Giáo trình Điều khiển hệ thống cơ điện tử sử dụng PLC
Ngôn ngữ lập trình: PLC S7-300 có ba ngôn ngữ lập trình cơ bản sau:
Ngôn ngữ lập trình liệt kê lệnh STL (Statement List). Đây là
dạng ngôn ngữ lập trình thông thường của máy tính. Một chương trình
được hoàn chỉnh bởi sự ghép nối của nhiều câu lệnh theo một thuật
toán nhất định, mỗi lệnh chiếm một hàng và có cấu trúc chung “tên
lệnh” + “toán hạng”.
Ngôn ngữ lập trình LAD (Ladder Logic). Đây là dạng ngôn ngữ
đồ hoạ, thích hợp với những người lập trình quen với việc thiết kế
mạch điều khiển logic.
Ngôn ngữ lập trình FBD (Function Block Diagram). Đây cũng là
dạng ngôn ngữ đồ hoạ, thích hợp cho những người quen thiết kế mạch
điều khiển số.
Trong PLC có nhiều ngôn ngữ lập trình nhằm phục vụ cho các
đối tượng sử dụng khác nhau. Tuy nhiên một chương trình viết trên
ngôn ngữ LAD hay FBD có thể chuyển sang dạng STL, nhưng ngược
lại thì không. Và trong STL có nhiều lệnh mà LAD hoặc FBD không
có. Đây cũng là thế mạnh của ngôn ngữ STL
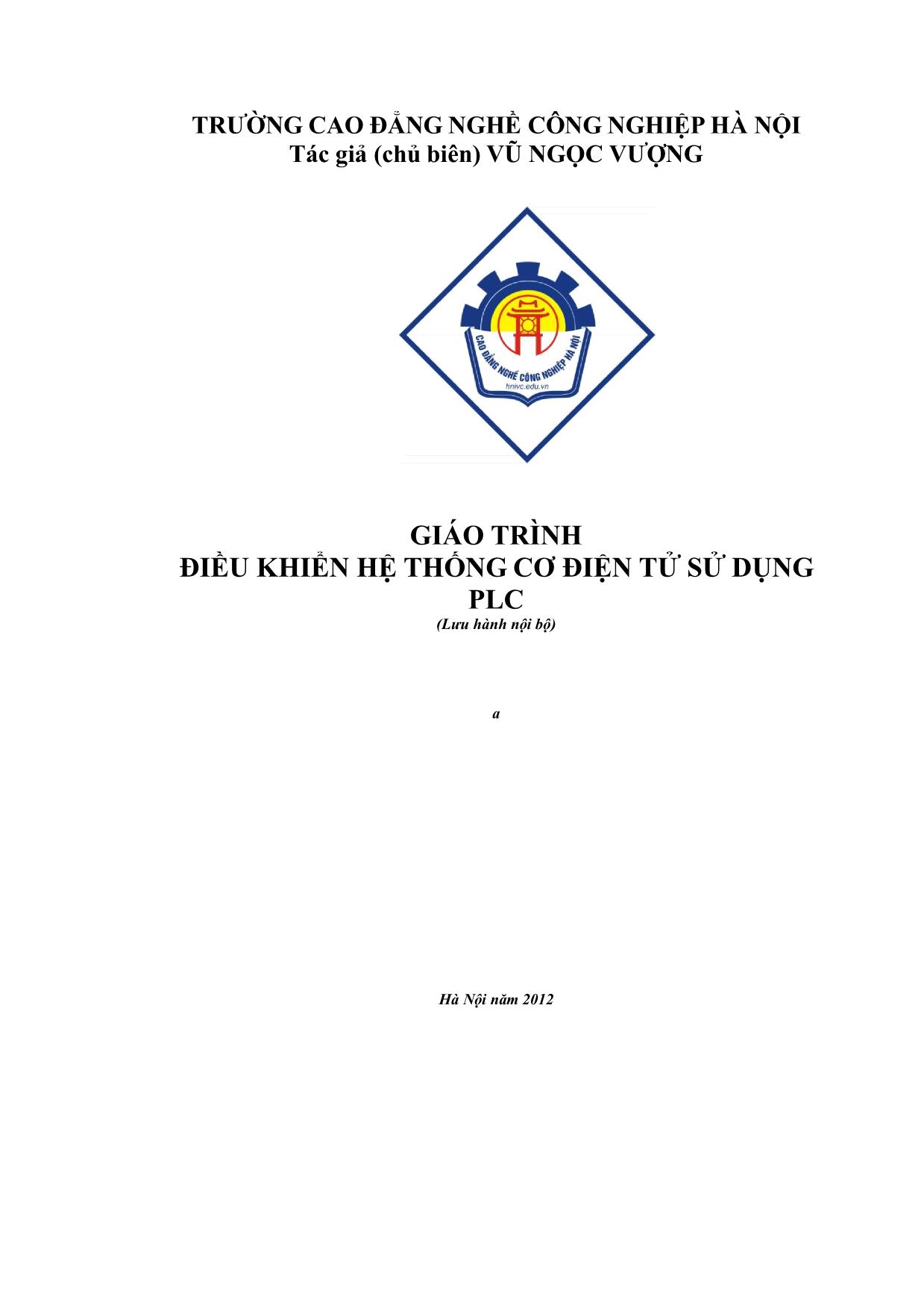
Trang 1
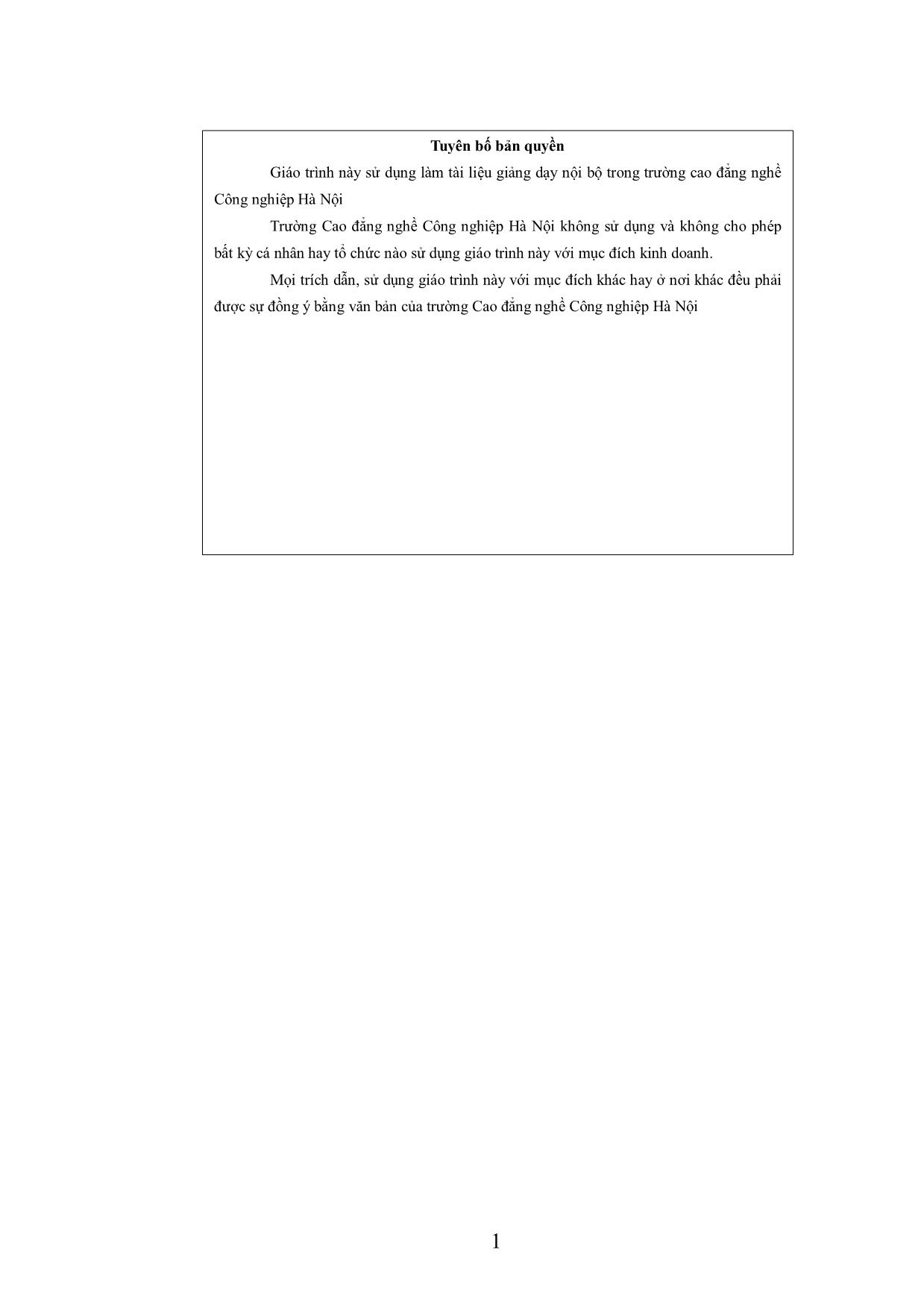
Trang 2
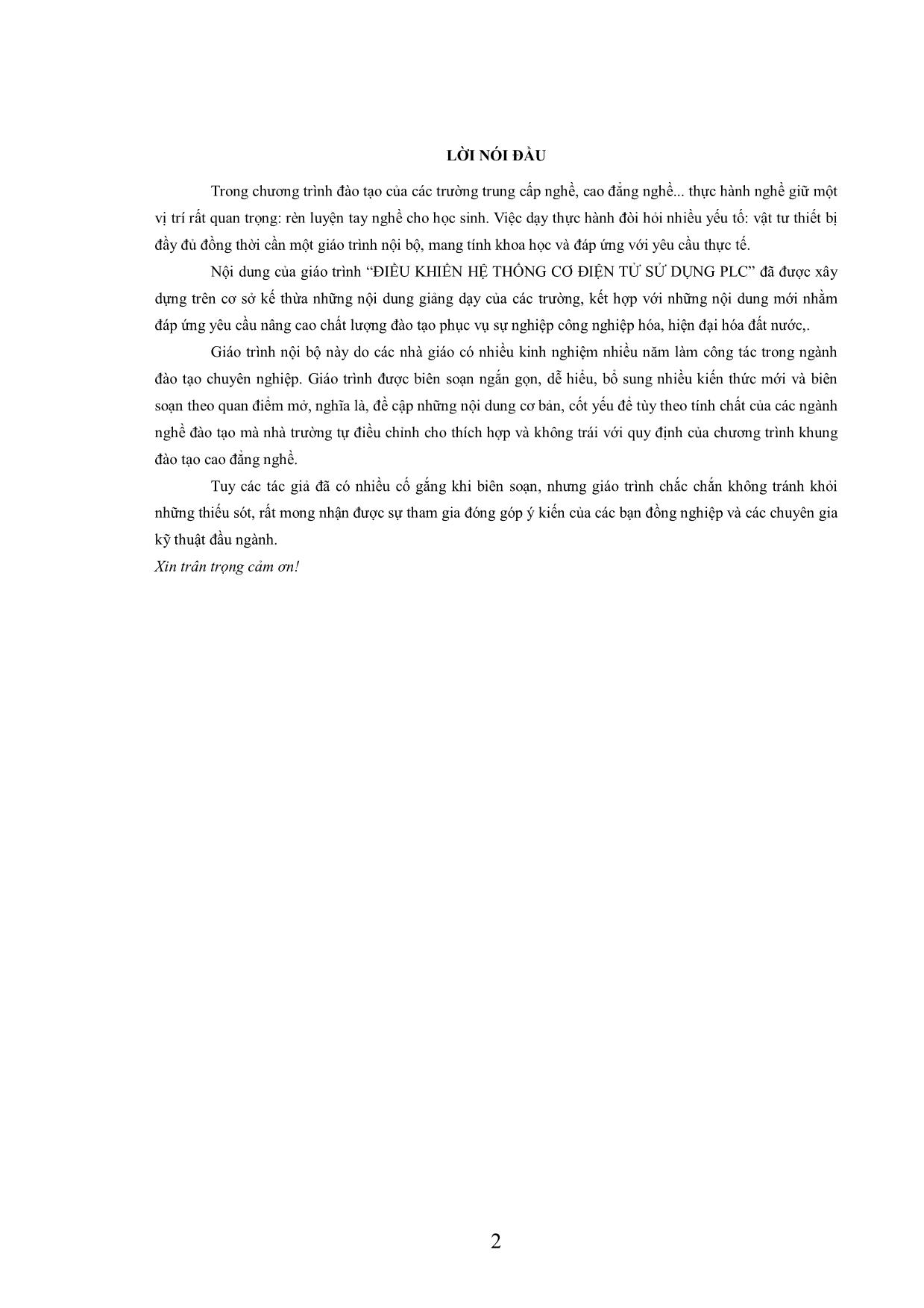
Trang 3
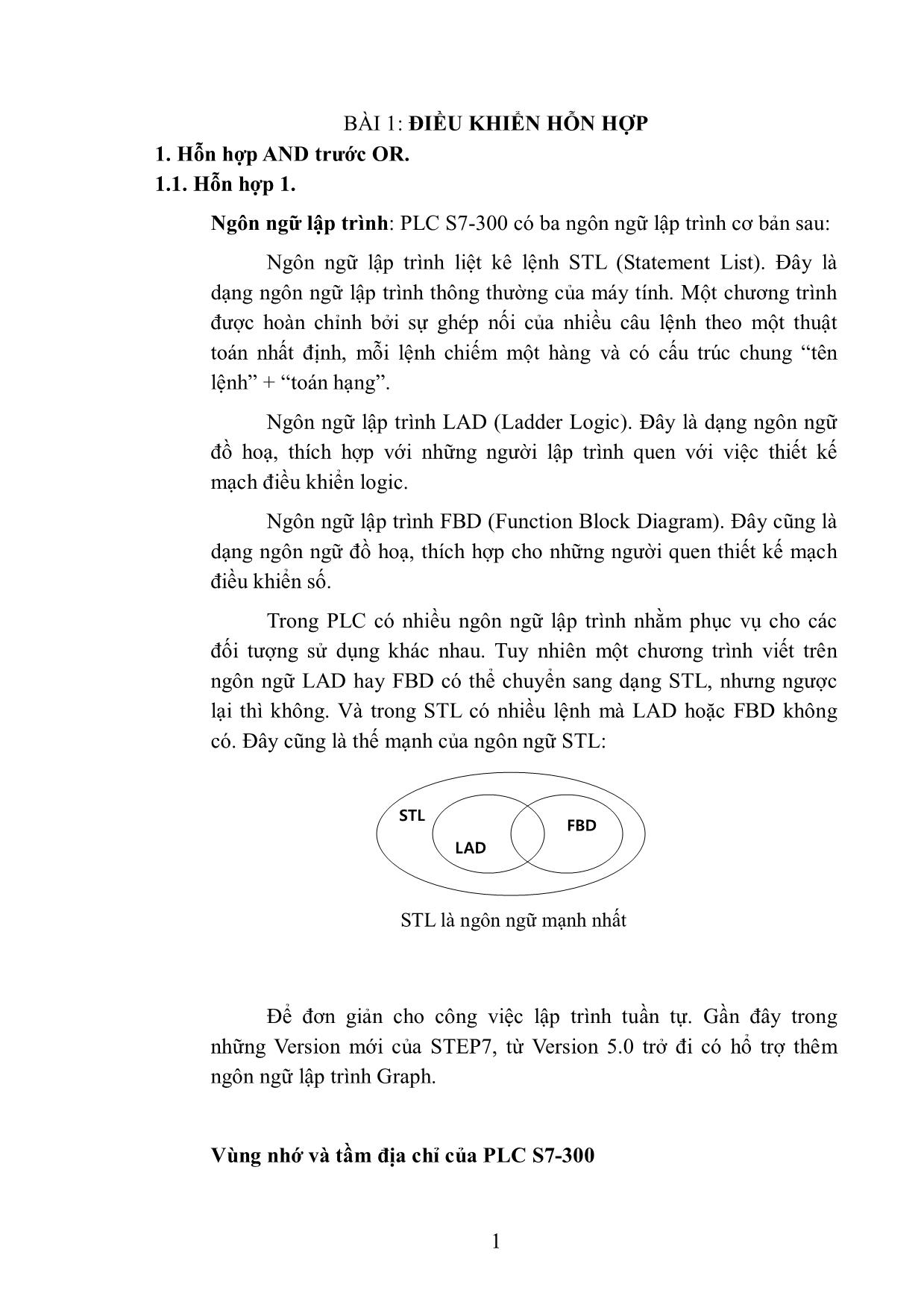
Trang 4
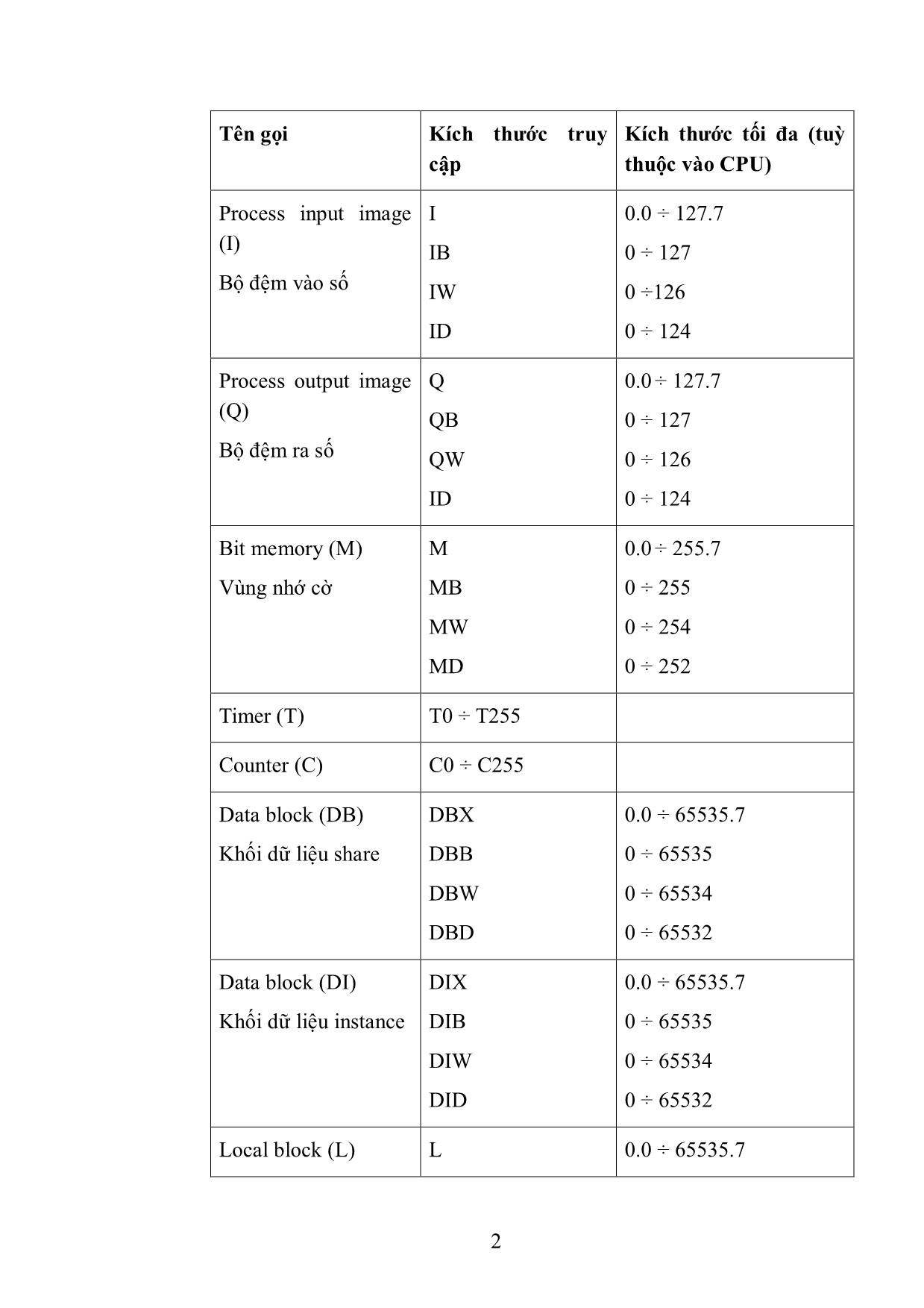
Trang 5
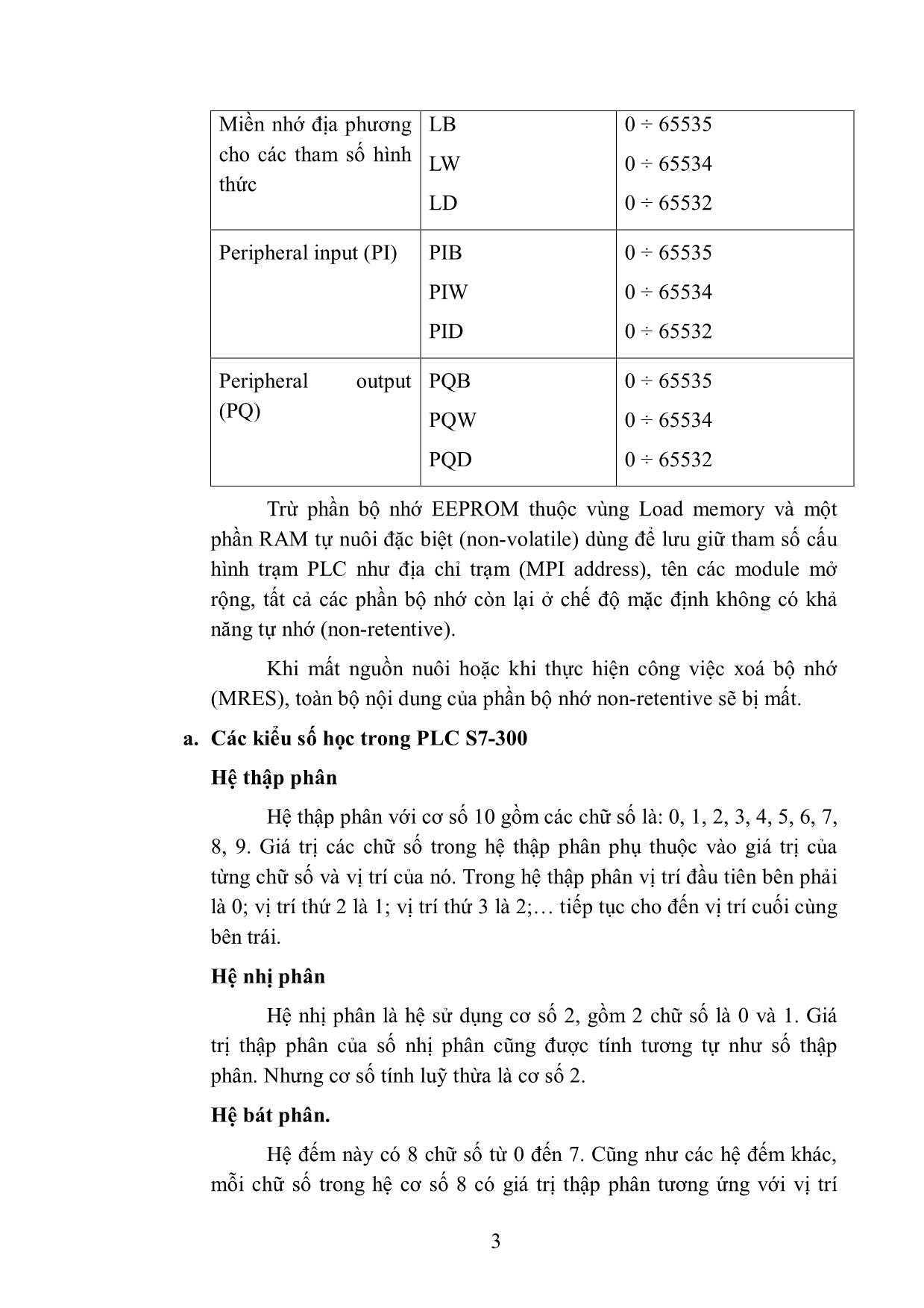
Trang 6
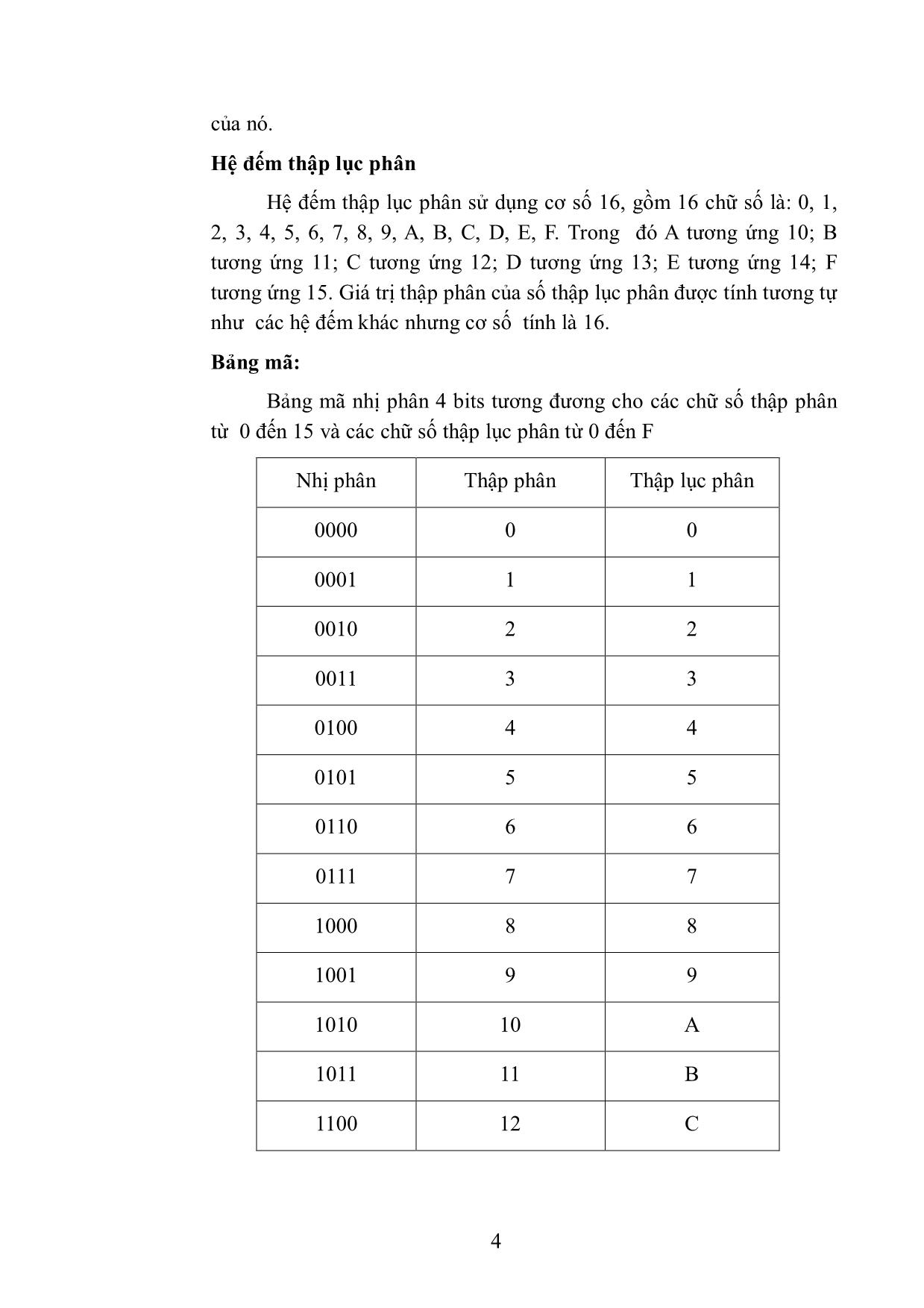
Trang 7
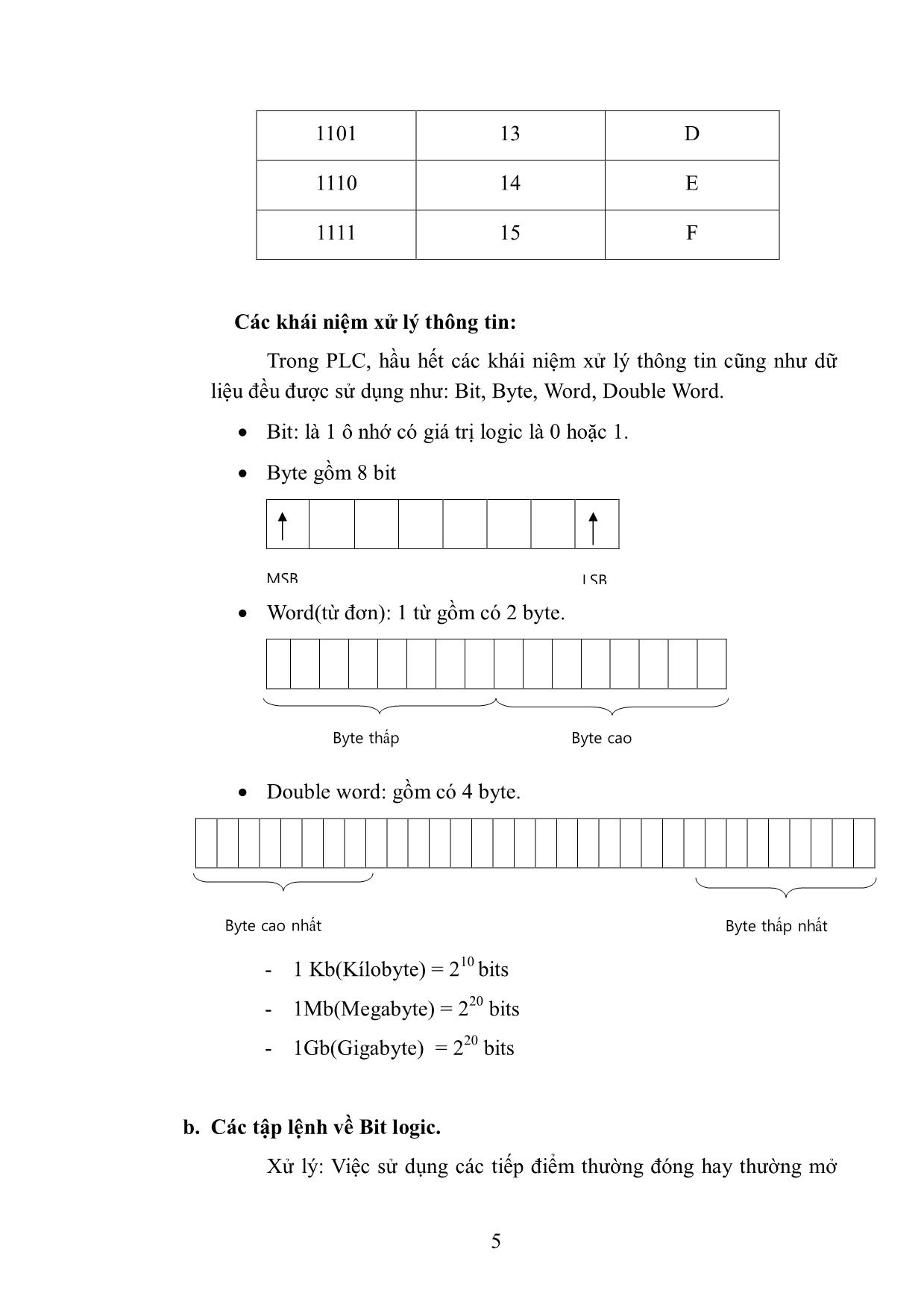
Trang 8
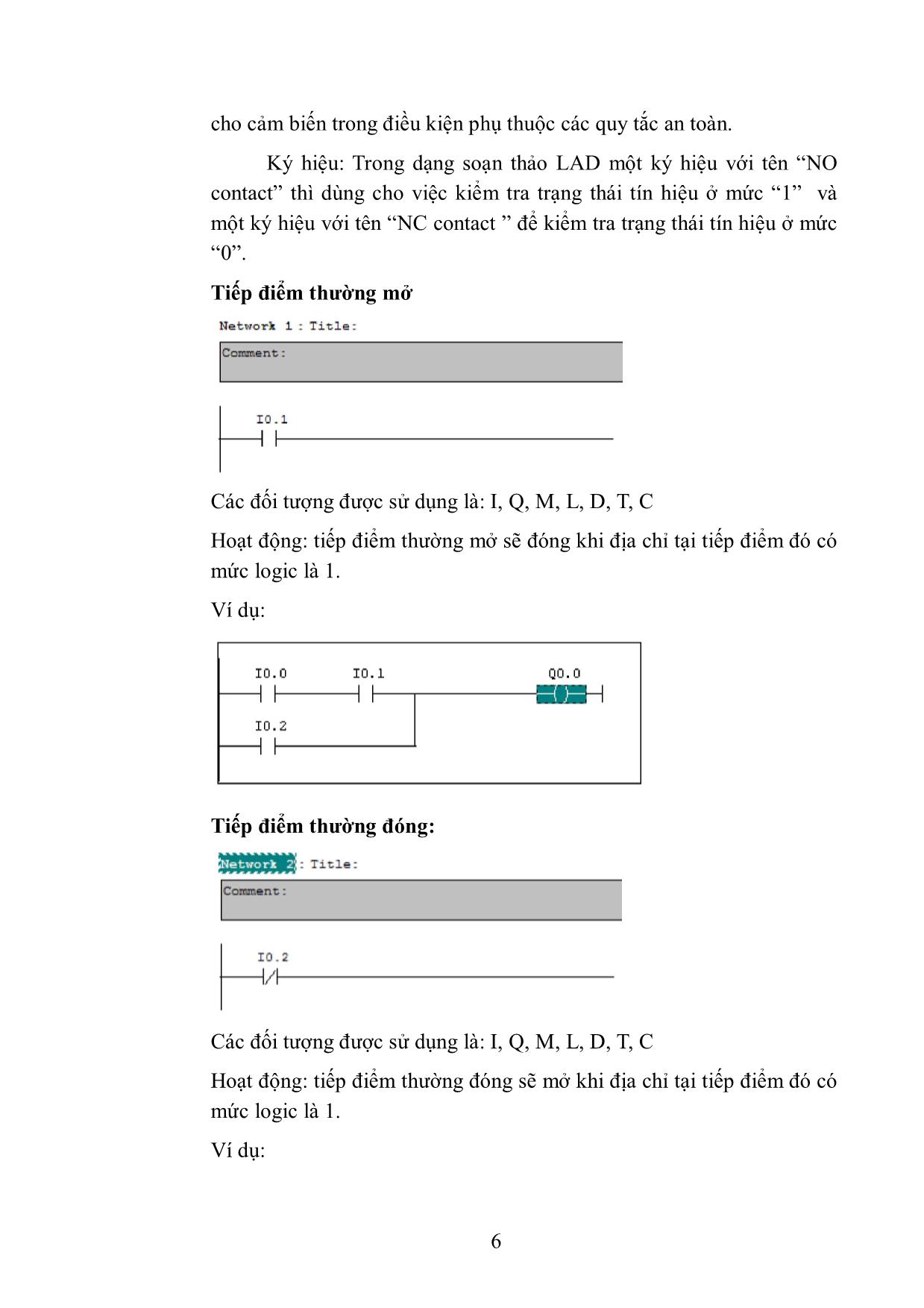
Trang 9
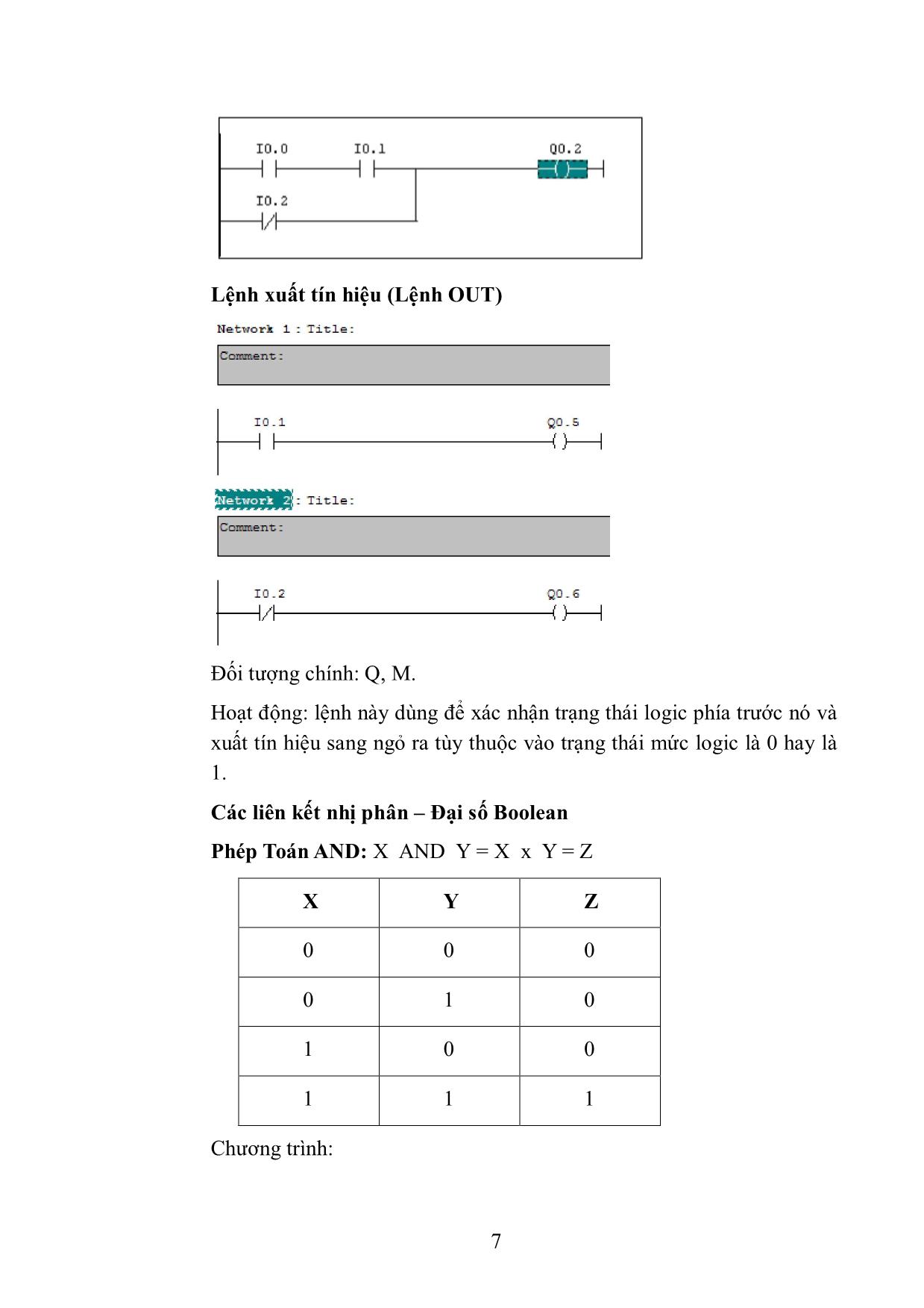
Trang 10
Tải về để xem bản đầy đủ
Tóm tắt nội dung tài liệu: Giáo trình Điều khiển hệ thống cơ điện tử sử dụng PLC
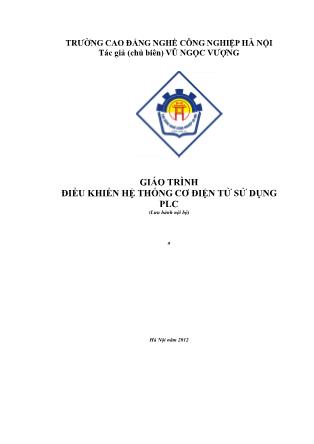
h bàn máy chuyển động của các máy cắt gọt kim loại. Bước 1: Phân tích yêu cầu công nghệ Bước 2: Qui định địa chỉ vào/ra. Bước 3: Viết chương trình điều khiển. Bước 4 Đặt thời gian thực cho CPU 90 BÀI 7: LẬP TRÌNH CẤU TRÚC Mục tiêu: - Trình bày được ưu điểm, pham vi ứng dụng của lập trình cấu trúc. - Mô tả các yêu cầu, phương pháp lập trình cấu trúc. - Lập trình theo cấu