Nuclear Science and Technology - Volume 10, Number 3, September 2020
Abstract: This study investigates short-range atmospheric transport of radiocesium (137Cs) after
Fukushima nuclear accident using the Weather Research and Forecasting (WRF) model and the
Lagrangian particle dispersion FLEXPART-WRF model. The most up-to-date ERA5 reanalysis
dataset is used as initial and boundary condition for the WRF model for every hour. Four experiments
were carried out to examine the sensitivity of simulation results to micro-physics parameterizations in
the WRF model with two configured domains of 5 km and 1 km horizontal resolution. Compared with
observation at Futaba and Naraha station, all experiments reproduce reasonably the variation of 137Cs
concentration from 11/03 to 26/03/2011. Statistical verification as shown in Taylor diagrams
highlights noticeable sensitivity of simulation results to different micro-physics choices. Three
configurations of the WRF model are also recommended for further study based on their better
performance among all.
Keywords: 137Cs dispersion, Fukushima Daiichi nuclear power plant, FLEXPART–WRF model,
ERA5 reanalysis data, Futaba, Naraha.
I. INTRODUCITON
The massive earthquake in Japan occurred
at 14:46 JST on 11/03/2011, with a magnitude of
9.0 [1] that caused heavy damage to infrastructure
along the east coast. It was followed by the
inundations of tsunami that caused power outages
and flooding in a large residential and industrial
area. This event had a major impact on five
nuclear power plants along Japan's northeast coast,
Higashidori, Onagawa, Fukushima Daiichi,
Fukushima Daini and Tokai Daini. Fig. 1 shows
the epicenter of the earthquake was far from
Fukushima Daiichi nuclear power plant (FDNPP)
180km in the northeast and Onagawa NPP 130km
in the east [2,3].
The FDNPP consists of six units that
were strongly impacted by the earthquake and
tsunami, leading to a serious nuclear accident,
radioactive substances were released from the
plant area and released into soil, water and air
environments (Fig. 2). The most serious is that
radioactive materials are released into the air,
