Nghiên cứu quá trình cháy bột than và nâng cao hiệu quả đốt than trộn trong các lò hơi đốt than phun trên mô hình mô phỏng
Việc nghiên cứu nâng cao hiệu suất cháy than đặc biệt là than antraxit khó cháy của Việt Nam
đã là một nhu cầu thực tế cấp bách. Mục tiêu chính của nghiên cứu là ứng dụng phần mềm CFD để
nghiên cứu, đánh giá quá trình cháy bột than trong lò hơi đốt than phun kiểu tiếp tuyến và nghiên cứu
ảnh hưởng của việc trộn than nhập khẩu Indonexia (á-bitum) với than nội địa (Hòn Gai) đến quá trình
cháy. Kết quả phân tích khí động học và nhiệt độ cho thấy quá trình cháy tạo thành vùng trung tâm
buồng đốt, nhiệt độ trong khoảng 1540oC – 1640oC. Thời gian lưu lại các hạt than trong buồng đốt lớn
hơn 3 giây đủ thời gian để cháy kiệt hạt than. Tỷ lệ chuyển hóa cốc cao (99.48%). Tỷ lệ chuyển hóa cốc
tăng lên 99.63% khi tỷ lệ trộn than nhập là 5%, tuy nhiên khi tăng tỷ lệ trộn lên 10% và 20% thì tỷ lệ
chuyển hóa cốc giảm xuống tương ứng là 99.57% và 99.45.Tốc độ cháy chất bốc tăng, tốc độ cháy cốc
giảm khi tăng tỷ lệ trộn.

Trang 1
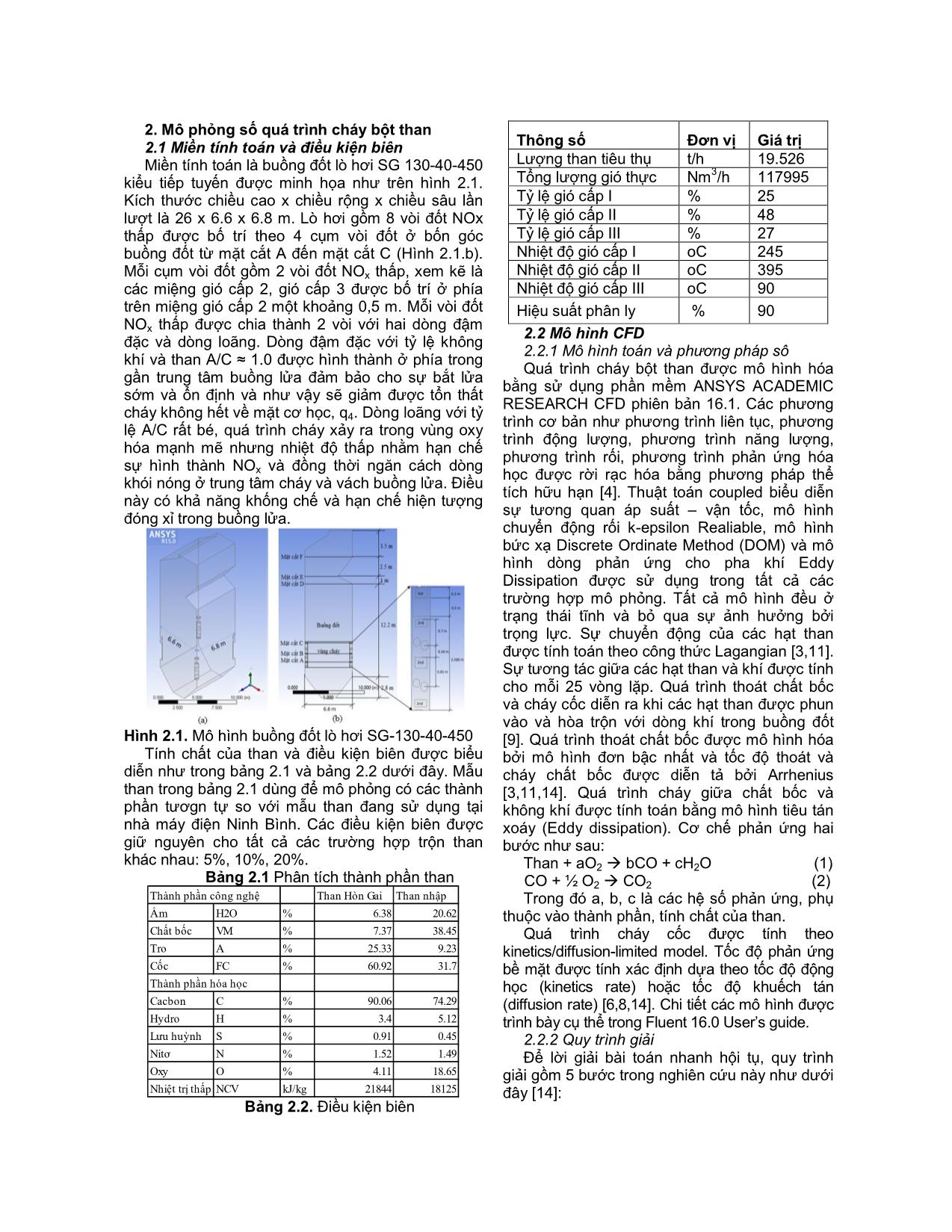
Trang 2
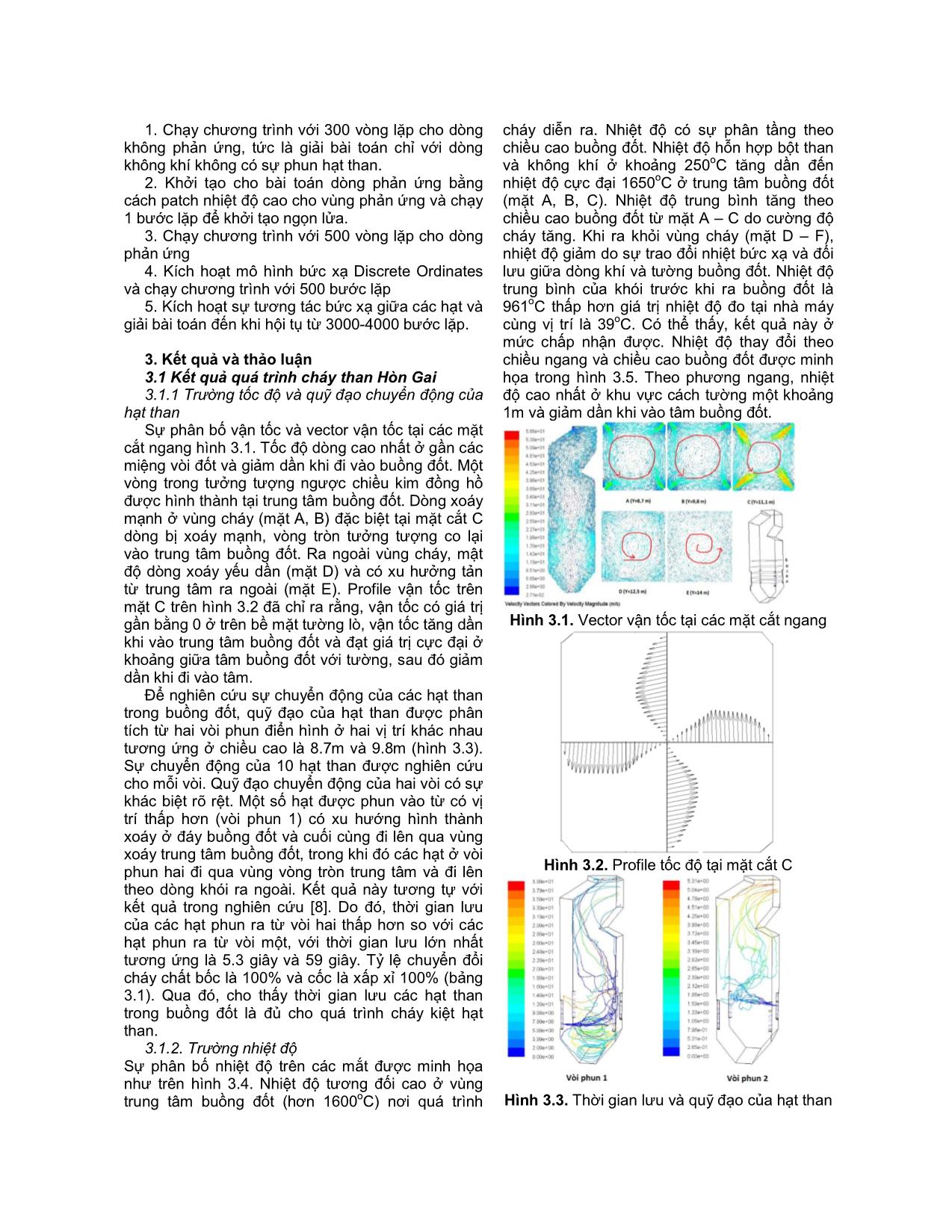
Trang 3
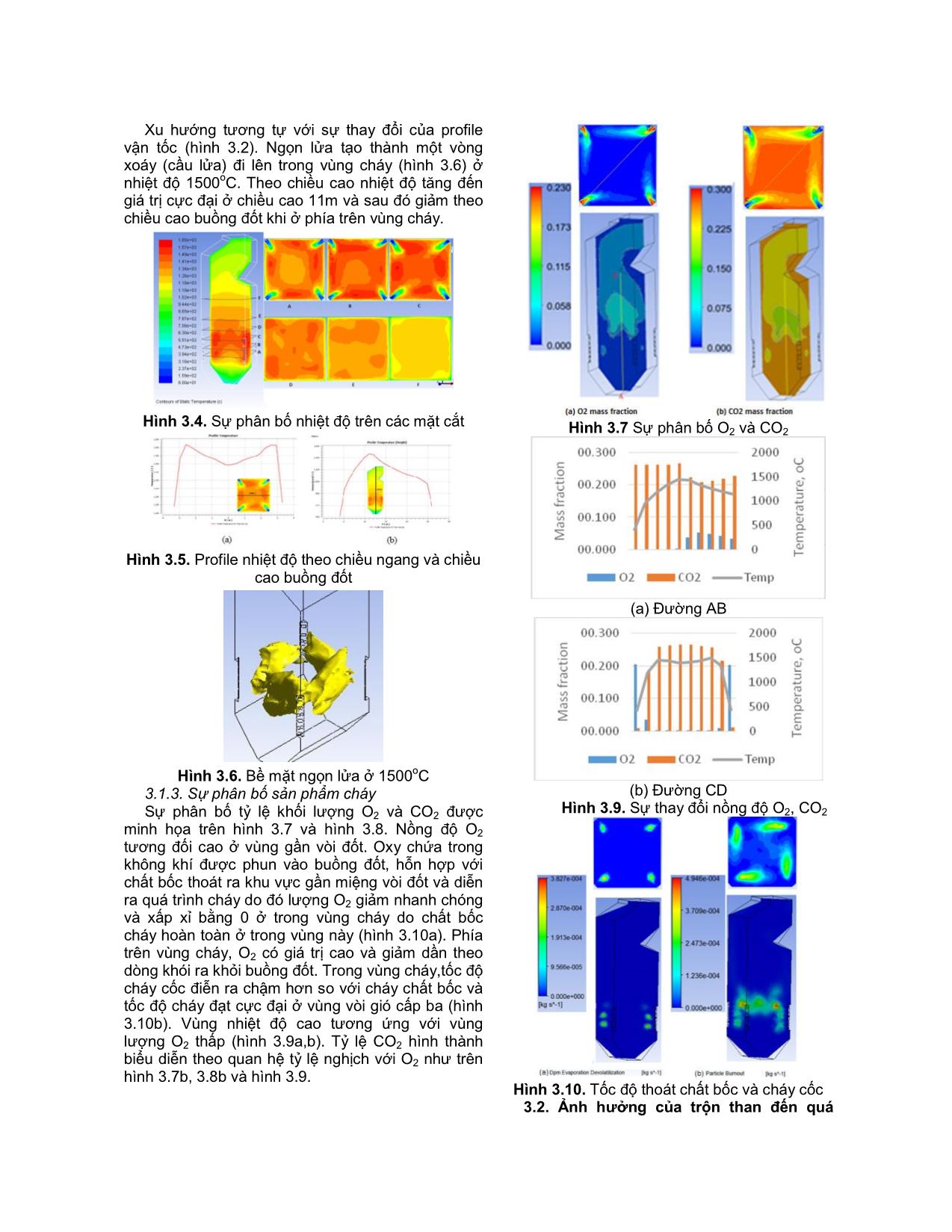
Trang 4
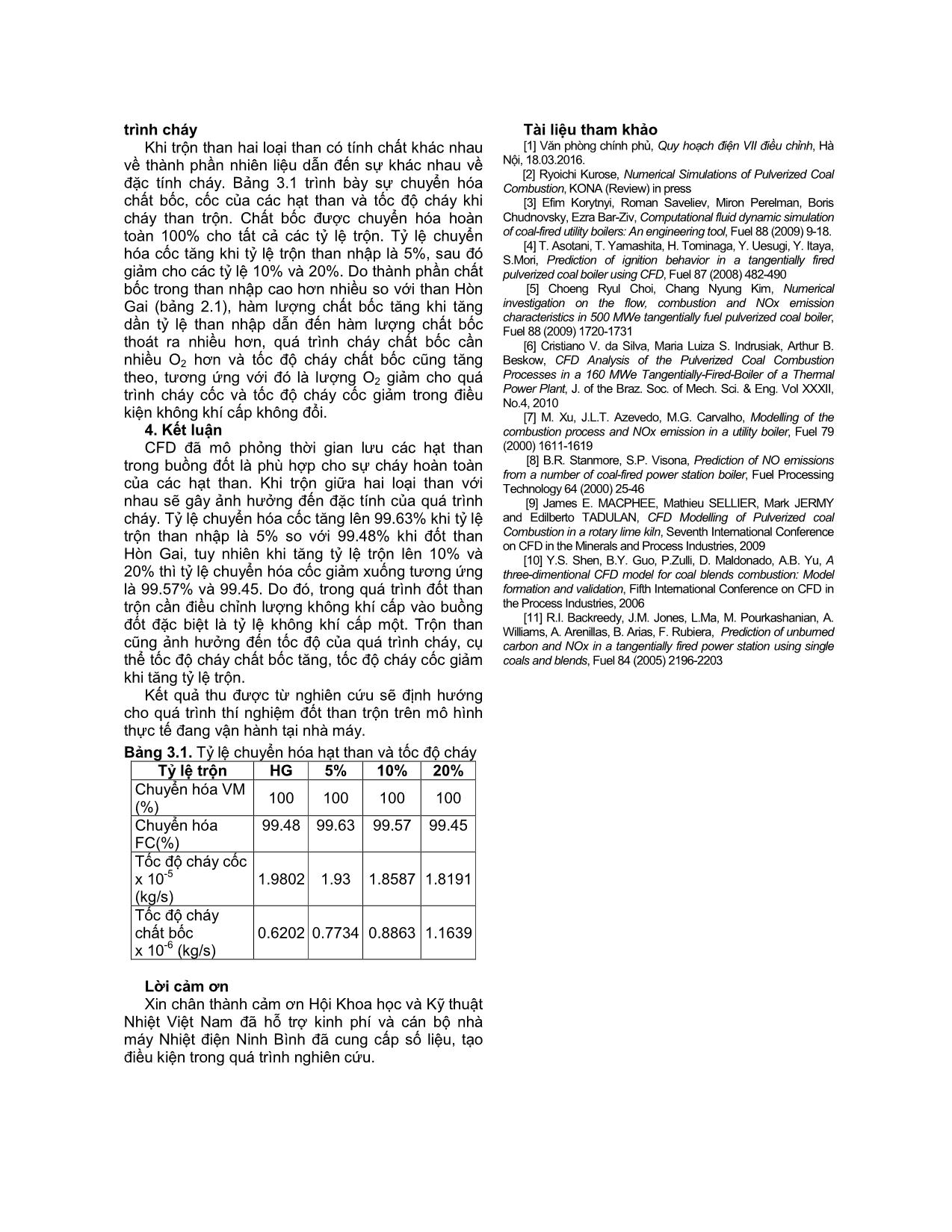
Trang 5
Tóm tắt nội dung tài liệu: Nghiên cứu quá trình cháy bột than và nâng cao hiệu quả đốt than trộn trong các lò hơi đốt than phun trên mô hình mô phỏng
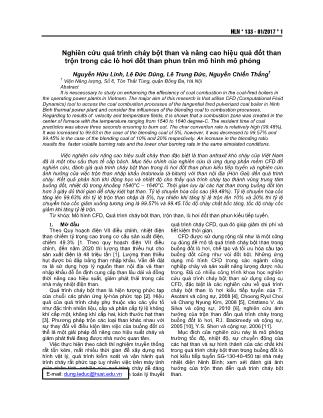
khí cấp hai, kích thước hạt than [3]. Phương pháp trộn các loại than khác nhau với sự thay đổi về điều kiện làm việc của buồng đốt có thể là một giải pháp để nâng cao hiệu suất cháy và giảm phát thải đang được nhà nước quan tâm. Việc thực hiện theo cách thí nghiệm truyền thống rất tốn kém, mất nhiều thời gian để xây dựng mô hình vật lý, quá trình kiểm soát và vận hành quá trình cháy rất phức tạp tuy nhiên việc trên máy tính giúp phân tích, nghiên cứu quá trình cháy dễ dàng hơn rất nhiều thông qua công cụ tính toán lý thuyết quá trình cháy