Giáo trình Công nghệ hàn - Nghề: Hàn
Giới thiệu:
Nghề hàn được ứng dụng rộng rãi trong nhiều lĩnh vực của các ngành công nghiệp.
Nắm vững những kiến thức chung về hàn sẽ giúp người học hiểu rõ hơn bản chất
của phương pháp hàn, qua đó có cơ hội để phát triển nghề nghiệp, góc sức vào
công cuộc xây dựng nền kinh tế nước ta.
Mục tiêu:
- Nắm được thực chất, đặc điểm và phân loại các phương pháp hàn.
- Trình bầy được quá trình vật lý và luyện kim khi hàn nóng chảy.
- Phân loại và đánh giá tính hàn của kim loại và hợp kim.
Nội dung chính:
1. Thực chất, đặc điểm và phân loại các phương pháp hàn.
1.1. Thực chất và đặc điểm
1.1.1. Thực chất
Hàn là quá trình công nghệ nối hai hoặc nhiều phần tử (chi tiết, bộ phận) thành
một khối thống nhất bằng cách dùng nguồn nhiệt nung nóng chỗ cần nối đến trạng thái
lỏng (hoặc dẻo), sau đó kim loại tự kết tinh (hoặc dùng lực ép) tạo thành mối hàn.
1.1.2. Đặc điểm
+ Liên kết hàn là một liên kết ‘’cứng’’ không tháo rời được.
+ So với đinh tán tiết kiệm (10 - 20)% khối lượng kim loại, so với đúc tiết kiệm khoảng
50%.
+ Hàn chế tạo được các chi tiết có hình dáng phức tạp, liên kết các kim loại có cùng tính
chất hoặc khác tính chất với nhau.
+ Mối hàn có độ bền và độ kín cao, đáp ứng yêu cầu làm việc quan trọng của các kết
cấu quan trọng (vỏ tàu, bồn chứa, nồi hơi,.v.v ).
+ Có thể cơ khí hóa và tự động hóa quá trình hàn.
+ Giá thành chế tạo kết cấu rẻ.
Tuy vậy, hàn còn có một số nhược điểm : sau khi hàn tồn tại ứng suất và biến dạng dư,
xuất hiện vùng ảnh hưởng nhiệt làm giảm khả năng chịu lực của kết cấu.
1.2. Phân loại các phương pháp hàn
1.2.1. Căn cứ dạng năng lượng sử dụng, hàn được phân ra các phương pháp hàn sau:
- Các phương pháp hàn điện : dùng điện năng biến thành nhiệt năng (hàn điện hồ
quang, hàn điện tiếp xúc,.v.v ).
- Các phương pháp hàn cơ học : sử dụng cơ năng làm biến dạng kim loại tại khu vực
hàn (hàn nguội, hàn ma sát, hàn siêu âm,.v.v ).
- Các phương pháp hàn hóa học : sử dụng năng lượng do các phản ứng hóa học tạo ra
để nung nóng kim loại mối hàn (hàn khí, hàn hóa nhiệt,.v.v ).6
- Các phương pháp hàn kết hợp : sử dụng kết hợp các dạng năng lượng nêu trên (hàn
các vật liệu có tính hàn khó).