they will be spreaded under different weather
conditions and can be fell in continent and sea
areas that is very far from the accident site.
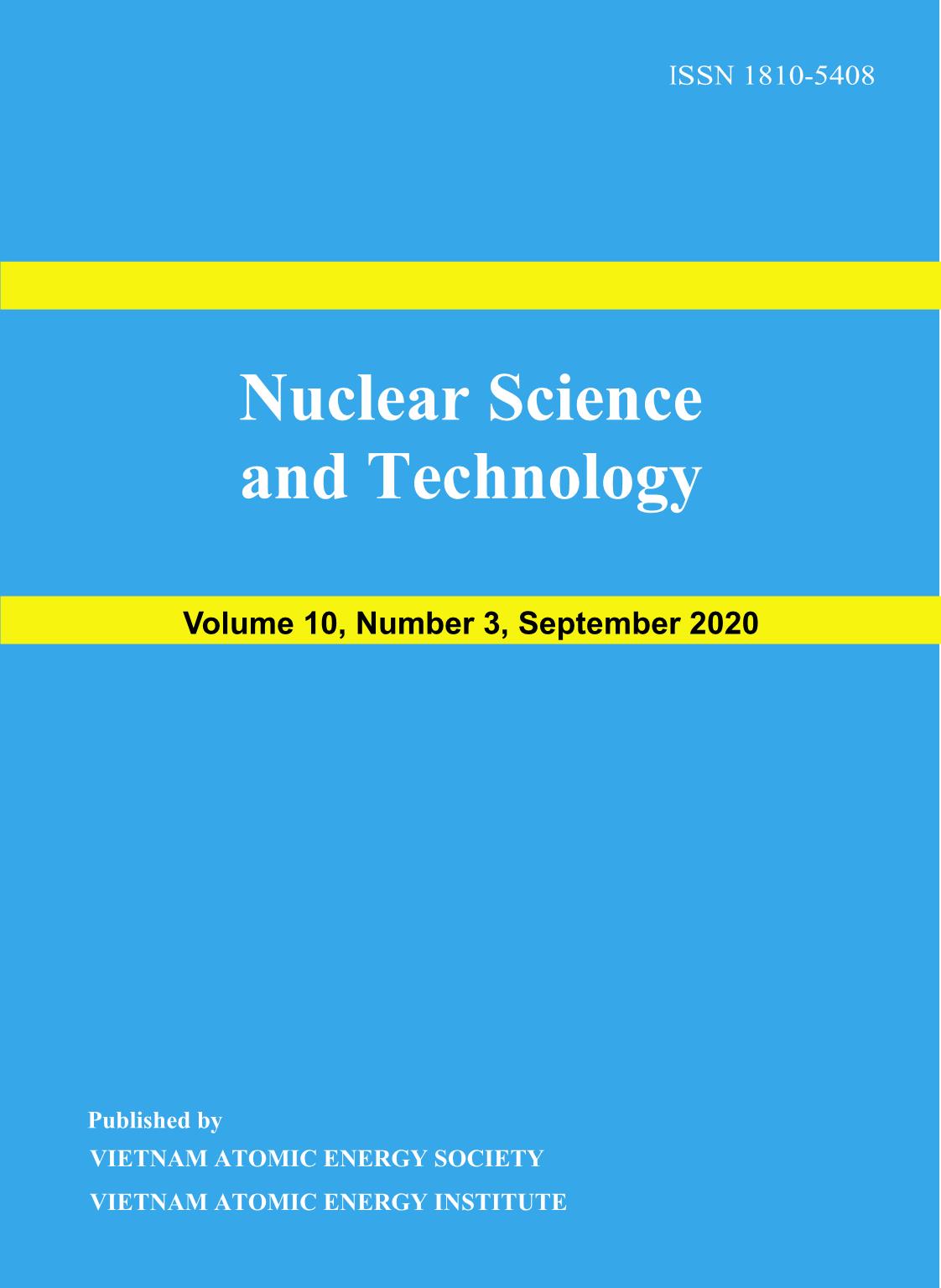
Trang 1
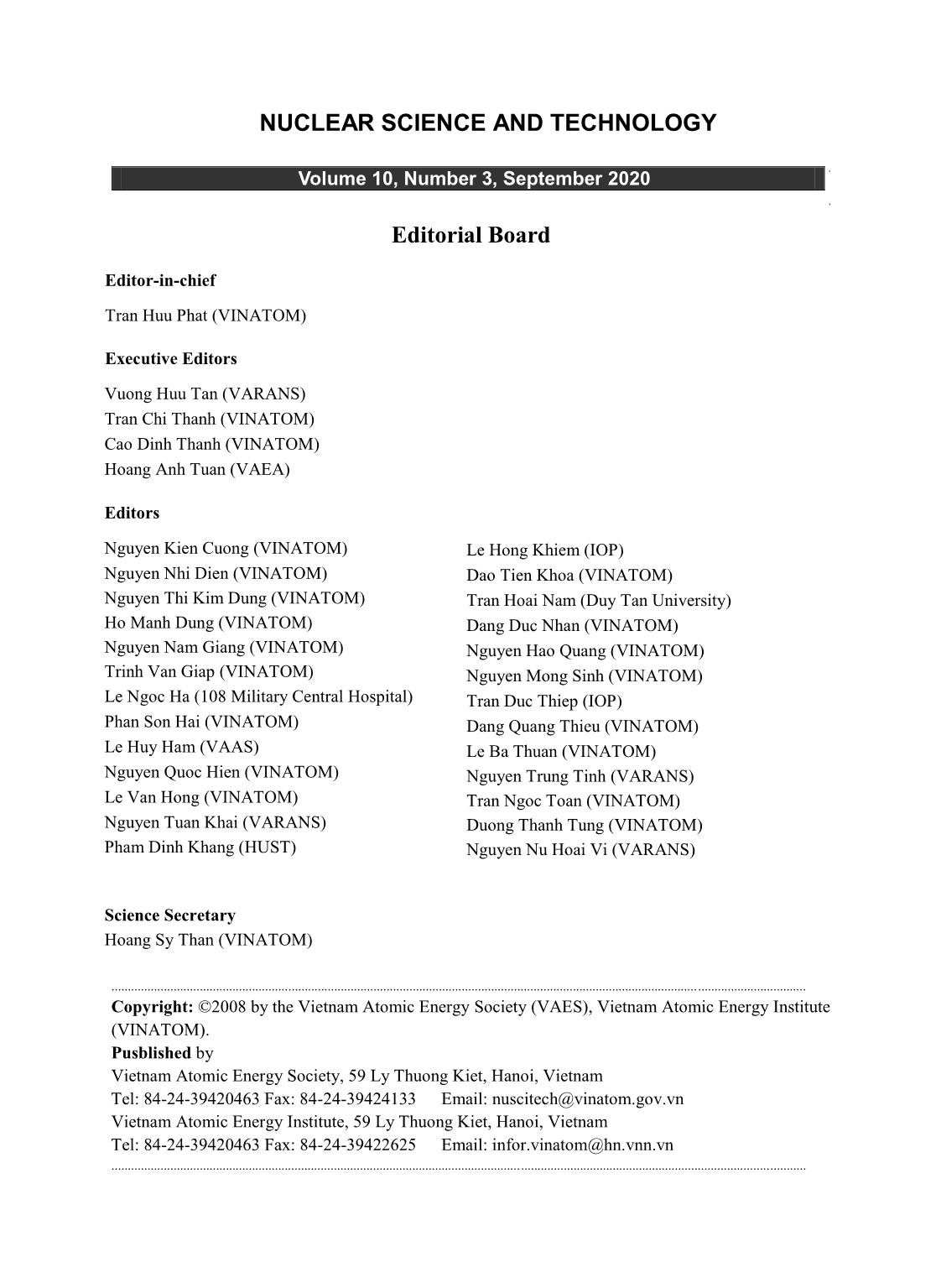
Trang 2
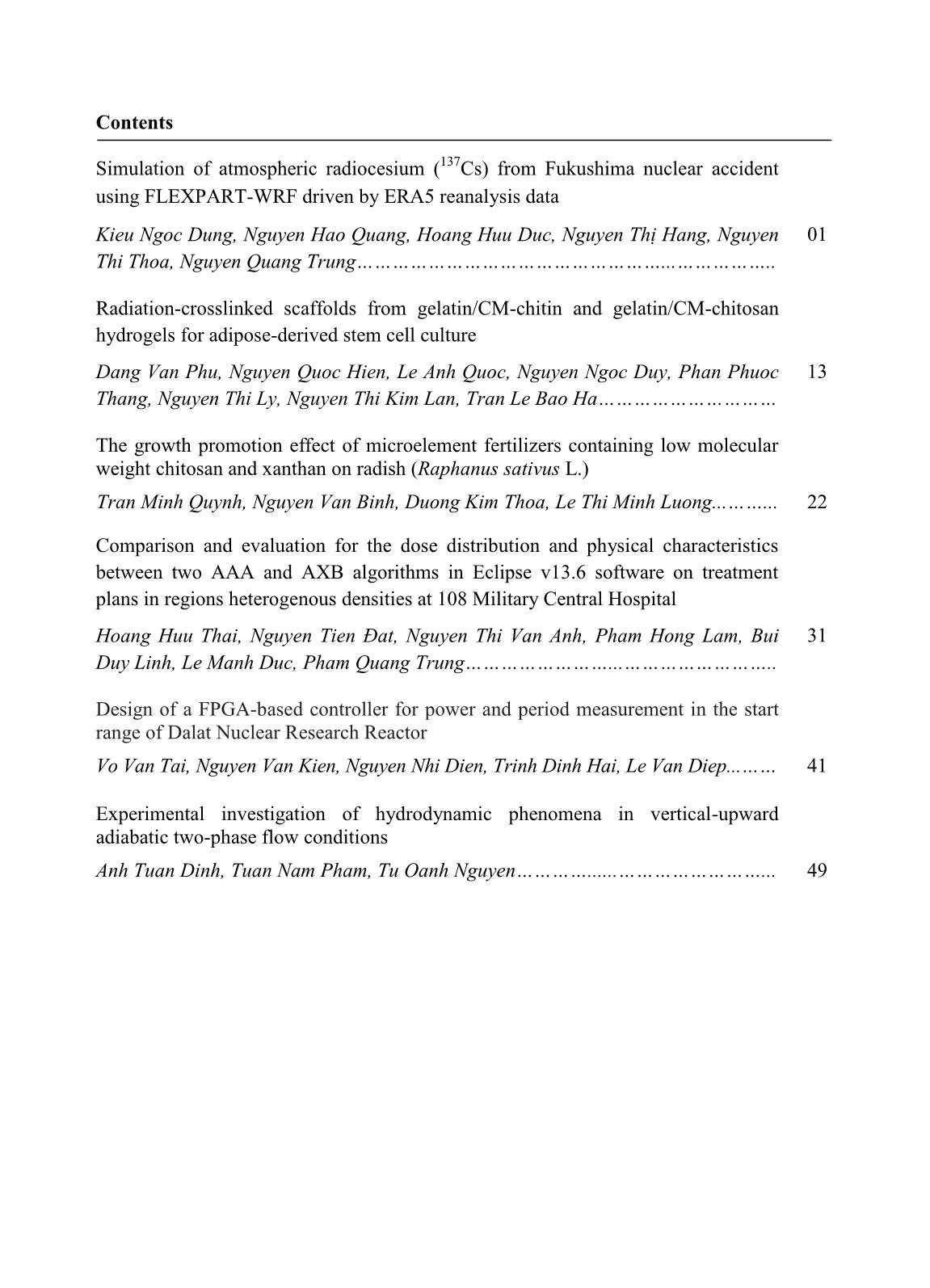
Trang 3
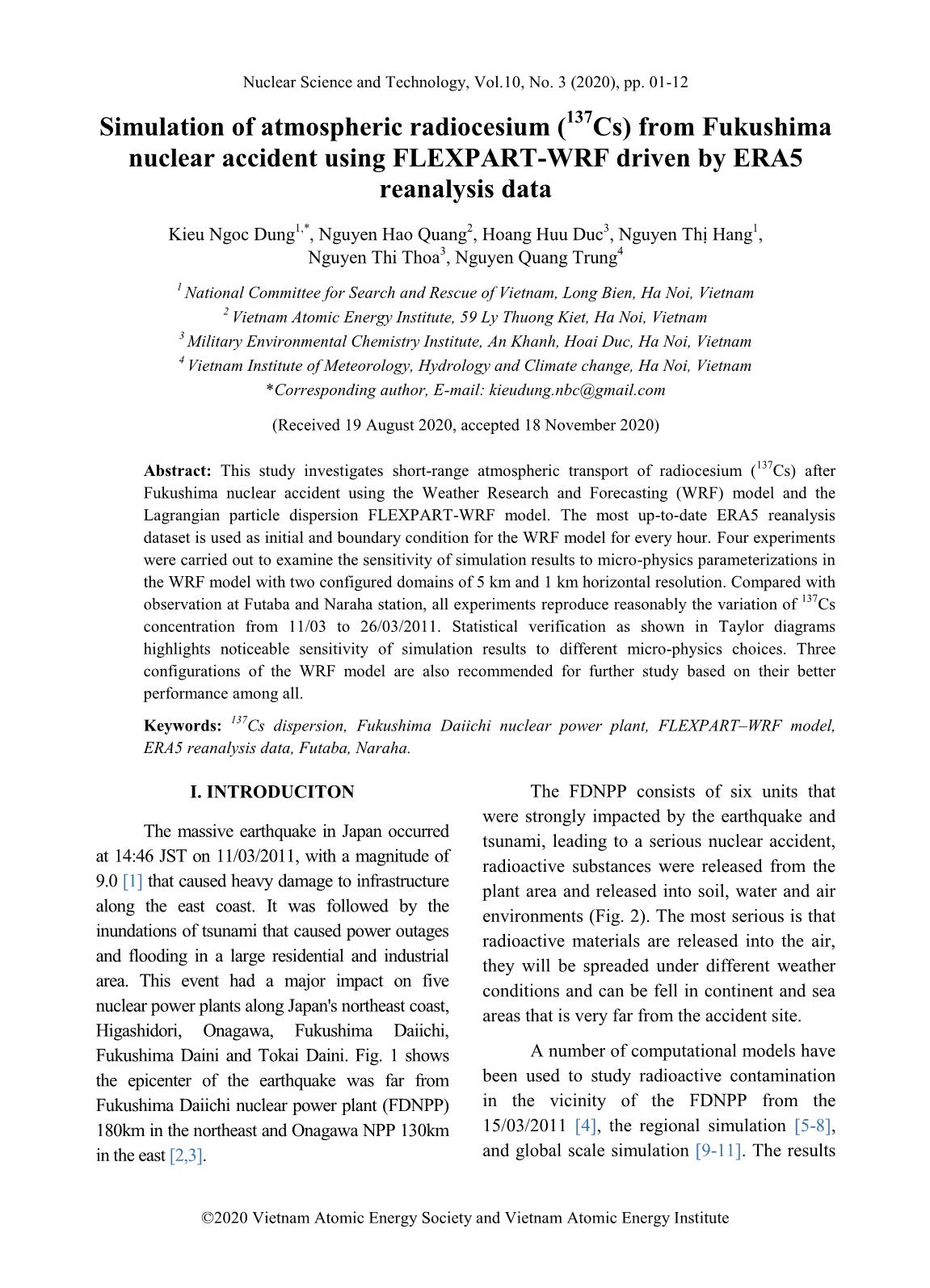
Trang 4
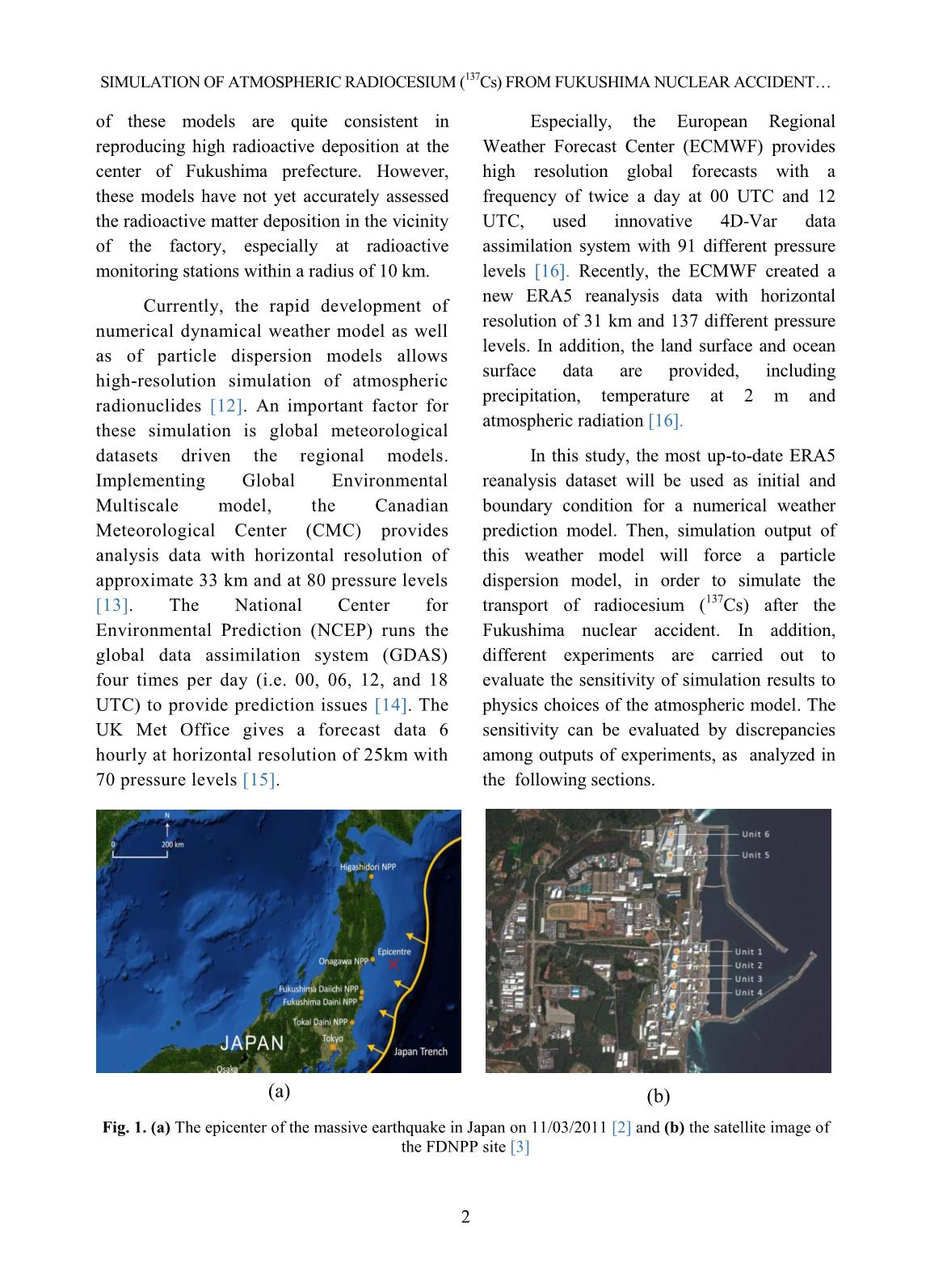
Trang 5
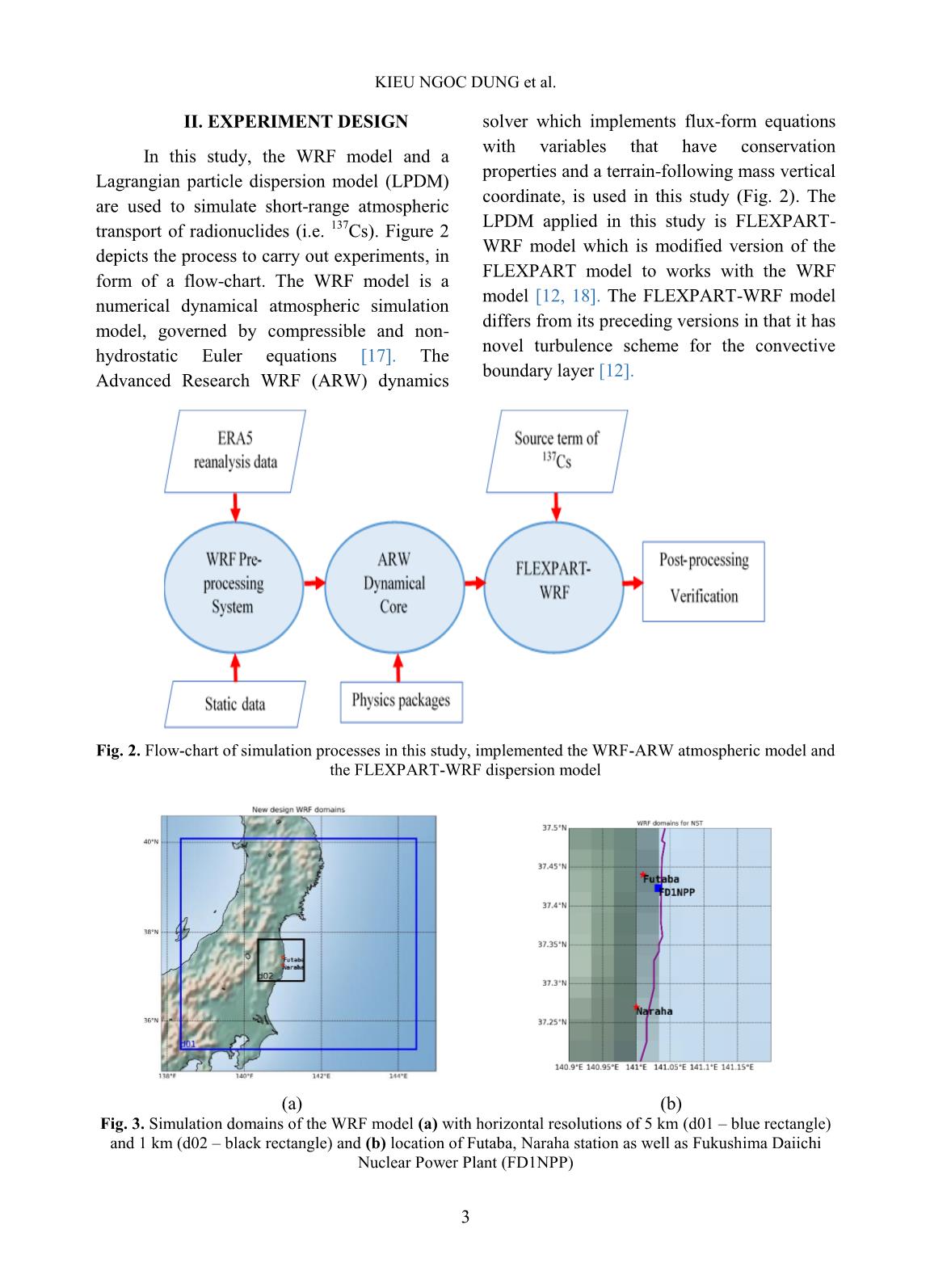
Trang 6
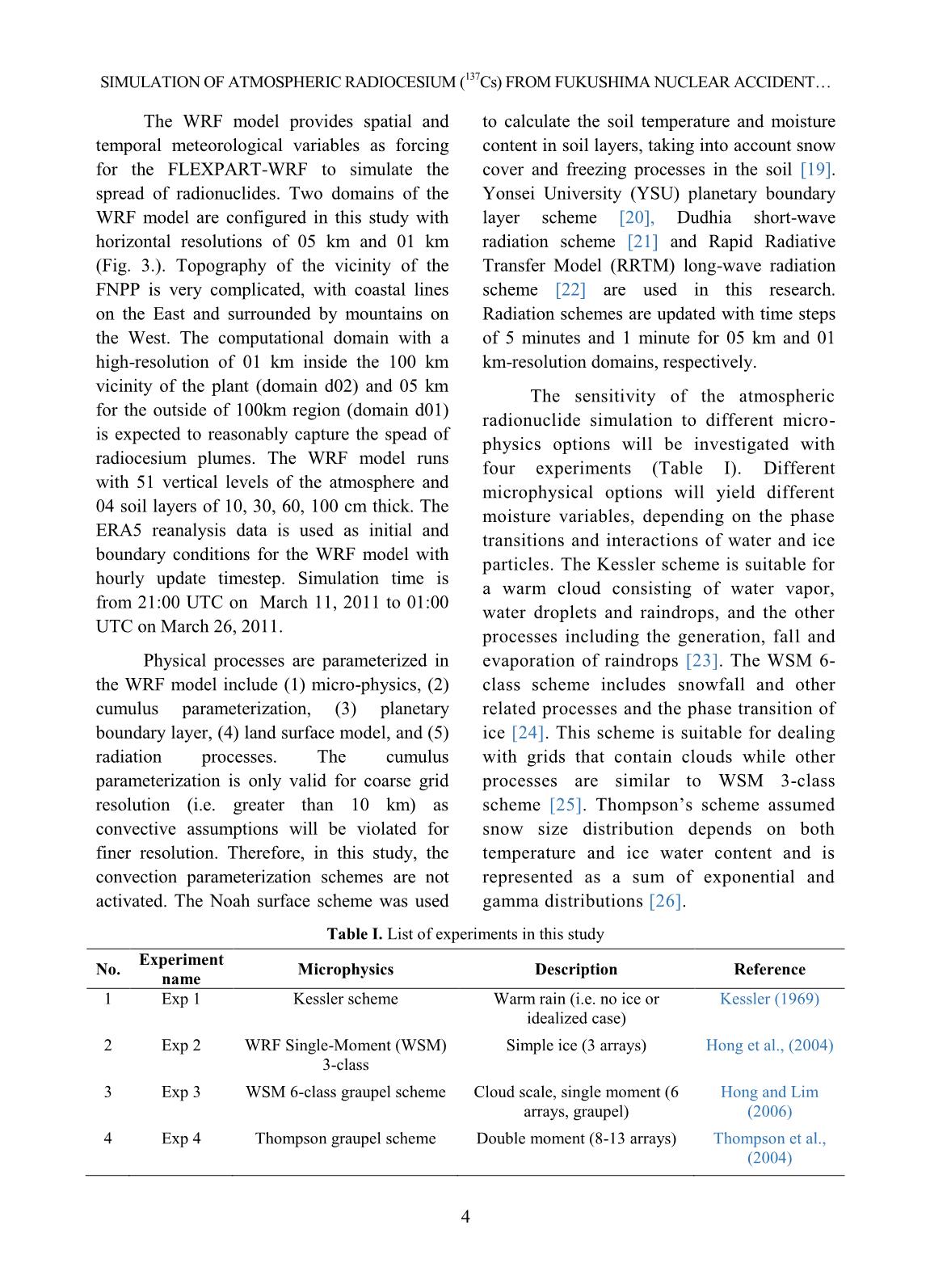
Trang 7
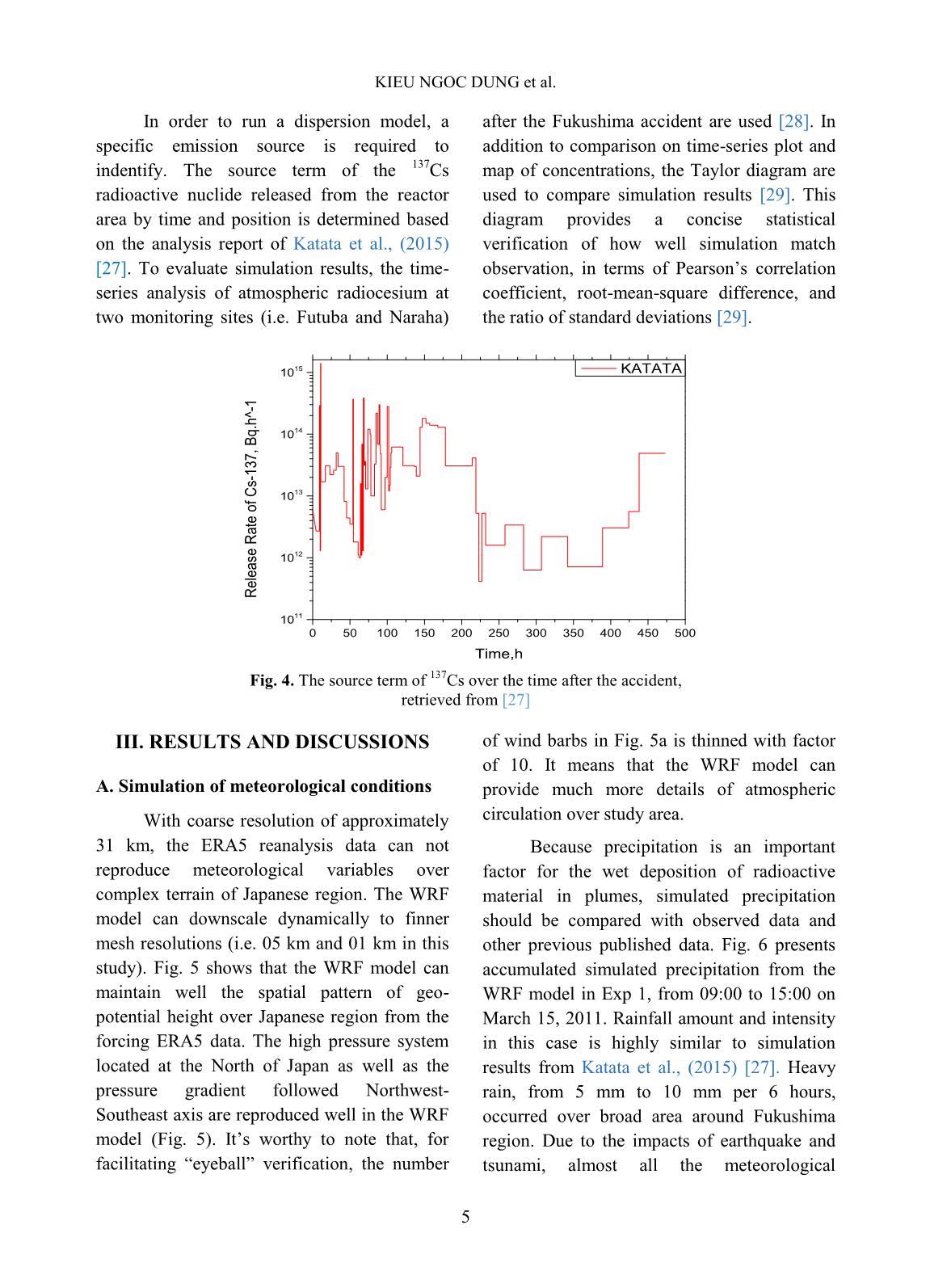
Trang 8
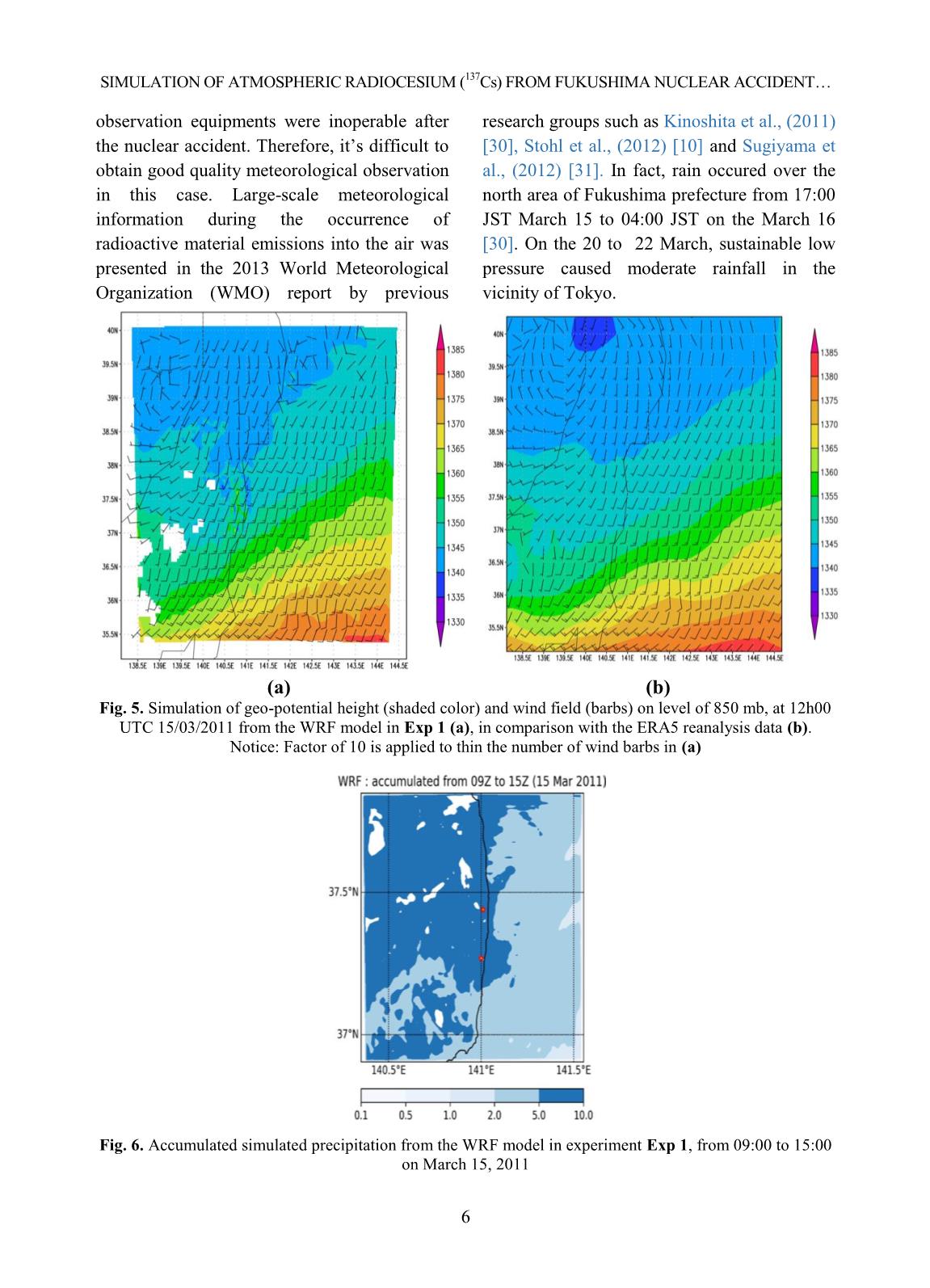
Trang 9
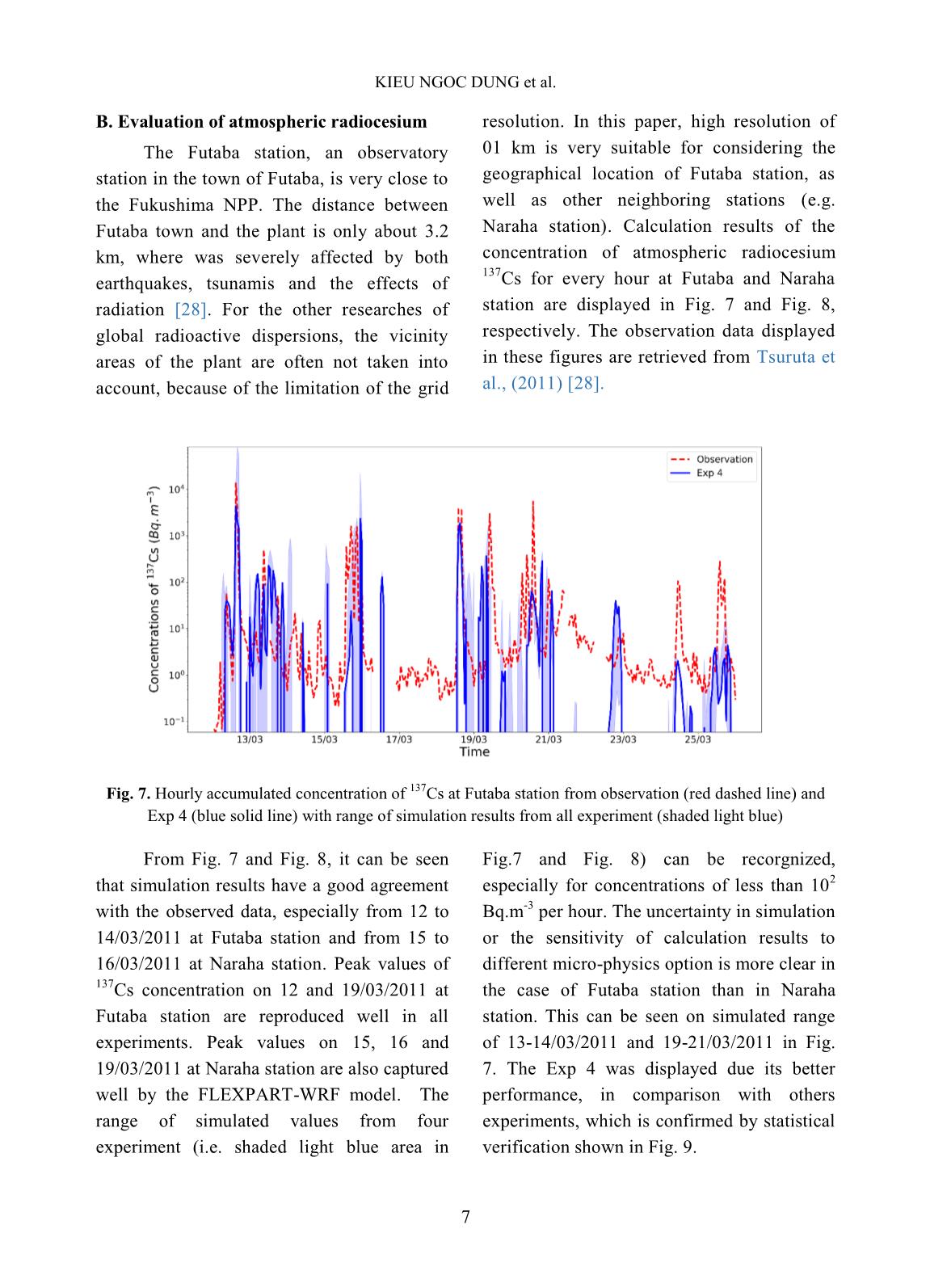
Trang 10
Tải về để xem bản đầy đủ
Tóm tắt nội dung tài liệu: Nuclear Science and Technology - Volume 10, Number 3, September 2020
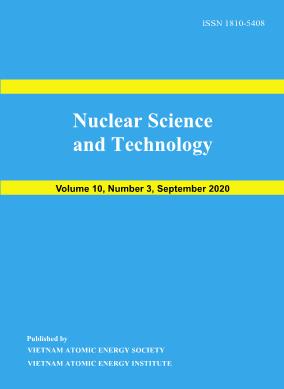
difference between the two measurement techniques is within ± 15%. This result is good and suitable for use in the two-phase flow experiment. B. Local time-averaged void fraction In order to present better local parameter distribution and transport characteristics, the results of bubbly flow test condition Run 4 is selected. The time- averaged local void fraction and bubble velocity profiles at all three axial locations are given in Figure 7. Each row from top to bottom represents the result at L/D = 14.4, 51.2 and 71.3, respectively. DINH ANH TUAN et al. 55 Fig. 6. Comparison of bubble velocity obtained by Imaging Technique and Conductivity Probe (a) (b) Fig. 7. Local profile of void fraction for run 4: jf = 1 m/s, jg = 0.05 m/s (a) Front Sensor; (b) Rear Sensor In Run 4, the void distribution experiences a change process of transition (flat) (L/D = 14.4) – wall peak (L/D = 51.2 and 71.3). This reason is explained by the bubble breakup mechanism. At inlet position (L/D = 14.4), wake entrainment mechanism is dominant, small bubbles coalescence to larger bubble, and drive bubbles toward pipe center. Along the flow path, the liquid velocity is high, and bubbles will be break up to smaller bubbles due to the turbulent effect and forced toward the wall by lift force, resulting in the wall peak void distribution. This bubble interaction mechanism also results in small