CFD, qua đó giúp giảm chi phí và tiết kiệm thời gian. CFD được sử dụng rộng rãi như là một công cụ dùng để mô tả quá trình cháy bột than trong buồng đốt lò hơi, chế tạo và tối ưu hóa cấu tạo buồng đốt cũng như vòi đốt bột. Những ứng dụng mô hình CFD trong các ngành công nghiệp cháy và sản xuất năng lượng được nêu trong. Đã có nhiều công trình khoa học nghiên cứu quá trình cháy bột than sử dụng công cụ CFD, đặc biệt là các nghiên cứu về quá trình cháy bột than lò hơi kiểu tiếp tuyến của T. Asotani và cộng sự, 2008 [4], Choeng Ryul Choi và Chang Nyung Kim, 2008 [5], Cristiano V. da Silva và cộng sự, 2010 [6], nghiên cứu ảnh hưởng của trộn than đến quá trình cháy trong buồng đốt lò hơi, R.I. Backreedy và cộng sự, 2005 [10], Y.S. Shen và cộng sự, 2006 [11]. Mục đích của nghiên cứu này là mô phỏng trường tốc độ, nhiệt độ, sự chuyển động của các hạt than và sự hình thành của các chất khí trong quá trình cháy bột than trong buồng đốt lò hơi kiểu tiếp tuyến SG-130-40-450 tại nhà máy nhiệt điện Ninh Bình; xem xét đánh giá ảnh hưởng của trộn than đến quá trình cháy bột than. E-mail: dung.leduc@hust.edu.vn 2. Mô phỏng số quá trình cháy bột than 2.1 Miền tính toán và điều kiện biên Miền tính toán là buồng đốt lò hơi SG 130-40-450 kiểu tiếp tuyến được minh họa như trên hình 2.1. Kích thước chiều cao x chiều rộng x chiều sâu lần lượt là 26 x 6.6 x 6.8 m. Lò hơi gồm 8 vòi đốt NOx thấp được bố trí theo 4 cụm vòi đốt ở bốn góc buồng đốt từ mặt cắt A đến mặt cắt C (Hình 2.1.b). Mỗi cụm vòi đốt gồm 2 vòi đốt NOx thấp, xem kẽ là các miệng gió cấp 2, gió cấp 3 được bố trí ở phía trên miệng gió cấp 2 một khoảng 0,5 m. Mỗi vòi đốt NOx thấp được chia thành 2 vòi với hai dòng đậm đặc và dòng loãng. Dòng đậm đặc với tỷ lệ không khí và than A/C ≈ 1.0 được hình thành ở phía trong gần trung tâm buồng lửa đảm bảo cho sự bắt lửa sớm và ổn định và như vậy sẽ giảm được tổn thất cháy không hết về mặt cơ học, q4. Dòng loãng với tỷ lệ A/C rất bé, quá trình cháy xảy ra trong vùng