trúc, kết nối, chạy thử, hiệu chỉnh, đảm bảo yêu cầu bài tập. - Nghiêm túc trong học tập 1. Khái niệm về lập trình cấu trúc, nhiệm vụ của các khối chức năng. 2. Khai báo local block cho FC, 3. Gọi khối FC và thủ tục tham trị. 4. local block của FB. 5. Gọi khối FB và thủ tục tham trị. 6. Ngăn xếp B và ngăn xếp L ( B- Stack, L- Stack) 7. Bài tập ứng dụng đèn quảng cáo. 91 BÀI 8 : ĐIỀU KHIỂN ĐỘNG CƠ BƯỚC Mục tiêu: - Trình bày được nguyên lý điều khiển tốc độ, chiều quay của động cơ bước. - Thiết lập được thuật toán điều khiển động cơ bước. - Lập trình, kết nối, chạy thử, hiệu chỉnh, đảm bảo yêu cầu bài tập. - Làm việc đúng nguyên tắc, cẩn thận, tỉ mỉ. 1.Thuật toán điều khiển động cơ bước. 2. Điều khiển động cơ bước theo thời gian. 3. Điều khiển động cơ bước theo yêu cầu của thiết bị ngoại vi. 4. Động cơ bước điều khiển tay gạt cơ khí. Bài 9 : Lập trình ghép nối PLC với thiết bị ngoại vi Mục tiêu: - Mô tả được nguyên lý làm việc cơ bản và các thông số về tín hiệu đầu vào, ra của chương trình điều khiển - Lập trình, kết nối, chạy thử. - Lắp ráp được mạch điện ghép nối với PLC - Giữ đúng nội qui, đảm bảo an toàn trong thao tác với thiết bị điện. 1. Giới thiệu các thiết bị, linh kiện phục vụ ghép nối PLC với thiết bị ngoại vi. 1.1 Kết nối dây giữa PLC và các thiết bị ngoại vi Việc kết nối dây giữa PLC với ngoại vi rất quan trọng. Nó quyết định đến việc PLC có thể giao tiếp được với thiết bị lập trình (máy tính) cũng như hệ thống điều khiển có thể hoạt động đúng theo yêu cầu được thiết kế hay không. Ngoài ra việc nối dây còn liên quan đến an toàn cho PLC cũng như hệ thống điều khiển. a. Giới thiệu CPU 224 và cách kết nối với thiết bị ngoại vi Sơ đồ bề mặt của bộ điều khiển lập trình S7-200 CPU 224 được cho như hình 5.1. 