1.2.2. Căn cứ vào trạng thái kim loại mối hàn tại thời điểm hàn
- Hàn nóng chảy: Bao gồm các phương pháp hàn : hàn khí, hàn điện xỉ, hàn hồ
quang,.v.v Kim loại mối hàn ở trạng thái lỏng trong quá trình hàn.
- Hàn áp lực: bao gồm các phương pháp hàn : hàn siêu âm, hàn nổ, hàn khuếch tán, hàn
điện trở tiếp xúc,.v.v trong quá trình hàn, kim loại mối hàn ở trạng thái chảydẻo.
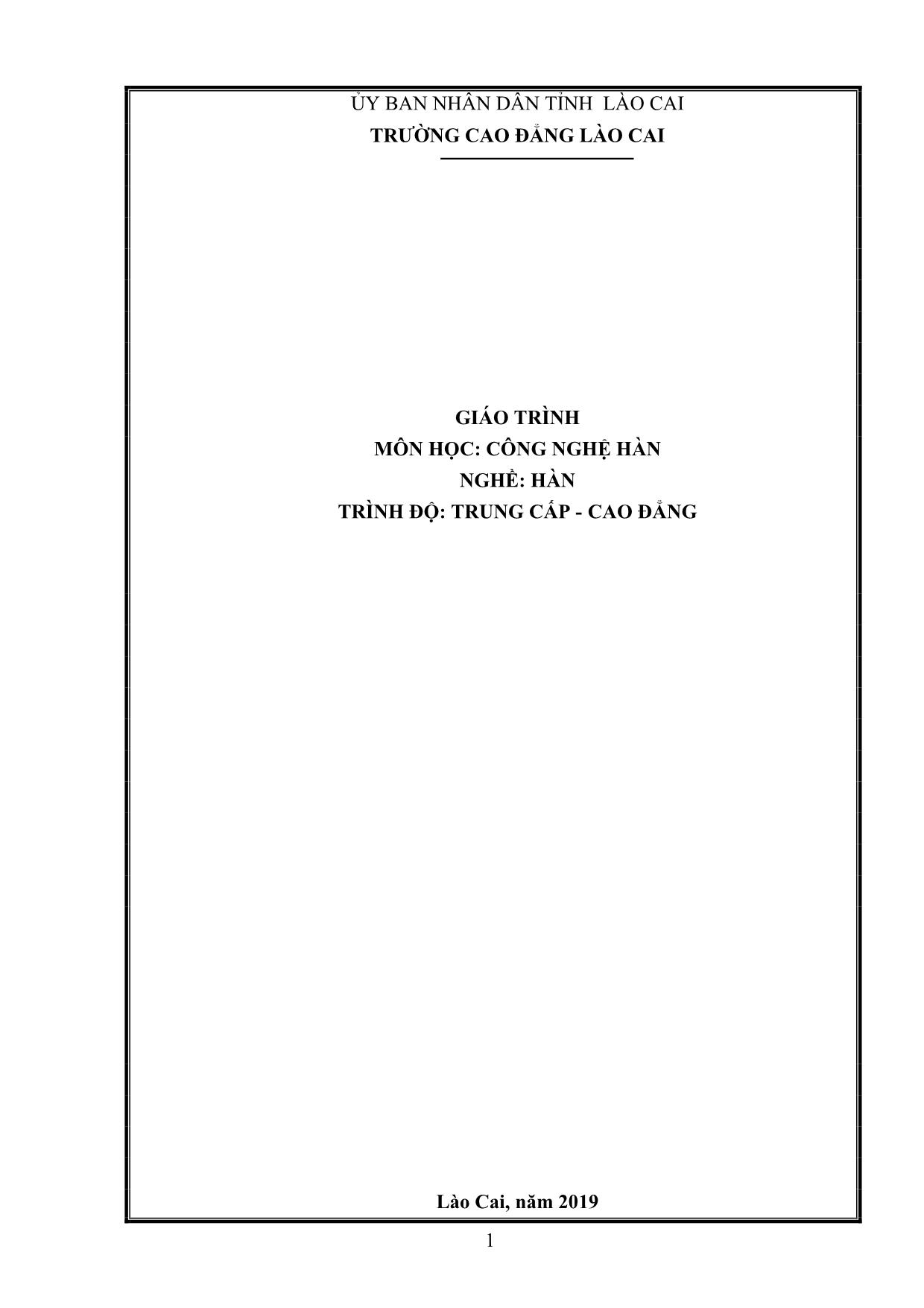
Trang 1
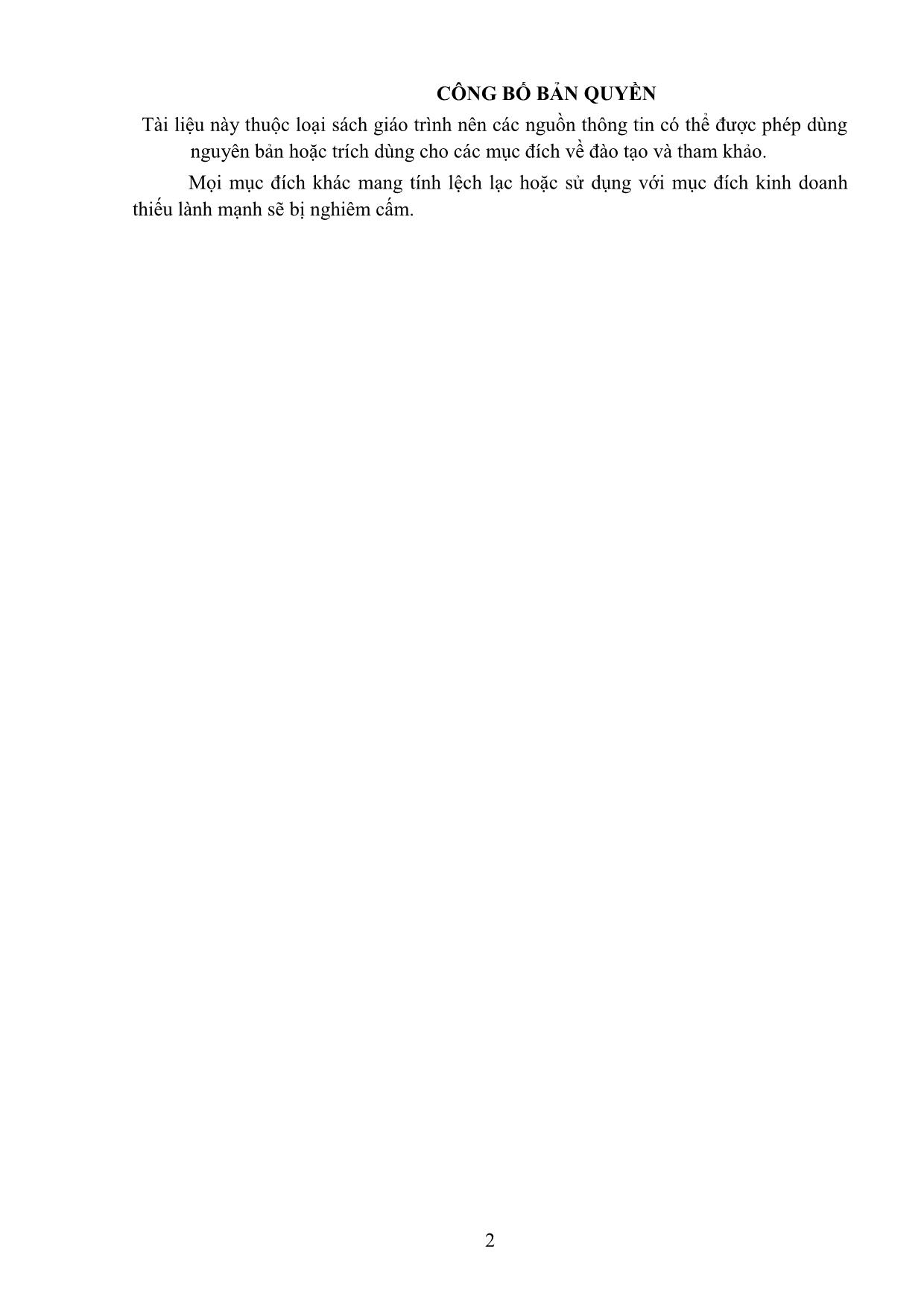
Trang 2
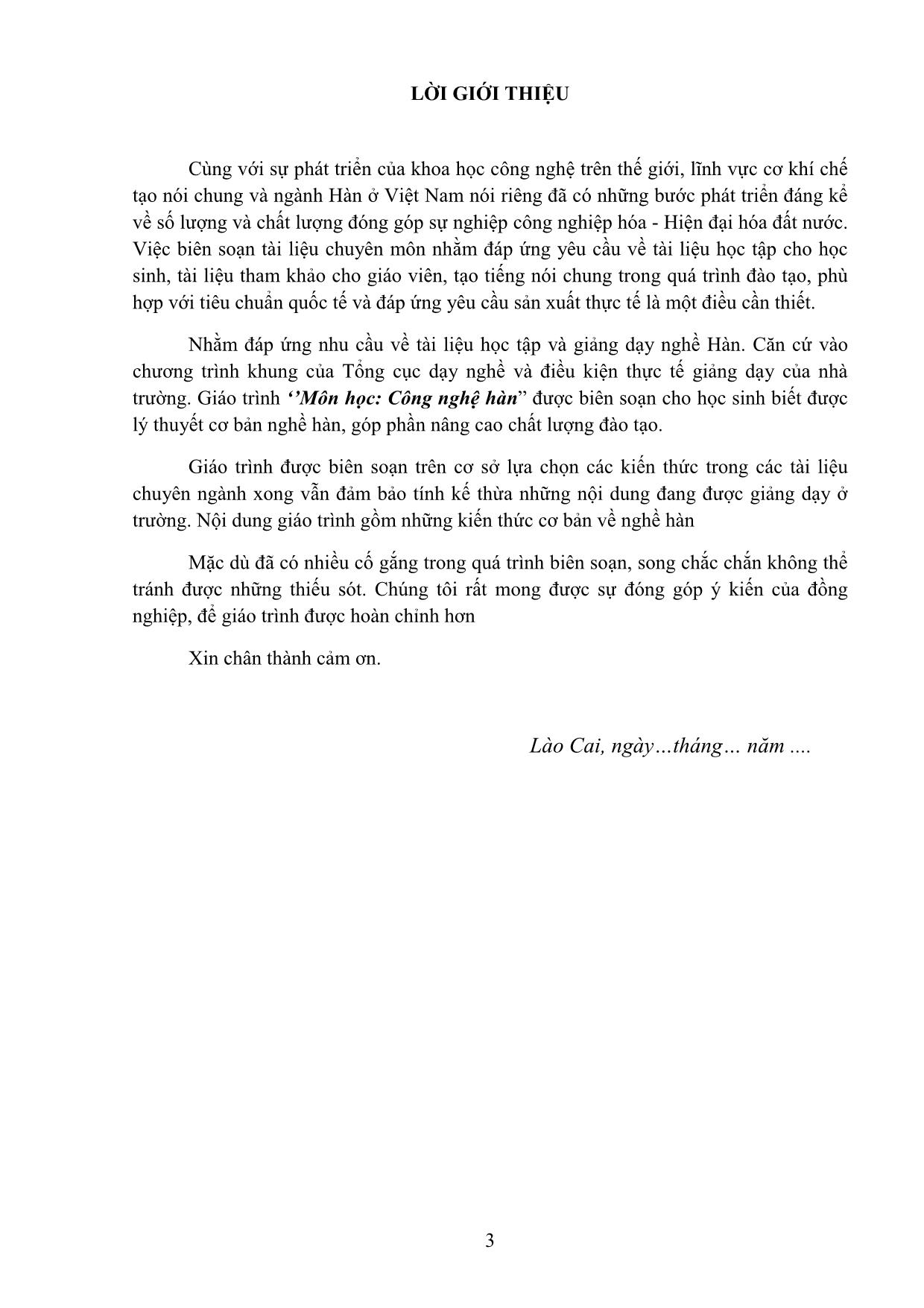
Trang 3
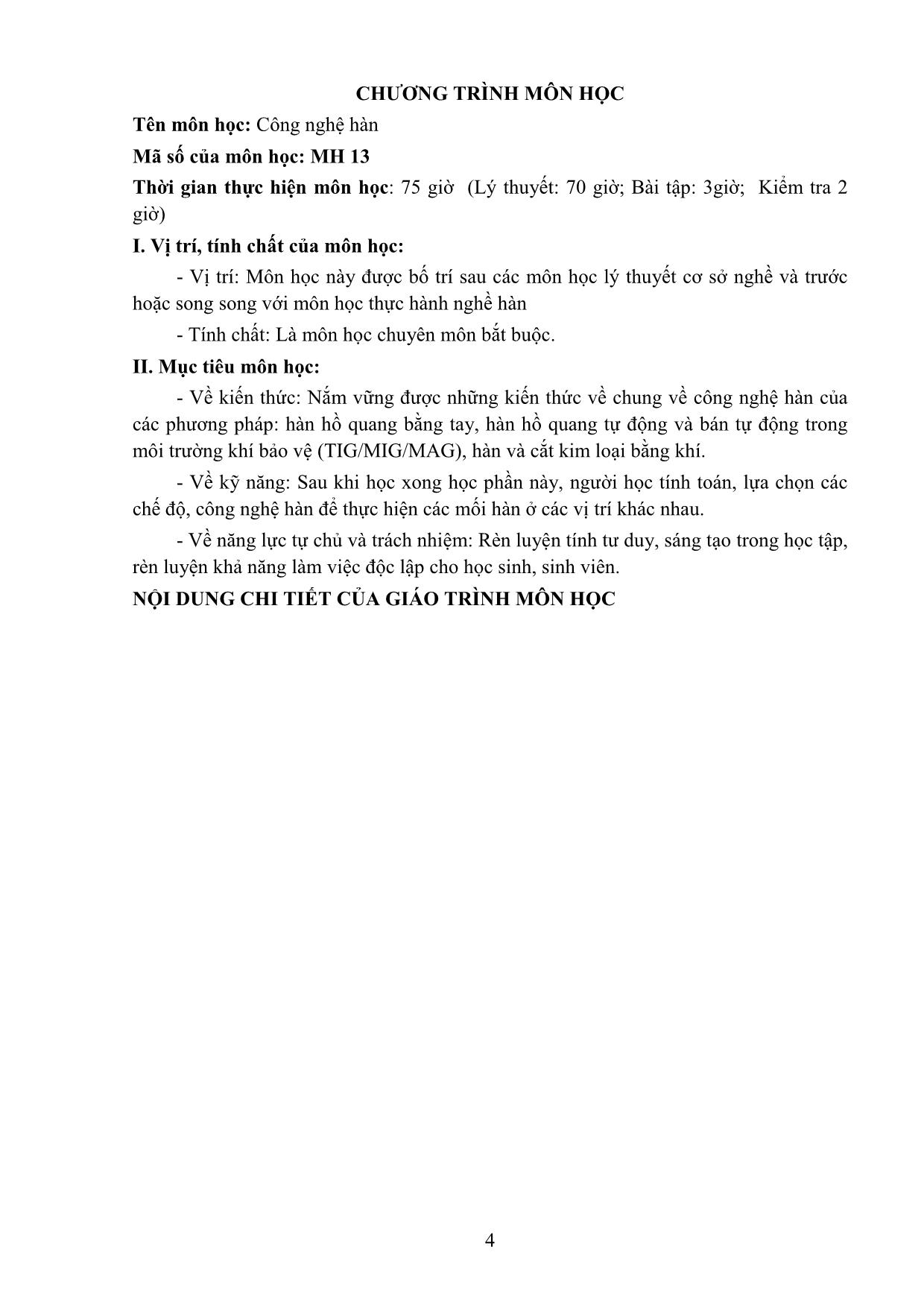
Trang 4
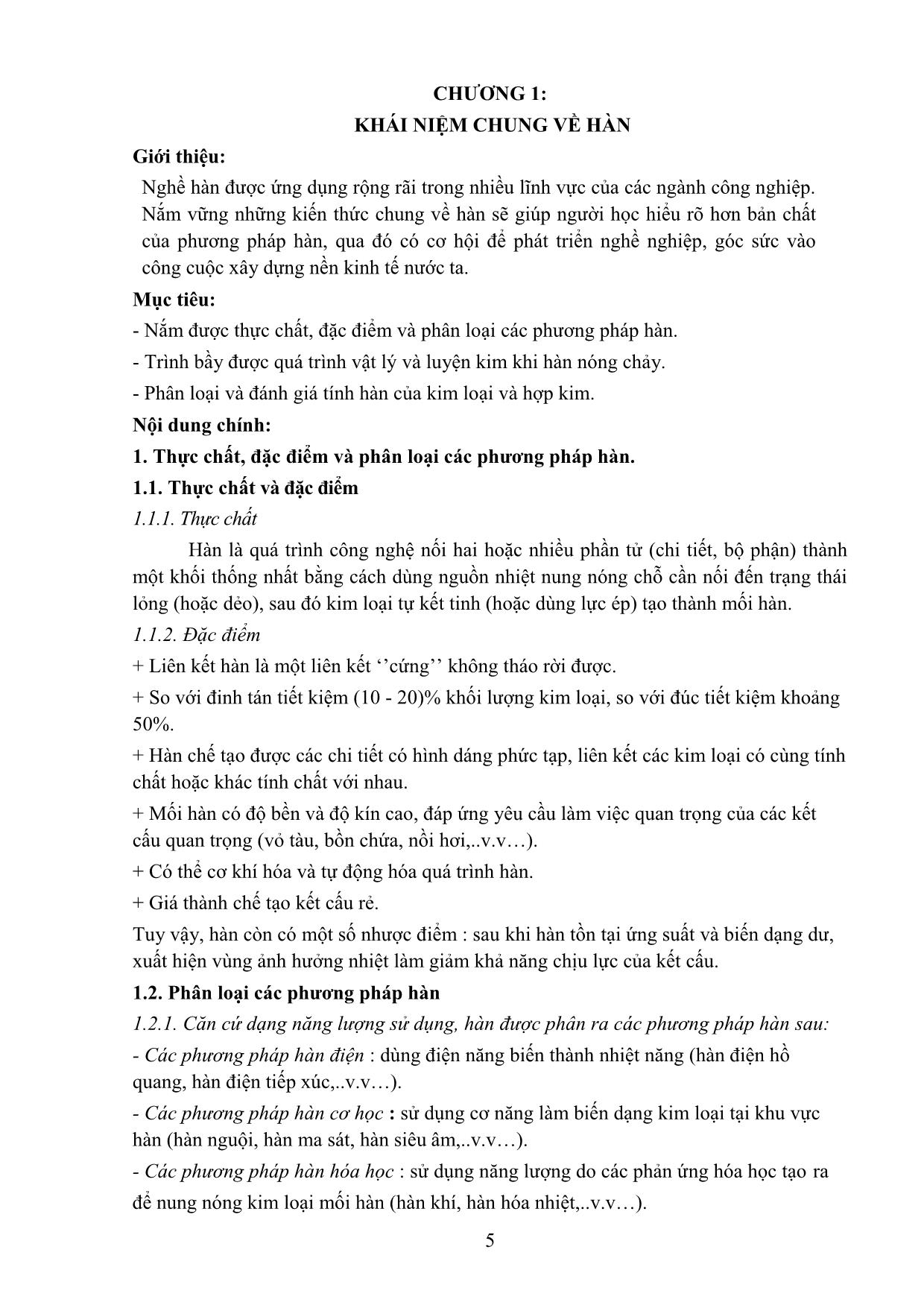
Trang 5
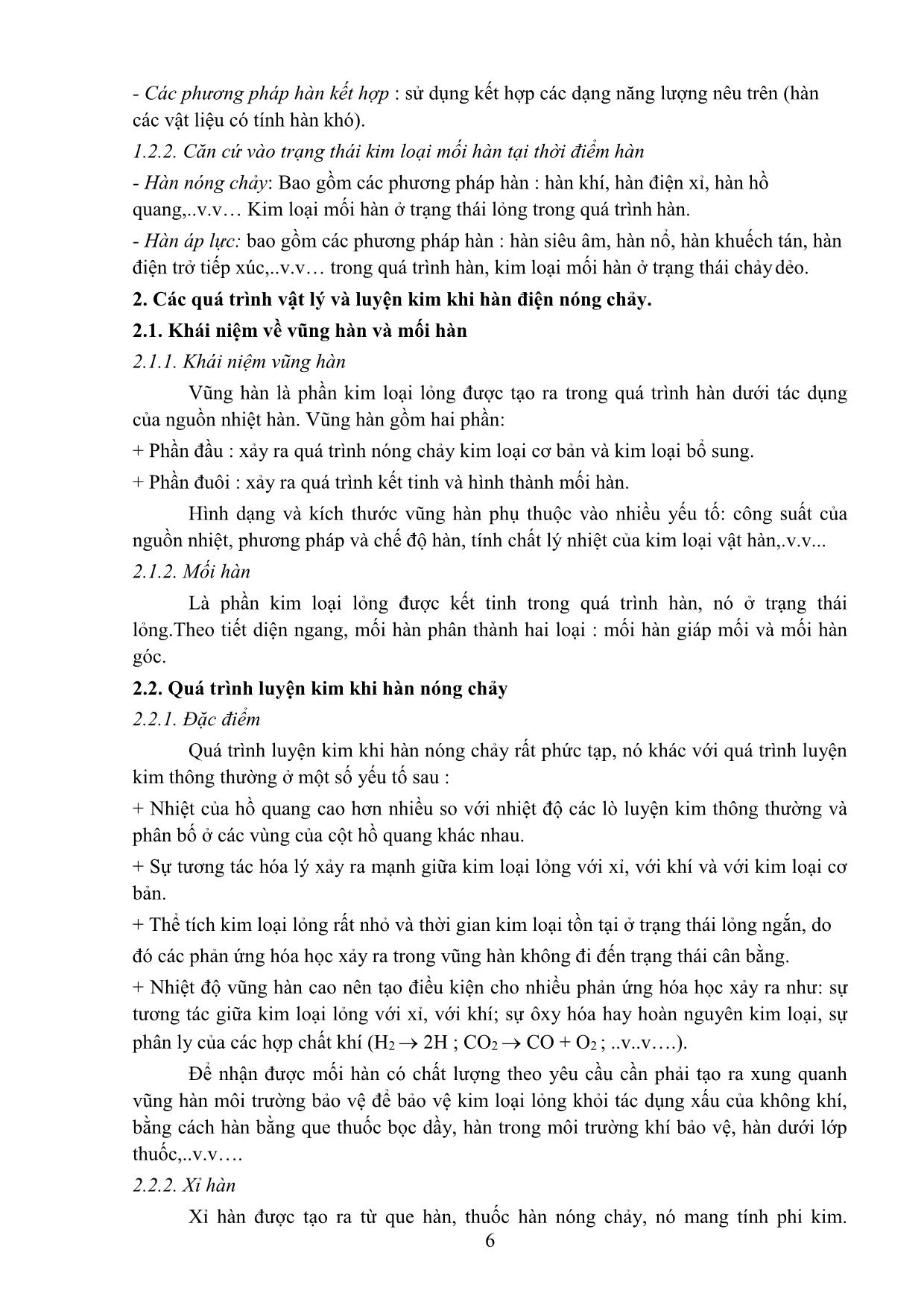
Trang 6
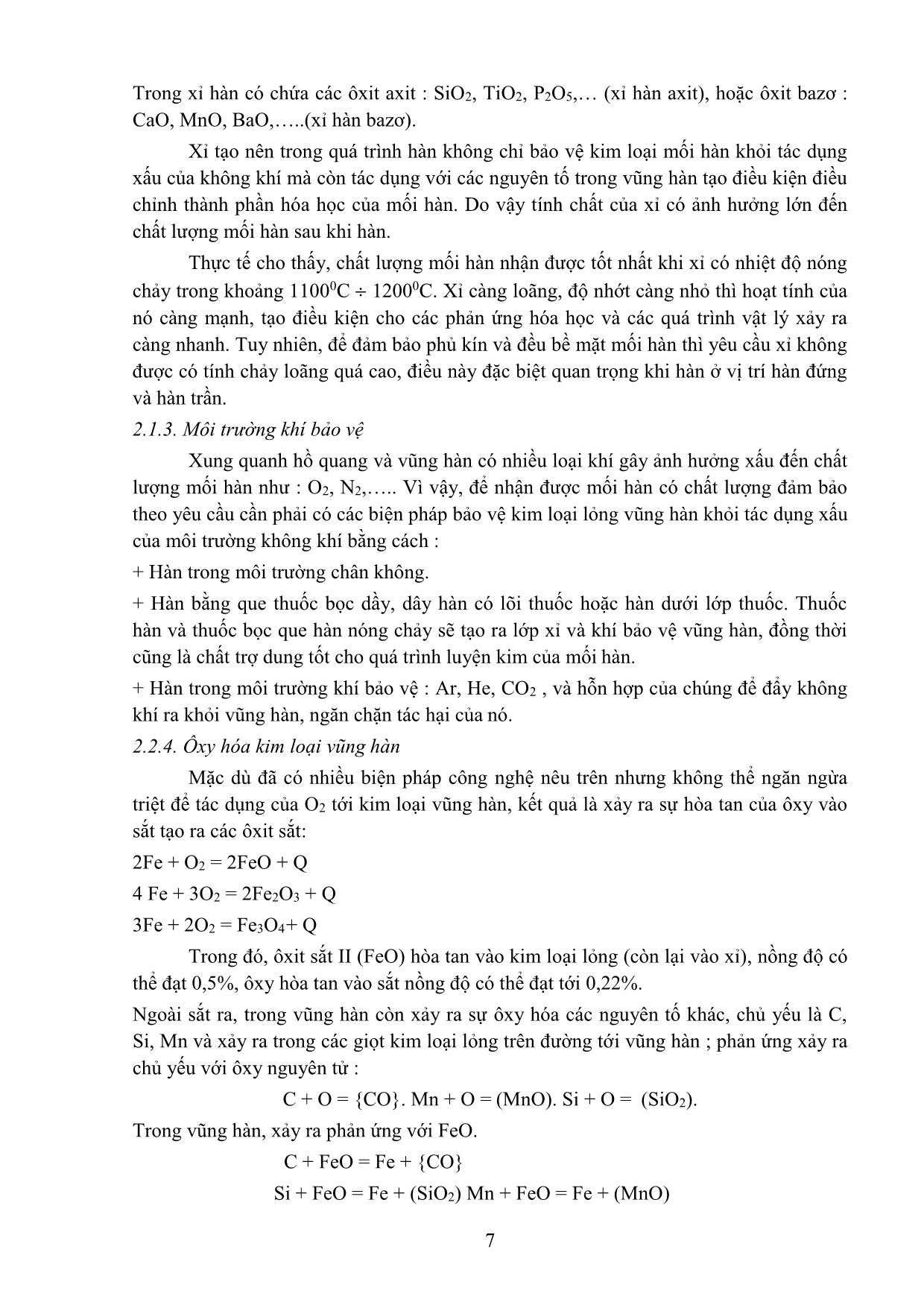
Trang 7
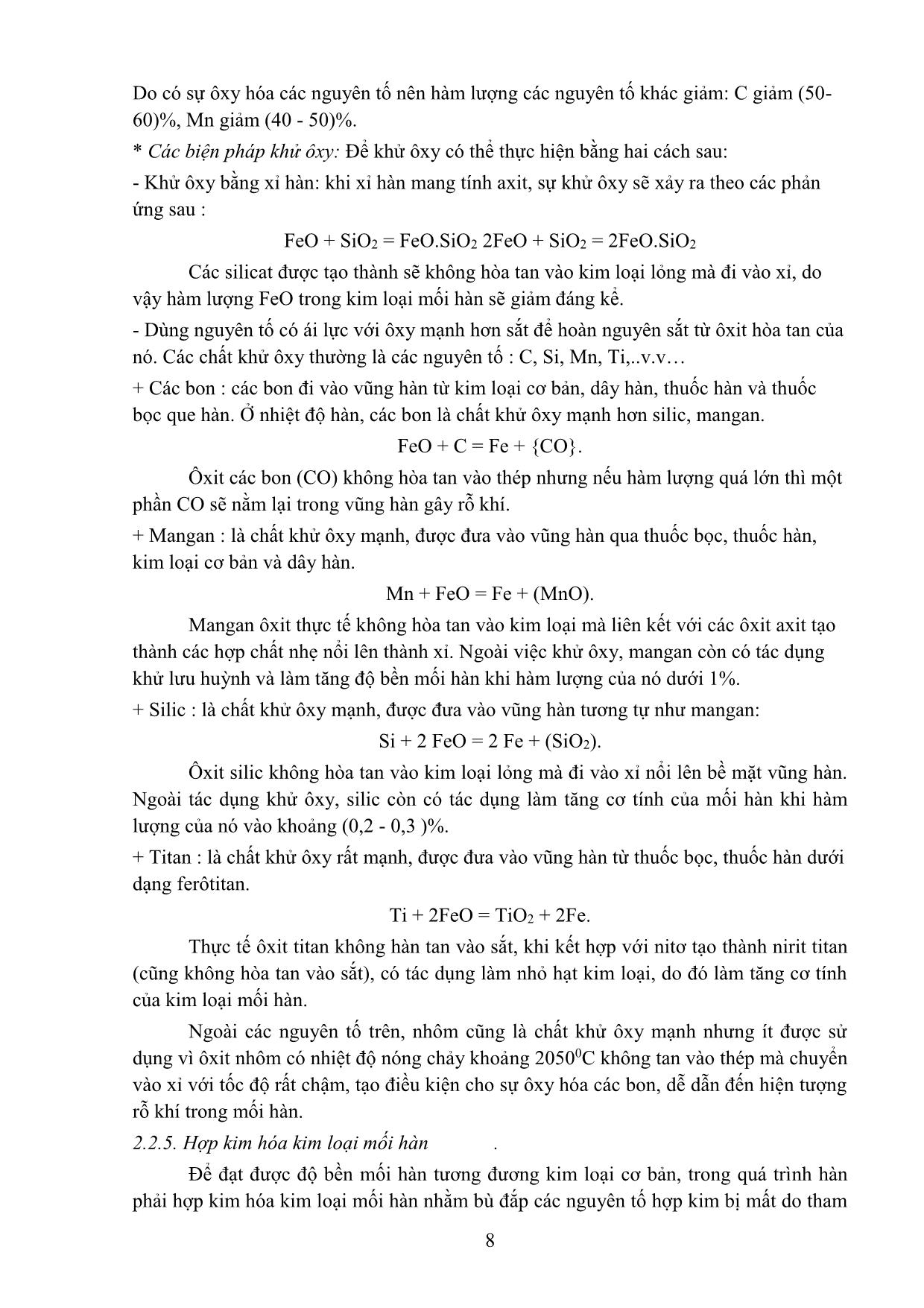
Trang 8
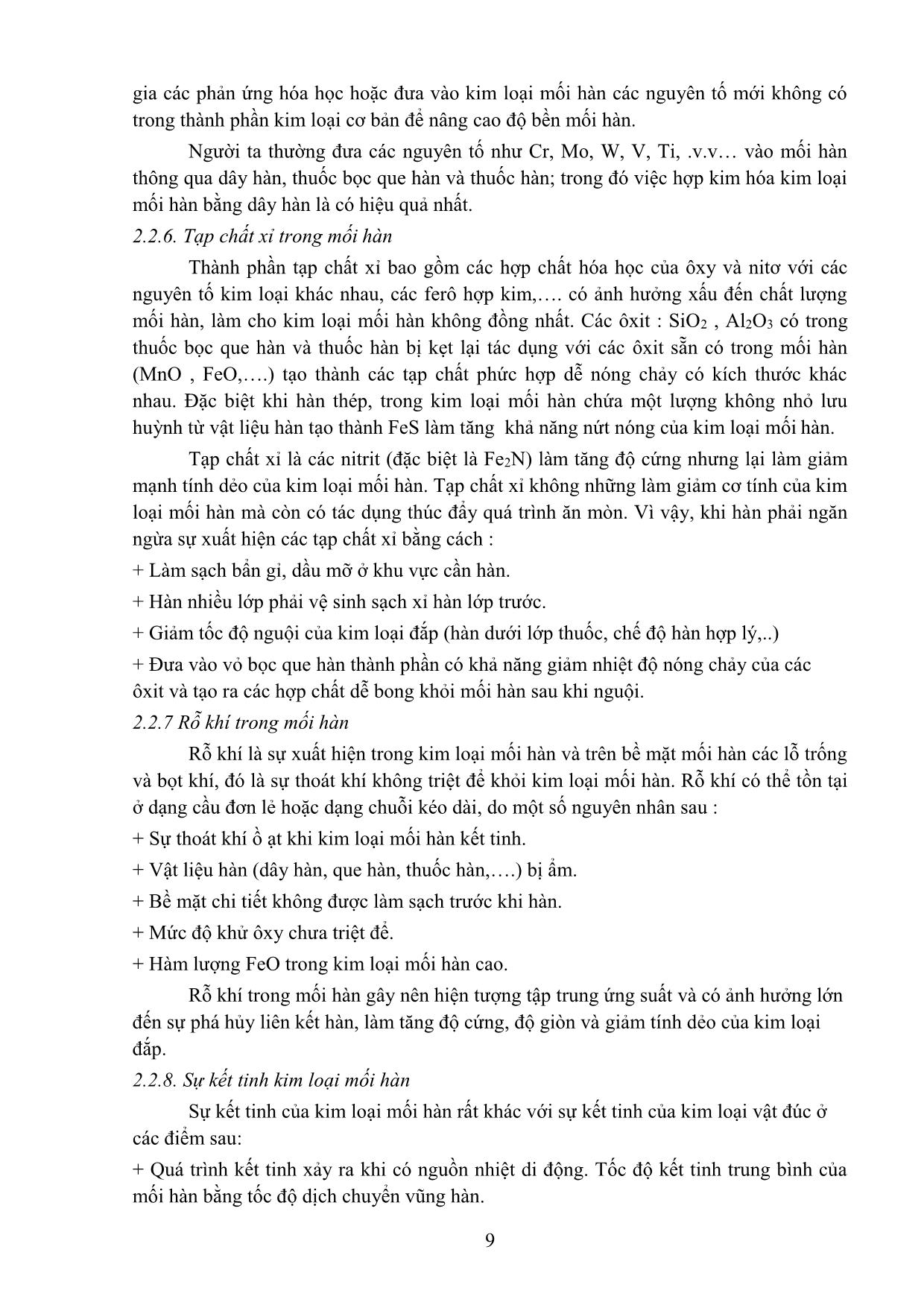
Trang 9
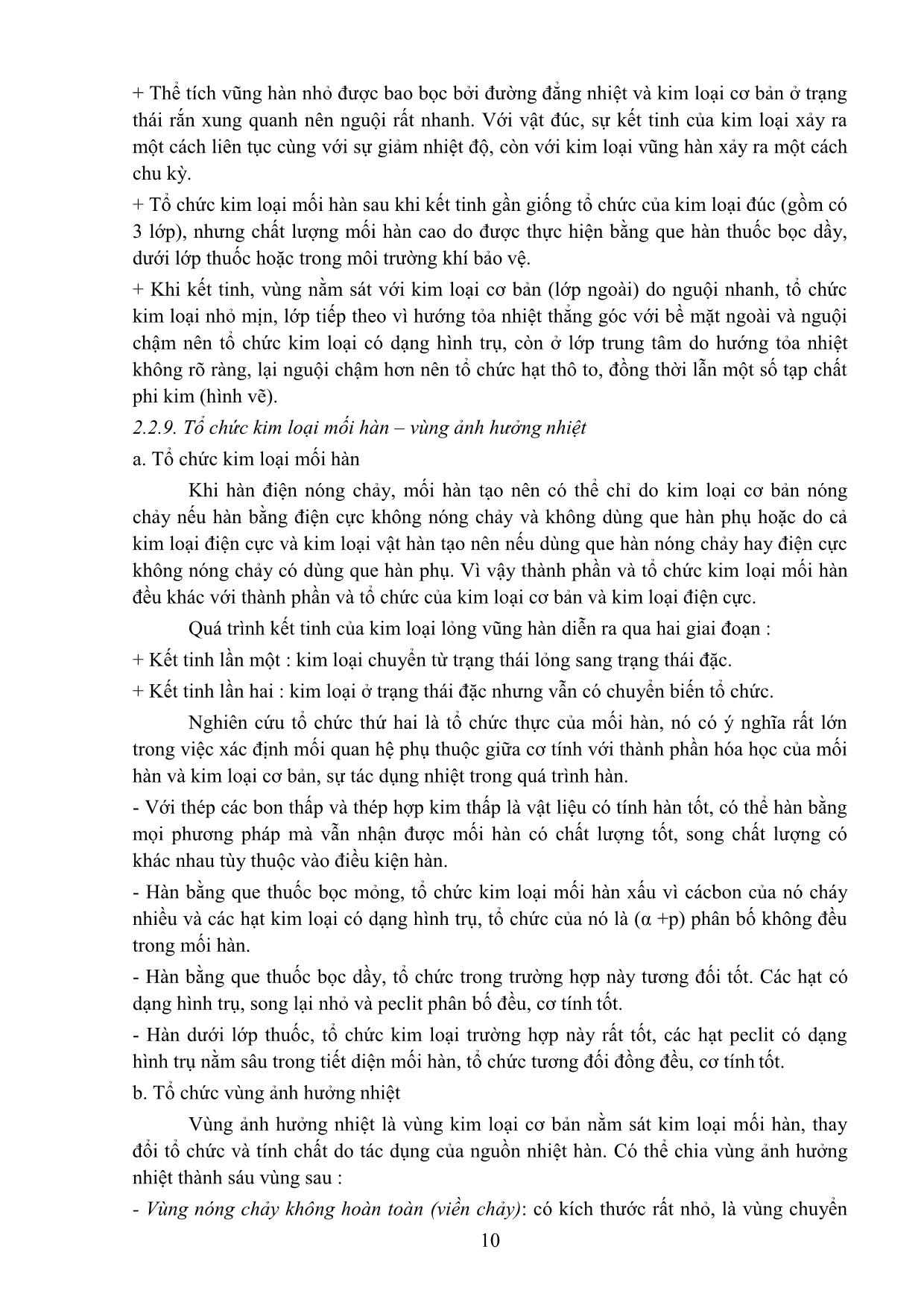
Trang 10
Tải về để xem bản đầy đủ
Tóm tắt nội dung tài liệu: Giáo trình Công nghệ hàn - Nghề: Hàn
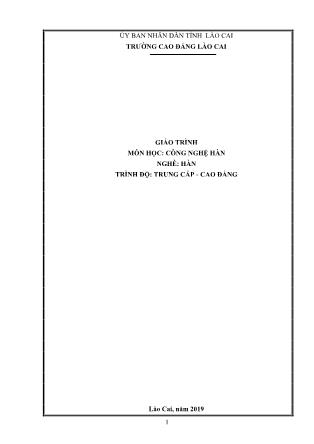
ế chứng minh vật hàn có <3mm thì tốt nhất dùng phương pháp hàn trái. Vật hàn có > 5mm dùng phương pháp hàn phải. - Chọn phương pháp hàn tuỳ thuộc vào vị trí mối hàn trong không gian. Khi hàn bằng có thể hàn phải hoặc trái tùy thuộc theo chiều dày vật hàn. Khi hàn đứng từ dưới lên nên hàn trái những vật hàn có > 8mm nên hàn phải. Khi hàn ngang nên hàn phải vì ngọn 143 lửa hàn hướng trực tiếp vào mối hàn và có tác dụng giữ giọt kim loại không bị rơi. Khi hàn trần tốt nhất hàn trái. 3.4.3. Chuẩn bị chi tiết hàn Căn cứ vào các thông số cơ bản để tiến hành chuẩn bị b h b - chiều rộng mối hàn mm h - Chiều cao mm H S H - Chiều sâu mối hàn mm a S - Chiều dày mm 20 40 60 100 a: khe hở liên kết Vh, m/h 3.4.4. Chế độ hàn 3.4.4.1. Đường kính que hàn Que hàn phụ dùng để hàn phải thoả mãn các yêu cầu như: có đường kính tỷ lệ với chiều dày chi tiết hàn; bề mặt phải sạch( không gỉ, không dính dầu mỡ và các chất bẩn khác); ít gây ra hiện tượng bắn túe kim loại lỏng ra khỏi vũng hàn; không chứa các chất phi kim và dễ tạo thành các bọt khí trong kim loại mối hàn. Ta có thể dùng công thức thực nghiệm sau: + Hàn trái: d = S/2 + 1 (mm) + Hàn phải: d = S/2 (mm) (d - Đường kính que hàn; s - Chiều dày chi tiết hàn) 3.4.4.2. Công