Mô phỏng nhiệt, so sánh cấu trúc làm mát động cơ servo không đồng bộ
Bài báo nghiên cứu mô phỏng nhiệt và so sánh các cấu trúc làm mát khác
nhau của động cơ servo không đồng bộ. Với ưu điểm tốc độ tính toán gần như tức thời,
quá trình thiết kế nhanh chóng phân tích được các thay đổi nhiệt trong động cơ, phần
mềm Motor-CAD được sử dụng để lựa chọn các thông số liên quan quá trình phát nhiệt
khi thiết kế tối ưu động cơ. Việc áp dụng mô phỏng nhiệt-điện từ trong quá trình thiết kế,
giúp giảm yêu cầu về việc sản xuất nguyên mẫu và thử nghiệm, vì vậy, giảm thời gian
nghiên cứu chế tạo sản xuất và chi phí. Dựa trên các kết quả phân tích nhiệt và giới hạn
ngưỡng nhiệt độ của các thành phần trong động cơ, bài báo hướng đến hai mục đích: xem
xét tối ưu các thông số động cơ và lựa chọn phương thức, cấu trúc làm mát để động cơ
thiết kế tối thiểu hóa khối lượng hay giá thành sản xuất, trong khi vẫn tăng momen cực đại
của động cơ servo.
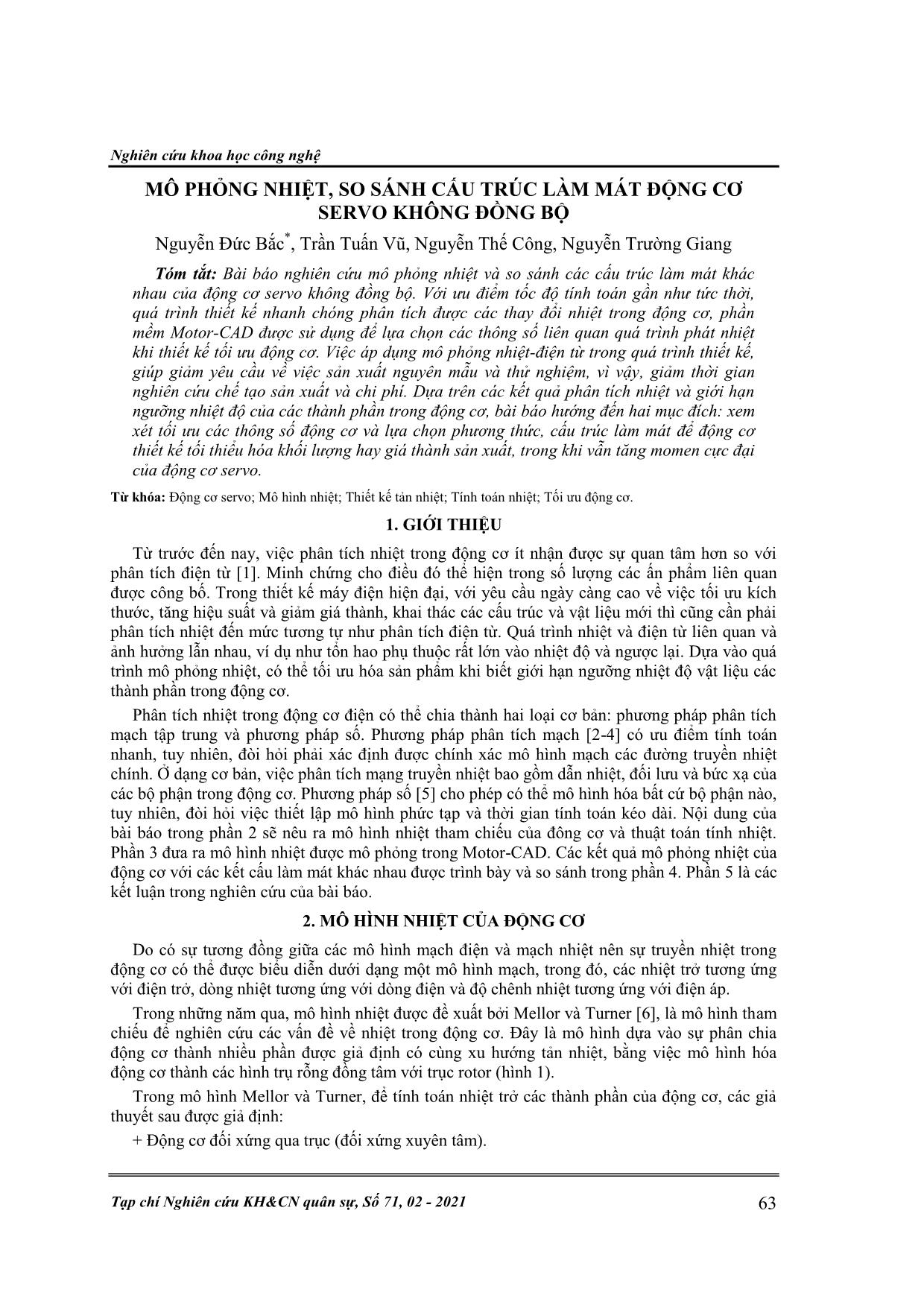
Trang 1
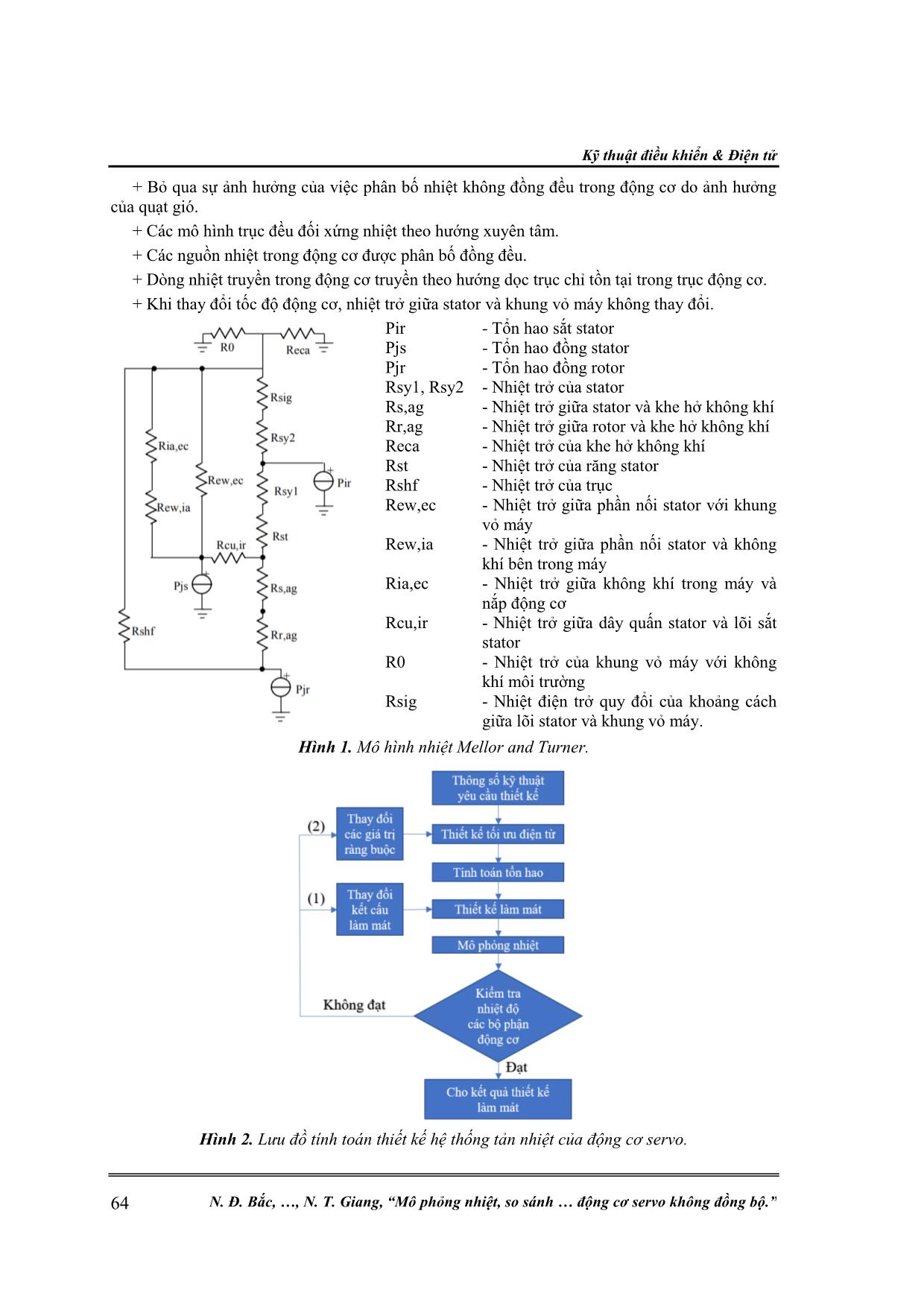
Trang 2
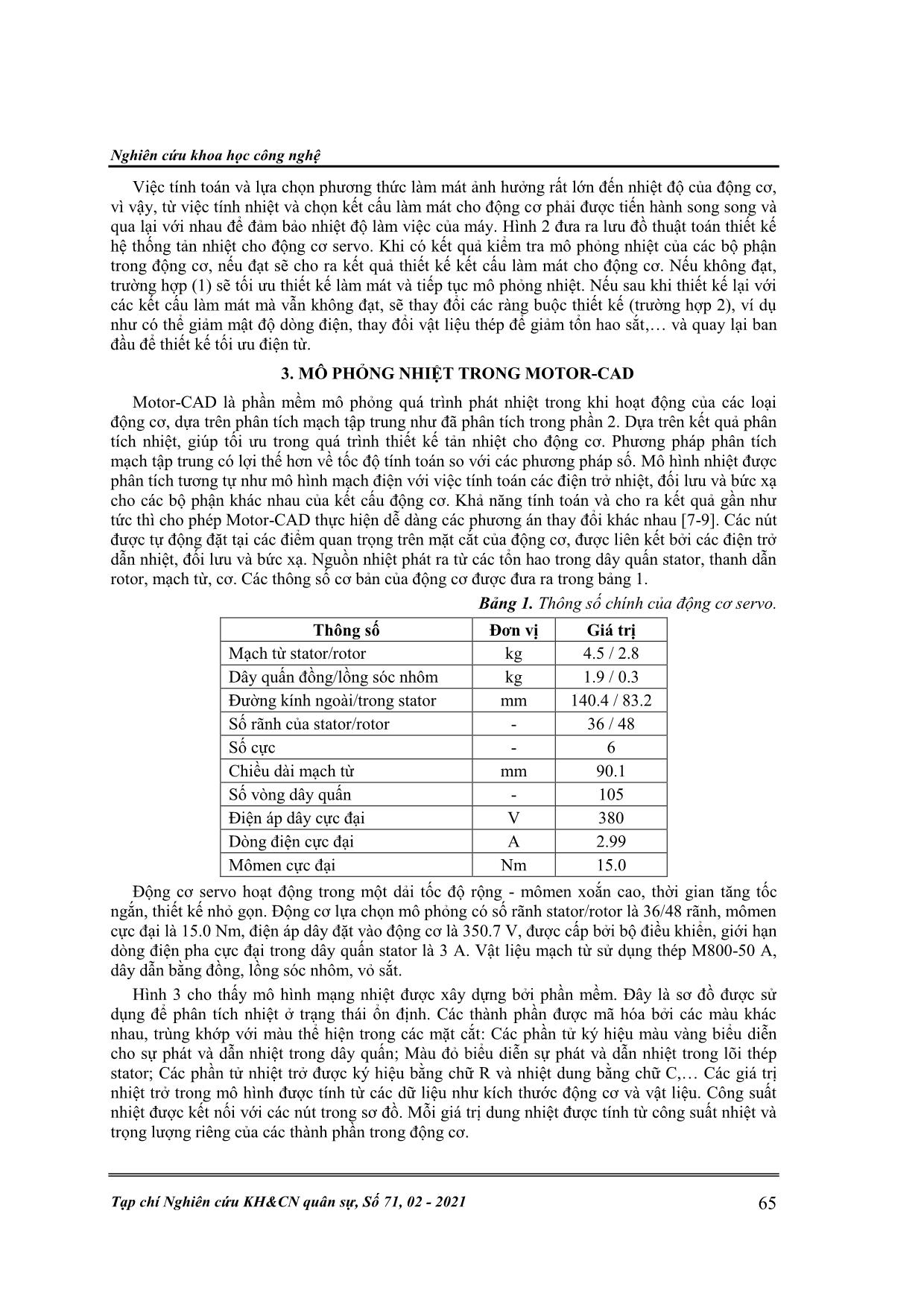
Trang 3
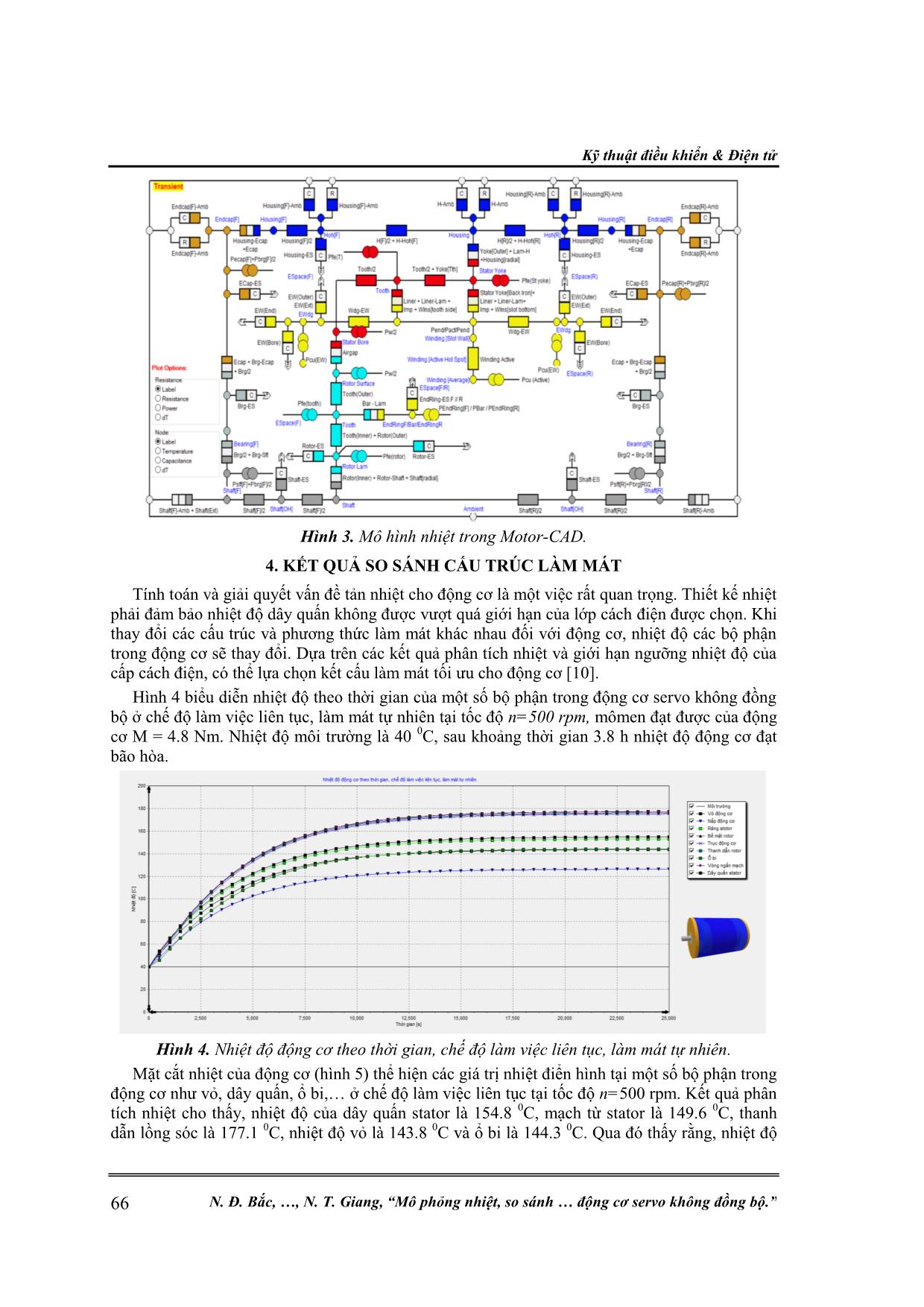
Trang 4
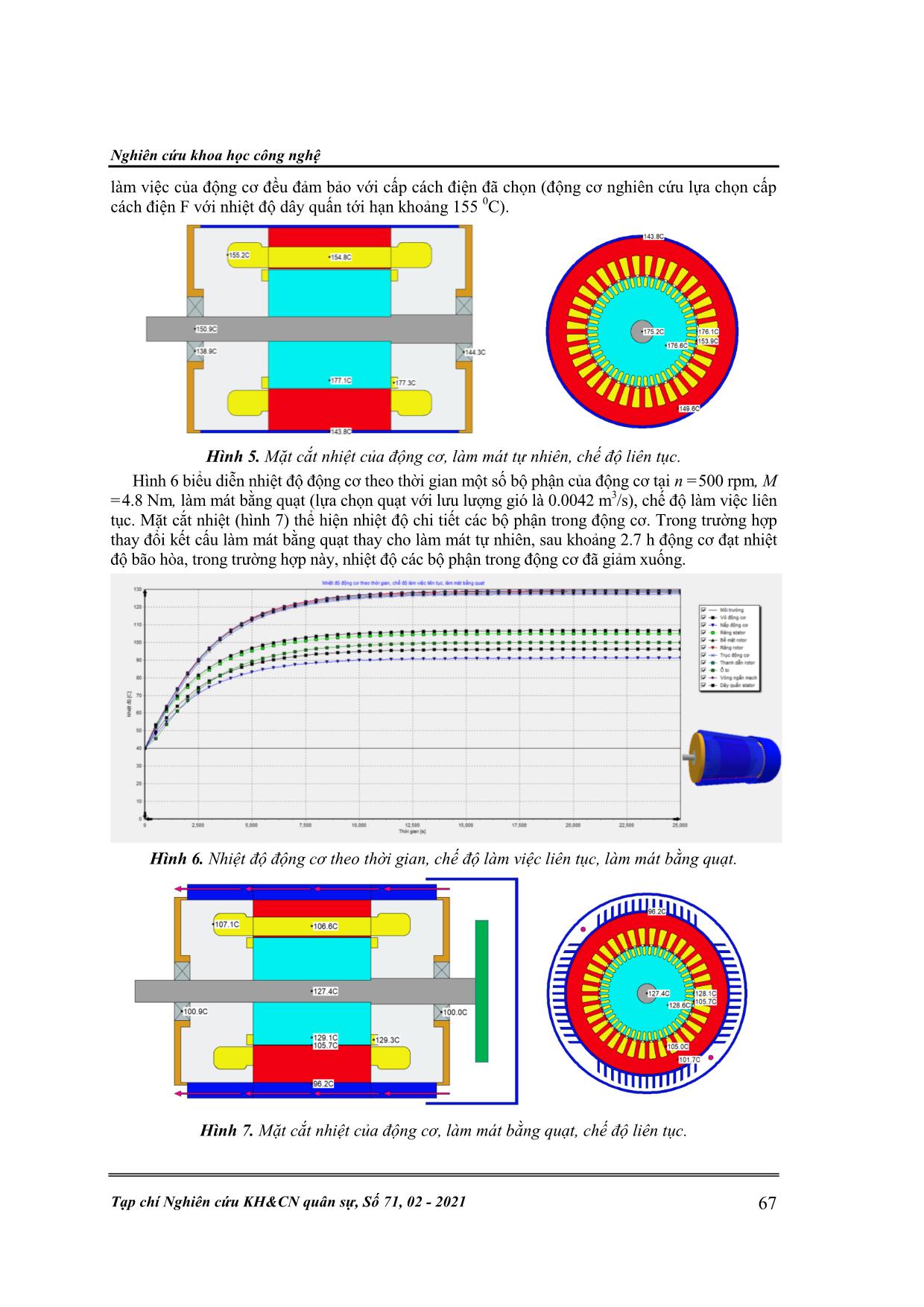
Trang 5
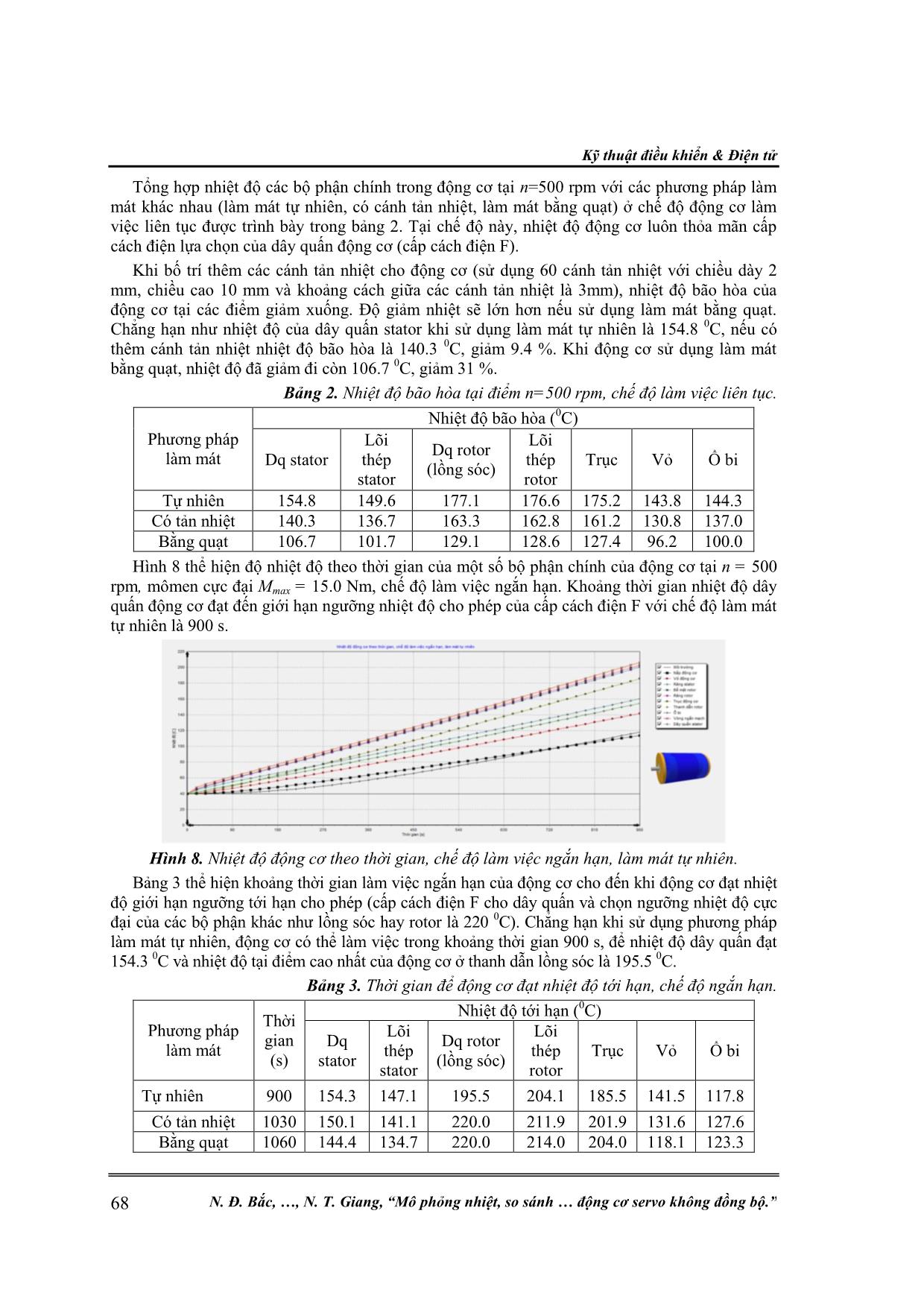
Trang 6
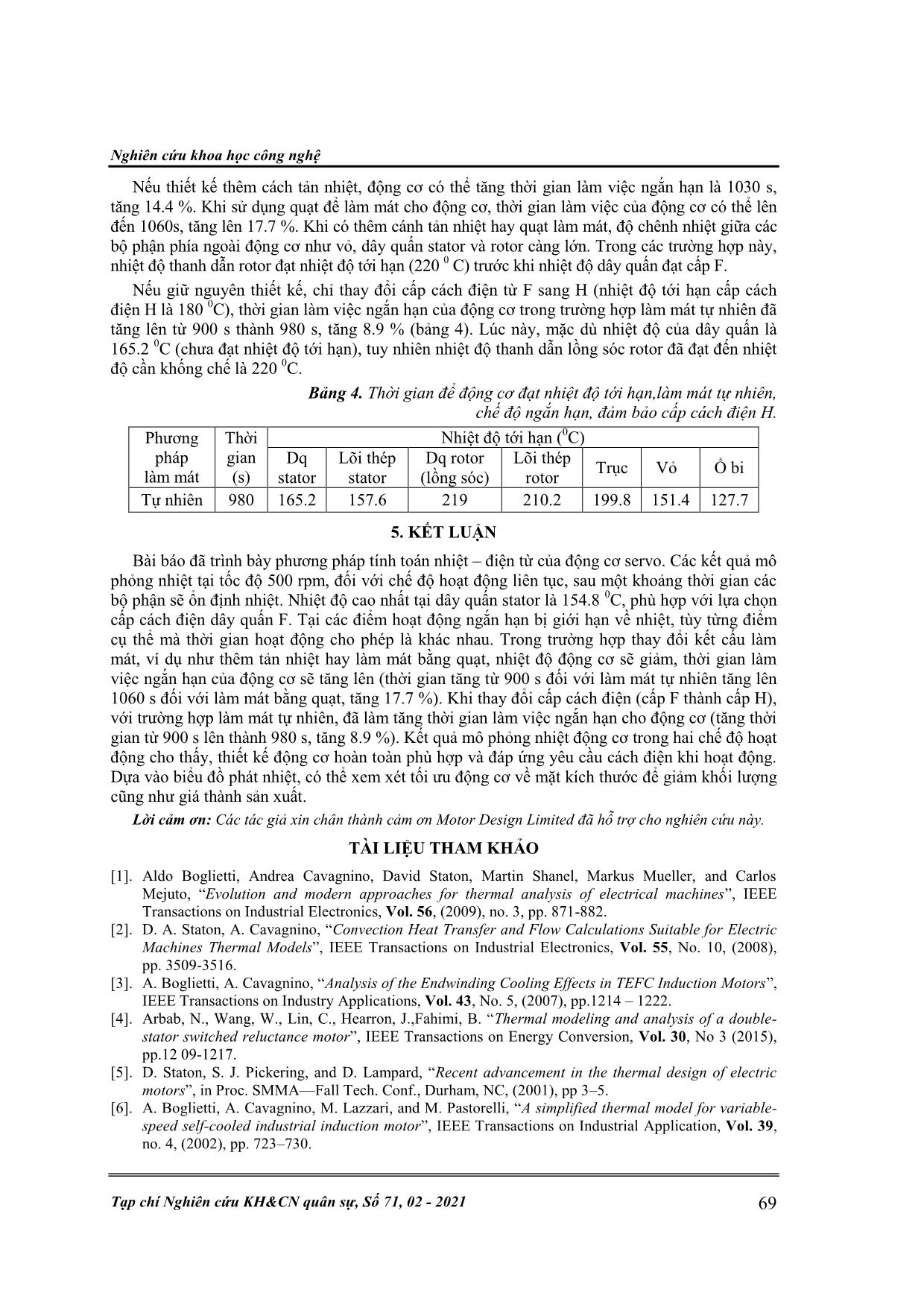
Trang 7
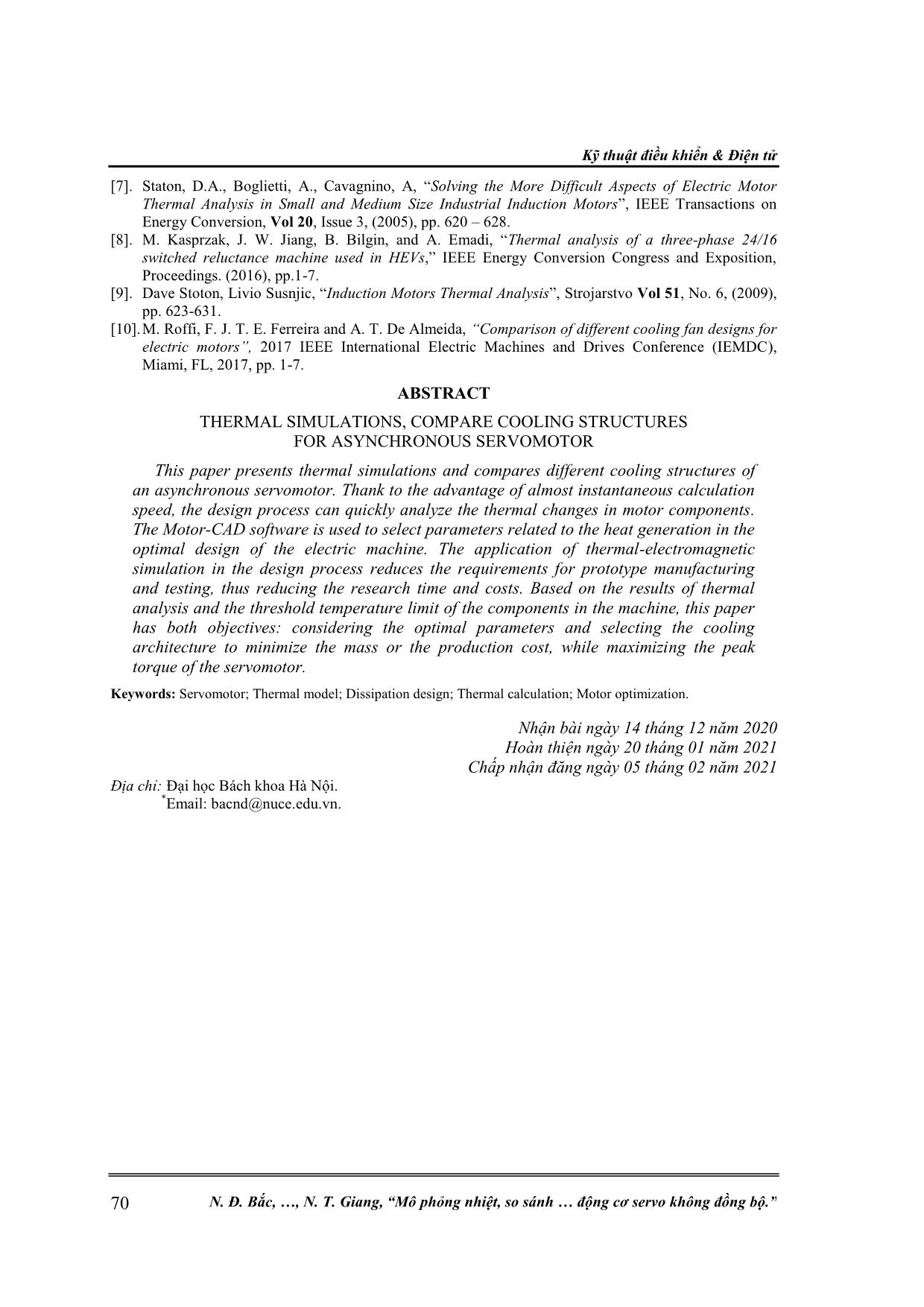
Trang 8
Tóm tắt nội dung tài liệu: Mô phỏng nhiệt, so sánh cấu trúc làm mát động cơ servo không đồng bộ
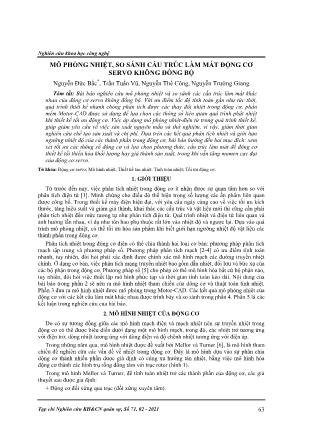
khí trong máy và nắp động cơ Rcu,ir - Nhiệt trở giữa dây quấn stator và lõi sắt stator R0 - Nhiệt trở của khung vỏ máy với không khí môi trường Rsig - Nhiệt điện trở quy đổi của khoảng cách giữa lõi stator và khung vỏ máy. Hình 1. Mô hình nhiệt Mellor and Turner. Hình 2. Lưu đồ tính toán thiết kế hệ thống tản nhiệt của động cơ servo. Nghiên cứu khoa học công nghệ Tạp chí Nghiên cứu KH&CN quân sự, Số 71, 02 - 2021 65 Việc tính toán và lựa chọn phương thức làm mát ảnh hưởng rất lớn đến nhiệt độ của động cơ, vì vậy, từ việc tính nhiệt