amount change of void fraction at two upper axial positions. This phenomenon matches the measurement result in the work of Dang [5]. When the flow rate of gas is higher in run 9, the bubbles are fluctuated at the first EXPERIMENTAL INVESTIGATION OF HYDRODYNAMIC PHENOMENA IN 56 measurement position. Therefore, the void fraction at Front Sensor and Rear Sensor are quite different. Along the flow path, the bubble breakup to form smaller bubbles and concentrates at the wall region (Figure 8). Therefore, the void fraction in the wall region, at two upper measuring positions are higher than that of position measurement first. (a) (b) Fig. 8. Local profile of void fraction for run 9: jf = 1 m/s, jg = 0.1 m/s (a) Front Sensor; (b) Rear Sensor; (a) (b) Fig. 9. Local profile of void fraction for run 13: jf = 0.5 m/s, jg = 0.2 m/s (a) Front Sensor; (b) Rear Sensor; The local profiles of Run 13 are given in Figure. 9. In this flow condition, the major bubble shape is a slug and they cover the entire flow channel. Thus, group void distribution matches the shape of a slug bubble. However, under the same flow condition, the bubbly regime was recorded in previous study [15]. This experimental data was located near the boundary between bubbly and slug flow regime in Figure 5. Therefore, the difference can be explained by the fluctuation of air flow rate during the experiment, thus the flow regime was shifted from bubbly to slug flow. At the inlet position, bubbles coalescence to DINH ANH TUAN et al. 57 form larger bubbles. At second measuring position, the void distribution is affected by slug bubbles that small bubbles follow the slug bubbles, distributing in the slug bubbles’ wake regions. Besides, the effect of shear off mechanism starts to contribute to the number of small bubbles near-wall region. According to shear off mechanism, when slug bubbles are large enough, they are sheared at the rim, and many small bubbles show up. C. Bubble Velocity (a) (b) (c) Fig. 10. Local profile of bubble velocity: (a) Run 4; (b) Run 9; (c) Run 13 In run 4 and run 9, the interfacial velocity is distributed corresponding to the single-phase velocity profile