suất ngọn lửa Công suất ngọn lửa hàn tính bằng lượng tiêu hao khí trong một giờ, phụ thuộc vào chiều dày và tính chất lý nhiệt của kim loại. Kim loại càng dày, nhiệt độ chảy, tính dẫn nhiệt càng cao thì công suất ngọn lửa càng lớn. Khi hàn thép ít cacbon và thép hợp kim thấp, lượng C2H2 tiêu hao trong một giờ tính theo công thức sau: + Hàn trái: VC2H2 = (100 120) S ( lít/giờ); + Hàn phải: VC2H2 = (120 150) S ( lít/giờ); S - Chiều dày chi tiết (mm) 3.4.4.3. Góc nghiêng mỏ hàn Góc nghiêng của mỏ hàn so với bề mặt chi tiết hàn phụ thuộc chủ yếu vào chiều dày và tính chất lý nhiệt của kim loại hàn. Chiều dày càng lớn, góc nghiêng càng phải lớn. 144 Góc nghiêng mỏ hàn có thể thay đổi trong quá trình hàn. Lúc đầu, để nung nóng kim loại được tốt và hình thành mối hàn nhanh, góc nghiêng mỏ hàn từ 800 900. Trong quá trình hàn được thay đổi cho phù hợp với chiều dày và tính chất của kim loại. Lúc gần kết thúc, để mối hàn được điền đầy và tránh sự chảy của kim loại, phải giảm góc nghiêng của mỏ hàn xuống. Lúc đó ngọn lửa gần như trượt trên bề mặt chi tiết. 3.4.5. Chuyển động của mỏ hàn và que hàn Chuyển động của mỏ hàn và que hàn ảnh hưởng rất lớn đến sự tạo thành mối hàn. Căn cứ vào vị trí mối hàn trong không gian, chiều dày vật hàn, yêu cầu kích thước của mối hàn để chọn chuyển động của mỏ hàn và que hàn cho hợp lý. Để hàn mối hàn sấp bằng phương pháp hàn trái ( không vát mép) khi chiều dày nhỏ hơn 3mm hoặc khi hàn vật tương đối dày bằng phương pháp hàn phải ( vát mép hoặc không vát mép) chuyển động của mỏ hàn và que hàn thường dùng nhất như hình sau: 1 1. Chuyển động của mỏ hàn 2 2. Chuyển động của que hàn Chương 5 : CẮT KIM LOẠI VÀ HỢP KIM Giới thiệu: Cắt kim loại và hợp kim được áp dụng nhiều trong thực tế Mục tiêu: - Hiểu được thực chất, đặc điểm và phạm vi ứng dụng cắt kim loại bằng ngọn lửa khí, cắt bằng hồ quang điện, cắt bằng hồ quang Plasma khí nén 145 - Trình bày được kỹ thuật cắt kim loại bằng ngọn lửa khí, cắt bằng hồ quang điện, cắt bằng hồ quang Plasma khí nén 1. Cắt kim loại bằng ngọn lửa khí cháy với ôxy 1.1. Thực chất, đặc điểm và phạm vi ứng dụng Quá trình cắt khí là sự đốt cháy kim loại bằng dòng O2 để tạo nên các ôxít và các ôxít này bị