Chế tạo hạt nano Pt/C, Pt-Ru/C và ảnh hưởng của quá trình ép nhiệt trên hiệu suất của pin nhiên liệu dùng methanol trực tiếp
Mục tiêu nghiên cứu của đề tài nhằm khảo sát vai trò của nhiệt độ trong quá trình chế
tạo màng phủ xúc tác (CCM) bằng phương pháp decal và tổng hợp xúc tác hạt nano tại
cathode và anode là Pt/C, PtRu/C. Từ kết quả FESEM cho thấy sự phân bố hạt trên bề
mặt lớp xúc tác tại các nhiệt độ 175 oC, 185 oC, 195 oC và tính đường kính trung bình độ
xốp. Qua đó, khi ở nhiệt độ 185 oC sự phân bố đồng đều nhất và đường kính trung bình
độ xốp là 0,85m . Màng CCM tại nhiệt độ 185 oC cải thiện được sự tiếp xúc giữa lớp
xúc tác và màng, hiệu suất đầu ra của pin là cao nhất thông qua đường đặc trưng I-V và
xác định mối quan hệ I-P, đạt giá trị điện thế, mật độ dòng điện và mật độ công suất lớn
nhất là 0,625V, 162 mA.cm-2, 22,4 mW.cm-2. Khi nhiệt độ tăng đến 195 oC điện thế, mật
độ dòng điện và mật độ công suất giảm đáng kể là 0,58 V, 122 mA.cm-2, 15,2 mW.cm-2.
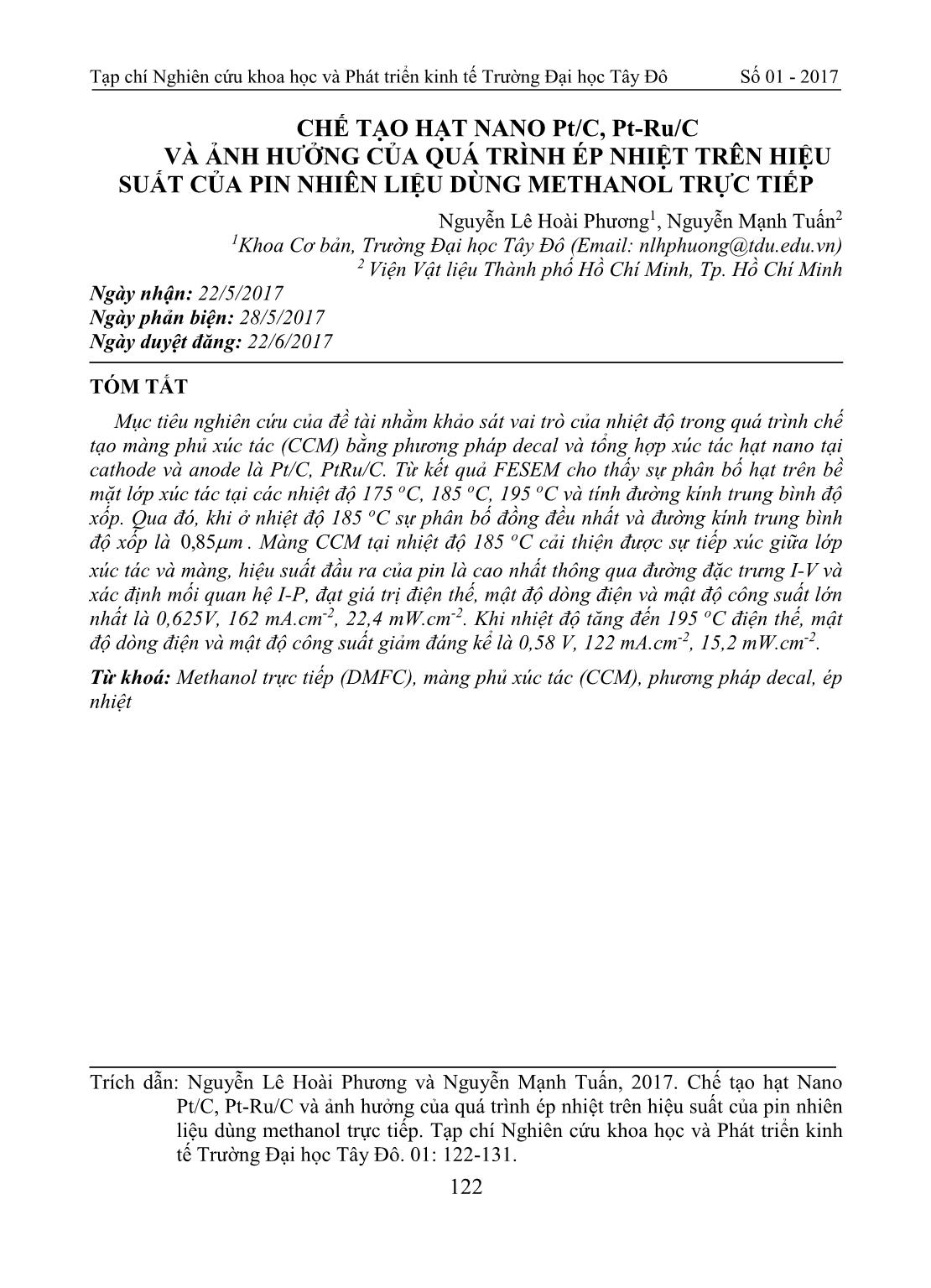
Trang 1
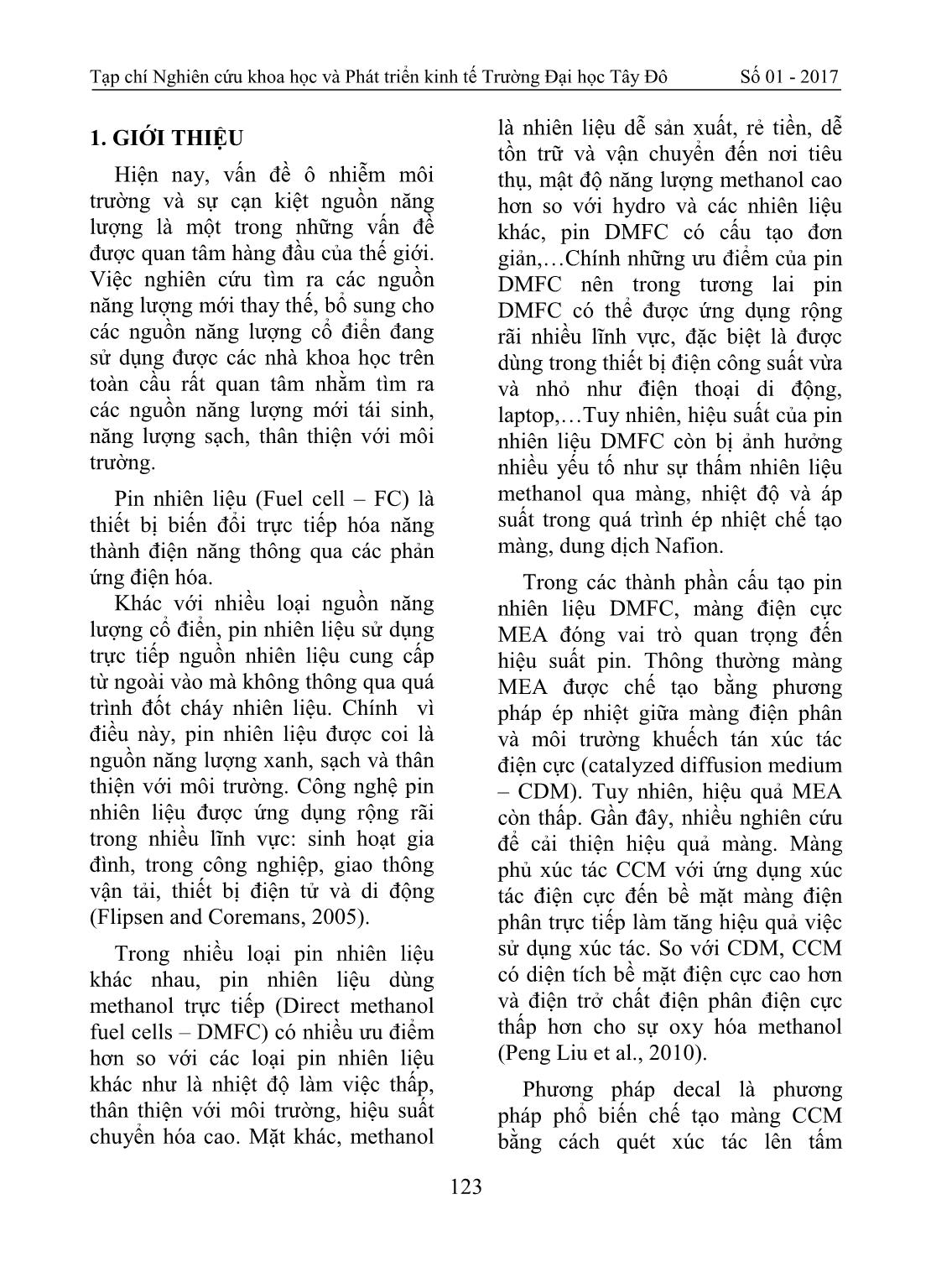
Trang 2
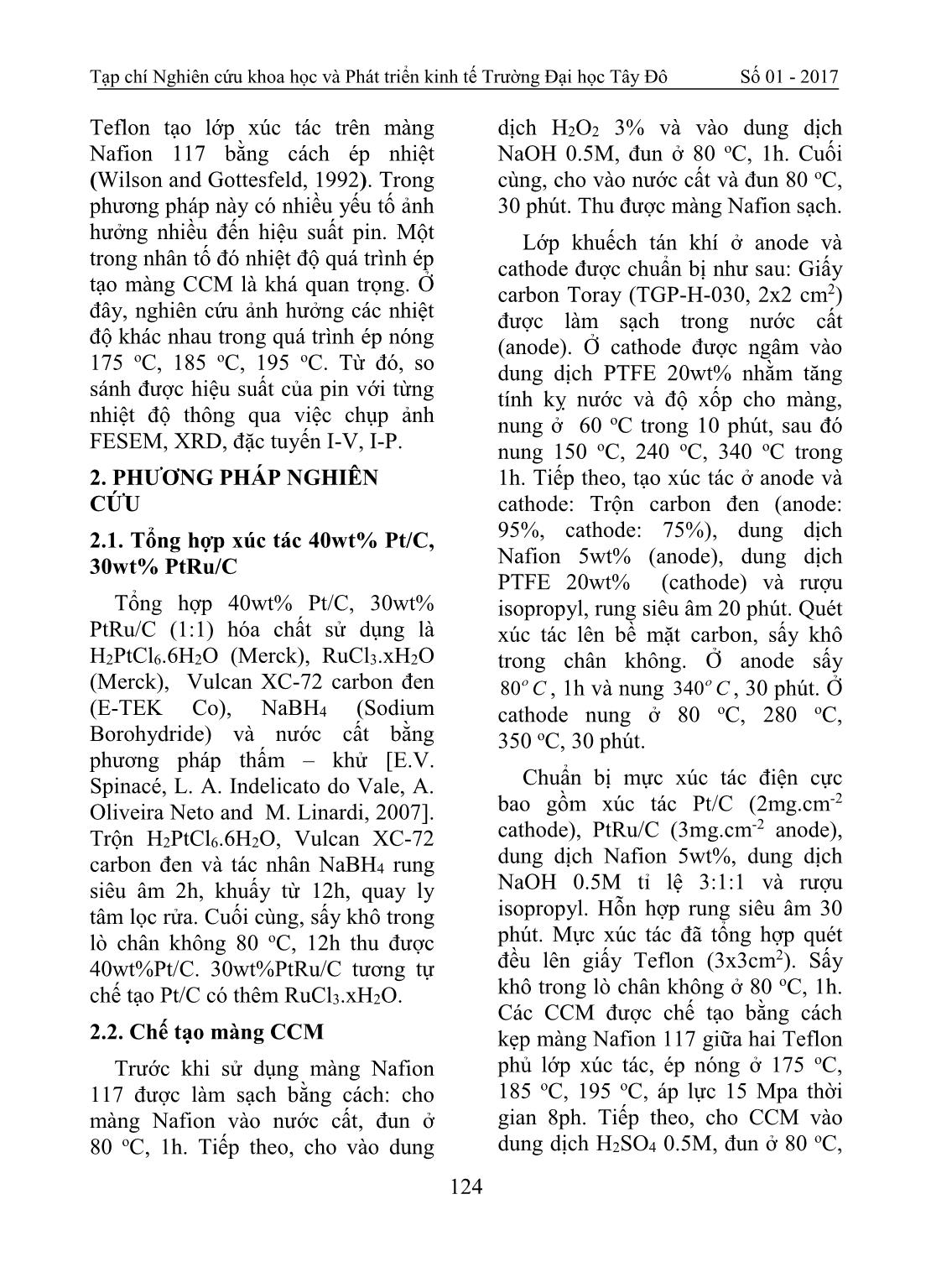
Trang 3

Trang 4

Trang 5
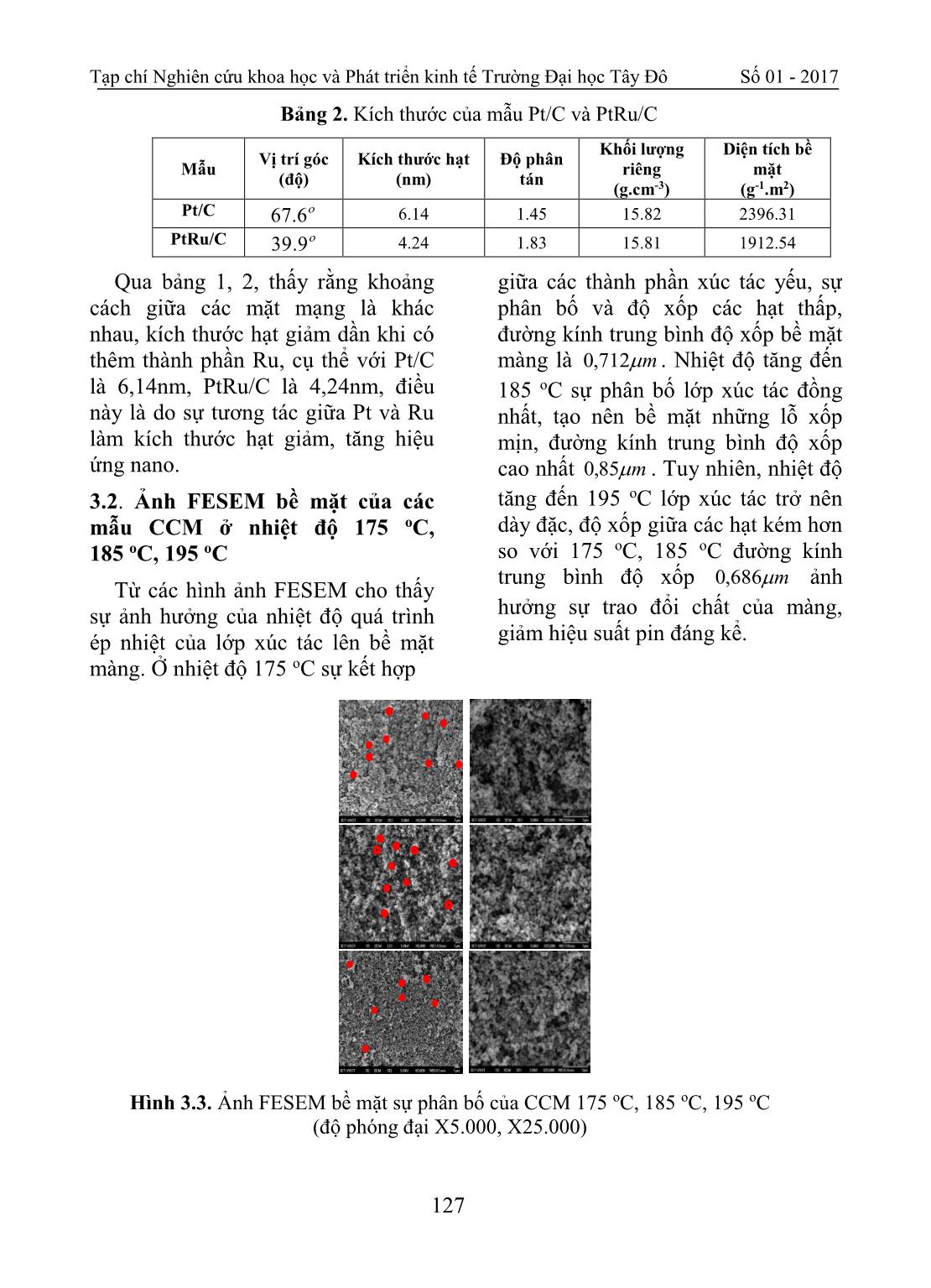
Trang 6
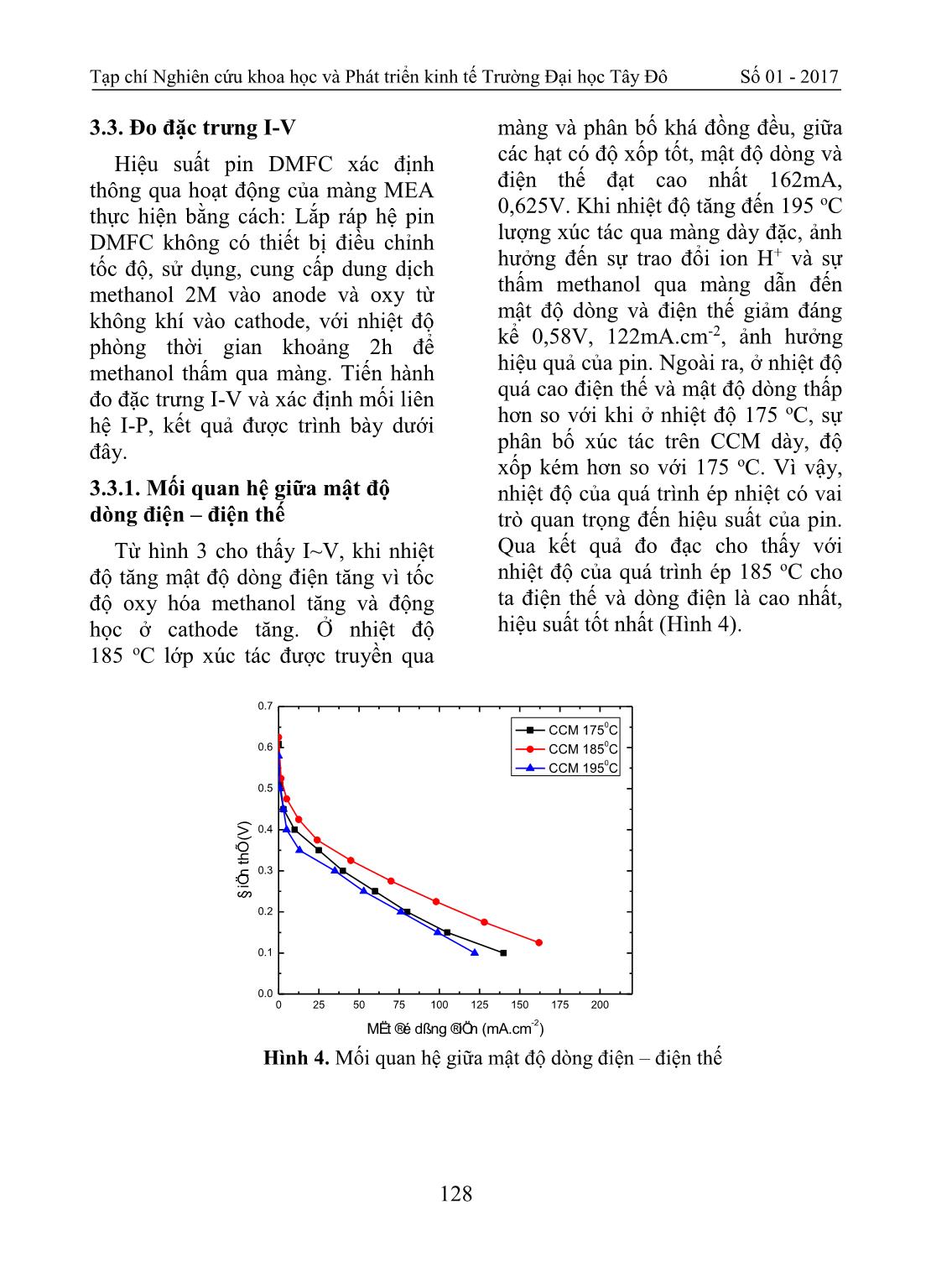
Trang 7
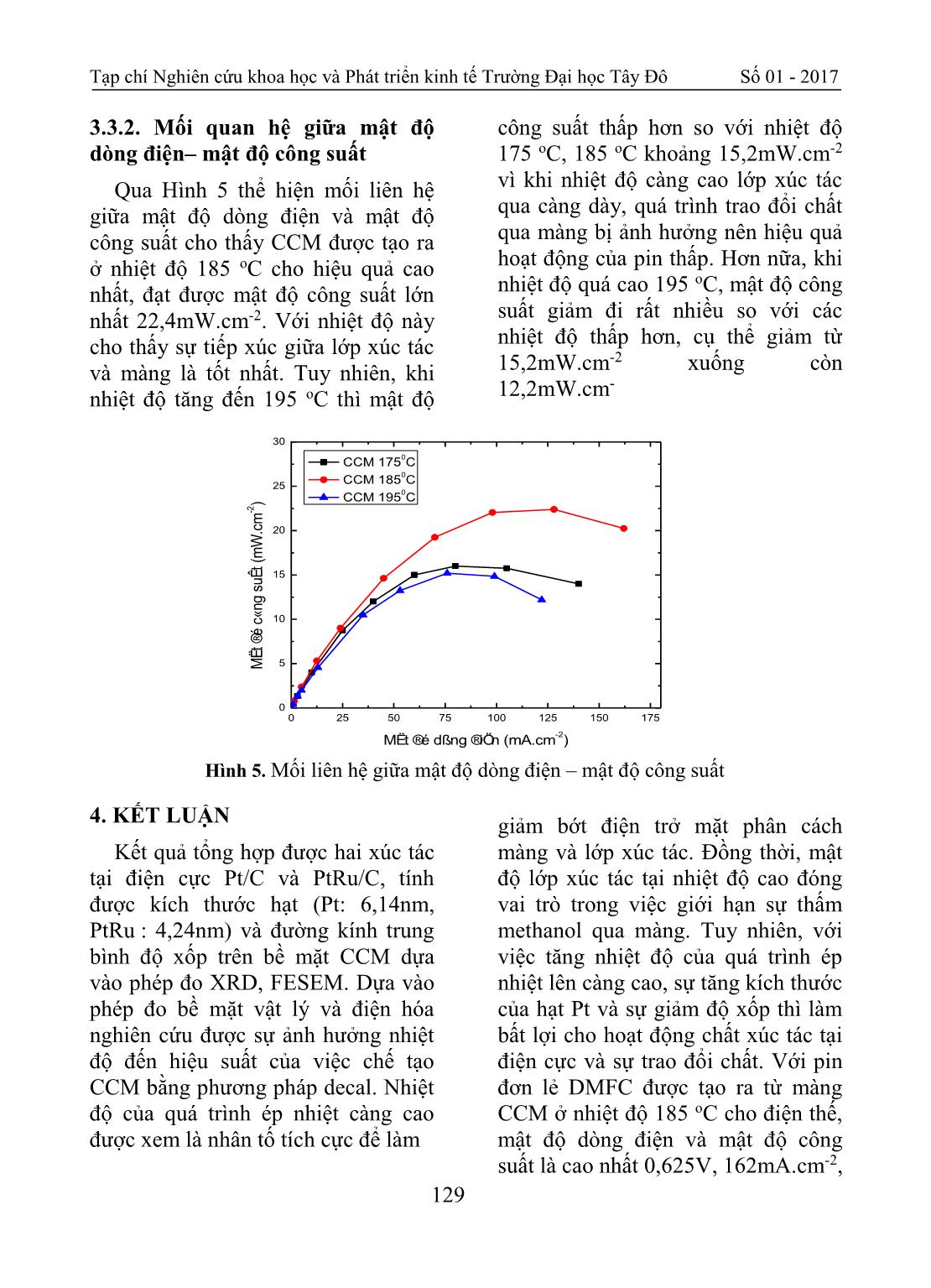
Trang 8
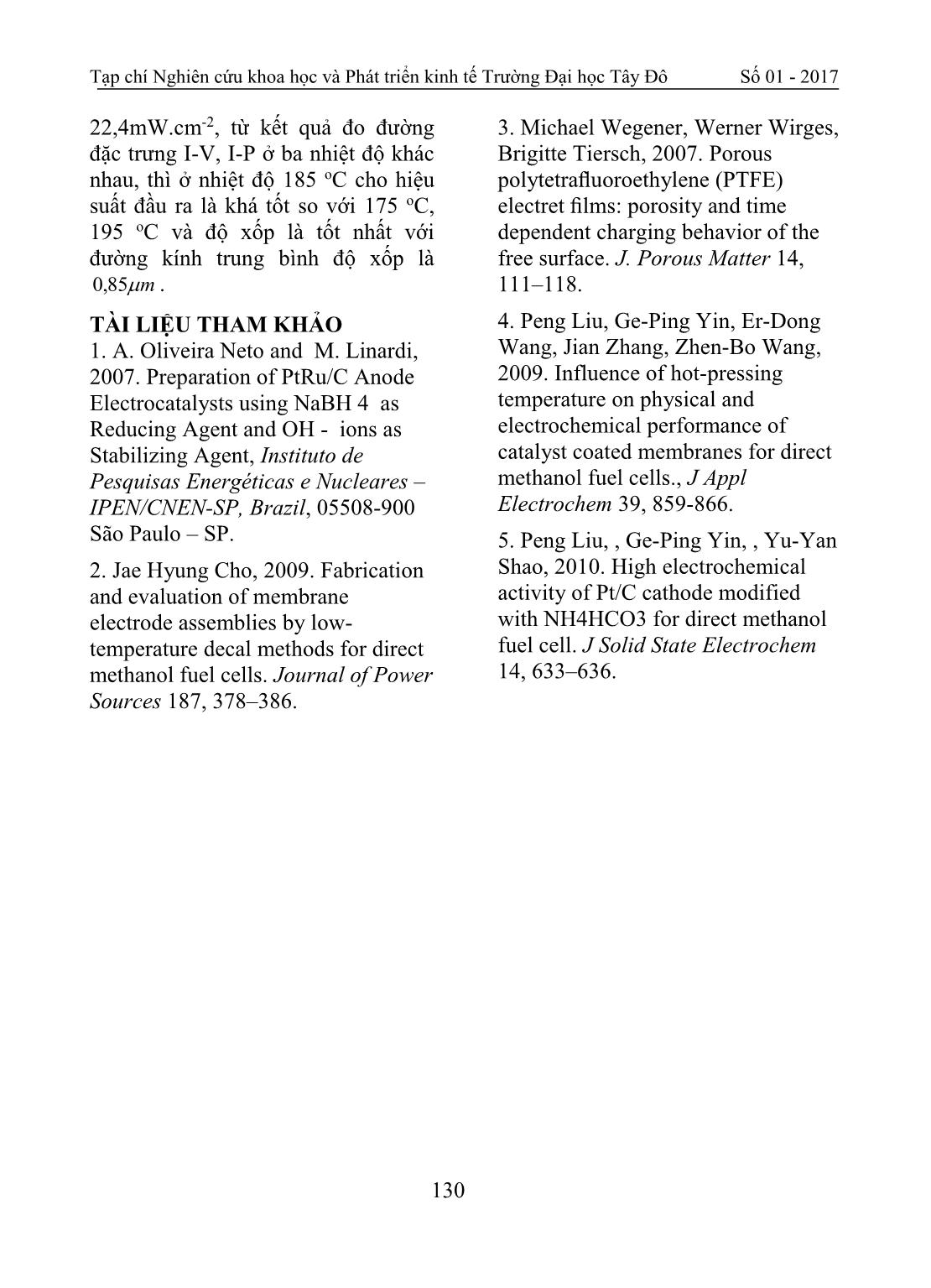
Trang 9
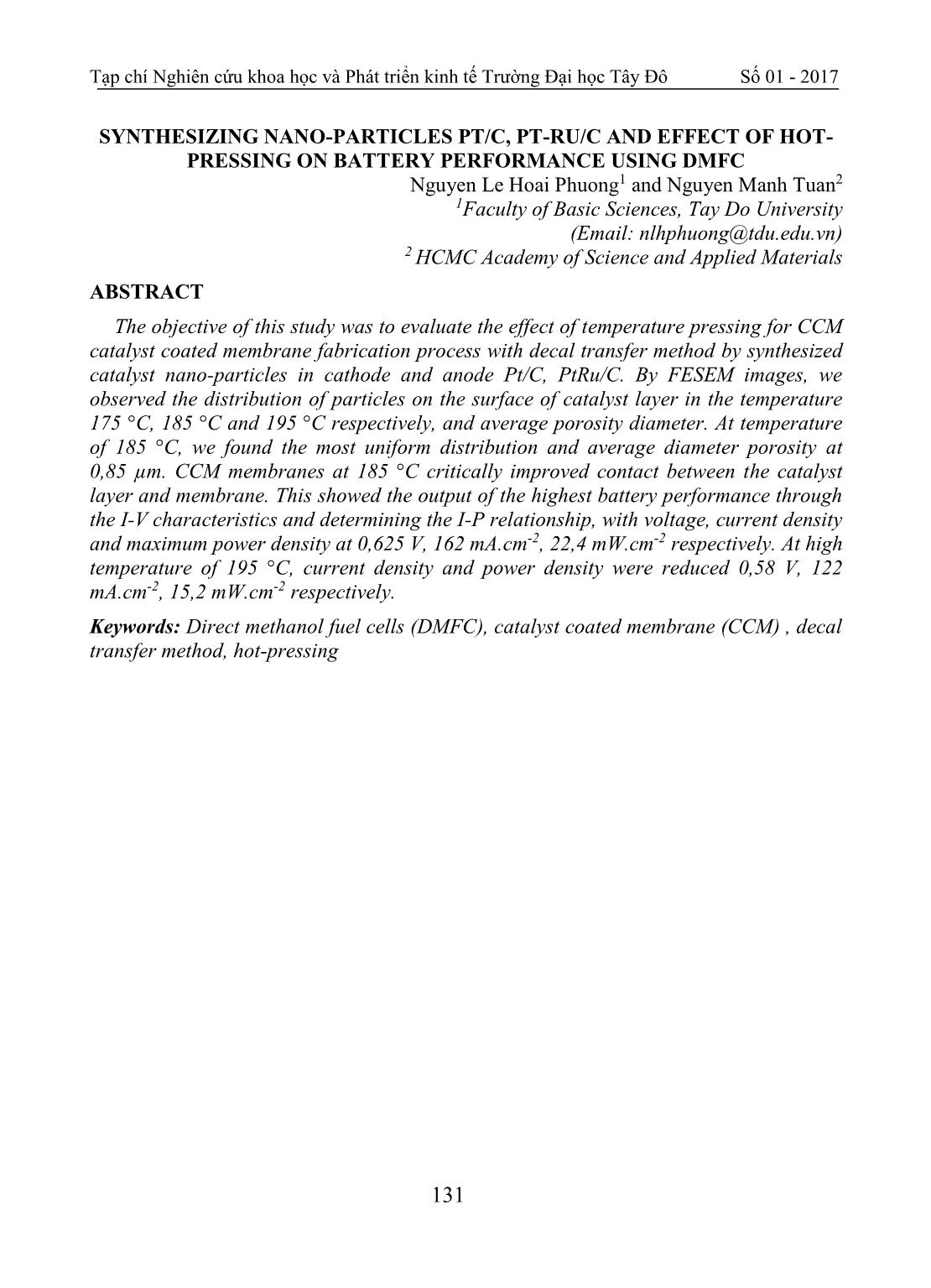
Trang 10
Tóm tắt nội dung tài liệu: Chế tạo hạt nano Pt/C, Pt-Ru/C và ảnh hưởng của quá trình ép nhiệt trên hiệu suất của pin nhiên liệu dùng methanol trực tiếp
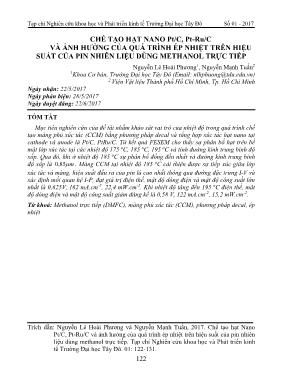
iao thông vận tải, thiết bị điện tử và di động (Flipsen and Coremans, 2005). Trong nhiều loại pin nhiên liệu khác nhau, pin nhiên liệu dùng methanol trực tiếp (Direct methanol fuel cells – DMFC) có nhiều ưu điểm hơn so với các loại pin nhiên liệu khác như là nhiệt độ làm việc thấp, thân thiện với môi trường, hiệu suất chuyển hóa cao. Mặt khác, methanol là nhiên liệu dễ sản xuất, rẻ tiền, dễ tồn trữ và vận chuyển đến nơi tiêu thụ, mật độ năng lượng methanol cao hơn so với hydro và các nhiên liệu khác, pin DMFC có cấu tạo đơn giản,Chính những ưu điểm của pin DMFC nên trong tương lai pin DMFC có thể được ứng dụng rộng rãi nhiều lĩnh vực, đặc biệt là được dùng trong thiết bị điện công suất vừa và nhỏ như điện thoại di động, laptop,Tuy nhiên, hiệu suất của pin nhiên liệu DMFC còn bị ảnh hưởng nhiều yếu tố như sự thấm nhiên liệu methanol qua màng, nhiệt độ và áp suất trong quá trình ép nhiệt chế tạo màng, dung dịch Nafion. Trong các thành phần cấu tạo pin nhiên liệu DMFC, màng điện cực MEA đóng vai trò quan trọng đến hiệu suất pin. Thông thường màng MEA được chế tạo bằng phương pháp ép nhiệt giữa màng điện phân và môi trường khuếch tán xúc tác điện cực (catalyzed diffusion medium – CDM). Tuy nhiên, hiệu quả MEA còn thấp. Gần đây, nhiều nghiên cứu để cải thiện hiệu quả màng. Màng phủ xúc tác CCM với ứng dụng xúc tác điện cực đến bề mặt màng điện phân trực tiếp làm tăng hiệu quả việc sử dụng xúc tác. So với CDM, CCM có diện tích bề mặt điện cực cao hơn và điện trở chất điện phân điện cực thấp hơn cho sự oxy hóa methanol (Peng Liu et al., 2010). Phương pháp decal là phương pháp phổ biến chế tạo màng CCM bằng cách quét xúc tác lên tấm Tạp chí Nghiên cứu khoa học và Phát triển kinh tế Trường Đại học Tây Đô Số 01 - 2017 124 Teflon tạo lớp xúc tác trên màng Nafion 117 bằng cách ép nhiệt (Wilson and Gottesfeld, 1992). Trong phương pháp này có nhiều yếu tố ảnh hưởng nhiều đến hiệu suất pin. Một trong nhân tố đó nhiệt độ quá trình ép tạo màng CCM là khá quan trọng. Ở đây, nghiên cứu ảnh hưởng các nhiệt độ khác nhau trong quá trình ép nóng 175 oC, 185 oC, 195 oC. Từ đó, so sánh được hiệu suất của pin với từng nhiệt độ thông qua việc chụp ảnh FESEM, XRD, đặc tuyến I-V, I-P. 2. PHƯƠNG PHÁP NGHIÊN CỨU 2.1. Tổng hợp xúc tác 40wt% Pt/C, 30wt% PtRu/C Tổng hợp 40wt% Pt/C, 30wt% PtRu/C (1:1) hóa chất sử dụng là H2PtCl6.6H2O (Merck), RuCl3.xH2O (Merck), Vulcan XC-72 carbon đen (E-TEK Co), NaBH4 (Sodium Borohydride) và nước cất bằng phương pháp thấm – khử [E.V. Spinacé, L. A. Indelicato do Vale, A. Oliveira Neto and M. Linardi, 2007]. Trộn H2PtCl6.6H2O, Vulcan XC-72 carbon đen và tác nhân NaBH4 rung siêu âm 2h, khuấy từ 12h, quay ly tâm lọc rửa. Cuối cùng, sấy khô trong lò chân không 80 oC, 12h thu được 40wt%Pt/C. 30wt%PtRu/C tương tự chế tạo Pt/C có thêm RuCl3.xH2O. 2.2. Chế tạo màng CCM Trước khi sử dụng màng Nafion 117 được làm sạch bằng cách: cho màng Nafion vào nước cất, đun ở 80 oC, 1h. Tiếp theo, cho vào dung dịch H2O2 3% và vào dung dịch NaOH 0.5M, đun ở 80 oC, 1h. Cuối cùng, cho vào nước cất và đun 80 oC, 30 phút. Thu được màng Nafion sạch. Lớp khuếch tán khí ở anode và cathode được chuẩn bị như sau: Giấy carbon Toray (TGP-H-030, 2x2 cm2) được làm sạch trong nước cất (anode). Ở cathode được ngâm vào dung dịch PTFE 20wt% nhằm tăng tính kỵ nước và độ xốp cho màng, nung ở 60 oC trong 10 phút, sau đó nung 150 oC, 240 oC, 340 oC trong 1h. Tiếp theo, tạo xúc tác ở anode và cathode: Trộn carbon đen (anode: 95%, cathode: 75%), dung dịch Nafion 5wt% (anode), dung dịch PTFE 20wt% (cathode) và rượu isopropyl, rung siêu âm 20 phút. Quét xúc tác lên bề mặt carbon, sấy khô trong chân không. Ở anode sấy C 80 , 1h và nung C 340 , 30 phút. Ở cathode nung ở 80 oC, 280 oC, 350 oC, 30 phút. Chuẩn bị mực xúc tác điện cực bao gồm xúc tác Pt/C (2mg.cm-2 cathode), PtRu/C (3mg.cm-2 anode), dung dịch Nafion 5wt%, dung dịch NaOH 0.5M tỉ lệ 3:1:1 và rượu isopropyl. Hỗn hợp rung siêu âm 30 phút. Mực xúc tác đã tổng hợp quét đều lên giấy Teflon (3x3cm2). Sấy khô trong lò chân không ở 80 oC, 1h. Các CCM được chế tạo bằng cách kẹp màng Nafion 117 giữa hai Teflon phủ lớp xúc tác, ép nóng ở 175 oC, 185 oC, 195 oC, áp lực 15 Mpa thời gian 8ph. Tiếp theo, cho CCM vào dung dịch H2SO4 0.5M, đun ở 80 oC, Tạp chí Nghiên cứu khoa học và Phát triển kinh tế Trường Đại học Tây Đô Số 01 - 2017 125 1h và đun