Numerical investigation of fluid – structure interaction (FSI) on sodium leakage accident at prototype fast breeder reactor monju
This study presents a numerical investigation of fluid-structure interaction about sodium
leakage accident at prototype fast breeder reactor Monju. The dynamic forces of sodium liquid flow
acting on the thermowell are the main cause of fatigue failure, which leads to the occurrence of
thermowell cracking due to intense stresses and high fatigue-cycle. Since the location and magnitude
of these stresses are unknown, an analysis of the vibrational characteristics and stresses caused by FSI
was performed by using ANSYS to prevent similar accidents in the future. The most dangerous case
was found for FSI analysis by comparisons between the natural frequency of thermowell and vortex
shedding frequency at several operating conditions. The results showed that a stress concentration
location is similar to the location of broken thermowell, and the amplitude of stress is large enough for
fatigue damage.
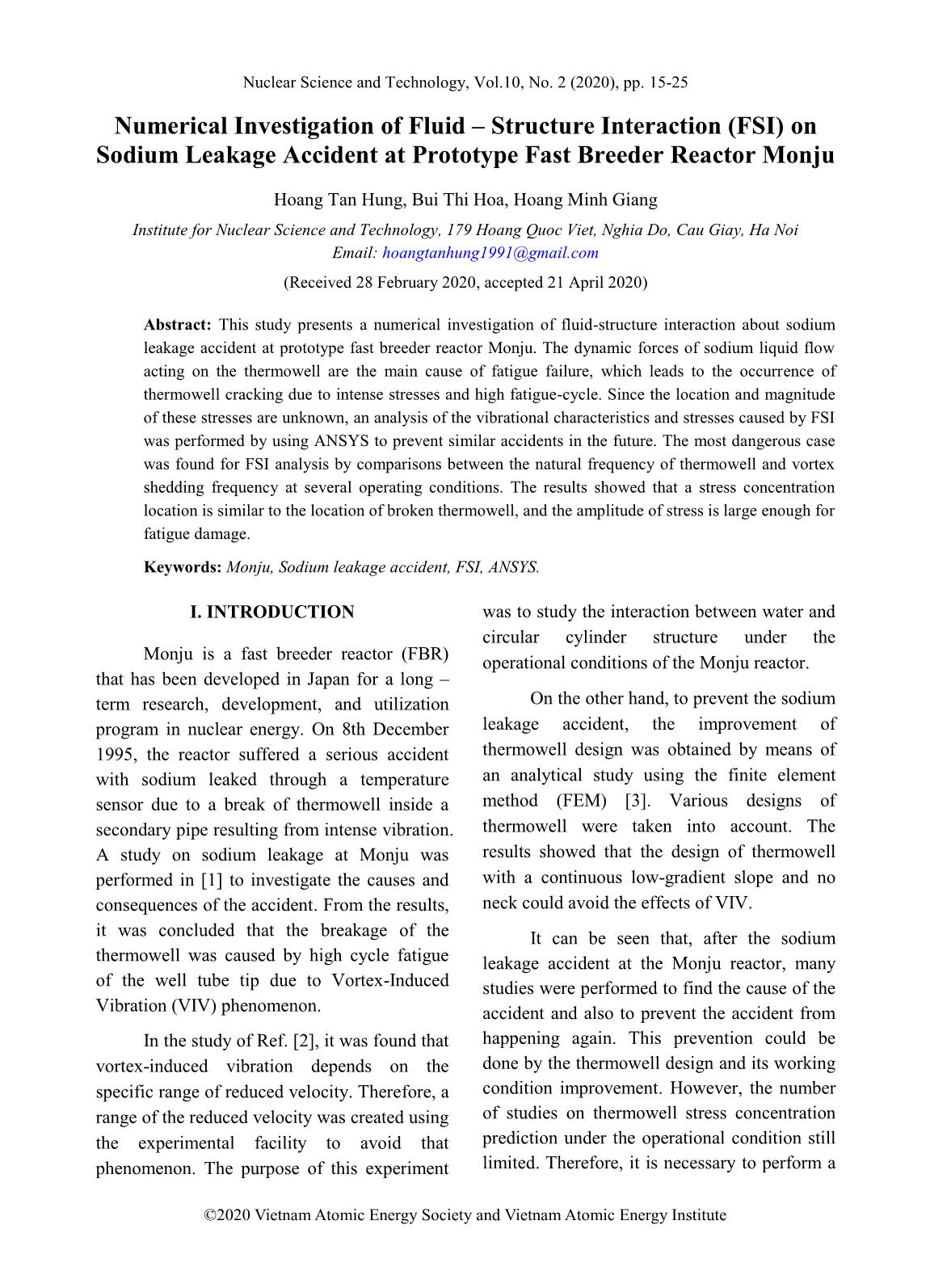
Trang 1
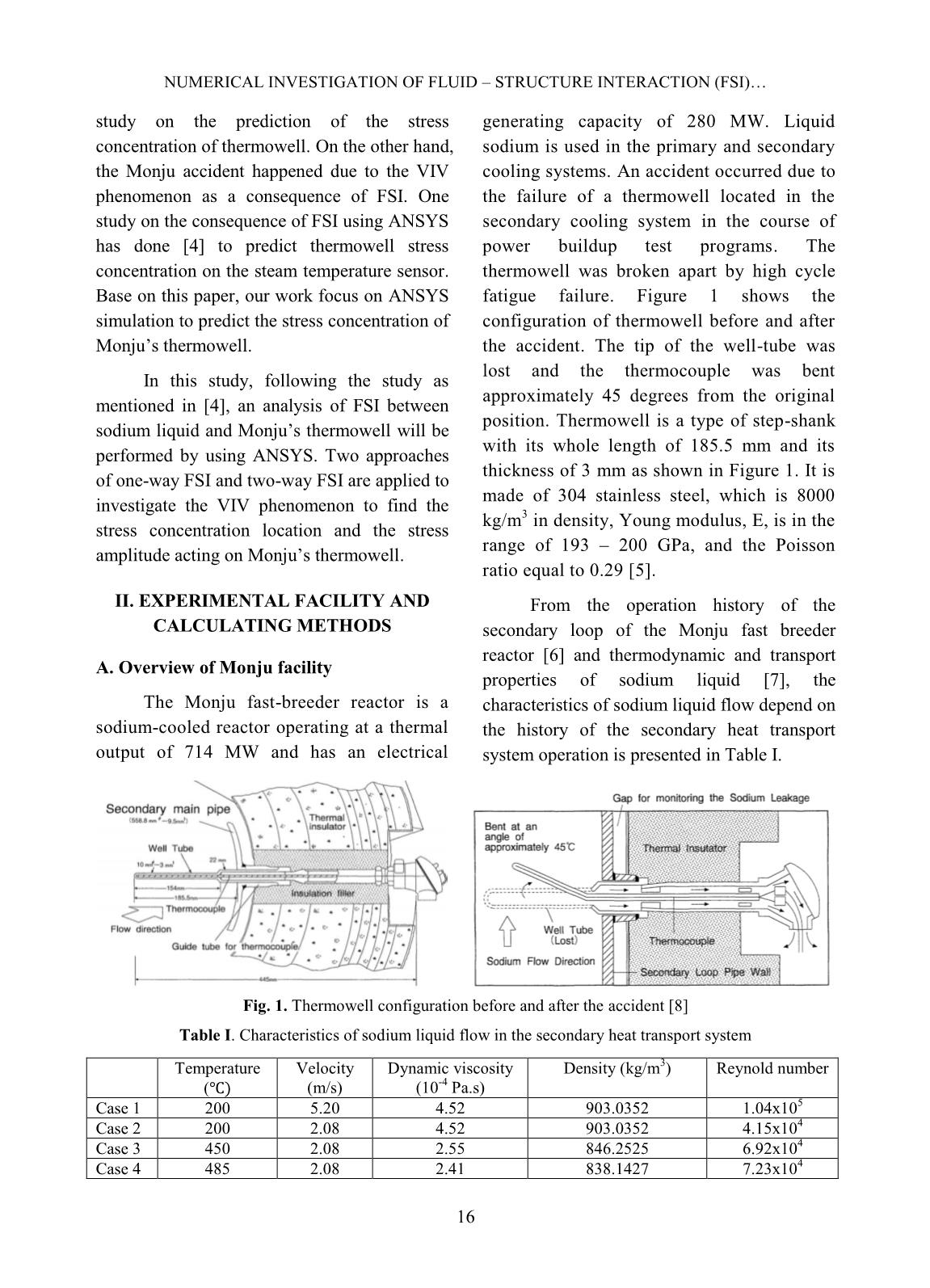
Trang 2
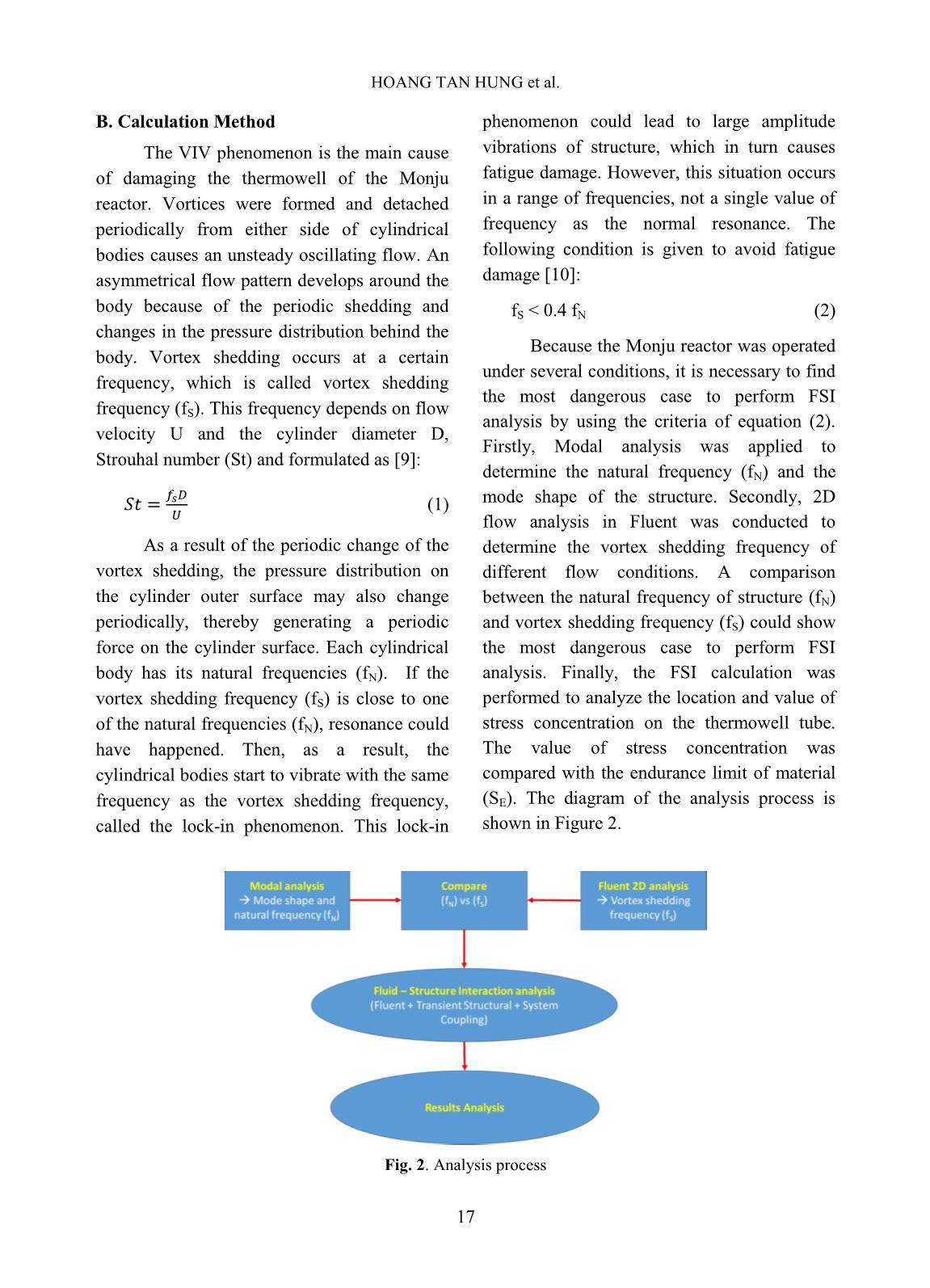
Trang 3
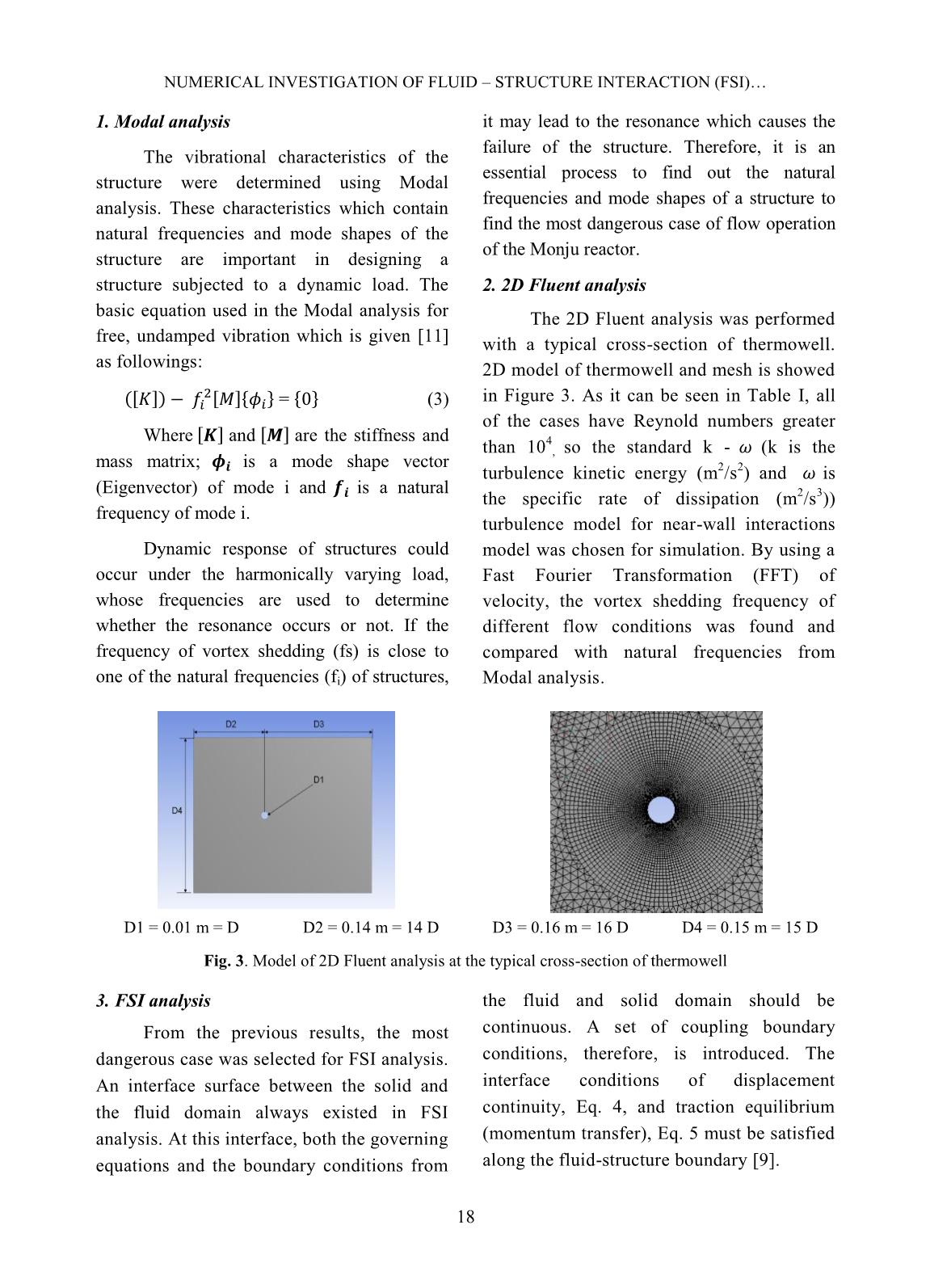
Trang 4
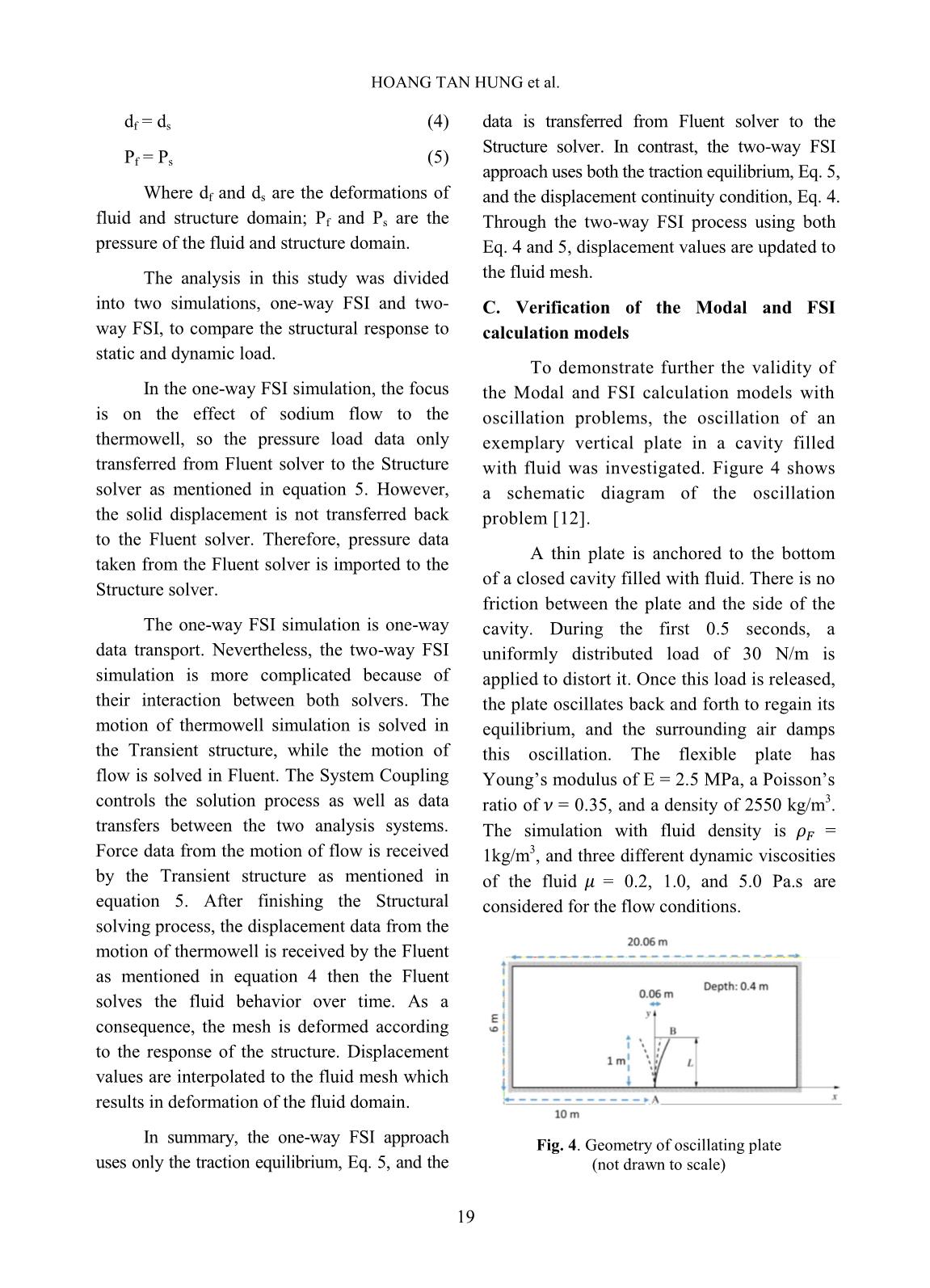
Trang 5
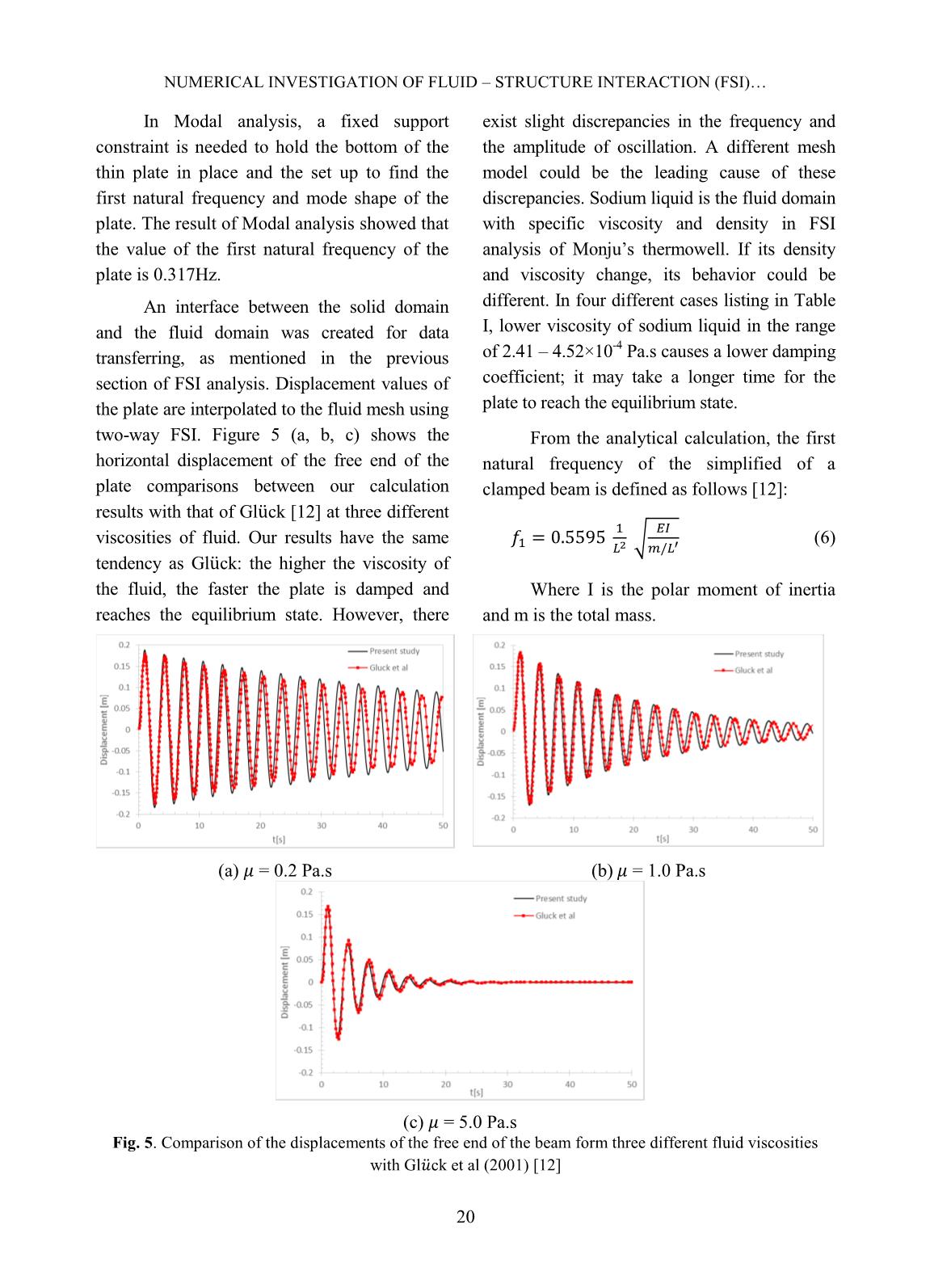
Trang 6
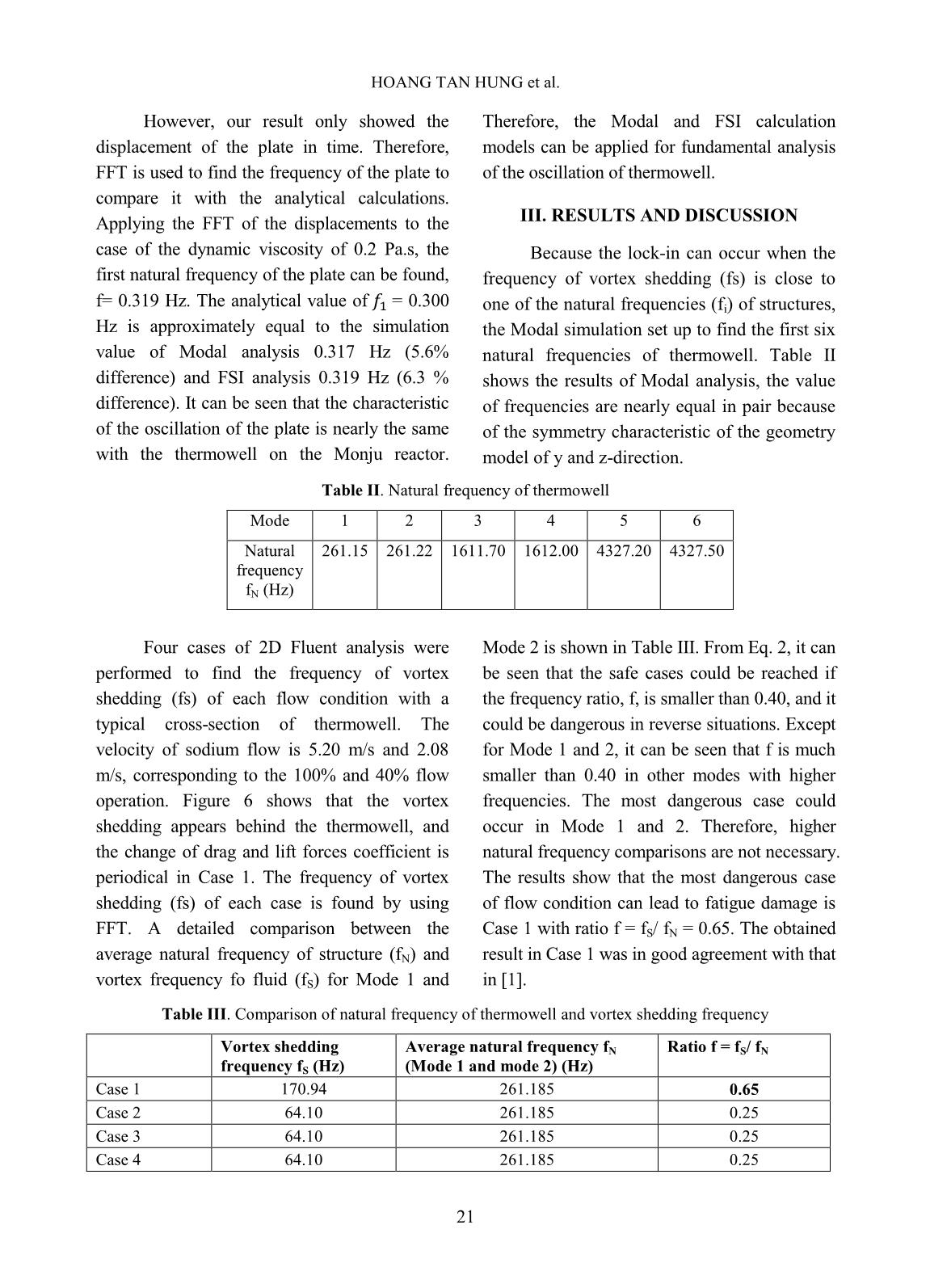
Trang 7
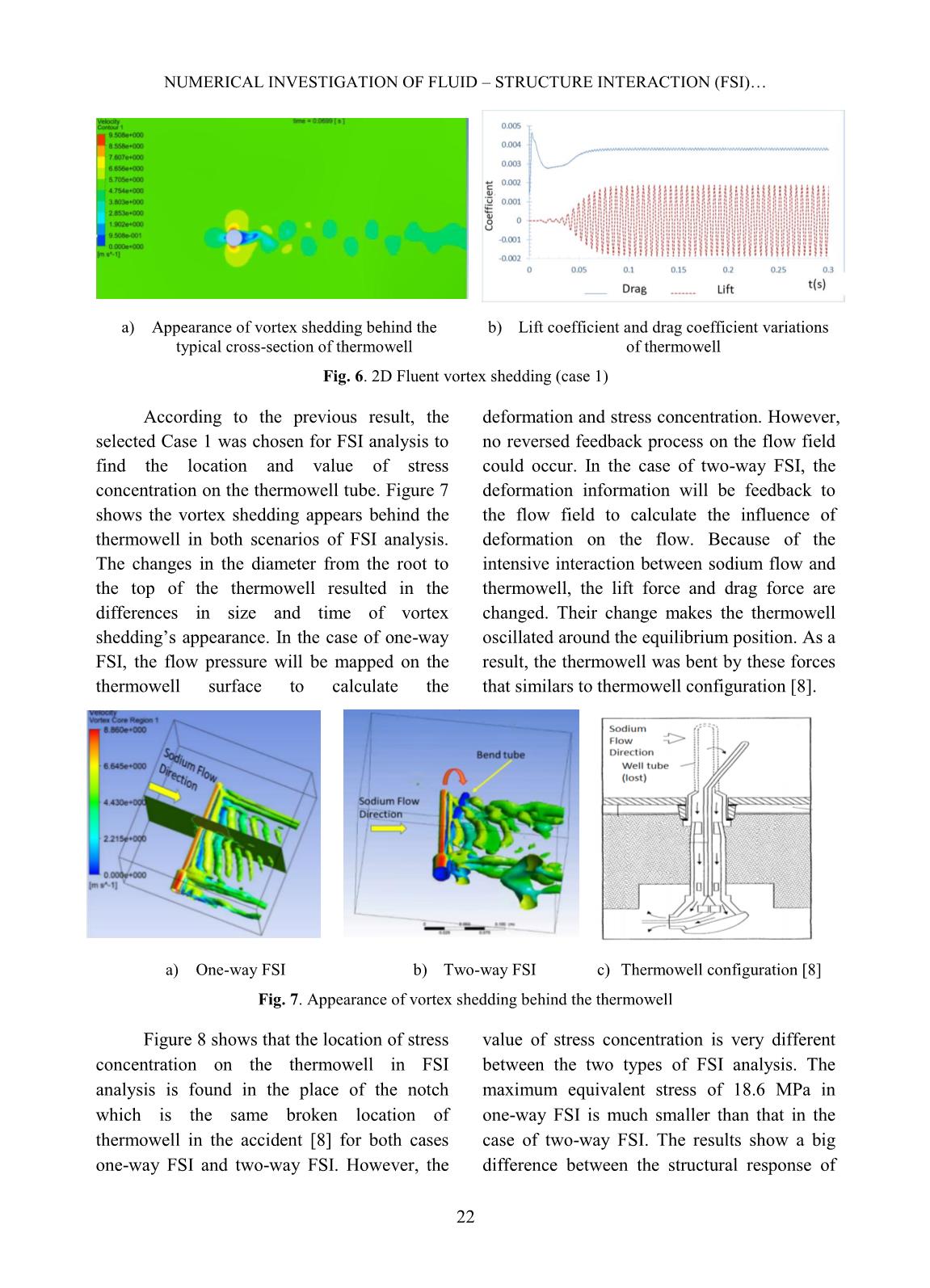
Trang 8
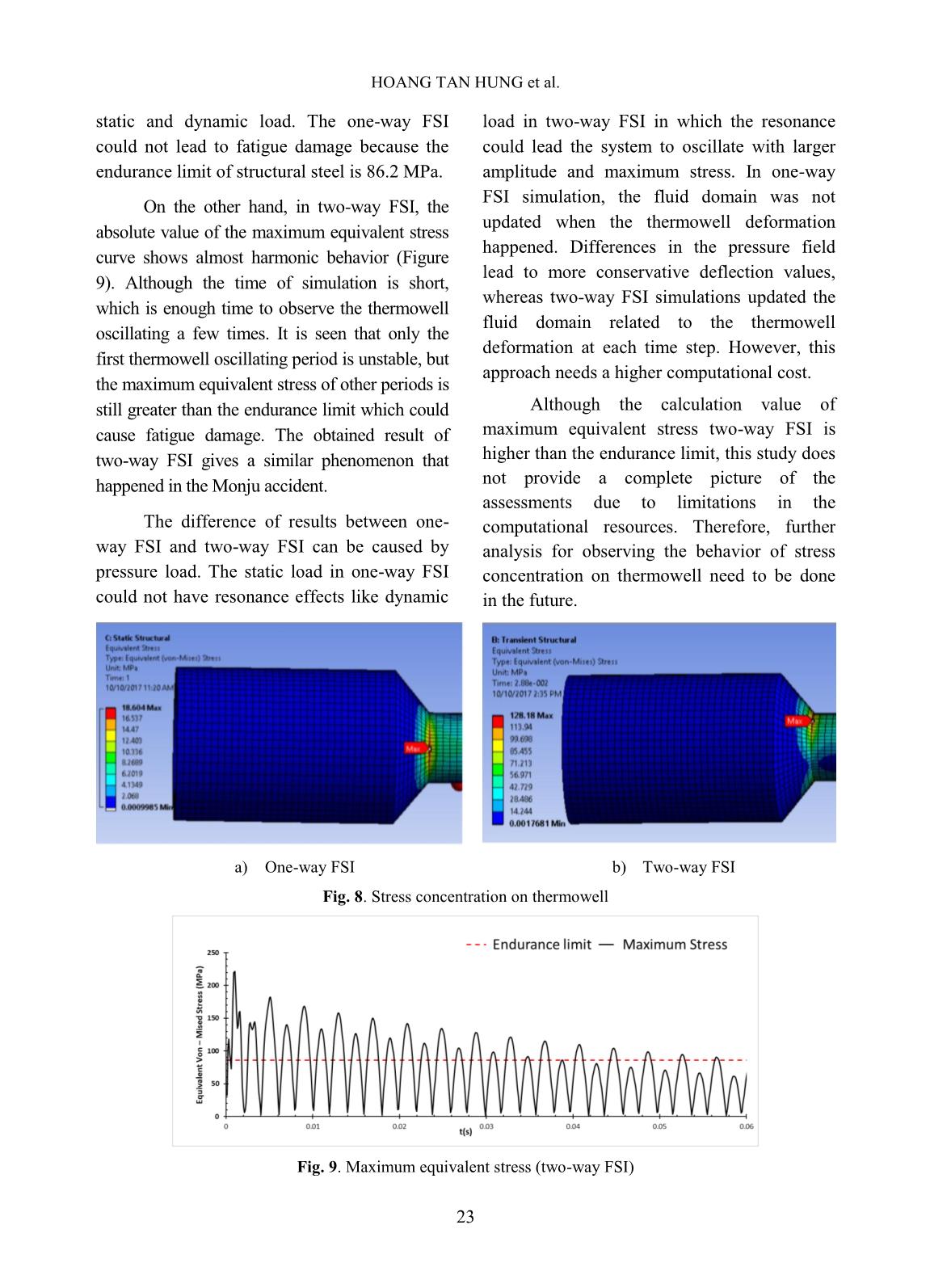
Trang 9
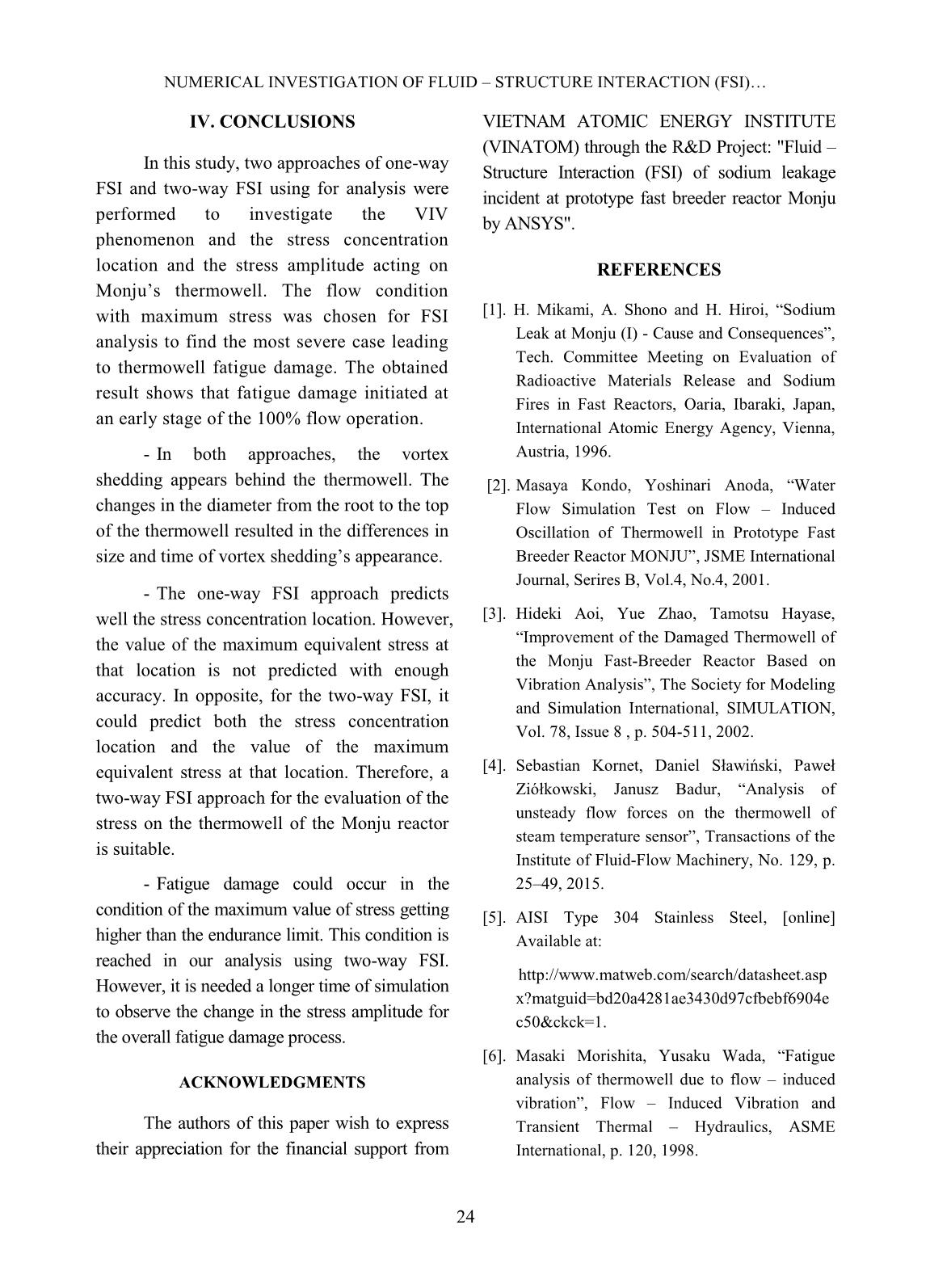
Trang 10
Tải về để xem bản đầy đủ
Tóm tắt nội dung tài liệu: Numerical investigation of fluid – structure interaction (FSI) on sodium leakage accident at prototype fast breeder reactor monju
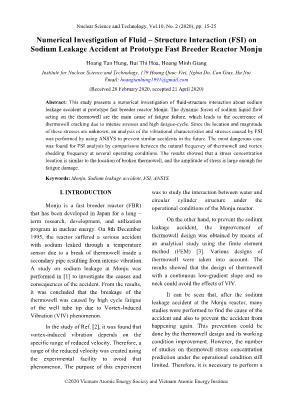
