NO2 gas sensing characteristics of SNO2 nanofiber - based sensors
In this work, the SnO2 nanofibers (NFs) were directly synthesized through a electrospinning method
following the annealing treatment process at 600 °C for 3h. The morphological, compositional, crystal
properties of material were characterized using field emission scanning electron microscopy (FESEM),
energy dispersive X-ray spectroscopy (EDX), X-ray diffraction (XRD), respectively. The FESEM images of
SnO2 NFs shows the typical spider-net like morphology with ∼ 150 nm in diameter. Besides, the EDX
spectrum reveals the presence of Sn and O atoms in the synthesized nanofibers. The XRD exhibited the
formation of crystalline phases of tetragonal SnO2. The gas sensing properties of fibers were tested towards
NO2 gas as a function concentration within a temperature range of 250 to 450 °C. Under the optimal
operating temperature of 350 °C, the SnO2 NF sensors can be detected NO2 gas at low concentration down
to 0.015 ppm. These results show its ability for NO2 gas detection in gas sensor application.
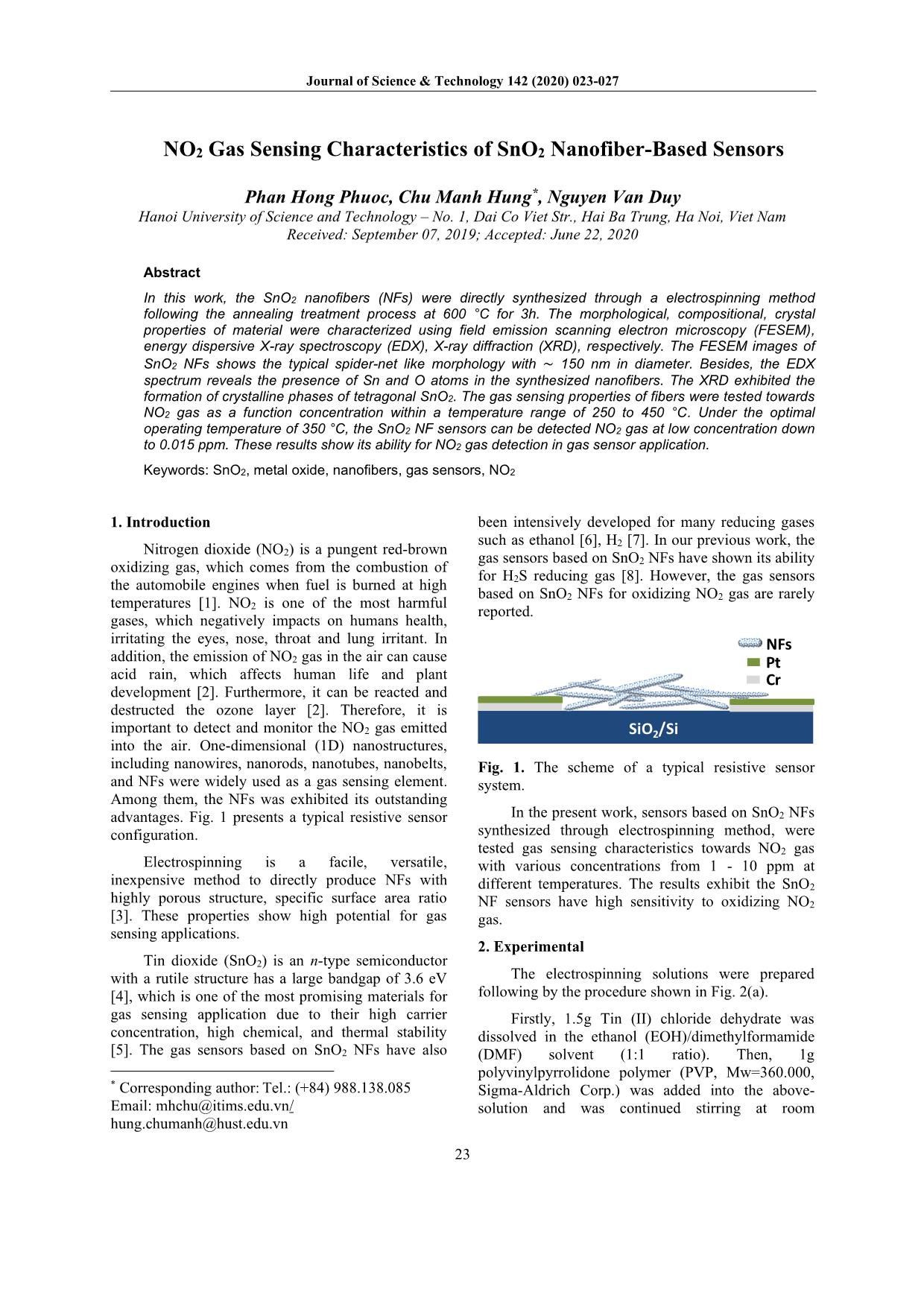
Trang 1
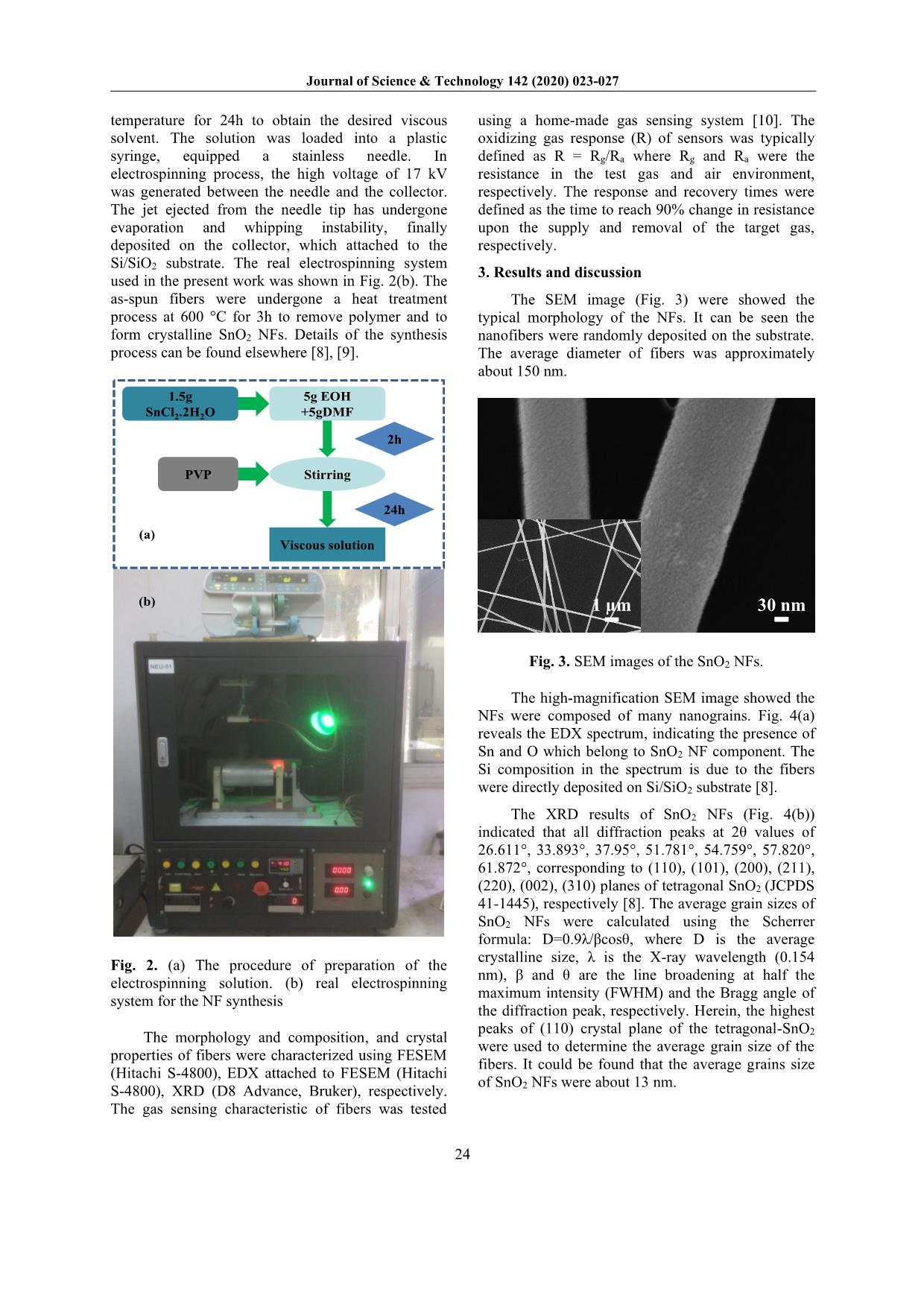
Trang 2
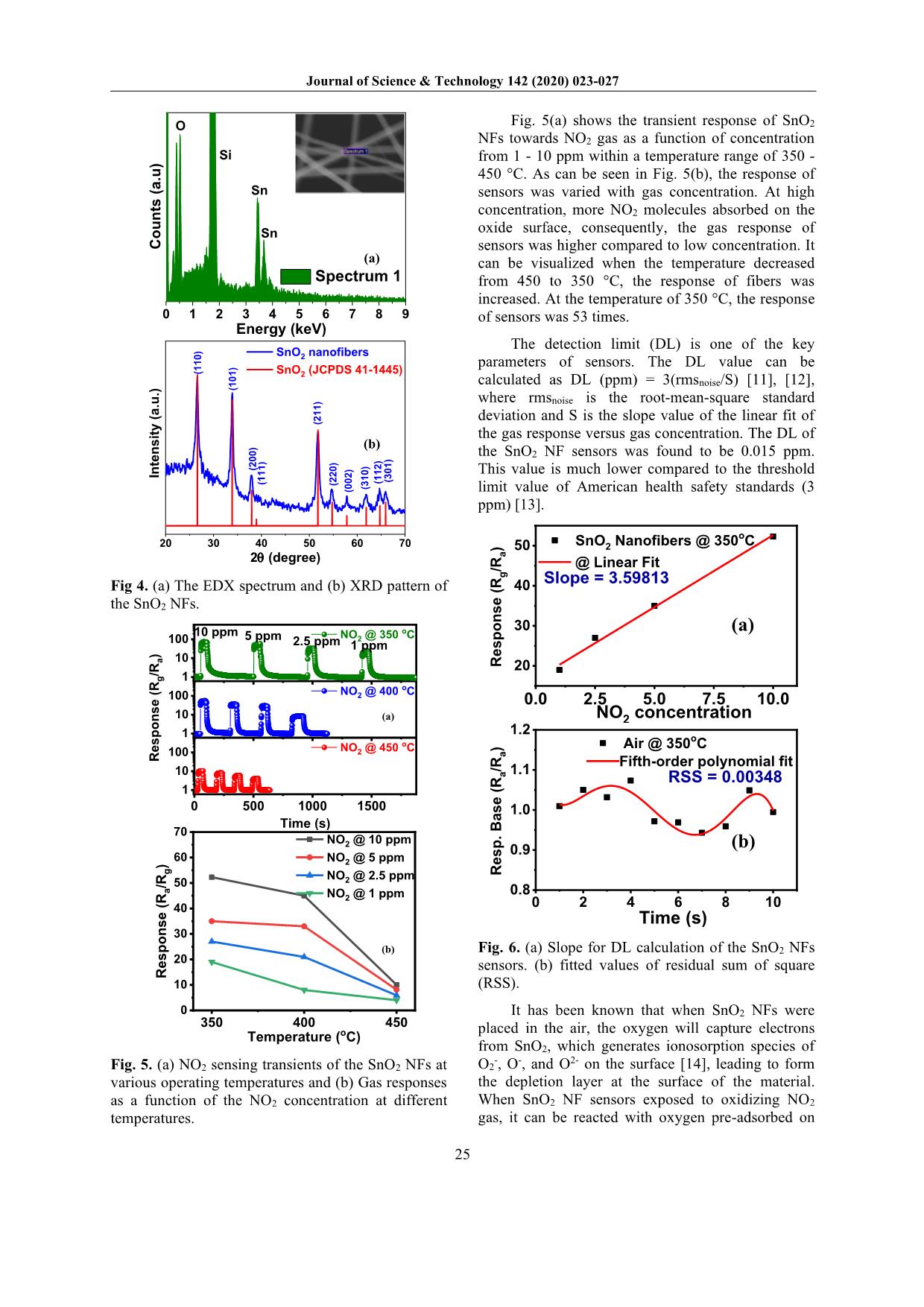
Trang 3
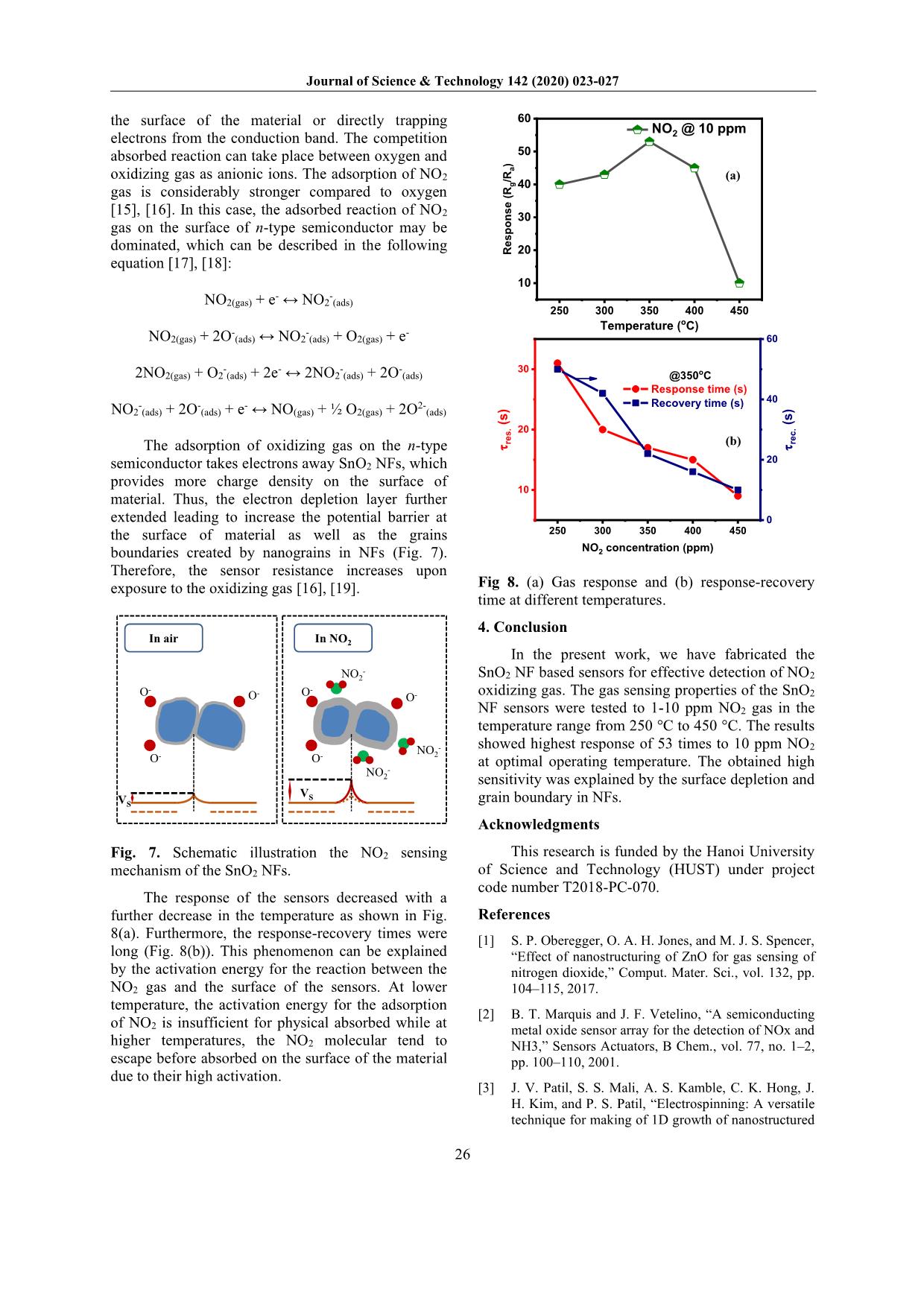
Trang 4
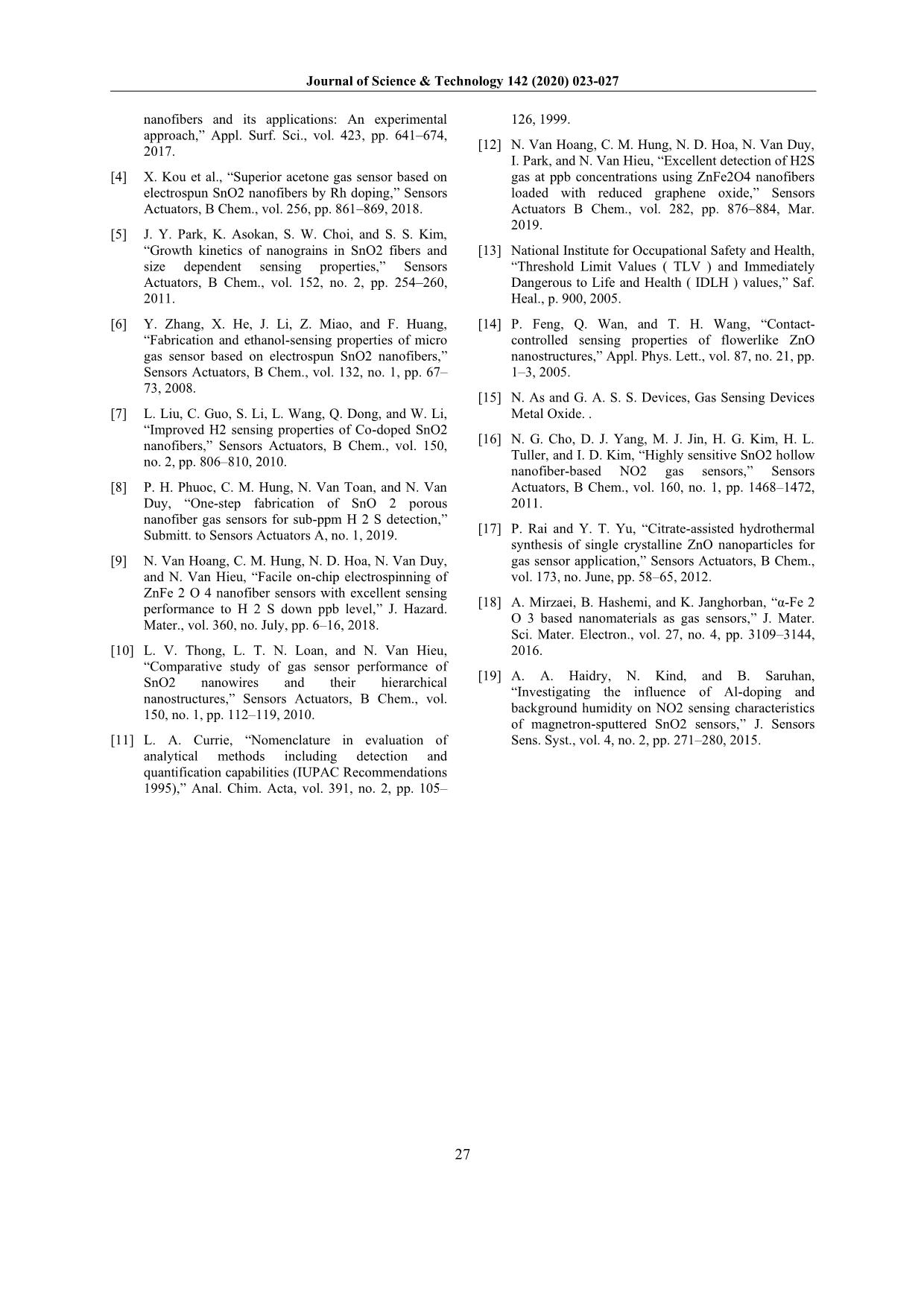
Trang 5
Tóm tắt nội dung tài liệu: NO2 gas sensing characteristics of SNO2 nanofiber - based sensors
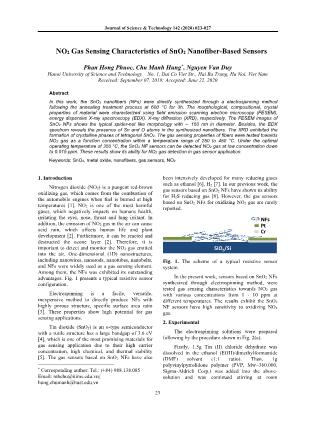
d rain, which affects human life and plant development [2]. Furthermore, it can be reacted and destructed the ozone layer [2]. Therefore, it is important to detect and monitor the NO2 gas emitted into the air. One-dimensional (1D) nanostructures, including nanowires, nanorods, nanotubes, nanobelts, and NFs were widely used as a gas sensing element. Among them, the NFs was exhibited its outstanding advantages. Fig. 1 presents a typical resistive sensor configuration. Electrospinning is a