and this agrees with Hibiki [18]. The liquid velocity profile is flattened when the gas is added. As shown in Figure 10, the value of bubble velocity is approximately equal to the sum of superficial velocities. When bubbles enter the wake region, they will accelerate and may collide with the leading one. Therefore, the bubble velocity at first position is slightly higher than the two upper measuring positions. In addition, near to the wall region, the velocity of the bubbles is strongly fluctuated due to wall friction and turbulent intensity. EXPERIMENTAL INVESTIGATION OF HYDRODYNAMIC PHENOMENA IN 58 In Run 13, the channel-averaged velocity at the higher measuring positions are gradually decreased and are distributed almost uniformly in the radius. This phenomenon occurs in the case of low water superficial velocity, and drag force is domination. As the bubble grows, the bubble is normally accelerated by the effect of buoyancy force. However, due to the effect of drag force, velocity in run 13 is suitable. V. CONCLUSIONS The experimental investigation on local interfacial parameters for vertical upward air- water two-phase flow was performed in this study. Two-sensor conductivity probe was used for the measurement of 25 flow conditions that covers from bubbly flow to slug flow. The local parameters included are a time-averaged void fraction and bubble interfacial velocity. The data acquisition frequency of 10 kHz and the sampling time of 60 s were applied. From the local experimental results, the profiles of void fraction and interfacial velocity along the axial and radial of the flow channel were discussed in detail. The bubble interaction mechanisms caused the differences in local parameter distribution. For high liquid superficial velocity (jf), the effect of buoyancy force is dominant, and bubble break up phenomena is observed. On the contrary, for low liquid superficial velocity (jf), the effect of drag force is dominant and bubble interaction mechanism will change from bubble break up to bubble coalescence. When changing the flow conditions, the void fraction distribution changes from wall peaking at Run 4 and Run 