of the structure. Displacement values are interpolated to the fluid mesh which results in deformation of the fluid domain. In summary, the one-way FSI approach uses only the traction equilibrium, Eq. 5, and the data is transferred from Fluent solver to the Structure solver. In contrast, the two-way FSI approach uses both the traction equilibrium, Eq. 5, and the displacement continuity condition, Eq. 4. Through the two-way FSI process using both Eq. 4 and 5, displacement values are updated to the fluid mesh. C. Verification of the Modal and FSI calculation models To demonstrate further the validity of the Modal and FSI calculation models with oscillation problems, the oscillation of an exemplary vertical plate in a cavity filled with fluid was investigated. Figure 4 shows a schematic diagram of the oscillation problem [12]. A thin plate is anchored to the bottom of a closed cavity filled with fluid. There is no friction between the plate and the side of the cavity. During the first 0.5 seconds, a uniformly distributed load of 30 N/m is applied to distort it. Once this load is released, the plate oscillates back and forth to regain its equilibrium, and the surrounding air damps this oscillation. The flexible plate has Young’s modulus of E = 2.5 MPa, a Poisson’s ratio of = 0.35, and a density of 2550 kg/m3. The simulation with fluid density is = 1kg/m 3 , and three different dynamic viscosities of the fluid = 0.2, 1.0, and 5.0 Pa.s are considered for the flow conditions. Fig. 4. Geometry of oscillating plate (not drawn to scale) NUMERICAL INVESTIGATION OF FLUID – STRUCTURE INTERACTION (FSI) 20 In Modal analysis, a fixed support constraint is needed to hold the bottom of the thin plate in place and the set up to find the first natural frequency and mode shape of the plate. The result of Modal analysis showed that the value of the first natural frequency of the plate is 0.317Hz. An interface between the solid domain and the fluid domain was created for data transferring, as mentioned in the previous section of FSI analysis. Displacement values of the plate are interpolated to the fluid mesh using two-way FSI. Figure 5 (a, b, c) shows the horizontal displacement of the free end of the plate comparisons between our calculation results with that of