oxy hóa mạnh mẽ nhưng nhiệt độ thấp nhằm hạn chế sự hình thành NOx và đồng thời ngăn cách dòng khói nóng ở trung tâm cháy và vách buồng lửa. Điều này có khả năng khống chế và hạn chế hiện tượng đóng xỉ trong buồng lửa. Hình 2.1. Mô hình buồng đốt lò hơi SG-130-40-450 Tính chất của than và điều kiện biên được biểu diễn như trong bảng 2.1 và bảng 2.2 dưới đây. Mẫu than trong bảng 2.1 dùng để mô phỏng có các thành phần tươgn tự so với mẫu than đang sử dụng tại nhà máy điện Ninh Bình. Các điều kiện biên được giữ nguyên cho tất cả các trường hợp trộn than khác nhau: 5%, 10%, 20%. Bảng 2.1 Phân tích thành phần than Than Hòn Gai Than nhập Ẩm H2O % 6.38 20.62 Chất bốc VM % 7.37 38.45 Tro A % 25.33 9.23 Cốc FC % 60.92 31.7 Cacbon C % 90.06 74.29 Hydro H % 3.4 5.12 Lưu huỳnh S % 0.91 0.45 Nitơ N % 1.52 1.49 Oxy O % 4.11 18.65 Nhiệt trị thấp NCV kJ/kg 21844 18125 Thành phần công nghệ Thành phần hóa học Bảng 2.2. Điều kiện biên Thông số Đơn vị Giá trị Lượng than tiêu thụ t/h 19.526 Tổng lượng gió thực Nm3/h 117995 Tỷ lệ gió cấp I % 25 Tỷ lệ gió cấp II % 48 Tỷ lệ gió cấp III % 27 Nhiệt độ gió cấp I oC 245 Nhiệt độ gió cấp II oC 395 Nhiệt độ gió cấp III oC 90 Hiệu suất phân ly % 90 2.2 Mô hình CFD 2.2.1 Mô hình toán và phương pháp sô Quá trình cháy bột than được mô hình hóa bằng sử dụng phần mềm ANSYS ACADEMIC RESEARCH CFD phiên bản 16.1. Các phương trình cơ bản như phương trình liên tục, phương trình động lượng, phương trình năng lượng, phương trình rối, phương trình phản ứng hóa học được rời rạc hóa bằng phương pháp thể tích hữu hạn [4]. Thuật toán coupled biểu diễn sự tương quan áp suất – vận tốc, mô hình chuyển động rối k-epsilon Realiable, mô hình bức xạ Discrete Ordinate Method (DOM) và mô hình dòng phản ứng cho pha khí Eddy Dissipation được sử dụng trong tất cả các trường hợp mô phỏng. Tất cả mô hình đều ở trạng thái tĩnh và bỏ qua sự ảnh hưởng bởi trọng lực. Sự chuyển động của các hạt than được tính toán theo công thức Lagangian [3,11]. Sự tương tác giữa