và chọn kết cấu làm mát cho động cơ phải được tiến hành song song và qua lại với nhau để đảm bảo nhiệt độ làm việc của máy. Hình 2 đưa ra lưu đồ thuật toán thiết kế hệ thống tản nhiệt cho động cơ servo. Khi có kết quả kiểm tra mô phỏng nhiệt của các bộ phận trong động cơ, nếu đạt sẽ cho ra kết quả thiết kế kết cấu làm mát cho động cơ. Nếu không đạt, trường hợp (1) sẽ tối ưu thiết kế làm mát và tiếp tục mô phỏng nhiệt. Nếu sau khi thiết kế lại với các kết cấu làm mát mà vẫn không đạt, sẽ thay đổi các ràng buộc thiết kế (trường hợp 2), ví dụ như có thể giảm mật độ dòng điện, thay đổi vật liệu thép để giảm tổn hao sắt, và quay lại ban đầu để thiết kế tối ưu điện từ. 3. MÔ PHỎNG NHIỆT TRONG MOTOR-CAD Motor-CAD là phần mềm mô phỏng quá trình phát nhiệt trong khi hoạt động của các loại động cơ, dựa trên phân tích mạch tập trung như đã phân tích trong phần 2. Dựa trên kết quả phân tích nhiệt, giúp tối ưu trong quá trình thiết kế tản nhiệt cho động cơ. Phương pháp phân tích mạch tập trung có lợi thế hơn về tốc độ tính toán so với các phương pháp số. Mô hình nhiệt được phân tích tương tự như mô hình mạch điện với việc tính toán các điện trở nhiệt, đối lưu và bức xạ cho các bộ phận khác nhau của kết cấu động cơ. Khả năng tính toán và cho ra kết quả gần như tức thì cho phép Motor-CAD thực hiện dễ dàng các phương án thay đổi khác nhau [7-9]. Các nút được tự động đặt tại các điểm quan trọng trên mặt cắt của động cơ, được liên kết bởi các điện trở dẫn nhiệt, đối lưu và bức xạ. Nguồn nhiệt phát ra từ các tổn hao trong dây quấn stator, thanh dẫn rotor, mạch từ, cơ. Các thông số cơ bản của động cơ được đưa ra trong bảng 1. Bảng 1. Thông số chính của động cơ servo. Thông số Đơn vị Giá trị Mạch từ stator/rotor kg 4.5 / 2.8 Dây quấn đồng/lồng sóc nhôm kg 1.9 / 0.3 Đường kính ngoài/trong stator mm 140.4 / 83.2 Số rãnh của stator/rotor - 36 / 48 Số cực - 6 Chiều dài mạch từ mm 90.1 Số vòng dây quấn - 105 Điện áp dây cực đại V 380 Dòng điện cực đại A 2.99 Mômen cực đại Nm 15.0 Động cơ servo hoạt