Gl ̈ck [12] at three different viscosities of fluid. Our results have the same tendency as Gl ̈ck: the higher the viscosity of the fluid, the faster the plate is damped and reaches the equilibrium state. However, there exist slight discrepancies in the frequency and the amplitude of oscillation. A different mesh model could be the leading cause of these discrepancies. Sodium liquid is the fluid domain with specific viscosity and density in FSI analysis of Monju’s thermowell. If its density and viscosity change, its behavior could be different. In four different cases listing in Table I, lower viscosity of sodium liquid in the range of 2.41 – 4.52×10-4 Pa.s causes a lower damping coefficient; it may take a longer time for the plate to reach the equilibrium state. From the analytical calculation, the first natural frequency of the simplified of a clamped beam is defined as follows [12]: √ (6) Where I is the polar moment of inertia and m is the total mass. (a) = 0.2 Pa.s (b) = 1.0 Pa.s (c) = 5.0 Pa.s Fig. 5. Comparison of the displacements of the free end of the beam form three different fluid viscosities with Gl ̈ck et al (2001) [12] HOANG TAN HUNG et al. 21 However, our result only showed the displacement of the plate in time. Therefore, FFT is used to find the frequency of the plate to compare it with the analytical calculations. Applying the FFT of the displacements to the case of the dynamic viscosity of 0.2 Pa.s, the first natural frequency of the plate can be found, f= 0.319 Hz. The analytical value of = 0.300 Hz is approximately equal to the simulation value of Modal analysis 0.317 Hz (5.6% difference) and FSI analysis 0.319 Hz (6.3 % difference). It can be seen that the characteristic of the oscillation of the plate is nearly the same with the thermowell on the Monju reactor. Therefore, the Modal and FSI calculation models can be applied for fundamental analysis of the oscillation of thermowell. III. RESULTS AND DISCUSSION Because the lock-in can occur when the frequency of