các hạt than và khí được tính cho mỗi 25 vòng lặp. Quá trình thoát chất bốc và cháy cốc diễn ra khi các hạt than được phun vào và hòa trộn với dòng khí trong buồng đốt [9]. Quá trình thoát chất bốc được mô hình hóa bởi mô hình đơn bậc nhất và tốc độ thoát và cháy chất bốc được diễn tả bởi Arrhenius [3,11,14]. Quá trình cháy giữa chất bốc và không khí được tính toán bằng mô hình tiêu tán xoáy (Eddy dissipation). Cơ chế phản ứng hai bước như sau: Than + aO2 bCO + cH2O (1) CO + ½ O2 CO2 (2) Trong đó a, b, c là các hệ số phản ứng, phụ thuộc vào thành phần, tính chất của than. Quá trình cháy cốc được tính theo kinetics/diffusion-limited model. Tốc độ phản ứng bề mặt được tính xác định dựa theo tốc độ động học (kinetics rate) hoặc tốc độ khuếch tán (diffusion rate) [6,8,14]. Chi tiết các mô hình được trình bày cụ thể trong Fluent 16.0 User’s guide. 2.2.2 Quy trình giải Để lời giải bài toán nhanh hội tụ, quy trình giải gồm 5 bước trong nghiên cứu này như dưới đây [14]: 1. Chạy chương trình với 300 vòng lặp cho dòng không phản ứng, tức là giải bài toán chỉ với dòng không khí không có sự phun hạt than. 2. Khởi tạo cho bài toán dòng phản ứng bằng cách patch nhiệt độ cao cho vùng phản ứng và chạy 1 bước lặp để khởi tạo ngọn lửa. 3. Chạy chương trình với 500 vòng lặp cho dòng phản ứng 4. Kích hoạt mô hình bức xạ Discrete Ordinates và chạy chương trình với 500 bước lặp 5. Kích hoạt sự tương tác bức xạ giữa các hạt và giải bài toán đến khi hội tụ từ 3000-4000 bước lặp. 3. Kết quả và thảo luận 3.1 Kết quả quá trình cháy than Hòn Gai 3.1.1 Trường tốc độ và quỹ đạo chuyển động của hạt than Sự phân bố vận tốc và vector vận tốc tại các mặt cắt ngang hình 3.1. Tốc độ dòng cao nhất ở gần các miệng vòi đốt và giảm dần khi đi vào buồng đốt. Một vòng trong tưởng tượng ngược chiều kim đồng hồ được hình thành tại trung tâm buồng đốt. Dòng xoáy mạnh ở vùng cháy (mặt A, B) đặc biệt tại mặt cắt C dòng bị xoáy mạnh, vòng tròn tưởng tượng co lại vào trung tâm buồng đốt. Ra