thổi đi để tạo thành rãnh cắt. Quá trình cắt bắt đầu bằng sự đốt kim loại đến nhiệt độ cháy (ôxy hoá mãnh liệt) nhờ ngọn lửa hàn sau đó cho dòng ôxy thổi qua. Để đốt nóng kim loại đến nhiệt độ cháy, dùng nhiệt của phản ứng giữa O2 và C2H2 (hoặc các loại khí cháy C2H 2, C6H6...). Khi đã đạt đến nhiệt độ cháy, cho dòng O2 kỹ thuật nguyên chất ( 98 đến 99,7% O2) vào ở giữa rãnh mỏ cắt và nó sẽ trực tiếp ôxi hoá kim loại tạo thành ôxít sắt và thổi chúng khỏi rãnh cắt. Sự phát nhiệt trong quá trình cắt giúp cho việc nung nóng vùng xung quanh đến nhiệt độ cháy, do đó dòng O2 cứ tiếp tục mở để cắt cho đến kết thúc đường cắt. Cắt bằng O2 được dùng rộng rãi trong công nghiệp luyện kim và gia công kim loại, xây dựng... Hiện nay cắt bằng phương pháp thủ công vẫn đuợc ứng dụng rộng rãi để cắt thép tấm, thép tròn và các chi tiết đơn giản hay phức tạp... Cắt bằng máy ngày càng đuợc phát triển và có năng suất cao, độ chính xác mép cắt phẳng và hiệu quả kinh tế lớn. * Điều kiện cắt được của kim loại bằng ôxy: Không phải mọi kim loại hay hợp kim loai đều có thể cắt đuợc bằng O2 mà kim loại cắt được phải thoả mãn các điều kiện sau: - Nhiệt độ chảy cần phải cao hơn nhiệt độ cháy với O2. Đối với thép các bon thấp có hàm lượng C (0,7%) nhiệt độ cháy khoảng 1350C, còn nhiệt độ chảy gần 15000C nếu thoả mãn điều kiện này. Đối với thép các bon cao, ví dụ ( từ 1,1 đến 1.2%) nhiệt độ chảy gần bằng nhiệt độ cháy nên trước khi cắt cần phải đốt nóng từ (300 đến 6500C). Đối với thép các bon cao và thép kim cao Crôm - Ni ken, gang, kim loại màu muốn cắt phải dùng thuốc cắt. - Nhiệt độ cháy của ôxít kim loại phải nhỏ hơn nhiệt độ cháy của kim loại đó. Nếu ngược lại lớp ôxít được tạo ra trên bề mặt kim loại vì không bị chảy ra nên khi có dòng O2 thổi vào lớp ôxít sẽ ngăn cản việc ôxi hoá lớp kim loại phía dưới. - Nhiệt lượng sinh ra khi làm kim loại cháy trong dòng O2 phải đủ để duy trì quá trình liên tục. - Tính dẫn nhiệt của kim loại không quá cao, trường hợp quá cao thì nhiệt lượng bị truyền ra xung quanh, làm cho nhiệt độ cắt tại chỗ không đủ hoặc gián đoạn quá trình cắt. 146 - Ôxít phải có tính chảy loãng cao để kim loại dễ bị thổi khỏi rãnh cắt, nếu ngược lại sẽ cản trở dòng O2 tức là cản trở quá trình cắt. - Kim loại dùng để cắt phải hạn chế bớt nồng độ của một số chất làm cản trở quá trình cắt như: C(cacbon), Cr(crom), Si(silich), ....và một số chất nâng cao tính sôi của thép như Mo(mulitden), W(vonpram).... 