92 Để cho bộ điều khiển lập trình này hoạt động được thì người sử dụng phải kết nối PLC với nguồn cung cấp và các đầu vào ra của nó với thiết bị ngoại vi. Muốn nạp chương trình vào CPU, người sử dụng phải soạn thảo chương trình bằng các thiết bị lập trình hoặc máy tính với phần mềm tương ứng cho loại PLC đang sử dụng và có thể nạp trực tiếp vào CPU hoặc copy chương trình vào card nhớ để cắm vào rãnh cắm card nhớ trên CPU của PLC. Thông thường khi lập trình cũng như khi kiểm tra hoạt động của PLC thì người lập trình thường kết nối trực tiếp thiết bị lập trình hoặc máy tính cá nhân với PLC. Như vậy, để hệ thống điều khiển khiển bằng PLC hoạt động cũng như lập trình cho nó, cần phải kết nối PLC với máy tính cũng như các đầu vào ra với ngoại vi. 2. Cách nối dây. 2.1. Kết nối với máy tính Đối với các thiết bị lập trình của hãng Siemens có các cổng giao tiếp PPI thì có thể kết nối trực tiếp với PLC thông qua một sợi cáp. Tuy nhiên đối với máy tính cá nhân cần thiết phải có cáp chuyển đổi PC/PPI. Có 2 loại cáp chuyển đổi là cáp RS-232/PPI Multi-Master và cáp USB/PPI Multi-Master. * Cáp RS-232/PPI multi-master: Hình dáng của cáp và công tắc chọn chế độ truyền được cho ở hình 5.2. 93 Hình dáng cáp RS-232/PPI và các chuyển mạch trên cáp. Tùy theo tốc độ truyền giữa máy tính và CPU mà các công tắc 1,2,3 được để ở vị trí thích hợp. Thông thường đối với CPU 22x thì tốc độ truyền thường đặt là 9,6 KBaud (tức công tắc 123 được đặt theo thứ tự là 010). Tùy theo truyền thông là 10 Bit hay 11 Bit mà công tắc 7 được đặt ở vị trí thích hợp. Khi kết nối bình thường với máy tính thì công tắc 7 chọn ở chế độ truyền thông 11 Bit (công tắc 7 đặt ở vị trí 0). Công tắc 6 ở cáp RS-232/PPI Multi-Master được sử dụng để kết nối port truyền thông RS-232 của một modem với S7-200 CPU. Khi kết nối bình thường với máy tính thì công tắc 6 được đặt ở vị trí data Comunications Equipment (DCE) (công tắc 6 ở vị trí 0). Khi kết nối cáp PC/PPI với một Equipment (DTE) (công tắc 6 ở vị trí 1). Công tắc 5 được sử dụng để đặt cáp RS-232/PPI Multi-Master thay thế cáp PC/PPI hoặc hoạt động ở chế độ Freeport thì đặt ở chế độ PPI/Freeport (công tắc 5 ở vị trí 0). Nếu kết nối bình thường là PPI (master) với phần mềm STEP 7 Micro/Win 3.2 SP4 hoặc cao hơn thì đặt ở chế độ PPI (công tắc 5 ở vịtrí 1). Sơ đồ nối cáp RS-232/PPI Multi-Master giữa máy tính và CPU S7-200 với tốc độ truyền 9,6 Kbaud được cho như hình 5.3. 