động trong một dải tốc độ rộng - mômen xoắn cao, thời gian tăng tốc ngắn, thiết kế nhỏ gọn. Động cơ lựa chọn mô phỏng có số rãnh stator/rotor là 36/48 rãnh, mômen cực đại là 15.0 Nm, điện áp dây đặt vào động cơ là 350.7 V, được cấp bởi bộ điều khiển, giới hạn dòng điện pha cực đại trong dây quấn stator là 3 A. Vật liệu mạch từ sử dụng thép M800-50 A, dây dẫn bằng đồng, lồng sóc nhôm, vỏ sắt. Hình 3 cho thấy mô hình mạng nhiệt được xây dựng bởi phần mềm. Đây là sơ đồ được sử dụng để phân tích nhiệt ở trạng thái ổn định. Các thành phần được mã hóa bởi các màu khác nhau, trùng khớp với màu thể hiện trong các mặt cắt: Các phần tử ký hiệu màu vàng biểu diễn cho sự phát và dẫn nhiệt trong dây quấn; Màu đỏ biểu diễn sự phát và dẫn nhiệt trong lõi thép stator; Các phần tử nhiệt trở được ký hiệu bằng chữ R và nhiệt dung bằng chữ C, Các giá trị nhiệt trở trong mô hình được tính từ các dữ liệu như kích thước động cơ và vật liệu. Công suất nhiệt được kết nối với các nút trong sơ đồ. Mỗi giá trị dung nhiệt được tính từ công suất nhiệt và trọng lượng riêng của các thành phần trong động cơ. Kỹ thuật điều khiển & Điện tử 66 N. Đ. Bắc, , N. T. Giang, “Mô phỏng nhiệt, so sánh động cơ servo không đồng bộ.” Hình 3. Mô hình nhiệt trong Motor-CAD. 4. KẾT QUẢ SO SÁNH CẤU TRÚC LÀM MÁT Tính toán và giải quyết vấn đề tản nhiệt cho động cơ là một việc rất quan trọng. Thiết kế nhiệt phải đảm bảo nhiệt độ dây quấn không được vượt quá giới hạn của lớp cách điện được chọn. Khi thay đổi các cấu trúc và phương thức làm mát khác nhau đối với động cơ, nhiệt độ các bộ phận trong động cơ sẽ thay đổi. Dựa trên các kết quả phân tích nhiệt và giới hạn ngưỡng nhiệt độ của cấp cách điện, có thể lựa chọn kết cấu làm mát tối ưu cho động cơ [10]. Hình 4 biểu diễn nhiệt độ theo thời gian của một số bộ phận trong động cơ servo không đồng bộ ở chế độ làm việc liên tục, làm mát tự nhiên tại tốc độ n=500 rpm, mômen đạt được của động cơ M = 4.8 Nm. Nhiệt độ môi trường là 40 0C, sau khoảng thời gian 3.8 h nhiệt độ động