facile, versatile, inexpensive method to directly produce NFs with highly porous structure, specific surface area ratio [3]. These properties show high potential for gas sensing applications. Tin dioxide (SnO2) is an n-type semiconductor with a rutile structure has a large bandgap of 3.6 eV [4], which is one of the most promising materials for gas sensing application due to their high carrier concentration, high chemical, and thermal stability [5]. The gas sensors based on SnO2 NFs have also * Corresponding author: Tel.: (+84) 988.138.085 Email: mhchu@itims.edu.vn/ hung.chumanh@hust.edu.vn been intensively developed for many reducing gases such as ethanol [6], H2 [7]. In our previous work, the gas sensors based on SnO2 NFs have shown its ability for H2S reducing gas [8]. However, the gas sensors based on SnO2 NFs for oxidizing NO2 gas are rarely reported. SiO2/Si Cr Pt NFs Fig. 1. The scheme of a typical resistive sensor system. In the present work, sensors based on SnO2 NFs synthesized through electrospinning method, were tested gas sensing characteristics towards NO2 gas with various concentrations from 1 - 10 ppm at different temperatures. The results exhibit the SnO2 NF sensors have high sensitivity to oxidizing NO2 gas. 2. Experimental The electrospinning solutions were prepared following by the procedure shown in Fig. 2(a). Firstly, 1.5g Tin (II) chloride dehydrate was dissolved in the ethanol (EOH)/dimethylformamide (DMF) solvent (1:1 ratio). Then, 1g polyvinylpyrrolidone polymer (PVP, Mw=360.000, Sigma-Aldrich Corp.) was added into the above- solution and was continued stirring at room Journal of Science & Technology 142 (2020) 023-027 24 temperature for 24h to obtain the desired viscous solvent. The solution was loaded into a plastic syringe, equipped a stainless needle. In electrospinning process, the high voltage of 17 kV was generated between the needle and the collector. The jet ejected from the needle tip has undergone