1.2. Kỹ thuật cắt kim loại bằng ngọn lửa khí cháy với oxi 1.2.1. Bắt đầu cắt Ngọn lửa hướng vào vùng cắt để đốt nóng kim loại đến nhiệt độ cháy để đốt cháy cạnh tấm kim loại. Khi vật tươơng đối dày, mỏ cắt bắt đầu nghiêng đi một góc 5÷100 so với mặt vật cắt, nhằm mục đích làm cho mép vật cắt nung nóng tốt trên toàn bộ chiều dày và bắt đầu quá trình cắt dễ dàng. Khi vật dầy dưới 50mm mỏ cắt bắt đầu đặt thẳng góc với vật. Khi cắt bắt đầu từ giữa tấm ra ngoài cần phải gia công trước một lỗ khi chiều dày nhỏ hơn 20mm có thể dùng mỏ cắt để cắt thành lỗ này, nhưng để tránh ngọn lửa tạt trở vào, trước tiên phải nung nóng đến nhiệt độ chảy sau đó mới phun dòng O2. Bắt đầu đốt vật cắt ở mép sau đó dịch mỏ cắt tới vị trí cắt lỗ. Khi chiều dày vật từ dùng máy khoan để gia công lỗ, sau khi gia công lỗ xong ta bắt đầu cắt từ lỗ ra ngoài. 1.2.2. Khoảng cách từ mỏ cắt đến bề mặt vật cắt 147 Khoảng cách từ nhân ngọn lửa đến vật cắt tốt nhất là 1,5 đến 2,5mm. Khoảng cách từ đầu mỏ đến mặt kim loại khi cắt tấm thép có chiều dày s < 100mm có thể tính như sau: h = L + 2 (mm) L: Chiều dày nhân ngọn lửa (mm) Để khoảng cách này không đổi trong khi cắt ta có thể gá thêm một cặp bánh xe. Khi cắt những tấm dày hơn 100mm, khoảng cách có thể lớn hơn. 1.2.3. Vị trí và sự di chuyển mỏ cắt Khi cắt tấm theo đường thẳng, hợp lý nhất là mỏ cắt nghiêng một góc 20 đến 300 về phía ngược hướng cắt, bằng phương pháp này khi cắt thép dày 20 đến 30mm cho phép nâng cao năng suất của quá trình cắt. 1.2.4. Tốc độ cắt Quá trình cắt ổn định, chất lượng mối cắt tốt, có thể đạt được nếu tốc độ dịch chuyển của mỏ cắt tương ứng với tốc độ ôxy hoá kim loại theo chiều dày tấm cắt hoặc phôi. Tốc độ cắt nhỏ sẽ làm hỏng mép cắt, tốc độ cắt lớn sẽ làm sót lại nhiều không cắt hết và phá huỷ quá trình cắt. Tốc độ cắt chọn trên bảng chế độ cắt. 2. Cắt bằng hồ quang điện 2.1. Thực chất, đặc điểm và phạm vi ứng dụng a. Thực chất: C¾t kim lo¹i b»ng hå quang lµ lîi dông nhiÖt cña hå