ngoài vùng cháy, mật độ dòng xoáy yếu dần (mặt D) và có xu hưởng tản từ trung tâm ra ngoài (mặt E). Profile vận tốc trên mặt C trên hình 3.2 đã chỉ ra rằng, vận tốc có giá trị gần bằng 0 ở trên bề mặt tường lò, vận tốc tăng dần khi vào trung tâm buồng đốt và đạt giá trị cực đại ở khoảng giữa tâm buồng đốt với tường, sau đó giảm dần khi đi vào tâm. Để nghiên cứu sự chuyển động của các hạt than trong buồng đốt, quỹ đạo của hạt than được phân tích từ hai vòi phun điển hình ở hai vị trí khác nhau tương ứng ở chiều cao là 8.7m và 9.8m (hình 3.3). Sự chuyển động của 10 hạt than được nghiên cứu cho mỗi vòi. Quỹ đạo chuyển động của hai vòi có sự khác biệt rõ rệt. Một số hạt được phun vào từ có vị trí thấp hơn (vòi phun 1) có xu hướng hình thành xoáy ở đáy buồng đốt và cuối cùng đi lên qua vùng xoáy trung tâm buồng đốt, trong khi đó các hạt ở vòi phun hai đi qua vùng vòng tròn trung tâm và đi lên theo dòng khói ra ngoài. Kết quả này tương tự với kết quả trong nghiên cứu [8]. Do đó, thời gian lưu của các hạt phun ra từ vòi hai thấp hơn so với các hạt phun ra từ vòi một, với thời gian lưu lớn nhất tương ứng là 5.3 giây và 59 giây. Tỷ lệ chuyển đổi cháy chất bốc là 100% và cốc là xấp xỉ 100% (bảng 3.1). Qua đó, cho thấy thời gian lưu các hạt than trong buồng đốt là đủ cho quá trình cháy kiệt hạt than. 3.1.2. Trường nhiệt độ Sự phân bố nhiệt độ trên các mắt được minh họa như trên hình 3.4. Nhiệt độ tương đối cao ở vùng trung tâm buồng đốt (hơn 1600oC) nơi quá trình cháy diễn ra. Nhiệt độ có sự phân tầng theo chiều cao buồng đốt. Nhiệt độ hỗn hợp bột than và không khí ở khoảng 250oC tăng dần đến nhiệt độ cực đại 1650oC ở trung tâm buồng đốt (mặt A, B, C). Nhiệt độ trung bình tăng theo chiều cao buồng đốt từ mặt A – C do cường độ cháy tăng. Khi ra khỏi vùng cháy (mặt D – F), nhiệt độ giảm do sự trao đổi nhiệt bức xạ và đối lưu giữa dòng khí và tường buồng đốt. Nhiệt độ trung bình của khói trước khi ra buồng đốt là 961oC thấp hơn giá trị nhiệt độ đo tại nhà máy