Conceptual design of a small-pressurized water reactor using the AP1000 fuel assembly design
This paper presents the conceptual design of a 300 MWt small modular reactor (SMR)
using fuel assemblies of the AP1000 reactor. Numerical calculations have been performed to evaluate
a proper active core size and core loading pattern using the SRAC code system and the JENDL-4.0
data library. The analysis showed that Doppler, moderator temperature, void, and power reactivity
coefficients are all negative over the core lifetime. Semi-analytical thermal hydraulics analysis reveals
acceptable radial and axial fuel element temperature profiles with significant safety margin of fuel and
clad surface temperature. The minimum departure from nucleate boiling ratio (MDNBR) is also
calculated. The results indicate that a cycle length of 2.22 years is achievable while satisfying the
operation and safety-related design criteria with sufficient margins.
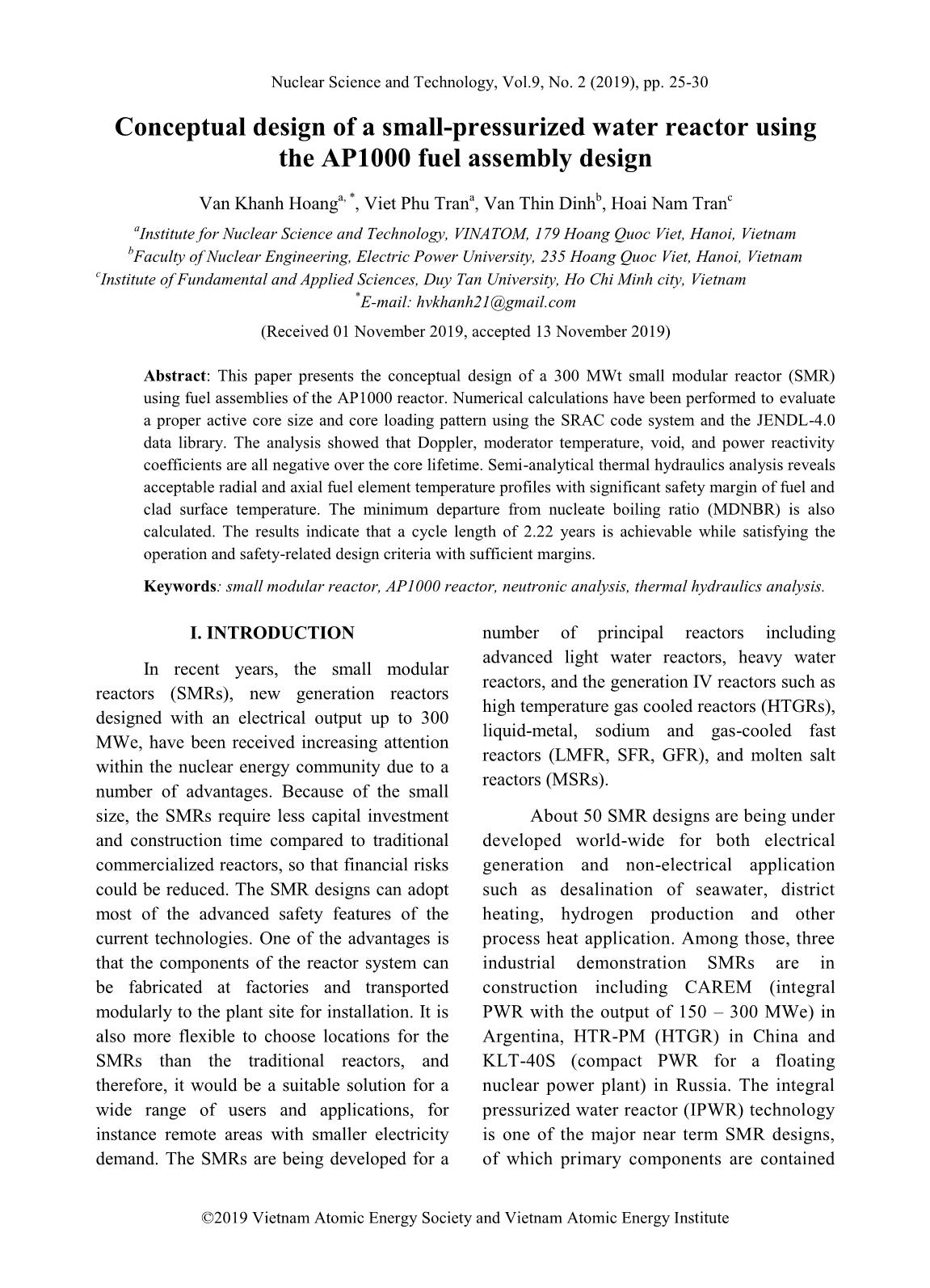
Trang 1
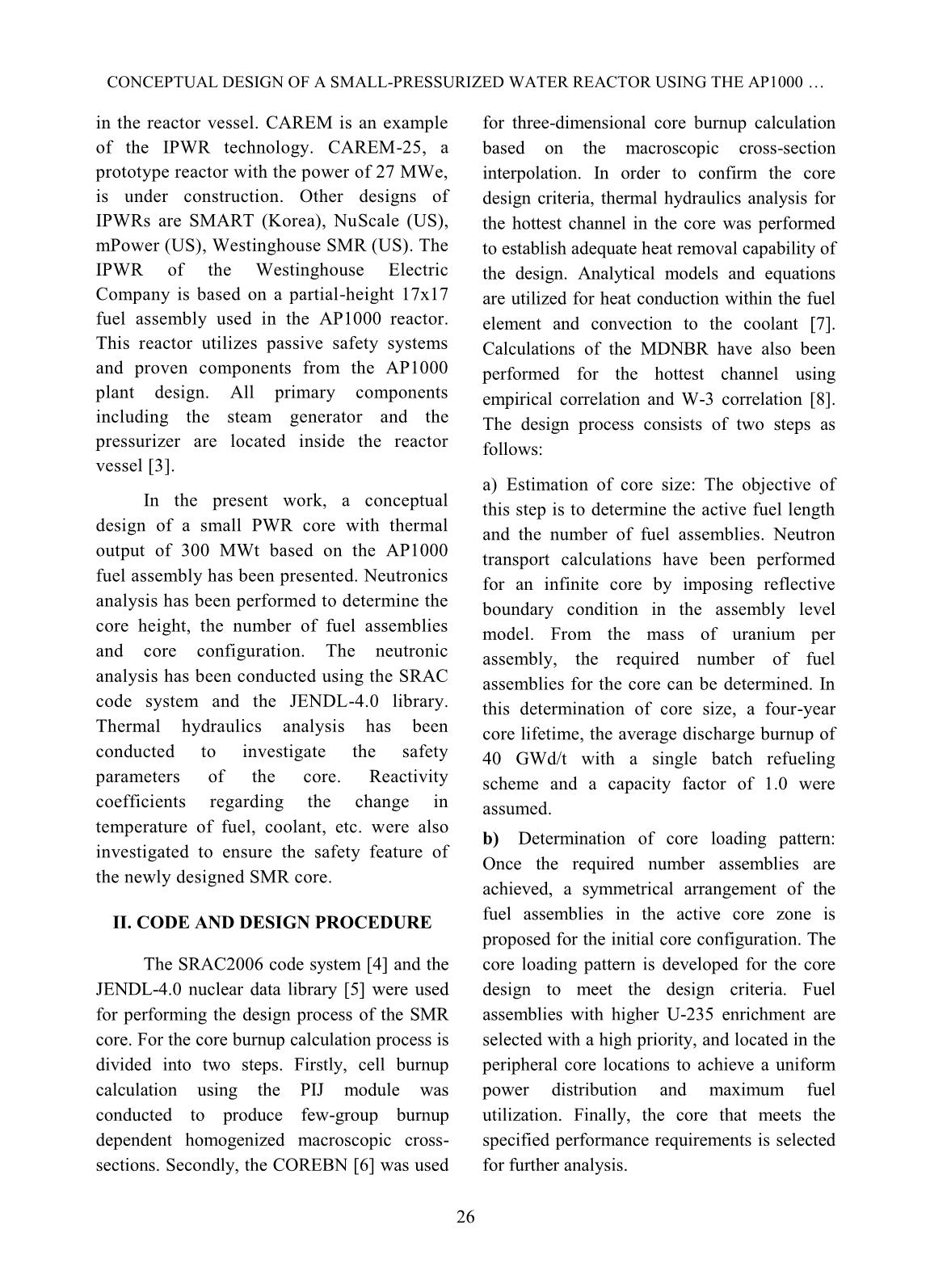
Trang 2
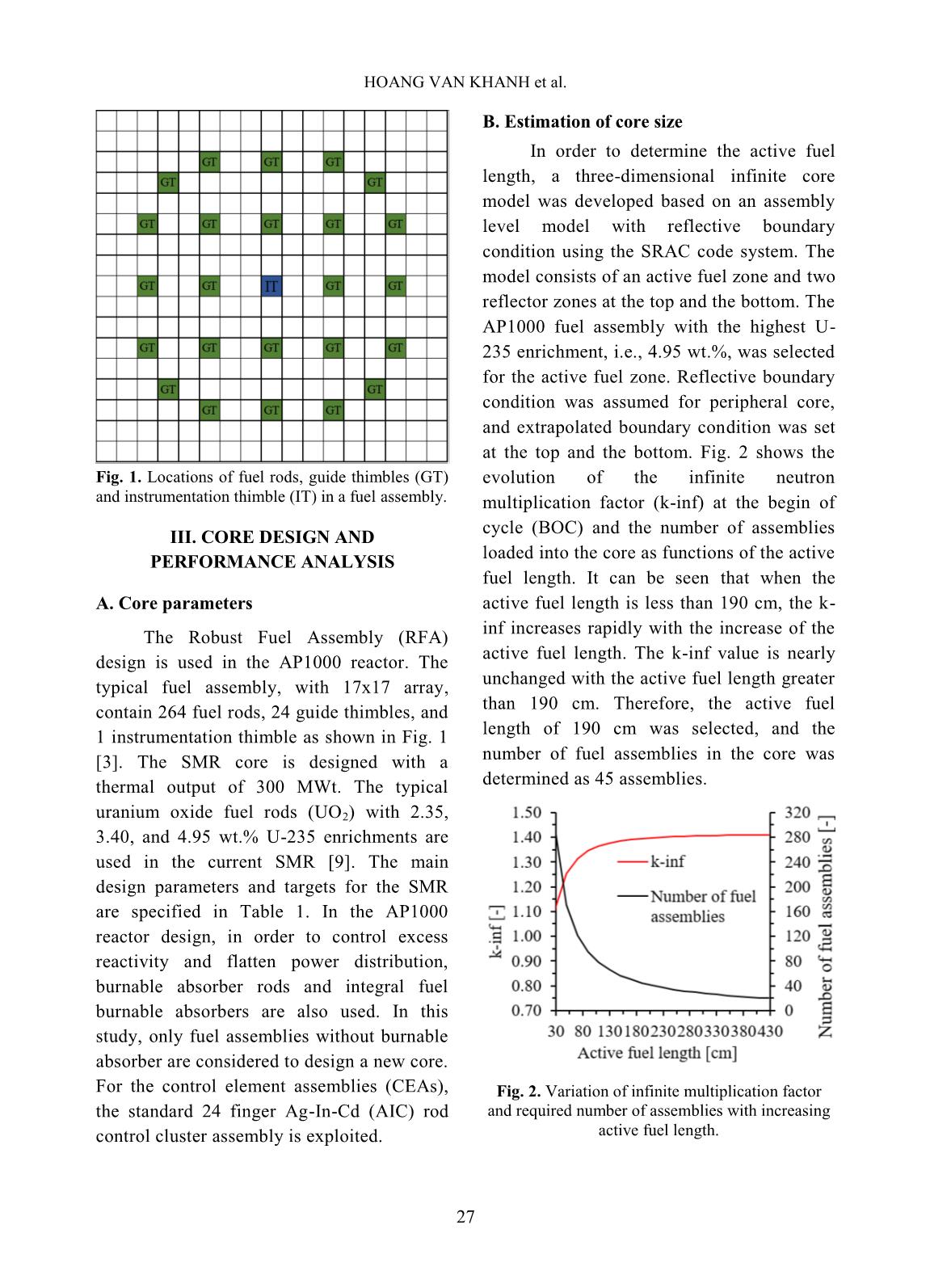
Trang 3
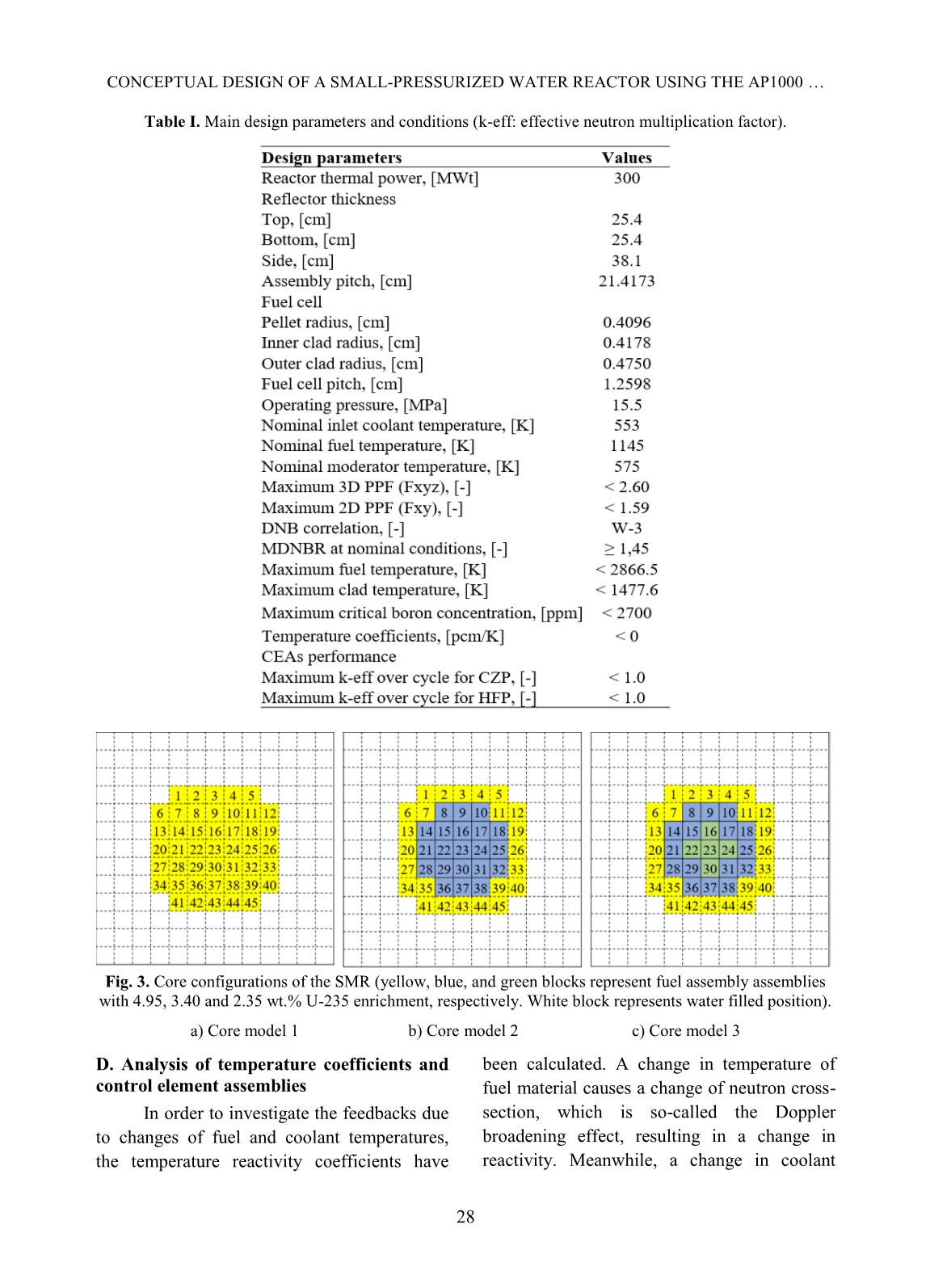
Trang 4

Trang 5
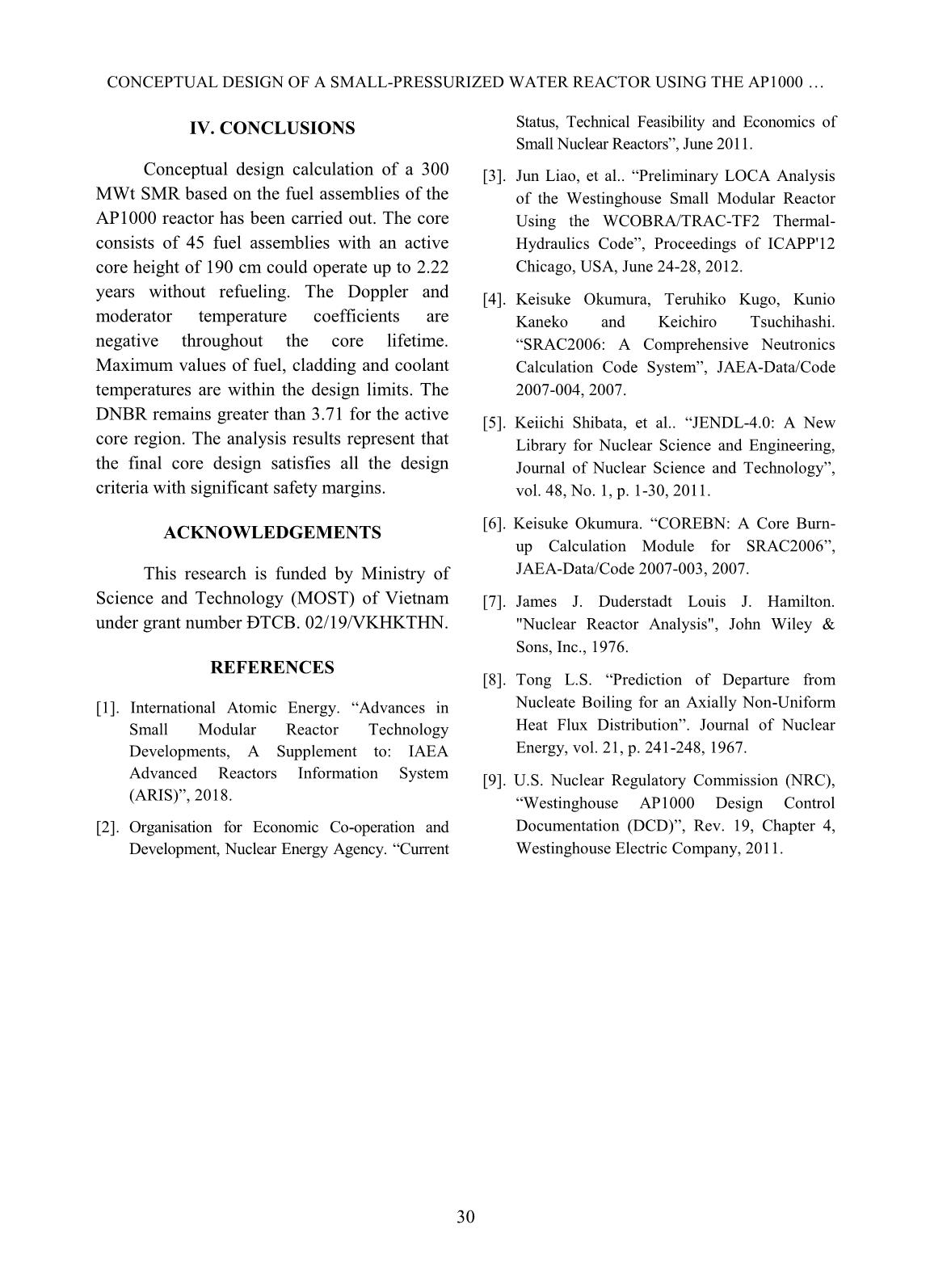
Trang 6
Tóm tắt nội dung tài liệu: Conceptual design of a small-pressurized water reactor using the AP1000 fuel assembly design
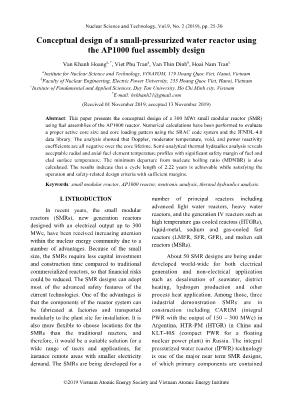
Nuclear Science and Technology, Vol.9, No. 2 (2019), pp. 25-30 ©2019 Vietnam Atomic Energy Society and Vietnam Atomic Energy Institute Conceptual design of a small-pressurized water reactor using the AP1000 fuel assembly design Van Khanh Hoang a, * , Viet Phu Tran a , Van Thin Dinh b , Hoai Nam Tran c a Institute for Nuclear Science and Technology, VINATOM, 179 Hoang Quoc Viet, Hanoi, Vietnam b Faculty of Nuclear Engineering, Electric Power University, 235 Hoang Quoc Viet, Hanoi, Vietnam c Institute of Fundamental