vortex shedding (fs) is close to one of the natural frequencies (fi) of structures, the Modal simulation set up to find the first six natural frequencies of thermowell. Table II shows the results of Modal analysis, the value of frequencies are nearly equal in pair because of the symmetry characteristic of the geometry model of y and z-direction. Table II. Natural frequency of thermowell Mode 1 2 3 4 5 6 Natural frequency fN (Hz) 261.15 261.22 1611.70 1612.00 4327.20 4327.50 Four cases of 2D Fluent analysis were performed to find the frequency of vortex shedding (fs) of each flow condition with a typical cross-section of thermowell. The velocity of sodium flow is 5.20 m/s and 2.08 m/s, corresponding to the 100% and 40% flow operation. Figure 6 shows that the vortex shedding appears behind the thermowell, and the change of drag and lift forces coefficient is periodical in Case 1. The frequency of vortex shedding (fs) of each case is found by using FFT. A detailed comparison between the average natural frequency of structure (fN) and vortex frequency fo fluid (fS) for Mode 1 and Mode 2 is shown in Table III. From Eq. 2, it can be seen that the safe cases could be reached if the frequency ratio, f, is smaller than 0.40, and it could be dangerous in reverse situations. Except for Mode 1 and 2, it can be seen that f is much smaller than 0.40 in other modes with higher frequencies. The most dangerous case could occur in Mode 1 and 2. Therefore, higher natural frequency comparisons are not necessary. The results show that the most dangerous case of flow condition can lead to fatigue damage is Case 1 with ratio f = fS/ fN = 0.65. The obtained result in Case 1 was in good agreement with that in [1]. Table III. Comparison of natural frequency of thermowell and vortex shedding frequency Vortex shedding frequency fS (Hz) Average natural frequency fN (Mode 1 and mode 2) (Hz) Ratio f = fS/ fN Case 1 170.94 261.185 0.65 Case 2 64.10 261.185 0.25 Case 3 64.10 261.185 0.25 Case 4 64.10 261.185 0.25 NUMERICAL INVESTIGATION OF FLUID – STRUCTURE INTERACTION (FSI) 22 a) Appearance of vortex shedding behind the typical cross-section of thermowell b) Lift coefficient and drag coefficient variations of thermowell Fig. 6. 