trong nước cất loại acid. Cuối cùng, màng MEA hình thành bằng cách kẹp CCM giữa các lớp khuếch tán khí, được ép nhiệt ở nhiệt độ 140 oC với áp lực 8MPa trong 8 phút. Đo XRD của Pt/C và PtRu/C, hình ảnh bề mặt của màng CCM bằng phương pháp FESEM, đường đặc tuyến I-V và xác định mối liên hệ I-P. 3. KẾT QUẢ VÀ THẢO LUẬN 3.1. Phân tích phổ nhiễu xạ của mẫu Pt/C và PtRu/C Kết quả đo phổ nhiễu xạ tia X của điện cực Pt/C (Hình 1). - Ray của mẫu Pt/C cho ta thấy sự hiện diện của Pt có cấu trúc fcc. Với đỉnh nhiễu xạ tại góc 25º là do nhiễu xạ từ mặt mạng (002) của carbon tăng cường. Những đỉnh vạch nhiễu xạ mạnh tại các góc thỏa điều kiện Vulff-Bragg là 39,82º; 46,3º; 67,6º thì tương ứng với các mặt mạng (110), (200), (220). Theo phương trình Scherrer ta tính được kích thước hạt. 2 ax 0.9 os m d B c Ở đây, kích thước trung bình của hạt được tính tại góc 67,6º vì tại đỉnh (220) này hoàn toàn tách biệt với đỉnh nhiễu xạ của carbon tăng cường, Hình 1. Phổ nhiễu xạ tia X của Pt/C Tạp chí Nghiên cứu khoa học và Phát triển kinh tế Trường Đại học Tây Đô Số 01 - 2017 126 khi đó kích thước hạt Pt tính được khoảng 4 - 7nm. Kết quả đo phổ nhiễu xạ tia X điện cực Pt-Ru/C được trình bày ở Hình 2. Qua phổ nhiễu xạ của mẫu PtRu/C cho thấy các đỉnh vạch nhiễu xạ chỉ đặc trưng cho Pt mà không có đỉnh nào đặc trưng cho Ru, đây là do có sự hình thành dung dịch rắn của Ru trong Pt nên không có sự tách pha, dẫn đến không có xuất hiện đỉnh vạch nhiễu xạ cho Ru. Các đỉnh vạch nhiễu xạ của Pt trong mẫu PtRu/C bị lệch so với Pt/C, cụ thể tại các đỉnh vạch nhiễu xạ thõa mãn điều kiện Vulff-Bragg là 39,9º; 46,2º; 67.8º. Đối với mẫu PtRu/C khi ta thêm lượng Ru vào Pt, qua hình ảnh nhiễu xạ ta thấy các đỉnh vạch nhiễu tại các góc lớn hơn so với Pt/C do sự tạo thành hợp kim Pt và Ru. Mẫu Khoảng cách giữa các mặt mạng (nm) (110) (200) (220) Pt/C 2.26434 1.95934 1.38307 PtRu/C 2.26114 1.95754 1.37982 Bảng 1. Khoảng cách giữa các mặt mạng của Pt/C và PtRu/C Hình 2. Ảnh nhiễu