cơ đạt bão hòa. Hình 4. Nhiệt độ động cơ theo thời gian, chế độ làm việc liên tục, làm mát tự nhiên. Mặt cắt nhiệt của động cơ (hình 5) thể hiện các giá trị nhiệt điển hình tại một số bộ phận trong động cơ như vỏ, dây quấn, ổ bi, ở chế độ làm việc liên tục tại tốc độ n=500 rpm. Kết quả phân tích nhiệt cho thấy, nhiệt độ của dây quấn stator là 154.8 0C, mạch từ stator là 149.6 0C, thanh dẫn lồng sóc là 177.1 0C, nhiệt độ vỏ là 143.8 0C và ổ bi là 144.3 0C. Qua đó thấy rằng, nhiệt độ Nghiên cứu khoa học công nghệ Tạp chí Nghiên cứu KH&CN quân sự, Số 71, 02 - 2021 67 làm việc của động cơ đều đảm bảo với cấp cách điện đã chọn (động cơ nghiên cứu lựa chọn cấp cách điện F với nhiệt độ dây quấn tới hạn khoảng 155 0C). Hình 5. Mặt cắt nhiệt của động cơ, làm mát tự nhiên, chế độ liên tục. Hình 6 biểu diễn nhiệt độ động cơ theo thời gian một số bộ phận của động cơ tại n =500 rpm, M =4.8 Nm, làm mát bằng quạt (lựa chọn quạt với lưu lượng gió là 0.0042 m3/s), chế độ làm việc liên tục. Mặt cắt nhiệt (hình 7) thể hiện nhiệt độ chi tiết các bộ phận trong động cơ. Trong trường hợp thay đổi kết cấu làm mát bằng quạt thay cho làm mát tự nhiên, sau khoảng 2.7 h động cơ đạt nhiệt độ bão hòa, trong trường hợp này, nhiệt độ các bộ phận trong động cơ đã giảm xuống. Hình 6. Nhiệt độ động cơ theo thời gian, chế độ làm việc liên tục, làm mát bằng quạt. Hình 7. Mặt cắt nhiệt của động cơ, làm mát bằng quạt, chế độ liên tục. Kỹ thuật điều khiển & Điện tử 68 N. Đ. Bắc, , N. T. Giang, “Mô phỏng nhiệt, so sánh động cơ servo không đồng bộ.” Tổng hợp nhiệt độ các bộ phận chính trong động cơ tại n=500 rpm với các phương pháp làm mát khác nhau (làm mát tự nhiên, có cánh tản nhiệt, làm mát bằng quạt) ở chế độ động cơ làm việc liên tục được trình bày trong bảng 2. Tại chế độ này, nhiệt độ động cơ luôn thỏa mãn cấp cách điện lựa chọn của dây quấn động cơ (cấp cách điện F). Khi bố trí thêm các cánh tản nhiệt cho động cơ (sử dụng 60 cánh tản nhiệt với chiều dày 2 mm, chiều cao 10 mm và khoảng cách giữa các cánh