and Applied Sciences, Duy Tan University, Ho Chi Minh city, Vietnam * E-mail: hvkhanh21@gmail.com (Received 01 November 2019, accepted 13 November 2019) Abstract: This paper presents the conceptual design of a 300 MWt small modular reactor (SMR) using fuel assemblies of the AP1000 reactor. Numerical calculations have been performed to evaluate a proper active core size and core loading pattern using the SRAC code system and the JENDL-4.0 data library. The analysis showed that Doppler, moderator temperature, void, and power reactivity coefficients are all negative over the core lifetime. Semi-analytical thermal hydraulics analysis reveals acceptable radial and axial fuel element temperature profiles with significant safety margin of fuel and clad surface temperature. The minimum departure from nucleate boiling ratio (MDNBR) is also calculated. The results indicate that a cycle length of 2.22 years is achievable while satisfying the operation and safety-related design criteria with sufficient margins. Keywords: small modular reactor, AP1000 reactor, neutronic analysis, thermal hydraulics analysis. I. INTRODUCTION In recent years, the small modular reactors (SMRs), new generation reactors designed with an electrical output up to 300 MWe, have been received increasing attention within the nuclear energy community due to a number of advantages. Because of the small size, the SMRs require less capital investment and construction time compared to traditional commercialized reactors, so that financial risks could be reduced. The SMR designs can adopt most of the advanced safety features of the current technologies. One of the advantages is that the components of the reactor system can be fabricated at factories and transported modularly to the plant site for installation. It is also more flexible to choose locations for the SMRs than the traditional