94 Kết nối máy tính với CPU S7-200 RS-232/PPI Multi-Master Cáp USB/PPI multi-master: Hình dáng của cáp được cho ở hình 5.4. Hình dáng cáp USB/PPI. Cách thức kết nối cáp USB/PPI Multi-Master cũng tương tự như cáp RS- 232/PPI Multi-Master. Để sử dụng cáp này, phần mềm cần phải là STEP 7- Micro/WIN 3.2 Service Pack 4 (hoặc cao hơn). Cáp chỉ có thể được sử dụng với loại CPU22x hoặc sau này. Cáp USB không được hỗ trợ truyền thông Freeport và download cấu hình màn TP070 từ phần mềm TP Designer Nối nguồn cung cấp cho CPU Tùy theo loại và họ PLC mà các CPU có thể là khối riêng hoặc có đặt sẵn các đầu vào và ra cũng như một số chức năng đặc biệt khác. Hầu hết các PLC họ S7-200 được nhà sản xuất lắp đặt các khâu vào, khâu ra và CPU trong cùng một vỏ hộp. Nhưng nguồn cung cấp cho các khâu này hoàn toàn độc lập nhau. Nguồn cung cấp cho CPU của họ S7-200 có thể là: Xoay chiều: 20...29 VAC , f = 47...63 Hz; 85...264 VAC, f = 47...63 Hz Một chiều: 20,4 ... 28,8 VDC Hình 5.5 a,b là sơ đồ nối dây nguồn cung cấp cho CPU 95 Để có thể nhận biết việc cấp nguồn cho CPU, khối vào, khối ra số ta căn cứ vào các chữ số đi kèm theo CPU. Các mã số kèm theo CPU 2xx có thể có như sau: · CPU 2xx DC/DC/DC: Nguồn cấp cho CPU là DC, nguồn cho đầu vào là DC, nguồn cấp cho đầu ra là DC. · CPU 2xx AC/DC/Relay: Nguồn cấp cho CPU là AC, nguồn cho đầu vào là DC, đầu ra là Relay có thể cấp nguồn là DC hoặc AC. Kết nối vào/ra số với ngoại vi Các đầu vào, ra của PLC cần thiết để điều khiển và giám sát quá trình điều khiển. Các đầuvào và ra có thể được phân thành 2 loại cơ bản: số (Digital) và tương tự (analog). Hầu hết các ứng dụng sử dụng các vào/ra số. Trong bài này chỉ đề cập đến việc kết nối các đầu vào/ra số với ngoại vi, còn đối với đầu vào/ra tương tự sẽ trình bày ở chương “xử lý tín hiệu analog”. Đối với bộ điều khiển lập trình họ S7-200, hãng Siemens đã đưa