tản nhiệt là 3mm), nhiệt độ bão hòa của động cơ tại các điểm giảm xuống. Độ giảm nhiệt sẽ lớn hơn nếu sử dụng làm mát bằng quạt. Chẳng hạn như nhiệt độ của dây quấn stator khi sử dụng làm mát tự nhiên là 154.8 0C, nếu có thêm cánh tản nhiệt nhiệt độ bão hòa là 140.3 0C, giảm 9.4 %. Khi động cơ sử dụng làm mát bằng quạt, nhiệt độ đã giảm đi còn 106.7 0C, giảm 31 %. Bảng 2. Nhiệt độ bão hòa tại điểm n=500 rpm, chế độ làm việc liên tục. Phương pháp làm mát Nhiệt độ bão hòa (0C) Dq stator Lõi thép stator Dq rotor (lồng sóc) Lõi thép rotor Trục Vỏ Ổ bi Tự nhiên 154.8 149.6 177.1 176.6 175.2 143.8 144.3 Có tản nhiệt 140.3 136.7 163.3 162.8 161.2 130.8 137.0 Bằng quạt 106.7 101.7 129.1 128.6 127.4 96.2 100.0 Hình 8 thể hiện độ nhiệt độ theo thời gian của một số bộ phận chính của động cơ tại n = 500 rpm, mômen cực đại Mmax = 15.0 Nm, chế độ làm việc ngắn hạn. Khoảng thời gian nhiệt độ dây quấn động cơ đạt đến giới hạn ngưỡng nhiệt độ cho phép của cấp cách điện F với chế độ làm mát tự nhiên là 900 s. Hình 8. Nhiệt độ động cơ theo thời gian, chế độ làm việc ngắn hạn, làm mát tự nhiên. Bảng 3 thể hiện khoảng thời gian làm việc ngắn hạn của động cơ cho đến khi động cơ đạt nhiệt độ giới hạn ngưỡng tới hạn cho phép (cấp cách điện F cho dây quấn và chọn ngưỡng nhiệt độ cực đại của các bộ phận khác như lồng sóc hay rotor là 220 0C). Chẳng hạn khi sử dụng phương pháp làm mát tự nhiên, động cơ có thể làm việc trong khoảng thời gian 900 s, để nhiệt độ dây quấn đạt 154.3 0 C và nhiệt độ tại điểm cao nhất của động cơ ở thanh dẫn lồng sóc là 195.5 0C. Bảng 3. Thời gian để động cơ đạt nhiệt độ tới hạn, chế độ ngắn hạn. Phương pháp làm mát Thời gian (s) Nhiệt độ tới hạn (0C) Dq stator Lõi thép stator Dq rotor (lồng sóc) Lõi thép rotor Trục Vỏ Ổ bi Tự nhiên 900 154.3 147.1 195.5 204.1 185.5 141.5 117.8 Có tản nhiệt 1030 150.1 141.1 220.0 211.9 201.9 131.6 127.6 Bằng quạt 1060 144.4 134.7 220.0 214.0 204.0 118.1 123.3 Nghiên cứu khoa học công nghệ Tạp chí Nghiên cứu KH&CN quân sự, Số 71, 02 - 2021 