reactors, and therefore, it would be a suitable solution for a wide range of users and applications, for instance remote areas with smaller electricity demand. The SMRs are being developed for a number of principal reactors including advanced light water reactors, heavy water reactors, and the generation IV reactors such as high temperature gas cooled reactors (HTGRs), liquid-metal, sodium and gas-cooled fast reactors (LMFR, SFR, GFR), and molten salt reactors (MSRs). About 50 SMR designs are being under developed world-wide for both electrical generation and non-electrical application such as desalination of seawater, district heating, hydrogen production and other process heat application. Among those, three industrial demonstration SMRs are in construction including CAREM (integral PWR with the output of 150 – 300 MWe) in Argentina, HTR-PM (HTGR) in China and KLT-40S (compact PWR for a floating nuclear power plant) in Russia. The integral pressurized water reactor (IPWR) technology is one of the major near term SMR designs, of which primary components are contained CONCEPTUAL DESIGN OF A SMALL-PRESSURIZED WATER REACTOR USING THE AP1000 26 in the reactor vessel. CAREM is an example of the IPWR technology. CAREM-25, a prototype reactor with the power of 27 MWe, is under construction. Other designs of IPWRs are SMART (Korea), NuScale (US), mPower (US), Westinghouse SMR (US). The IPWR of the Westinghouse Electric Company is based on a partial-height 17x17 fuel assembly used in the AP1000 reactor. This reactor utilizes passive safety systems and proven components from the AP1000 plant design. All primary components including the steam generator and the pressurizer are located inside the reactor vessel [3]. In the present work, a conceptual design of a small PWR core with thermal output of 300 MWt based on the AP1000 fuel assembly has been presented. Neutronics