cùng vị trí là 39oC. Có thể thấy, kết quả này ở mức chấp nhận được. Nhiệt độ thay đổi theo chiều ngang và chiều cao buồng đốt được minh họa trong hình 3.5. Theo phương ngang, nhiệt độ cao nhất ở khu vực cách tường một khoảng 1m và giảm dần khi vào tâm buồng đốt. Hình 3.1. Vector vận tốc tại các mặt cắt ngang Hình 3.2. Profile tốc độ tại mặt cắt C Hình 3.3. Thời gian lưu và quỹ đạo của hạt than Xu hướng tương tự với sự thay đổi của profile vận tốc (hình 3.2). Ngọn lửa tạo thành một vòng xoáy (cầu lửa) đi lên trong vùng cháy (hình 3.6) ở nhiệt độ 1500oC. Theo chiều cao nhiệt độ tăng đến giá trị cực đại ở chiều cao 11m và sau đó giảm theo chiều cao buồng đốt khi ở phía trên vùng cháy. Hình 3.4. Sự phân bố nhiệt độ trên các mặt cắt Hình 3.5. Profile nhiệt độ theo chiều ngang và chiều cao buồng đốt Hình 3.6. Bề mặt ngọn lửa ở 1500oC 3.1.3. Sự phân bố sản phẩm cháy Sự phân bố tỷ lệ khối lượng O2 và CO2 được minh họa trên hình 3.7 và hình 3.8. Nồng độ O2 tương đối cao ở vùng gần vòi đốt. Oxy chứa trong không khí được phun vào buồng đốt, hỗn hợp với chất bốc thoát ra khu vực gần miệng vòi đốt và diễn ra quá trình cháy do đó lượng O2 giảm nhanh chóng và xấp xỉ bằng 0 ở trong vùng cháy do chất bốc cháy hoàn toàn ở trong vùng này (hình 3.10a). Phía trên vùng cháy, O2 có giá trị cao và giảm dần theo dòng khói ra khỏi buồng đốt. Trong vùng cháy,tốc độ cháy cốc điễn ra chậm hơn so với cháy chất bốc và tốc độ cháy đạt cực đại ở vùng vòi gió cấp ba (hình 3.10b). Vùng nhiệt độ cao tương ứng với vùng lượng O2 thấp (hình 3.9a,b). Tỷ lệ CO2 hình thành biểu diễn theo quan hệ tỷ lệ nghịch với O2 như trên hình 3.7b, 3.8b và hình 3.9. Hình 3.7 Sự phân bố O2 và CO2 (a) Đường AB (b) Đường CD Hình 3.9. Sự thay đổi nồng độ O2, CO2 Hình 3.10. Tốc độ thoát chất bốc và cháy cốc 3.2. Ảnh hưởng của trộn than đến quá trình cháy Khi trộn than hai loại than có tính chất khác nhau về thành phần nhiên liệu dẫn đến sự khác nhau về đặc tính cháy. Bảng 3.1 trình bày sự chuyển hóa chất