ra rất nhiều loại CPU với điện áp cung cấp cho các đầu vào ra khác nhau. Tùy thuộc từng loại CPU mà ta có thể nối dây khác nhau. Việc thực hiện nối dây cho CPU có thể tra cứu sổ tay kèm theo của hãng sản xuất. Kết nối các đầu vào số với ngoại vi Các đầu vào số của PLC có thể được chế tạo là một khối riêng, hoặc kết hợp với các đầu ra chung trong một khối hoặc được tích hợp trên khối CPU. Trong trường hợp nào cũng vậy, các đầu vào cũng phải được cung cấp nguồn riêng với cấp điện áp tùy thuộc vào loại đầu vào. Cần lưu ý trong một khối đầu vào cũng như các đầu vào được tích hợp sẵn trên CPU có thể có các nhóm được cung cấp nguồn độc lập nhau. Vì vậy cần lưu ý khi cấp nguồn cho các nhóm này. Nguồn cung cấp cho các khối vào của họ S7-200 có thể là: 96 Xoay chiều: 15...35 VAC, f = 47...63 Hz; dòng cần thiết nhỏ nhất 4mA 79...135 VAC, f = 47...63 Hz; dòng cần thiết nhỏ nhất 4mA Một chiều: 15 ... 30 VDC; dòng cần thiết nhỏ nhất 4mA Sơ đồ mạch điện bên trong của một số đầu vào được cho như hình Mạch điện của 1 đầu vào số sử dụng nguồn cung cấp DC b) Mạch điện của 1 đầu vào số sử dụng nguồn cung cấp AC Tùy theo yêu cầu mà có thể quyết định sử dụng loại đầu vào nào. + Đầu vào DC: - Điện áp DC thường thấp do đó an toàn hơn. - Đáp ứng đầu vào DC rất nhanh. - Điện áp DC có thể được kết nối với nhiều phần tử trong hệ thống điện. Kiểm tra việc kết nối dây bằng phần mềm Một công việc quan trọng cho người lắp đặt và vận hành là biết được các kết nối của các đầu vào/ra với ngoại vi có đúng hay không trước khi nạp chương trình điều khiển vào CPU. Hoặc khi một hệ thống đang hoạt động bình thường nhưng một sự cố hư hỏng xảy ra thì các phần ngoại vi nào bị hư và phát hiện nó bằng cách nào. Các phần mềm cho các bộ điều khiển bằng PLC thường có trang bị thêm công cụ để kiểm tra việc kết nối dây đầu vào/ra với ngọai vi. Trong phần mềm Step 7 Micro/Win (phần mềm lập trình cho họ S7-200) có trang bị thêm phần này đó là mục Status Chart. Để sử dụng phần mềm tốt hơn hãy xem thêm chương “Phần mềm