analysis has been performed to determine the core height, the number of fuel assemblies and core configuration. The neutronic analysis has been conducted using the SRAC code system and the JENDL-4.0 library. Thermal hydraulics analysis has been conducted to investigate the safety parameters of the core. Reactivity coefficients regarding the change in temperature of fuel, coolant, etc. were also investigated to ensure the safety feature of the newly designed SMR core. II. CODE AND DESIGN PROCEDURE The SRAC2006 code system [4] and the JENDL-4.0 nuclear data library [5] were used for performing the design process of the SMR core. For the core burnup calculation process is divided into two steps. Firstly, cell burnup calculation using the PIJ module was conducted to produce few-group burnup dependent homogenized macroscopic cross- sections. Secondly, the COREBN [6] was used for three-dimensional core burnup calculation based on the macroscopic cross-section interpolation. In order to confirm the core design criteria, thermal hydraulics analysis for the hottest channel in the core was performed to establish adequate heat removal capability of the design. Analytical models and equations are utilized for heat conduction within the fuel element and convection to the coolant [7]. Calculations of the MDNBR have also been performed for the hottest channel using empirical correlation and W-3 correlation [8]. The design process consists of two steps as follows: a) Estimation of core size: The objective of this step is to determine the active fuel length and the number of fuel assemblies. Neutron transport calculations have been performed for an infinite core by imposing reflective boundary condition in the assembly level model. From the mass of uranium per assembly, the required number of fuel assemblies for the core can be determined. In this determination