evaporation and whipping instability, finally deposited on the collector, which attached to the Si/SiO2 substrate. The real electrospinning system used in the present work was shown in Fig. 2(b). The as-spun fibers were undergone a heat treatment process at 600 °C for 3h to remove polymer and to form crystalline SnO2 NFs. Details of the synthesis process can be found elsewhere [8], [9]. Stirring 5g EOH +5gDMF Viscous solution 1.5g SnCl2.2H2O PVP 2h 24h (a) (b) Fig. 2. (a) The procedure of preparation of the electrospinning solution. (b) real electrospinning system for the NF synthesis The morphology and composition, and crystal properties of fibers were characterized using FESEM (Hitachi S-4800), EDX attached to FESEM (Hitachi S-4800), XRD (D8 Advance, Bruker), respectively. The gas sensing characteristic of fibers was tested using a home-made gas sensing system [10]. The oxidizing gas response (R) of sensors was typically defined as R = Rg/Ra where Rg and Ra were the resistance in the test gas and air environment, respectively. The response and recovery times were defined as the time to reach 90% change in resistance upon the supply and removal of the target gas, respectively. 3. Results and discussion The SEM image (Fig. 3) were showed the typical morphology of the NFs. It can be seen the nanofibers were randomly deposited on the substrate. The average diameter of fibers was approximately about 150 nm. 30 nm1 µm Fig. 3. SEM images of the SnO2 NFs. The high-magnification SEM image showed the NFs were composed of many nanograins. Fig. 4(a) reveals the EDX spectrum, indicating the presence of Sn and O which belong to SnO2 NF component. The Si composition in the spectrum is due to the fibers were directly deposited on Si/SiO2 substrate [8]. The XRD results of SnO2 NFs (Fig. 4(b)) indicated that all diffraction peaks at 2θ values of 26.611°, 33.893°, 37.95°, 51.781°, 54.759°, 57.820°, 61.872°, corresponding to (110), (101), (200), (211), (220), (002), (310) planes of tetragonal SnO2 (JCPDS 41-1445), respectively [8]. The average grain sizes of SnO2 NFs were calculated using the Scherrer formula: D=0.9λ/βcosθ, where D is the average crystalline size, λ is the X-ray wavelength (0.154 nm), β and θ are the line broadening at half the maximum intensity (FWHM) and the Bragg angle of the diffraction peak, respectively. Herein, the highest peaks of (110) crystal plane of the tetragonal-SnO2 were used to determine the average grain size of the fibers. It could be found that the average grains size of SnO2 NFs were about 13 nm. Journal of Science & Technology 142 (2020) 023-027 25 0 1 2 3 4 5 6 7 8 9 C o u n ts ( a .u ) Spectrum 1 Sn Sn Si O Energy (keV) (a) (b) 20 30 40 50 60 70 (3 0 1 ) (1 1 2 ) (1 1 1 ) In te n s it y ( a .u .) 2q (degree) SnO2 nanofibers SnO2 (JCPDS 41-1445)( 1 1 0 ) (1 0 1 ) (2 0 0 ) (2 1 1 ) (2 2 0 ) (0 0 2 ) (3 1 0 ) Fig 4. (a) The EDX spectrum and (b) XRD pattern of the SnO2 NFs. (b) (a) 0 500 1000 1500 1 10 100 1 10 100 1 10 100 Time (s) NO2 @ 450 oC NO2 @ 400 oC 2.5 ppm 1 ppm 5 ppm R e s p o n s e ( R g /R a ) NO2 @ 350 oC10 ppm 350 400 450 0 10 20 30 40 50 60 70 R e s p o n s e ( R a /R g ) Temperature (oC) NO2 @ 10 ppm NO2 @ 5 ppm NO2 @ 2.5 ppm NO2 @ 1 ppm Fig. 5. (a) NO2 sensing transients of the SnO2 NFs at various operating temperatures and (b) Gas responses as a function of the NO2 concentration at different temperatures. Fig. 5(a) shows the transient response of SnO2 NFs towards NO2 gas as a function of concentration from 1 - 10 ppm within a temperature range of 350 - 450 °C. As can be seen in Fig. 5(b), the response of sensors was varied with gas concentration. At high concentration, more NO2 molecules absorbed on the oxide surface, consequently, the gas response of sensors was higher compared to low concentration. It can be visualized when the temperature decreased from 450 to 350 °C, the response of fibers was increased. At