2D Fluent vortex shedding (case 1) According to the previous result, the selected Case 1 was chosen for FSI analysis to find the location and value of stress concentration on the thermowell tube. Figure 7 shows the vortex shedding appears behind the thermowell in both scenarios of FSI analysis. The changes in the diameter from the root to the top of the thermowell resulted in the differences in size and time of vortex shedding’s appearance. In the case of one-way FSI, the flow pressure will be mapped on the thermowell surface to calculate the deformation and stress concentration. However, no reversed feedback process on the flow field could occur. In the case of two-way FSI, the deformation information will be feedback to the flow field to calculate the influence of deformation on the flow. Because of the intensive interaction between sodium flow and thermowell, the lift force and drag force are changed. Their change makes the thermowell oscillated around the equilibrium position. As a result, the thermowell was bent by these forces that similars to thermowell configuration [8]. a) One-way FSI b) Two-way FSI c) Thermowell configuration [8] Fig. 7. Appearance of vortex shedding behind the thermowell Figure 8 shows that the location of stress concentration on the thermowell in FSI analysis is found in the place of the notch which is the same broken location of thermowell in the accident [8] for both cases one-way FSI and two-way FSI. However, the value of stress concentration is very different between the two types of FSI analysis. The maximum equivalent stress of 18.6 MPa in one-way FSI is much smaller than that in the case of two-way FSI. The results show a big difference between the structural response of HOANG TAN HUNG et al. 23 static and dynamic load. The one-way