of core size, a four-year core lifetime, the average discharge burnup of 40 GWd/t with a single batch refueling scheme and a capacity factor of 1.0 were assumed. b) Determination of core loading pattern: Once the required number assemblies are achieved, a symmetrical arrangement of the fuel assemblies in the active core zone is proposed for the initial core configuration. The core loading pattern is developed for the core design to meet the design criteria. Fuel assemblies with higher U-235 enrichment are selected with a high priority, and located in the peripheral core locations to achieve a uniform power distribution and maximum fuel utilization. Finally, the core that meets the specified performance requirements is selected for further analysis. HOANG VAN KHANH et al. 27 Fig. 1. Locations of fuel rods, guide thimbles (GT) and instrumentation thimble (IT) in a fuel assembly. III. CORE DESIGN AND PERFORMANCE ANALYSIS A. Core parameters The Robust Fuel Assembly (RFA) design is used in the AP1000 reactor. The typical fuel assembly, with 17x17 array, contain 264 fuel rods, 24 guide thimbles, and 1 instrumentation thimble as shown in Fig. 1 [3]. The SMR core is designed with a thermal output of 300 MWt. The typical uranium oxide fuel rods (UO2) with 2.35, 3.40, and 4.95 wt.% U-235 enrichments are used in the current SMR [9]. The main design parameters and targets for the SMR are specified in Table 1. In the AP1000 reactor design, in order to control excess reactivity and flatten power distribution, burnable absorber rods and integral fuel burnable absorbers are also used. In this study, only fuel assemblies without burnable absorber are considered to design a new core. For the control element assemblies (CEAs), the standard 24 finger Ag-In-Cd (AIC) rod control cluster assembly is exploited. B. Estimation of core size In order to determine the active