quang lµm nãng ch¶y kim lo¹i ë chç c¾t vµ ®Èy nã ra khái ®ã ®Ó t¹o thµnh r·nh c¾t nhê ¸p lùc cña hå quang vµ träng l•îng riªng cña kim lo¹i láng b. Đặc điểm: - Qu¸ tr×nh c¾t b»ng c¸c m¸y hµn th«ng th•êng, kh«ng cÇn yªu cÇu thiÕt bÞ ®Æc biÖt. - Cã thÓ c¾t b×nh th•êng c¸c thÐp hîp kim cao, gang, kim lo¹i vµ hîp kim mµu 148 - C¾t ®•îc ë mäi vÞ trÝ trong kh«ng gian - C¾t b»ng hå quang nãi chung cho m¨ng suÊt thÊp - Khi c¾t b»ng hå quang th•êng mÐp c¾t kh«ng ph¼ng, xï x× ®ång thêi phÇn kim lo¹i bá ®i khi c¾t lín - Khã thùc hiÖn khi chiÒu dµy vËt c¾t lín - L•îng tiªu hao ®iÖn cùc lín, gi¸ thµnh cao c. Phạm vi ứng dụng: Dùng để cắt kim loại và hợp kim mà không cắt được bằng khí: Gang, đồng, thép k... 2.2. Kü thuËt c¾t kim loại bằng hồ quang điện C¾t kim lo¹i b»ng hå quang cã thÓ dùng ®iÖn cùc nãng ch¶y vµ ®iÖn cùc kh«ng nãng ch¶y. Dßng ®iÖn dïng ®Ó c¾t sö dông ®•îc c¶ dßng xoay chiÒu vµ dßng mét chiÒu. NÕu dùng dßng mét chiÒu th× ®Êu thuËn ®Ó cho ®iÖn cùc kh«ng qu¸ nãng. 2.2.1. ChuÈn bÞ vËt c¾t vµ v¹ch dÊu - VËt c¾t ph¶i ®•îc lµm s¹ch cÈn thËn tr•íc khi c¾t ®Ó ®¶m b¶o chÊt l•îng cña ®•êng c¾t vµ gi¶m ®éc h¹i cho ng•êi thao t¸c - Khi v¹ch dÊu ph¶i ®¶m b¶o yªu cÇu kÝch th•íc vµ ph¶I tÝnh to¸n sao cho tiÕt kiÖm ®•îc kim lo¹i nhÊt. 2.2.2. Gi¸ vËt c¾t Tr•íc khi c¾t, vËt c¾t ph¶i ®•îc ®Æt trªn g¸ ®Ó t¹o nªn kho¶ng trèng thÝch hîp cho qu¸ tr×nh c¾t. NÕu kho¶ng trèng qu¸ thÊp sÏ ¶nh h•ëng ®Õn ¸p lùc cña hå quang lµm vËt c¾t kh«ng ®¶m b¶o yªu cÇu chÊt l•îng. NÕu kho¶n trèng qu¸ caosÏ kh«ng ®¶m b¶o an toµn trong qu¸ tr×nh thao t¸c. Do vËy khi c¾t vËt th•êng ®Æt lªn gi¸ cao (179 – 280)mm 2.2.3. TiÕn hµnh c¾t a. Chän que hµn: Que hµn dïng ®Ó c¾t th•êng ding que hµn cã thuèc bäc dµy ®Ó r·nh c¾t gän vµ nhá. §•êng kÝnh que hµn chän cÇn c¨n cø vµo chiÒu dµy vËt c¾t. b. C•êng ®é dßng ®iÖn: C•êng ®é dßng ®iÖn khi c¾t ph¶I lÊy cao h¬n so víi khi hµn kho¶ng 30%. C•êng ®é dßng ®iÖn khi c¾t lÊy theo c«ng thøc: 149 I = (50-60)dqh c. Gãc nghiªng que hµn - C¨n cø vµo chiÒu dµy vËt c¾t ®Ó chän gãc nghiªng que hµn cho thÝch hîp - Lóc b¾t ®Çu c¾t que hµn ph¶I ®Æt vu«ng gãc víi bÒ mÆt vËt c¾t, sau ®ã nghiªng que hµn vÒ phÝa ng•îc víi h•íng c¾t mét gãc = (60 – 90o) d. ChuyÓn ®éng que hµn * C¾t