the temperature of 350 °C, the response of sensors was 53 times. The detection limit (DL) is one of the key parameters of sensors. The DL value can be calculated as DL (ppm) = 3(rmsnoise/S) [11], [12], where rmsnoise is the root-mean-square standard deviation and S is the slope value of the linear fit of the gas response versus gas concentration. The DL of the SnO2 NF sensors was found to be 0.015 ppm. This value is much lower compared to the threshold limit value of American health safety standards (3 ppm) [13]. (a) (b) 0.0 2.5 5.0 7.5 10.0 20 30 40 50 Slope = 3.59813 R e s p o n s e ( R g /R a ) SnO2 Nanofibers @ 350 oC @ Linear Fit NO2 concentration 0 2 4 6 8 10 0.8 0.9 1.0 1.1 1.2 RSS = 0.00348 R e s p . B a s e ( R a /R a ) Air @ 350oC Fifth-order polynomial fit Time (s) Fig. 6. (a) Slope for DL calculation of the SnO2 NFs sensors. (b) fitted values of residual sum of square (RSS). It has been known that when SnO2 NFs were placed in the air, the oxygen will capture electrons from SnO2, which generates ionosorption species of O2-, O-, and O2- on the surface [14], leading to form the depletion layer at the surface of the material. When SnO2 NF sensors exposed to oxidizing NO2 gas, it can be reacted with oxygen pre-adsorbed on Journal of Science & Technology 142 (2020) 023-027 26 the surface of the material or directly trapping electrons from the conduction band. The competition absorbed reaction can take place between oxygen and oxidizing gas as anionic ions. The adsorption of NO2 gas is considerably stronger compared to oxygen [15], [16]. In this case, the adsorbed reaction of NO2 gas on the surface of n-type semiconductor may be dominated, which can be described in the following equation [17], [18]: NO2(gas) + e- ↔ NO2-(ads) NO2(gas) + 2O-(ads) ↔ NO2-(ads) + O2(gas) + e- 2NO2(gas) + O2-(ads) + 2e- ↔ 2NO2-(ads) + 2O-(ads) NO2-(ads) + 2O-(ads) + e- ↔ NO(gas) + ½ O2(gas) + 2O2-(ads) The adsorption of oxidizing gas on the