fuel length, a three-dimensional infinite core model was developed based on an assembly level model with reflective boundary condition using the SRAC code system. The model consists of an active fuel zone and two reflector zones at the top and the bottom. The AP1000 fuel assembly with the highest U- 235 enrichment, i.e., 4.95 wt.%, was selected for the active fuel zone. Reflective boundary condition was assumed for peripheral core, and extrapolated boundary condition was set at the top and the bottom. Fig. 2 shows the evolution of the infinite neutron multiplication factor (k-inf) at the begin of cycle (BOC) and the number of assemblies loaded into the core as functions of the active fuel length. It can be seen that when the active fuel length is less than 190 cm, the k- inf increases rapidly with the increase of the active fuel length. The k-inf value is nearly unchanged with the active fuel length greater than 190 cm. Therefore, the active fuel length of 190 cm was selected, and the number of fuel assemblies in the core was determined as 45 assemblies. Fig. 2. Variation of infinite multiplication factor and required number of assemblies with increasing active fuel length. CONCEPTUAL DESIGN OF A SMALL-PRESSURIZED WATER REACTOR USING THE AP1000 28 Table I. Main design parameters and conditions (k-eff: effective neutron multiplication factor). Fig. 3. Core configurations of the SMR (yellow, blue, and green blocks represent fuel assembly assemblies with 4.95, 3.40 and 2.35 wt.% U-235 enrichment, respectively. White block represents water filled position). a) Core model 1 b) Core model 2 c) Core model 3 D. Analysis of temperature coefficients and control element assemblies In order to investigate the feedbacks due to changes of fuel and coolant temperatures, the temperature reactivity coefficients have been calculated. A change in temperature of