tÊm dµy: Ngoµi chuyÓn ®éng theo trôc r·nh c¾t, que hµn cßn cã chuyÓn ®éng lªn xuèng kh«ng ngõng gi÷a mÆt ph¼ng trªn vµ mÆt ph¼ng d•íi cña tÊm c¾t * C¾t tÊm máng: Que hµn chØ cÇn chuyÓn ®éng däc theo r·nh c¾t mµ kh«ng cÇn cã chuyÓn ®éng lªn xuèng. - Khi c¾t theo ®•êng th¼ng, ®Ó lµm dÔ dµng c«ng viÖc, ng•êi ta ding d•ìng ®Æt theo r·nh c¾t. - C¾t c¸c ®•êng c¾t dµi ph¶i chia ®•êng c¾t ra thµnh nhiÒu phÇn b»ng nhau vµ dïng c¸ch c¾t nh•îc chiÒu, so le. Khi c¾t kh«ng c¾t ®øt ngay mµ ®Ó l¹i mét gê nhá ë giao ®iÓm gi÷a c¸c ®•êng c¾t ë tõng ®o¹n ®Ó tr¸nh vËt c¾t bÞ cong vªnh. - C¾t b»ng hå quang, chiÒu dµy vËt c¾t kh«ng nªn qu¸ 30 mm vµ khi c¾t ph¶I sö dông hå quang dµi h¬n khi hµn. - §Ó rót ng¾n qu¸ tr×nh c¾t, cã thÓ tiÕn hµnh c¾t hå quang O2 3. Cắt bằng hồ quang plasma khí nén 3.1. Thực chất, đặc điểm và phạm vi ứng dụng - Plasma là một dạng vật chất thứ tư tồn tại sau thể rắn thể lỏng và thể khí. Plasma có cấu tạo bên trong gần giống như hồ quang điện, tức là một môi trường ion, plasma gồm các ion được gia tốc lớn lên nó có động năng mạnh. Khi được phun ra khỏi miệng phun nó có năng lượng nhiệt lớn, có thể làm nóng chảy tức thời kim loại trên đường đi của nó. 150 Hình 13.5.1 Nguyên lý hoạt động của máy cắt Plasma - Trong cắt kim loại người ta dùng không khí nén hoặc argon làm môi trường tạo ra plasma. - Ở các nước công nghiệp phát triển người ta đã ứng dụng rất rộng rãi các máy hàn cắt bằng plasma. Phương pháp hàn cắt bằng kỹ thuật plasma có năng suất cao hơn 1,5 đến 2 lần so với kỹ thuật khí, chất lượng mối hàn, đường cắt cao hơn hẳn, sạch sẽ không gây ô nhiễm môi trường, không có nguy cơ gây nổ, đa năng linh hoạt dễ di chuyển, giảm chi phí vận hành 1,5 đến 3 lần, mau hoàn vốn. Các loại máy hàn, cắt dùng plasma có rất nhiều kiểu loại. - Nhiệt độ của plasma rất cao cho phép cắt với chiều dày kim loại lớn, có thể cắt mọi kim loại và hợp kim. 3.2. Kỹ thuật cắt kim loại bằng hồ quang plasma khí nén Hình 3.4. Cắt đường thẳng Hình 3.5. Cắt đường tròn bằng compa - Do công suất lớn và tốc độ nung chảy cao, vận tốc cắt lớn nên khi cắt phải có compa và thước làm dưỡng tránh lệch đường vạch dấu - Năng lượng cột plasma lớn nến khi cắt từ trong ra không cần khoan lỗ như