xạ tia X của mẫu PtRu/C Tạp chí Nghiên cứu khoa học và Phát triển kinh tế Trường Đại học Tây Đô Số 01 - 2017 Mẫu Vị trí góc (độ) Kích thước hạt (nm) Độ phân tán Khối lượng riêng (g.cm-3) Diện tích bề mặt (g-1.m2) Pt/C 6.67 6.14 1.45 15.82 2396.31 PtRu/C 9.39 4.24 1.83 15.81 1912.54 Qua bảng 1, 2, thấy rằng khoảng cách giữa các mặt mạng là khác nhau, kích thước hạt giảm dần khi có thêm thành phần Ru, cụ thể với Pt/C là 6,14nm, PtRu/C là 4,24nm, điều này là do sự tương tác giữa Pt và Ru làm kích thước hạt giảm, tăng hiệu ứng nano. 3.2. Ảnh FESEM bề mặt của các mẫu CCM ở nhiệt độ 175 oC, 185 oC, 195 oC Từ các hình ảnh FESEM cho thấy sự ảnh hưởng của nhiệt độ quá trình ép nhiệt của lớp xúc tác lên bề mặt màng. Ở nhiệt độ 175 oC sự kết hợp giữa các thành phần xúc tác yếu, sự phân bố và độ xốp các hạt thấp, đường kính trung bình độ xốp bề mặt màng là m712,0 . Nhiệt độ tăng đến 185 oC sự phân bố lớp xúc tác đồng nhất, tạo nên bề mặt những lỗ xốp mịn, đường kính trung bình độ xốp cao nhất m85,0 . Tuy nhiên, nhiệt độ tăng đến 195 oC lớp xúc tác trở nên dày đặc, độ xốp giữa các hạt kém hơn so với 175 oC, 185 oC đường kính trung bình độ xốp m686,0 ảnh hưởng sự trao đổi chất của màng, giảm hiệu suất pin đáng kể. Bảng 2. Kích thước của mẫu Pt/C và PtRu/C Hình 3.3. Ảnh FESEM bề mặt sự phân bố của CCM 175 oC, 185 oC, 195 oC (độ phóng đại X5.000, X25.000) 127 Tạp chí Nghiên cứu khoa học và Phát triển kinh tế Trường Đại học Tây Đô Số 01 - 2017 3.3. Đo đặc trưng I-V Hiệu suất pin DMFC xác định thông qua hoạt động của màng MEA thực hiện bằng cách: Lắp ráp hệ pin DMFC không có thiết bị điều chỉnh tốc độ, sử dụng, cung cấp dung dịch methanol 2M vào anode và oxy từ không khí vào cathode, với nhiệt độ phòng thời gian khoảng 2h để methanol thấm qua màng. Tiến hành đo đặc trưng I-V và xác định mối liên hệ I-P, kết quả được trình bày dưới đây. 3.3.1. Mối quan hệ giữa mật độ dòng điện – điện thế Từ hình 3 cho thấy I~V, khi nhiệt độ tăng mật độ dòng điện tăng vì