bốc, cốc của các hạt than và tốc độ cháy khi cháy than trộn. Chất bốc được chuyển hóa hoàn toàn 100% cho tất cả các tỷ lệ trộn. Tỷ lệ chuyển hóa cốc tăng khi tỷ lệ trộn than nhập là 5%, sau đó giảm cho các tỷ lệ 10% và 20%. Do thành phần chất bốc trong than nhập cao hơn nhiều so với than Hòn Gai (bảng 2.1), hàm lượng chất bốc tăng khi tăng dần tỷ lệ than nhập dẫn đến hàm lượng chất bốc thoát ra nhiều hơn, quá trình cháy chất bốc cần nhiều O2 hơn và tốc độ cháy chất bốc cũng tăng theo, tương ứng với đó là lượng O2 giảm cho quá trình cháy cốc và tốc độ cháy cốc giảm trong điều kiện không khí cấp không đổi. 4. Kết luận CFD đã mô phỏng thời gian lưu các hạt than trong buồng đốt là phù hợp cho sự cháy hoàn toàn của các hạt than. Khi trộn giữa hai loại than với nhau sẽ gây ảnh hưởng đến đặc tính của quá trình cháy. Tỷ lệ chuyển hóa cốc tăng lên 99.63% khi tỷ lệ trộn than nhập là 5% so với 99.48% khi đốt than Hòn Gai, tuy nhiên khi tăng tỷ lệ trộn lên 10% và 20% thì tỷ lệ chuyển hóa cốc giảm xuống tương ứng là 99.57% và 99.45. Do đó, trong quá trình đốt than trộn cần điều chỉnh lượng không khí cấp vào buồng đốt đặc biệt là tỷ lệ không khí cấp một. Trộn than cũng ảnh hưởng đến tốc độ của quá trình cháy, cụ thể tốc độ cháy chất bốc tăng, tốc độ cháy cốc giảm khi tăng tỷ lệ trộn. Kết quả thu được từ nghiên cứu sẽ định hướng cho quá trình thí nghiệm đốt than trộn trên mô hình thực tế đang vận hành tại nhà máy. Bảng 3.1. Tỷ lệ chuyển hóa hạt than và tốc độ cháy Tỷ lệ trộn HG 5% 10% 20% Chuyển hóa VM (%) 100 100 100 100 Chuyển hóa FC(%) 99.48 99.63 99.57 99.45 Tốc độ cháy cốc x 10-5 (kg/s) 1.9802 1.93 1.8587 1.8191 Tốc độ cháy chất bốc x 10-6 (kg/s) 0.6202 0.7734 0.8863 1.1639 Lời cảm ơn Xin chân thành cảm ơn Hội Khoa học và Kỹ thuật Nhiệt Việt Nam đã hỗ trợ kinh phí và cán bộ nhà máy Nhiệt điện Ninh Bình đã cung cấp số liệu, tạo điều kiện trong quá trình nghiên cứu. Tài liệu tham khảo [1] Văn phòng chính phủ, Quy hoạch điện VII điều chỉnh, Hà Nội, 18.03.2016. [2] Ryoichi