FSI could not lead to fatigue damage because the endurance limit of structural steel is 86.2 MPa. On the other hand, in two-way FSI, the absolute value of the maximum equivalent stress curve shows almost harmonic behavior (Figure 9). Although the time of simulation is short, which is enough time to observe the thermowell oscillating a few times. It is seen that only the first thermowell oscillating period is unstable, but the maximum equivalent stress of other periods is still greater than the endurance limit which could cause fatigue damage. The obtained result of two-way FSI gives a similar phenomenon that happened in the Monju accident. The difference of results between one- way FSI and two-way FSI can be caused by pressure load. The static load in one-way FSI could not have resonance effects like dynamic load in two-way FSI in which the resonance could lead the system to oscillate with larger amplitude and maximum stress. In one-way FSI simulation, the fluid domain was not updated when the thermowell deformation happened. Differences in the pressure field lead to more conservative deflection values, whereas two-way FSI simulations updated the fluid domain related to the thermowell deformation at each time step. However, this approach needs a higher computational cost. Although the calculation value of maximum equivalent stress two-way FSI is higher than the endurance limit, this study does not provide a complete picture of the assessments due to limitations in the computational resources. Therefore, further analysis for observing the behavior of stress concentration on thermowell need to be done in the future. a) One-way FSI b) Two-way FSI Fig. 8. Stress concentration on thermowell Fig. 9. Maximum equivalent stress (two-way FSI) NUMERICAL INVESTIGATION OF FLUID – STRUCTURE INTERACTION (FSI) 24 IV. CONCLUSIONS In this study, two approaches of one-way FSI and two-way FSI using for analysis were performed to investigate the VIV phenomenon and the stress concentration location