n-type semiconductor takes electrons away SnO2 NFs, which provides more charge density on the surface of material. Thus, the electron depletion layer further extended leading to increase the potential barrier at the surface of material as well as the grains boundaries created by nanograins in NFs (Fig. 7). Therefore, the sensor resistance increases upon exposure to the oxidizing gas [16], [19]. In air O- O-O - In NO2 O- O- O- NO2 - NO2 - NO2 - VSVS Fig. 7. Schematic illustration the NO2 sensing mechanism of the SnO2 NFs. The response of the sensors decreased with a further decrease in the temperature as shown in Fig. 8(a). Furthermore, the response-recovery times were long (Fig. 8(b)). This phenomenon can be explained by the activation energy for the reaction between the NO2 gas and the surface of the sensors. At lower temperature, the activation energy for the adsorption of NO2 is insufficient for physical absorbed while at higher temperatures, the NO2 molecular tend to escape before absorbed on the surface of the material due to their high activation. (a) (b) 250 300 350 400 450 10 20 30 Response time (s) Recovery time (s) NO2 concentration (ppm) t r e s . ( s ) @350oC 0 20 40 60 t r e c . ( s ) 250 300 350 400 450 10 20 30 40 50 60 R e s p o n s e ( R g /R a ) NO2 @ 10 ppm Temperature (oC) Fig 8. (a) Gas response and (b) response-recovery time at different temperatures. 4. Conclusion In the present work, we have fabricated the SnO2 NF based sensors for effective detection of NO2 oxidizing gas. The gas sensing properties of the SnO2 NF sensors were tested to 1-10 ppm NO2 gas in the temperature range from 250 °C to 450 °C. The results showed highest response of 53 times to 10 ppm NO2 at optimal operating temperature. The obtained high sensitivity was explained by the surface depletion and grain boundary in NFs. Acknowledgments This research is funded by the Hanoi University of Science and Technology (HUST) under project code