69 Nếu thiết kế thêm cách tản nhiệt, động cơ có thể tăng thời gian làm việc ngắn hạn là 1030 s, tăng 14.4 %. Khi sử dụng quạt để làm mát cho động cơ, thời gian làm việc của động cơ có thể lên đến 1060s, tăng lên 17.7 %. Khi có thêm cánh tản nhiệt hay quạt làm mát, độ chênh nhiệt giữa các bộ phận phía ngoài động cơ như vỏ, dây quấn stator và rotor càng lớn. Trong các trường hợp này, nhiệt độ thanh dẫn rotor đạt nhiệt độ tới hạn (220 0 C) trước khi nhiệt độ dây quấn đạt cấp F. Nếu giữ nguyên thiết kế, chỉ thay đổi cấp cách điện từ F sang H (nhiệt độ tới hạn cấp cách điện H là 180 0C), thời gian làm việc ngắn hạn của động cơ trong trường hợp làm mát tự nhiên đã tăng lên từ 900 s thành 980 s, tăng 8.9 % (bảng 4). Lúc này, mặc dù nhiệt độ của dây quấn là 165.2 0C (chưa đạt nhiệt độ tới hạn), tuy nhiên nhiệt độ thanh dẫn lồng sóc rotor đã đạt đến nhiệt độ cần khống chế là 220 0C. Bảng 4. Thời gian để động cơ đạt nhiệt độ tới hạn,làm mát tự nhiên, chế độ ngắn hạn, đảm bảo cấp cách điện H. Phương pháp làm mát Thời gian (s) Nhiệt độ tới hạn (0C) Dq stator Lõi thép stator Dq rotor (lồng sóc) Lõi thép rotor Trục Vỏ Ổ bi Tự nhiên 980 165.2 157.6 219 210.2 199.8 151.4 127.7 5. KẾT LUẬN Bài báo đã trình bày phương pháp tính toán nhiệt – điện từ của động cơ servo. Các kết quả mô phỏng nhiệt tại tốc độ 500 rpm, đối với chế độ hoạt động liên tục, sau một khoảng thời gian các bộ phận sẽ ổn định nhiệt. Nhiệt độ cao nhất tại dây quấn stator là 154.8 0C, phù hợp với lựa chọn cấp cách điện dây quấn F. Tại các điểm hoạt động ngắn hạn bị giới hạn về nhiệt, tùy từng điểm cụ thể mà thời gian hoạt động cho phép là khác nhau. Trong trường hợp thay đổi kết cấu làm mát, ví dụ như thêm tản nhiệt hay làm mát bằng quạt, nhiệt độ động cơ sẽ giảm, thời gian làm việc ngắn hạn của động cơ sẽ tăng lên (thời gian tăng từ 900 s đối với làm mát tự nhiên tăng lên 1060 s đối với làm mát bằng quạt, tăng 17.7 %). Khi thay đổi cấp cách điện (cấp F thành cấp H), với trường hợp làm mát tự nhiên, đã làm tăng thời gian