tốc độ oxy hóa methanol tăng và động học ở cathode tăng. Ở nhiệt độ 185 oC lớp xúc tác được truyền qua màng và phân bố khá đồng đều, giữa các hạt có độ xốp tốt, mật độ dòng và điện thế đạt cao nhất 162mA, 0,625V. Khi nhiệt độ tăng đến 195 oC lượng xúc tác qua màng dày đặc, ảnh hưởng đến sự trao đổi ion H+ và sự thấm methanol qua màng dẫn đến mật độ dòng và điện thế giảm đáng kể 0,58V, 122mA.cm-2, ảnh hưởng hiệu quả của pin. Ngoài ra, ở nhiệt độ quá cao điện thế và mật độ dòng thấp hơn so với khi ở nhiệt độ 175 oC, sự phân bố xúc tác trên CCM dày, độ xốp kém hơn so với 175 oC. Vì vậy, nhiệt độ của quá trình ép nhiệt có vai trò quan trọng đến hiệu suất của pin. Qua kết quả đo đạc cho thấy với nhiệt độ của quá trình ép 185 oC cho ta điện thế và dòng điện là cao nhất, hiệu suất tốt nhất (Hình 4). Hình 4. Mối quan hệ giữa mật độ dòng điện – điện thế 0 25 50 75 100 125 150 175 200 0.0 0.1 0.2 0.3 0.4 0.5 0.6 0.7 § iÖ n t h Õ ( V ) MËt ®é dßng ®iÖn (mA.cm -2 ) CCM 175 0 C CCM 185 0 C CCM 195 0 C 128 Tạp chí Nghiên cứu khoa học và Phát triển kinh tế Trường Đại học Tây Đô Số 01 - 2017 3.3.2. Mối quan hệ giữa mật độ dòng điện– mật độ công suất Qua Hình 5 thể hiện mối liên hệ giữa mật độ dòng điện và mật độ công suất cho thấy CCM được tạo ra ở nhiệt độ 185 oC cho hiệu quả cao nhất, đạt được mật độ công suất lớn nhất 22,4mW.cm-2. Với nhiệt độ này cho thấy sự tiếp xúc giữa lớp xúc tác và màng là tốt nhất. Tuy nhiên, khi nhiệt độ tăng đến 195 oC thì mật độ công suất thấp hơn so với nhiệt độ 175 oC, 185 oC khoảng 15,2mW.cm-2 vì khi nhiệt độ càng cao lớp xúc tác qua càng dày, quá trình trao đổi chất qua màng bị ảnh hưởng nên hiệu quả hoạt động của pin thấp. Hơn nữa, khi nhiệt độ quá cao 195 oC, mật độ công suất giảm đi rất nhiều so với các nhiệt độ thấp hơn, cụ thể giảm từ 15,2mW.cm-2 xuống còn 12,2mW.cm- 4. KẾT LUẬN Kết quả tổng hợp được hai xúc tác tại điện cực Pt/C và PtRu/C, tính được kích thước hạt (Pt: 6,14nm, PtRu : 4,24nm) và đường kính trung bình