cắt khí a. Cắt tiếp xúc Khi cắt vật liệu tấm mỏng có chiều dày nhỏ hơn 9 ÷ 12mm, tốt nhất là sử dụng bép cắt loại “S”. Góc độ thích hợp của mỏ cắt với tấm cắt là 900 ± 50 151 - Bấm công tắc trên mỏ sẽ phát sinh hồ quang dẫn sau 1,5s - Đưa đầu bép cắt cách điểm bắt đầu cắt khoảng 1 ÷ 3mm, khi đó hồ quang plasma sẽ phát sinh - Để bép cắt tiếp xúc với bề mặt cắt theo đường vạch dấu một cách nhẹ nhàng và tiến hành di chuyển mỏ cắt - Khi cắt gần đến điểm cuối đường cắt, nhấc đầu bép cắt lên cách tấm khoảng 1 ÷ 3mm và tiếp tục cắt đến hết đường cắt. ÷3 c¾t tiÕp xóc hå quang 1 dÉn hå quang plasma Hình 3.6. Sơ đồ cắt tiếp xúc Nếu bấm công tắc mỏ cắt khi mỏ cắt tiếp xúc vuông góc với tấm cắt thì khí nén sẽ không thổi ra ngoài được và hồ quang sinh ra đốt cháy bên trong bép cắt. Vì lý do đó nên phải bấm công tắc trước khi cho bép cắt tiếp xúc với vật cắt và cho đầu bép cắt tiếp xúc nhẹ nhàng với bề mặt tấm cắt. Tốc độ cắt chính xác thì hồ quang plasma thổi nhẹ nhàng. Nếu tốc độ cắt lớn sẽ xảy ra hiện tượng thổi ngược lại, còn khi tốc độ cắt chậm thì sẽ làm kim loại trên bề mặt tấm cắt bị chảy nhiều. b. Cắt không tiếp xúc bằng tay Khi cắt các tấm có chiều dày lớn hoặc trung bình (lớn hơn 9mm) cần điều chỉnh mỏ cắt sao cho khoảng cách giữa đầu bép cắt với bề mặt tấm cắt từ 2 ÷ 4mm. Sử dụng bép cắt loại “H”, các bước thực hiện như cắt không tiếp xúc. c¾t kh«ng tiÕp ÷4 xóc hå quang 2 dÉn hå quang plasma Hình 3.7. Sơ đồ cắt không tiếp xúc 152 c. Cắt tự động Với máy cắt plasma tự động người vận hành chỉ cần khai báo các thông số cần thiết như loại vật liệu, chiều dày vật liệu và chất lượng cắt các thông số còn lại máy sẽ tự nội suy và vận hành một cách tối ưu hóa. Tuy vậy một số trường hợp thành phần kim loại cắt không đúng tiêu chuẩn hoặc người cắt không biết chính xác dẫn đến việc khai báo sai làm ảnh hưởng tới quá trình cắt. Trong trường hợp này người vận hành có thể điều chỉnh một khoảng nhỏ thông số này để phù hợp với thực tế. Để chuẩn bị cho quá trình cắt người thợ có thể tham khảo bảng chế độ để tính toán phôi liệu và chuẩn bị dụng cụ thiết bị phù hợp 153 154 155 156 157 158 159 160 161 162 163 164 165 166 167
File đính kèm:
giao_trinh_cong_nghe_han_nghe_han.pdf