number T2018-PC-070. References [1] S. P. Oberegger, O. A. H. Jones, and M. J. S. Spencer, “Effect of nanostructuring of ZnO for gas sensing of nitrogen dioxide,” Comput. Mater. Sci., vol. 132, pp. 104–115, 2017. [2] B. T. Marquis and J. F. Vetelino, “A semiconducting metal oxide sensor array for the detection of NOx and NH3,” Sensors Actuators, B Chem., vol. 77, no. 1–2, pp. 100–110, 2001. [3] J. V. Patil, S. S. Mali, A. S. Kamble, C. K. Hong, J. H. Kim, and P. S. Patil, “Electrospinning: A versatile technique for making of 1D growth of nanostructured Journal of Science & Technology 142 (2020) 023-027 27 nanofibers and its applications: An experimental approach,” Appl. Surf. Sci., vol. 423, pp. 641–674, 2017. [4] X. Kou et al., “Superior acetone gas sensor based on electrospun SnO2 nanofibers by Rh doping,” Sensors Actuators, B Chem., vol. 256, pp. 861–869, 2018. [5] J. Y. Park, K. Asokan, S. W. Choi, and S. S. Kim, “Growth kinetics of nanograins in SnO2 fibers and size dependent sensing properties,” Sensors Actuators, B Chem., vol. 152, no. 2, pp. 254–260, 2011. [6] Y. Zhang, X. He, J. Li, Z. Miao, and F. Huang, “Fabrication and ethanol-sensing properties of micro gas sensor based on electrospun SnO2 nanofibers,” Sensors Actuators, B Chem., vol. 132, no. 1, pp. 67– 73, 2008. [7] L. Liu, C. Guo, S. Li, L. Wang, Q. Dong, and W. Li, “Improved H2 sensing properties of Co-doped SnO2 nanofibers,” Sensors Actuators, B Chem., vol. 150, no. 2, pp. 806–810, 2010. [8] P. H. Phuoc, C. M. Hung, N. Van Toan, and N. Van Duy, “One-step fabrication of SnO 2 porous nanofiber gas sensors for sub-ppm H 2 S detection,” Submitt. to Sensors Actuators A, no. 1, 2019. [9] N. Van Hoang, C. M. Hung, N. D. Hoa, N. Van Duy, and N. Van Hieu, “Facile on-chip electrospinning of ZnFe 2 O 4 nanofiber sensors with excellent sensing performance to H 2 S down ppb level,” J. Hazard. Mater., vol. 360, no. July, pp. 6–16, 2018. [10] L. V. Thong, L. T. N. Loan, and