độ xốp trên bề mặt CCM dựa vào phép đo XRD, FESEM. Dựa vào phép đo bề mặt vật lý và điện hóa nghiên cứu được sự ảnh hưởng nhiệt độ đến hiệu suất của việc chế tạo CCM bằng phương pháp decal. Nhiệt độ của quá trình ép nhiệt càng cao được xem là nhân tố tích cực để làm giảm bớt điện trở mặt phân cách màng và lớp xúc tác. Đồng thời, mật độ lớp xúc tác tại nhiệt độ cao đóng vai trò trong việc giới hạn sự thấm methanol qua màng. Tuy nhiên, với việc tăng nhiệt độ của quá trình ép nhiệt lên càng cao, sự tăng kích thước của hạt Pt và sự giảm độ xốp thì làm bất lợi cho hoạt động chất xúc tác tại điện cực và sự trao đổi chất. Với pin đơn lẻ DMFC được tạo ra từ màng CCM ở nhiệt độ 185 oC cho điện thế, mật độ dòng điện và mật độ công suất là cao nhất 0,625V, 162mA.cm-2, 0 25 50 75 100 125 150 175 0 5 10 15 20 25 30 M Ë t ® é c « n g s u Ê t (m W .c m -2 ) MËt ®é dßng ®iÖn (mA.cm -2 ) CCM 175 0 C CCM 185 0 C CCM 195 0 C Hình 5. Mối liên hệ giữa mật độ dòng điện – mật độ công suất 129 Tạp chí Nghiên cứu khoa học và Phát triển kinh tế Trường Đại học Tây Đô Số 01 - 2017 22,4mW.cm-2, từ kết quả đo đường đặc trưng I-V, I-P ở ba nhiệt độ khác nhau, thì ở nhiệt độ 185 oC cho hiệu suất đầu ra là khá tốt so với 175 oC, 195 oC và độ xốp là tốt nhất với đường kính trung bình độ xốp là m85,0 . TÀI LIỆU THAM KHẢO 1. A. Oliveira Neto and M. Linardi, 2007. Preparation of PtRu/C Anode Electrocatalysts using NaBH 4 as Reducing Agent and OH - ions as Stabilizing Agent, Instituto de Pesquisas Energéticas e Nucleares – IPEN/CNEN-SP, Brazil, 05508-900 São Paulo – SP. 2. Jae Hyung Cho, 2009. Fabrication and evaluation of membrane electrode assemblies by low- temperature decal methods for direct methanol fuel cells. Journal of Power Sources 187, 378–386. 3. Michael Wegener, Werner Wirges, Brigitte Tiersch, 2007. Porous polytetrafluoroethylene (PTFE) electret films: porosity and time dependent charging behavior of the free surface. J. Porous Matter 14, 111–118. 