and the stress amplitude acting on Monju’s thermowell. The flow condition with maximum stress was chosen for FSI analysis to find the most severe case leading to thermowell fatigue damage. The obtained result shows that fatigue damage initiated at an early stage of the 100% flow operation. - In both approaches, the vortex shedding appears behind the thermowell. The changes in the diameter from the root to the top of the thermowell resulted in the differences in size and time of vortex shedding’s appearance. - The one-way FSI approach predicts well the stress concentration location. However, the value of the maximum equivalent stress at that location is not predicted with enough accuracy. In opposite, for the two-way FSI, it could predict both the stress concentration location and the value of the maximum equivalent stress at that location. Therefore, a two-way FSI approach for the evaluation of the stress on the thermowell of the Monju reactor is suitable. - Fatigue damage could occur in the condition of the maximum value of stress getting higher than the endurance limit. This condition is reached in our analysis using two-way FSI. However, it is needed a longer time of simulation to observe the change in the stress amplitude for the overall fatigue damage process. ACKNOWLEDGMENTS The authors of this paper wish to express their appreciation for the financial support from VIETNAM ATOMIC ENERGY INSTITUTE (VINATOM) through the R&D Project: "Fluid – Structure Interaction (FSI) of sodium leakage incident at prototype fast breeder reactor Monju by ANSYS". REFERENCES [1]. H. Mikami, A. Shono and H. Hiroi, “Sodium Leak at Monju (I) - Cause and Consequences”, Tech. Committee Meeting on Evaluation of Radioactive Materials Release and Sodium Fires in Fast Reactors, Oaria, Ibaraki, Japan, International Atomic Energy Agency, Vienna, Austria, 1996. [2]. Masaya Kondo, Yoshinari Anoda, “Water Flow Simulation Test on Flow – Induced Oscillation of Thermowell in Prototype Fast Breeder Reactor MONJU”, JSME