làm việc ngắn hạn cho động cơ (tăng thời gian từ 900 s lên thành 980 s, tăng 8.9 %). Kết quả mô phỏng nhiệt động cơ trong hai chế độ hoạt động cho thấy, thiết kế động cơ hoàn toàn phù hợp và đáp ứng yêu cầu cách điện khi hoạt động. Dựa vào biểu đồ phát nhiệt, có thể xem xét tối ưu động cơ về mặt kích thước để giảm khối lượng cũng như giá thành sản xuất. Lời cảm ơn: Các tác giả xin chân thành cảm ơn Motor Design Limited đã hỗ trợ cho nghiên cứu này. TÀI LIỆU THAM KHẢO [1]. Aldo Boglietti, Andrea Cavagnino, David Staton, Martin Shanel, Markus Mueller, and Carlos Mejuto, “Evolution and modern approaches for thermal analysis of electrical machines”, IEEE Transactions on Industrial Electronics, Vol. 56, (2009), no. 3, pp. 871-882. [2]. D. A. Staton, A. Cavagnino, “Convection Heat Transfer and Flow Calculations Suitable for Electric Machines Thermal Models”, IEEE Transactions on Industrial Electronics, Vol. 55, No. 10, (2008), pp. 3509-3516. [3]. A. Boglietti, A. Cavagnino, “Analysis of the Endwinding Cooling Effects in TEFC Induction Motors”, IEEE Transactions on Industry Applications, Vol. 43, No. 5, (2007), pp.1214 – 1222. [4]. Arbab, N., Wang, W., Lin, C., Hearron, J.,Fahimi, B. “Thermal modeling and analysis of a double- stator switched reluctance motor”, IEEE Transactions on Energy Conversion, Vol. 30, No 3 (2015), pp.12 09-1217. [5]. D. Staton, S. J. Pickering, and D. Lampard, “Recent advancement in the thermal design of electric motors”, in Proc. SMMA—Fall Tech. Conf., Durham, NC, (2001), pp 3–5. [6]. A. Boglietti, A. Cavagnino, M. Lazzari, and M. Pastorelli, “A simplified thermal model for variable- speed self-cooled industrial induction motor”, IEEE Transactions on Industrial Application, Vol. 39, no. 4, (2002), pp. 723–730. Kỹ thuật điều khiển & Điện tử 70 N. Đ. Bắc, , N. T. Giang, “Mô phỏng nhiệt, so sánh động cơ servo không đồng bộ.” [7]. Staton, D.A., Boglietti, A., Cavagnino, A, “Solving the More Difficult Aspects of Electric Motor Thermal Analysis in Small and