4. Peng Liu, Ge-Ping Yin, Er-Dong Wang, Jian Zhang, Zhen-Bo Wang, 2009. Influence of hot-pressing temperature on physical and electrochemical performance of catalyst coated membranes for direct methanol fuel cells., J Appl Electrochem 39, 859-866. 5. Peng Liu, , Ge-Ping Yin, , Yu-Yan Shao, 2010. High electrochemical activity of Pt/C cathode modified with NH4HCO3 for direct methanol fuel cell. J Solid State Electrochem 14, 633–636. 130 Tạp chí Nghiên cứu khoa học và Phát triển kinh tế Trường Đại học Tây Đô Số 01 - 2017 SYNTHESIZING NANO-PARTICLES PT/C, PT-RU/C AND EFFECT OF HOT- PRESSING ON BATTERY PERFORMANCE USING DMFC Nguyen Le Hoai Phuong1 and Nguyen Manh Tuan2 1Faculty of Basic Sciences, Tay Do University (Email: nlhphuong@tdu.edu.vn) 2 HCMC Academy of Science and Applied Materials ABSTRACT The objective of this study was to evaluate the effect of temperature pressing for CCM catalyst coated membrane fabrication process with decal transfer method by synthesized catalyst nano-particles in cathode and anode Pt/C, PtRu/C. By FESEM images, we observed the distribution of particles on the surface of catalyst layer in the temperature 175 °C, 185 °C and 195 °C respectively, and average porosity diameter. At temperature of 185 °C, we found the most uniform distribution and average diameter porosity at 0,85 µm. CCM membranes at 185 °C critically improved contact between the catalyst layer and membrane. This showed the output of the highest battery performance through the I-V characteristics and determining the I-P relationship, with voltage, current density and maximum power density at 0,625 V, 162 mA.cm-2, 22,4 mW.cm-2 respectively. At high temperature of 195 °C, current density and power density were reduced 0,58 V, 122 mA.cm-2, 15,2 mW.cm-2 respectively. Keywords: Direct methanol fuel cells (DMFC), catalyst coated membrane (CCM) , decal transfer method, hot-pressing 131
File đính kèm:
che_tao_hat_nano_ptc_pt_ruc_va_anh_huong_cua_qua_trinh_ep_nh.pdf