9 to center peak at Run 13. The reason might be due to the uncertainties in the measured results that need to be carefully considered and reduced in future works. In conclusion, the test facility, the experimental methods, and the preliminary experimental results obtained in this study can be helpful to study and comprehend the fundamental two-phase flow phenomena. For practical application in nuclear reactor safety, they are envisaged to be further improved and applied to verification and validation of calculation methods and codes, e.g., CFD codes, in modeling of two-phase flow. NOMENCLATURE D – pipe diameter g – acceleration of gravity L – length lchord – chord length N – number of bubble p – pressure t – time tdelay – delay time u – velocity V – Volume Greek Symbols α – void fraction µ – viscosity ρ – density σ – deviation standard Ω – total sampling time Subscripts b – bubble f – liquid g – gas ACKNOWLEDGEMENT This work was performed at Institute of Nuclear Science and Technology, Vietnam Atomic Energy Institute under the project “Construction of Thermal-hydraulic Experiment and Investigation of Hydrodynamic Phenomena of Two-phase Flow”, grant code DTCB.17/16/VKHKTHN. The authors would like to thank Ministry of Science and Technology for their support on this project. REFERENCES [1]. L.S. Tong and Y.S. Tang., Boiling Heat Transfer And Two-Phase Flow (Series in DINH ANH TUAN et al. 59 Chemical and Mechanical Engineering), CRC Press (book), 1997. [2]. L.G. Neal and S.G. Bankoff., A high resolution resistivity probe for determination of local void properties in gas-liquid flow. AIChEJ (9) 490-494, 1963. [3]. M. Walter., Study on interfacial area transport in vertical bubbly flows, Ingenieur Thesis, Korea Atomic Energy Research Institute, Korea, 2008. [4]. A. Manera, B. Ozar, S. Paranjape, M. Ishii, H.- M. Prasser., Comparison between wire-mesh sensors and conductive needle-probes for measurements of two-phase flow parameters, Nuclear Engineering and Design (239) 1718– 1724, 2009. [5]. Z. Dang, G. Wang, P. Ju, X. Yang, R. Bean, M. Ishii, S. Bajorek, M. Bernard., Experimental study of interfacial characteristics of vertical