Kurose, Numerical Simulations of Pulverized Coal Combustion, KONA (Review) in press [3] Efim Korytnyi, Roman Saveliev, Miron Perelman, Boris Chudnovsky, Ezra Bar-Ziv, Computational fluid dynamic simulation of coal-fired utility boilers: An engineering tool, Fuel 88 (2009) 9-18. [4] T. Asotani, T. Yamashita, H. Tominaga, Y. Uesugi, Y. Itaya, S.Mori, Prediction of ignition behavior in a tangentially fired pulverized coal boiler using CFD, Fuel 87 (2008) 482-490 [5] Choeng Ryul Choi, Chang Nyung Kim, Numerical investigation on the flow, combustion and NOx emission characteristics in 500 MWe tangentially fuel pulverized coal boiler, Fuel 88 (2009) 1720-1731 [6] Cristiano V. da Silva, Maria Luiza S. Indrusiak, Arthur B. Beskow, CFD Analysis of the Pulverized Coal Combustion Processes in a 160 MWe Tangentially-Fired-Boiler of a Thermal Power Plant, J. of the Braz. Soc. of Mech. Sci. & Eng. Vol XXXII, No.4, 2010 [7] M. Xu, J.L.T. Azevedo, M.G. Carvalho, Modelling of the combustion process and NOx emission in a utility boiler, Fuel 79 (2000) 1611-1619 [8] B.R. Stanmore, S.P. Visona, Prediction of NO emissions from a number of coal-fired power station boiler, Fuel Processing Technology 64 (2000) 25-46 [9] James E. MACPHEE, Mathieu SELLIER, Mark JERMY and Edilberto TADULAN, CFD Modelling of Pulverized coal Combustion in a rotary lime kiln, Seventh International Conference on CFD in the Minerals and Process Industries, 2009 [10] Y.S. Shen, B.Y. Guo, P.Zulli, D. Maldonado, A.B. Yu, A three-dimentional CFD model for coal blends combustion: Model formation and validation, Fifth International Conference on CFD in the Process Industries, 2006 [11] R.I. Backreedy, J.M. Jones, L.Ma, M. Pourkashanian, A. Williams, A. Arenillas, B. Arias, F. Rubiera, Prediction of unburned carbon and NOx in a tangentially fired power station using single coals and blends, Fuel 84 (2005) 2196-2203
File đính kèm:
nghien_cuu_qua_trinh_chay_bot_than_va_nang_cao_hieu_qua_dot.pdf