourabdollahian, Marco Taisch, Endris Kerga (2012), Serious Games in Manufacturing Education: Evaluation of Learners’ Engagement, Procedia Computer Science, Volume 15, 256-265. 4. European Commission: e-Skills for growth and jobs [Online] Available at: [Acessed 01-Mar-2017]. 5. Hart, J., (2016), Rethinking workplace learning, Learning in the Modern Workplace. 6. Lizunkov, V. G., & Sushko, A. V. (2015). Podkhod CDIO v podgotovke bakalavrov mashinostroeniya [CDIO approach in training of mechanical engineering bachelors]. Sovremennye problemy teorii mashin [Modern problems of theory of machines], 3, 62-66. 7. Kreimeier, D., Morlock, F., Prinz, C., Krückhans, B., Bakir, D. C. and Meier, H. (2014), Holistic Learning Factories – A Concept to Train Lean Management, Resource Efficiency as Well as Management and Organization Improvement Skills. Procedia CIRP 17, 184-188. 8.Marina Suzdalova, Ekaterina Politsinskaya, Anastasia Sushko; About the Problem of Professional Personnel Shortage in Mechanical Engineering Industry and Ways of Solving; 292 XV International Conference "Linguistic and Cultural Studies: Traditions and Innovations”, LKTI 2015, 9-11 November 2015, Tomsk, Russia 9.McKinsey&Company (2014). The future of German mechanical engineering. Operating successfully in a dynamic environment. VDM. German, July 2014. 10. Mincu, M. E. (2015), Teacher quality and school improvement: what is the role of research? Oxford Review of Education 41, 253-269. 11.Nina Tvenge, Kristian Martinsen (2018), Integration of digital learning in industry 4.0; 8th Conference on Learning Factories 2018 - Advanced Engineering Education & Training for Manufacturing Innovation 12. S. Suárez Fernández-Miranda, M. Marcos, M.E. Peralta, F. Aguayo (2017), The challenge of integrating Industry 4.0 in the degree of Mechanical Engineering; Manufacturing Engineering Society International Conference 2017, MESIC 2017, 28-30 June 2017, Vigo (Pontevedra), Spain 13. M. Rüßmann, M. Lorenz, P.Gerbert, M. Waldner, J. Justus, P. Engel, M. Harnisch M (2017). Industry 4.0: The future of productivity and growth in manufacturing industries. [Online] Available at: https://www.bcgperspectives.com/content/articles/engineered_products_project_business 14. Regina Javier (2015), The 4th Industrial Revolution: Must-Have Skills for Engineers, https://chemical-materials.elsevier.com/chemical-manufacturing-excellence/must-have-skills- for-engineers/, 1/12/2015 15.Suzdalova, M. A. (2013). Adaptatsiya obuchayushchikhsya uchrezhdeniy professional'nogo obrazovaniya k rynku truda [Adaptation of students of professional education institutions to labor market. Thesis abstract]. Kemerovo: KGU. 16.VDMA European Office (2016), Industrie 4.0: Mastering the transition, Brussels. 17.Wenger, E., 1988, Communities of Practice; learning meaning and identity. Cambridge University Press., Cambridge. 18.https://vietnamnews.vn/economy/373429/human-resources-to-drive-industry- 40.html#xQZmAMLz0WlqF73E.97 (13/6/2016). 293
File đính kèm:
requirements_of_human_resource_in_vietnam_mechanical_industr.pdf