N. Van Hieu, “Comparative study of gas sensor performance of SnO2 nanowires and their hierarchical nanostructures,” Sensors Actuators, B Chem., vol. 150, no. 1, pp. 112–119, 2010. [11] L. A. Currie, “Nomenclature in evaluation of analytical methods including detection and quantification capabilities (IUPAC Recommendations 1995),” Anal. Chim. Acta, vol. 391, no. 2, pp. 105– 126, 1999. [12] N. Van Hoang, C. M. Hung, N. D. Hoa, N. Van Duy, I. Park, and N. Van Hieu, “Excellent detection of H2S gas at ppb concentrations using ZnFe2O4 nanofibers loaded with reduced graphene oxide,” Sensors Actuators B Chem., vol. 282, pp. 876–884, Mar. 2019. [13] National Institute for Occupational Safety and Health, “Threshold Limit Values ( TLV ) and Immediately Dangerous to Life and Health ( IDLH ) values,” Saf. Heal., p. 900, 2005. [14] P. Feng, Q. Wan, and T. H. Wang, “Contact- controlled sensing properties of flowerlike ZnO nanostructures,” Appl. Phys. Lett., vol. 87, no. 21, pp. 1–3, 2005. [15] N. As and G. A. S. S. Devices, Gas Sensing Devices Metal Oxide. . [16] N. G. Cho, D. J. Yang, M. J. Jin, H. G. Kim, H. L. Tuller, and I. D. Kim, “Highly sensitive SnO2 hollow nanofiber-based NO2 gas sensors,” Sensors Actuators, B Chem., vol. 160, no. 1, pp. 1468–1472, 2011. [17] P. Rai and Y. T. Yu, “Citrate-assisted hydrothermal synthesis of single crystalline ZnO nanoparticles for gas sensor application,” Sensors Actuators, B Chem., vol. 173, no. June, pp. 58–65, 2012. [18] A. Mirzaei, B. Hashemi, and K. Janghorban, “α-Fe 2 O 3 based nanomaterials as gas sensors,” J. Mater. Sci. Mater. Electron., vol. 27, no. 4, pp. 3109–3144, 2016. [19] A. A. Haidry, N. Kind, and B. Saruhan, “Investigating the influence of Al-doping and background humidity on NO2 sensing characteristics of magnetron-sputtered SnO2 sensors,” J. Sensors Sens. Syst., vol. 4, no. 2, pp. 271–280, 2015.
File đính kèm:
no2_gas_sensing_characteristics_of_sno2_nanofiber_based_sens.pdf