fuel material causes a change of neutron cross- section, which is so-called the Doppler broadening effect, resulting in a change in reactivity. Meanwhile, a change in coolant HOANG VAN KHANH et al. 29 temperature results in the change of moderator density, which leads to a change in reactivity of the core. For safe operation, negative values of the temperature reactivity coefficients are desirable. In the numerical analysis, the temperature of fuel and/or coolant was increased by 50K. For the isothermal coefficient, both temperature of fuel and coolant were increased by 50K. The shutdown margins of the control rod assemblies were analyzed to ensure that the core has sufficient control rod worth. Fig. 4 shows the map of the control element assemblies. The CEAs are composed of shutdown banks (S) and regulating banks (R) located in the outer core and the inner core, respectively. The reactivity coefficients and CEAs performance of the selected core model (Core 3) at cold zero power (CZP) and hot full power (HFP) states are presented in Table 3. It can see that all coefficients are negative during the core lifetime. The CEAs of the core have sufficient shutdown margin. Table II. Summary of analysis results of the different core configurations. Fig. 4. Locations of the CEAs in the active core zone. Table III. Temperature coefficients and CEAs performance of the final core design. CONCEPTUAL DESIGN OF A SMALL-PRESSURIZED WATER REACTOR USING THE AP1000 30 IV. CONCLUSIONS Conceptual design calculation of a 300 MWt SMR based on the fuel assemblies of the AP1000 reactor has been carried out. The core consists of 45 fuel assemblies with an active core height of 190 cm could operate up to 2.22 years without refueling. The Doppler and moderator temperature coefficients are negative throughout the core lifetime. Maximum values of fuel, cladding and coolant temperatures