Medium Size Industrial Induction Motors”, IEEE Transactions on Energy Conversion, Vol 20, Issue 3, (2005), pp. 620 – 628. [8]. M. Kasprzak, J. W. Jiang, B. Bilgin, and A. Emadi, “Thermal analysis of a three-phase 24/16 switched reluctance machine used in HEVs,” IEEE Energy Conversion Congress and Exposition, Proceedings. (2016), pp.1-7. [9]. Dave Stoton, Livio Susnjic, “Induction Motors Thermal Analysis”, Strojarstvo Vol 51, No. 6, (2009), pp. 623-631. [10]. M. Roffi, F. J. T. E. Ferreira and A. T. De Almeida, “Comparison of different cooling fan designs for electric motors”, 2017 IEEE International Electric Machines and Drives Conference (IEMDC), Miami, FL, 2017, pp. 1-7. ABSTRACT THERMAL SIMULATIONS, COMPARE COOLING STRUCTURES FOR ASYNCHRONOUS SERVOMOTOR This paper presents thermal simulations and compares different cooling structures of an asynchronous servomotor. Thank to the advantage of almost instantaneous calculation speed, the design process can quickly analyze the thermal changes in motor components. The Motor-CAD software is used to select parameters related to the heat generation in the optimal design of the electric machine. The application of thermal-electromagnetic simulation in the design process reduces the requirements for prototype manufacturing and testing, thus reducing the research time and costs. Based on the results of thermal analysis and the threshold temperature limit of the components in the machine, this paper has both objectives: considering the optimal parameters and selecting the cooling architecture to minimize the mass or the production cost, while maximizing the peak torque of the servomotor. Keywords: Servomotor; Thermal model; Dissipation design; Thermal calculation; Motor optimization. Nhận bài ngày 14 tháng 12 năm 2020 Hoàn thiện ngày 20 tháng 01 năm 2021 Chấp nhận đăng ngày 05 tháng 02 năm 2021 Địa chỉ: Đại học Bách khoa Hà Nội. * Email: bacnd@nuce.edu.vn.
File đính kèm:
mo_phong_nhiet_so_sanh_cau_truc_lam_mat_dong_co_servo_khong.pdf