STEP 7-Micro/Win và ngôn ngữ lập trình”. Status Chart Chúng ta có thể sử dụng Status Chart để đọc, ghi hoặc cưỡng bức các biến trong chương trình theo mong muốn. Để có thể mở Status Chart, ta nhấp đúp chuột vào biểu tượng Status Chart trong cửa sổ Navigation Bar trên màn hình Step 7-Micro/Win32 hoặc vào mục View → Component → Status Chart. 3. Các mô hình và bài tập ứng dụng 3.1 Mô hình băng tải đếm sản phẩm. - Chương trình PLC được download xuống đúng trạm. - Máy tính được khởi động Runtime WinCC và kết nối mạng PROFIBUS giữa các PLC đến máy tính (nếu sử dụng). 97 ** Khi hoạt động với 02 trạm trở lên, ta khởi động lần lượt từ trạm sau đến trạm trước. 1. Mở nguồn điện, khí nén (6 bar). 2. Khởi động PLC. 3. Lấy hết phôi ra khỏi trạm. 4. Đèn báo RESET sáng, nhấn nút RESET trên bảng điều khiển. 5. Đèn báo START sáng, nhấn nút START trên bảng điều khiển. Nhấn nút STOP trạm ngừng hoạt động. Bảng tóm tắt chức năng đèn báo Trạm Trung Gian Đèn Q1 Đèn Q2 Đèn Q1 + Q2 Một số chức năng thường gặp: : Cho phép thoát chế độ Runtime của WinCC. : Cho phép trở về trang Tổng quan. : Cho phép chuyển đến trang kế tiếp. : Control Panel (Bảng điều khiển). : Bộ I/O Simulation, kiểm tra các tín hiệu ra/ vào. Chỉ sử dụng khi Trạm được kết nối với WinCC và chuyển các nút gạt sang vị trí OFF (màu đỏ) trước khi TẮT BỘ I/O SIM. 98 : Bật bộ I/O Sim. : Tắt bộ I/O Sim. (Lưu ý: Chuyển các nút gạt sang vị trí OFF (màu đỏ) trước khi TẮT BỘ I/O SIM). 01. Tổng Quan Trang tổng quan mô tả tổng quát về hệ thống MPS gồm 09 trạm, mỗi vùng tương ứng với mỗi trang của Trạm, dùng để chuyển trang cần đến: - Trạm Cấp Phôi (Distribution Station) - Trạm Kiểm Tra (Testing Station) - Trạm Gia Công (Processing Station) - Trạm Tay Gắp (Handling Station) - Trạm Trung Gian (Buffer Station) - Trạm Robot (Robot Station) - Trạm Lắp Ráp (Assembly Station) - Trạm Đột Dập Thủy Lực (Punching Station) - Trạm Phân Loại (Sorting Station) Khi bất kỳ trạm nào kết nối vào hệ thống, thì khu vực quanh trạm đó sẽ màu xanh dương. Alarm: Dùng để đến trang Tin báo của WinCC. PROFIBUS Network: Dùng để đến trang Mạng PROFIBUS. 