are within the design limits. The DNBR remains greater than 3.71 for the active core region. The analysis results represent that the final core design satisfies all the design criteria with significant safety margins. ACKNOWLEDGEMENTS This research is funded by Ministry of Science and Technology (MOST) of Vietnam under grant number ĐTCB. 02/19/VKHKTHN. REFERENCES [1]. International Atomic Energy. “Advances in Small Modular Reactor Technology Developments, A Supplement to: IAEA Advanced Reactors Information System (ARIS)”, 2018. [2]. Organisation for Economic Co-operation and Development, Nuclear Energy Agency. “Current Status, Technical Feasibility and Economics of Small Nuclear Reactors”, June 2011. [3]. Jun Liao, et al.. “Preliminary LOCA Analysis of the Westinghouse Small Modular Reactor Using the WCOBRA/TRAC-TF2 Thermal- Hydraulics Code”, Proceedings of ICAPP'12 Chicago, USA, June 24-28, 2012. [4]. Keisuke Okumura, Teruhiko Kugo, Kunio Kaneko and Keichiro Tsuchihashi. “SRAC2006: A Comprehensive Neutronics Calculation Code System”, JAEA-Data/Code 2007-004, 2007. [5]. Keiichi Shibata, et al.. “JENDL-4.0: A New Library for Nuclear Science and Engineering, Journal of Nuclear Science and Technology”, vol. 48, No. 1, p. 1-30, 2011. [6]. Keisuke Okumura. “COREBN: A Core Burn- up Calculation Module for SRAC2006”, JAEA-Data/Code 2007-003, 2007. [7]. James J. Duderstadt Louis J. Hamilton. "Nuclear Reactor Analysis", John Wiley & Sons, Inc., 1976. [8]. Tong L.S. “Prediction of Departure from Nucleate Boiling for an Axially Non-Uniform Heat Flux Distribution”. Journal of Nuclear Energy, vol. 21, p. 241-248, 1967. [9]. U.S. Nuclear Regulatory Commission (NRC), “Westinghouse AP1000 Design Control Documentation (DCD)”, Rev. 19, Chapter 4, Westinghouse Electric Company, 2011.
File đính kèm:
conceptual_design_of_a_small_pressurized_water_reactor_using.pdf