International Journal, Serires B, Vol.4, No.4, 2001. [3]. Hideki Aoi, Yue Zhao, Tamotsu Hayase, “Improvement of the Damaged Thermowell of the Monju Fast-Breeder Reactor Based on Vibration Analysis”, The Society for Modeling and Simulation International, SIMULATION, Vol. 78, Issue 8 , p. 504-511, 2002. [4]. Sebastian Kornet, Daniel Sławiński, Paweł Ziółkowski, Janusz Badur, “Analysis of unsteady flow forces on the thermowell of steam temperature sensor”, Transactions of the Institute of Fluid-Flow Machinery, No. 129, p. 25–49, 2015. [5]. AISI Type 304 Stainless Steel, [online] Available at: x?matguid=bd20a4281ae3430d97cfbebf6904e c50&ckck=1. [6]. Masaki Morishita, Yusaku Wada, “Fatigue analysis of thermowell due to flow – induced vibration”, Flow – Induced Vibration and Transient Thermal – Hydraulics, ASME International, p. 120, 1998. HOANG TAN HUNG et al. 25 [7]. J.K.Fink, L.Leibowitz, “Thermodynamic and Transport Properties of Sodium Liquid and Vapor”, Argonne National Laboratory, pp. 86- 95 and p. 207, 1995. [8]. A.Miyakawa, H.Maeda, Y.Kami, K.Ito, “Sodium Leakage Experience at the Prototype FBR Monju”, Unusual Occurrences during LMFR Operation, IAEA-TECDOC-1180, Vienna (Austria), p. 43 -56, 1998. [9] Anton Gustafsson, “Analysis of Vortex- Induced Vibrations of Rises”, Master’s thesis in Applied Mechanics, Chalmers University Of Technology, Sweden 2012. [10]. Brauschke D., Wiklund D., Kitzman A., Zulic D., “Thermowell calculations”, Emerson Process Management, White Paper 00840– 0200–2654, Rev AC, p. 11, March 2014. [11]. ANSYS Tutorials & Training Materials, “Fluid Structure Interaction FSI with ANSYS Fluent 17.0” and “ANSYS Mechanical Linear and Nonlinear Dynamic”, ANSYS Inc, 2016. [12].Gl ̈ck, M., Breuer, M., Durst, F., Halfmann, A., Rank, E., “Computation of fluid–structure interaction on lightweight structures”, Journal of Wind Engineering and Industrial Aerodynamics 89, p. 1351–1368, 2001.
File đính kèm:
numerical_investigation_of_fluid_structure_interaction_fsi_o.pdf