upward air-water two-phase flow in 25.4 mm ID round pipe. International Journal of Heat and Mass Transfer (108) 1825–1838, 2017. [6]. K. Sekoguchi, H. Fukui, M. Tsutsui and K. Nishikawa., Investigation into the statistical characteristics of bubbles in two-phase flow (2nd Report, Application and establishment of electrical resistivity probe method), Bull. JSME (18) 397-404, 1975. [7]. M.S. Hoffer and W. Resnick., A modified electro resistivity probe technique for steady- and unsteady-state measurements in fine dispersions – I. Hardware and practical aspects, Chem. Engng. Sci. (30) 473-480, 1975. [8]. J.M. Burgess and P.H. Calderbank., The measurement of bubble parameters in two- phase dispersions-I. The development of an improved probe techniques, Chem. Engng Sci. (30) 743-750, 1975. [9]. M. Behnia, S.J., Gillespie., Void fraction measurement by a computerized double-point resistivity probe. Flow. Meas. Instrum. (2) 243-247, 1991. [10]. W.H. Leung, S.T. Revankar, Y. Ishii and M. Ishii., Axial development of interfacial area and void concentration profiles measured by double-sensor probe method, Int. J. Heat Mass Transfer (38) 445-453, 1995. [11]. X. Zhao, G. Lucas, and S. Pradhan., Signal Processing method in using four-sensor probe for measuring the velocity vector of air-liquid two phase flow. Journal of the Japanese Society of Experimental Mechanics (JSEM) (9) 19-24, 2009. [12]. B.J. Yun, K.H. Kim, G.C. Park, C.H. Chung,, A study on the Measurement of Local Void Fraction. Journal of the Korean Nuclear Society 24(2) 168-177, 1992. [13]. D.J. Euh, B.J. Yun, C.H. Song, T.S. Kwon, M.K. Chung, U.C. Lee., Development of the five-sensor conductivity probe method for the measurement of the interfacial are concentration, Nuclear Engineering and Design (205) 35-51, 2001. [14]. I. Kataoka and A. Serizawa., Averaged bubble diameter and interfacial area in bubbly flow, Proc. 5th Two-phase Symp. Japan, Kobe, Japan, 28-29 November 77-80, 1984. [15]. Y. Taitel, D. Bornea and A. E. Dukler., Modelling Flow Pattern Transitions for Steady Upward Gas-Liquid Flow in Vertical Tubes, AlChE Journal (Vol. 26, No. 3) 345–354, 1980. [16]. M. Ishii