02. Alarm 99 Trang Tin báo chức năng báo: - Các hoạt động kết nối của PLC các trạm đến WinCC. - Báo các tín hiệu như: Trạm Cấp Phôi hết phôi ở ụ chứa, Trạm Phân Loại đầy phôi ở máng . 03. Network Trang Mạng PROFIBUS cho biết: - Địa chỉ PROFIBUS của từng PLC. - Trạng thái của các PLC. Đường màu đỏ biểu thị đường mạng kết nối giữa các PLC – WinCC. Trạm Trung Gian 100 Trang Trạm Trung Gian: - Biểu thị hình ảnh tổng quan về trạm Trung Gian. - Cho biết tín hiệu các địa chỉ vào/ ra của trạm Trung Gian. - Trạng thái kết nối của trạm Trung Gian. Trạm có Control Panel: cho phép điều khiển trạm bằng các nút nhấn từ máy tính. Trạm có bộ I/O Simulation: cho phép kiểm tra các tín hiệu ngỏ/ ra của trạm. PHỤ LỤC 1: BẢNG ĐỊA CHỈ STT Symbol Add Comment INPUT 1 Part_AV I0.0 CB biến phát hiện phôi 2 B2 I0.1 CB báo không có phôi trước gạt 3 B3 I0.2 CB báo không có phôi ở cuối b.tải 4 1B1 I0.3 Gạt vươn ra 5 1B2 I0.4 Gạt thu lại 6 I0.5 -- 7 I0.6 -- 8 IP_FI I0.7 CB truyền thông trạm sau (Nhận) 9 -S1 I1.0 Nút START 10 -S2 I1.1 Nút STOP (NC) 11 -S3 I1.2 SW AUTO/MAN 12 -S4 I1.3 Nút RESET 101 13 I1.4 14 I1.5 15 I1.6 16 I1.7 OUTPUT 1 1M1 Q0.0 Gạt vươn ra 2 M1 Q0.1 Băng tải chạy 3 Q0.2 -- 4 Q0.3 -- 5 Q0.4 -- 6 Q0.5 -- 7 Q0.6 -- 8 IP_N_FO Q0.7 CB truyền thông trạm trước (Gửi) 9 -H1 Q1.0 Đèn nút START 10 -H2 Q1.1 Đèn nút STOP 11 -H3 Q1.2 Đèn báo chức năng số 1 12 -H4 Q1.3 Đèn báo chức năng số 2 13 Q1.4 14 Q1.5 15 Q1.6 16 Q1.7 102 3.2. Mô hình đóng mở cửa tự động. 2. Chương trình điều khiển đóng mở cửa tự động - Điều khiển cửa tự động mở khi có người từ ngoài vào hoặc từ trong ra và đóng lại khi không có người. Sơ đồ hệ thống điều khiển đóng mở cửa tự động ①Chi tiết kĩ thuật điều khiển ⓐ Nhận biết người bằng cảm biến lắp trong và ngoài cửa → motor quay thuận → cửa mở ⓑ Nhận biết cửa đã mở hoàn toàn → motor dừng lại ⓒ Cửa mở hoàn toàn và 5 giây sau → motor quay ngược → cửa đóng ⓓ Nhận biết cửa đã đóng hoàn toàn → motor dừng lại. ② Quy định Input, Output ⓐ Bộ phận Input - Lắp đặt bên trong và bên ngoài mỗi bên 1 cảm biến nhận biết xem có người ở trước cửa hay không → 2 cảm biến nhận biết người - Nhận biết cửa đã mở hoàn toàn, nhận biết cửa đã đóng hoàn toàn → 2 công tắc giới hạn ⓑ Bộ phận output - Công tắc tơ điện tử MC1, MC2 để điều khiển quay motor thuận chiều, ngược chiều. 103 Sơ đồ hệ thống ⓒ Giải thích hình vẽ [Hình 7-8] - Cảm biến ở bộ phận Input cảm biến khi có người ra vào từ trong và ngoài cửa: SEN1, SEN2 - Công tắc giới hạn cảm nhận biết cửa đã đóng và mở hoàn toàn khi cửa mở và đóng: LS1, LS2 - Cần motor đóng mở cửa ở bộ phận Output, công tắc tơ điện tử dùng để điều khiển motor quay thuận (MC1), công tắc tơ điện tử dùng để điều khiển motor quay nghịch (MC2). ③ Bản vẽ chương trình - Mạch mở cửa khi nhận biết có người trong và ngoài cửa. Mạch mở cửa - SEN1: cảm biến cảm biến người ngoài cửa (P00) - SEN2: cảm biến cảm biến người trong cửa (P01) - P20: công tắc tơ điện tử điều khiển motor quay thuận chiều (MC1) ④ Chương trình điều khiển cửa đóng mở. P00 P20 P01 SEN1 SEN2 Khi có người bên trong đi ra Khi có người ngoài cửa Lệnh Mở cửa 104 Hình 13-10 Chương trình điều khiển cửa đóng mở 1. Chuẩn bị công việc - Hiểu rõ kĩ năng thao tác và điều kiện yêu cầu thao tác. - Hiểu rõ số mỗi điểm cuối của mạch điều khiển. - Kiểm tra xem vật tư và công cụ có vấn đề gì không. 2. Sắp xếp và cố định dụng cụ. 3. Nối dây trong mạch điện. 4. Kiểm tra 5. Kiểm tra hoạt động. 6. Yêu cầu kiểm tra xác nhận 7. Chỉnh lý chỉnh đốn. 3.3. Mô hình điều khiển động cơ У / Δ . 3.4. Mô hình thiết bị vô nước chai 3.5. Mô hình điều khiển máy nén khí công nghiệp. 105 TÀI LIỆU THAM KHẢO [1]- Nguyễn Trọng Thuần, Điều khiển logic và ứng dựng, NXB Khoa học kỹ thuật 2006 [2]- Trần Thế San (biên dịch), Hướng dẫn thiết kế mạch và lập trình PLC, NXB Đà Nằng 2005 [3]- Tăng Văn Mùi (biên dịch), Điều khiển logic lập trình PLC, NXB Thống kê 2006
File đính kèm:
giao_trinh_dieu_khien_he_thong_co_dien_tu_su_dung_plc.pdf