and S. Kim., Micro four-sensor probe measurement of interfacial area transport for bubbly flow in round pipes. Nuclear Engineering and Design 205 123-131, 2001. [17]. M. McCreary., Design and Testing Conductivity Probes for the Measurement of Two-Phase Flow Parameters. MS Thesis, Oregon State University, US, 2001. [18]. T. Hibiki, M. Ishii, Z. Xiao., Axial interfacial area transport of vertical bubbly flows, International Journal of Heat and Mass Transfer (44) 1869–1888, 2001. INSTRUCTIONS FOR AUTHORS GENERAL INFORMATION Nuclear Science and Technology (NST), an international journal of the Vietnam Atomic Energy Society (VAES) and Vietnam Atomic Energy Institute (VINATOM), quarterly publishes articles related to theory and application of nuclear science and technology. All papers and technical notes will be refereed. It is understood that the paper has been neither published nor currently submitted for publication elsewhere. The copyright of all published papers and notes will be transferred in VAES. DETAILED FIELDS NST coves all fields of nuclear science and technology for peaceful utilization of nuclear energy and radiation. Authors should choose one of the following fields at the time they submit their manuscript: 1) Nuclear Physics, 2) Nuclear Data, 3) Reactor Physics, 4) Thermal Hydraulics, 5) Nuclear Safety, 6) Nuclear I&C, 7) Nuclear Fuel and Materials, 8) Radioactive Waste Management, 9) Radiation Protection, 10) Radiation Technology, 11) Nuclear Techniques in Food and Agriculture, 12) Nuclear Medicine and Radiotherapy, 13) Nuclear Techniques in Industries, 14) Environment Radioactivity, 15) Isotope Hydrology, 16) Nuclear Analytical Methods, 17) Health Physics, 18) Fusion and Laser Technology. MANUSCRIPT SUBMISSION Manuscript for publication should be submitted to the Editorial Office in triplicate by postal mail. For electronical submission use nuscitech@vinatom.gov.vn. Submission Address Department of Planning, R&D Management Vietnam Atomic Energy Institute, 59 Ly Thuong Kiet Street, Hanoi, Vietnam E-mail: nuscitech@vinatom.gov.vn. MANUSCRIPT PREPARATION Manuscripts must be written in English with adequate margins and indented paragraph. All manuscript must use SI (metric) units in text, figures, and tables. Manuscripts should in general be organized in the following order: title, names of authors and their complete affiliation including zip code, abstract (not exceeding 200 words), keywords (up to 7), introduction, main body of a paper, acknowledgments, references, appendices, table & figure captions, tables and figures. Unnecessary sections may be omitted. Headings: Use I, II, for major headings and A, B, for secondary headings. Mathematical formulas: All mathematical formulas should be clearly written, with special consideration to distinctive legibility of sub-and superscripts. Equation (at least the principal ones) should be numbered consecutively using Arabic numerals in parentheses in the right hand margin. Tables and Figures: Tables should be numbered with Roman numerals. Figures should be numbered consecutively with Arabic numerals in order of their first appearance and have a complete descriptive title. They should be typed on separate sheets. Tables should no repeat data which are available elsewhere in the paper. Figures should be original ink drawing or computer drawn figures in the original and of high quality, ready for direct reproduction. Figures should be referred to in the text as, for example, Fig. 1., or Fig. 2. . Reference: References should be listed at the end of the text and presented as follows: [1] C. Y. Fu et al., Nuclear Data for Science and Technology, S. M. Qaim (Ed.), p. 587 (1991). [2] C. Kalbach, Z. Phys, A283, 401 (1977). [3] S. Shibata, M. Imamura, T. Miyachi and M. Mutou, “Photonuclear spallation reactions in Cu”, Phys. Rev. C 35, 254 (1987). KHOA HỌC VÀ CÔNG NGHỆ HẠT NHÂN Chịu trách nhiệm xuất bản TRẦN HỮU PHÁT Chịu trách nhiệm nội dung TRẦN HỮU PHÁT TRẦN CHÍ THÀNH Trình bày LÊ THÚY MAI In 200 cuốn, khổ 19x26,5cm tại Công ty TNHH Trần Công Địa chỉ: số 12 ngách 155/176 Đường Trường Chinh, Hà Nội Giấy đăng ký kế hoạch xuất bản số: 770/GP-BTTTT cấp ngày 20 tháng 5 năm 2011 In xong và nộp lưu chiểu Quý IV năm 2020 25 000đ
File đính kèm:
nuclear_science_and_technology_volume_10_number_3_september.pdf