Characteristics of plasma electrolytic oxidation coatings on 6061 al alloy prepared at different current densities
Plasma electrolytic oxidation (PEO) has earned much attention due to its powerful
and easy formation of hard and corrosion-resistant oxide layers on valve metals, such as Al
alloys. Here we report the effects of current density (CD) on microstructure and properties of
coatings on 6061 Al alloy by PEO using direct current mode. The electrolyte contains the
chemicals of Na2SiO3, Na2WO42H2O, and NaH2PO2H2O. The CDs adopted 5.0, 7.5, 10.0, and
12.5 A/dm2, respectively, for a fixed PEO time of 30 min. The thickness, surface morphology,
phase composition, hardness, and corrosion resistance of PEO coatings as a function of the
applied CD have been studied and discussed. Studied results show the coating thickness is
proportional to the applied CD. When the applied CD increased 2.5 times from 5.0 to 12.5
A/dm2, the growth rate of oxide layers increased by more than 3.5 times, from 0.423 to 1.493
μm/min, respectively. SEM images are characterized by a reduction in the ratio of agglomeratebumps-region/flatten-region as applied CD increases. However, cracks and larger pores appear
when the applied CD is higher than 10.0 A/dm2. X-ray diffraction pattern shows that the main
phases of Al, -Al2O3, α-Al2O3, and W are contained in all coatings. PEO coated sample has the
highest hardness of 1290 HV and highest polarization resistance of 8.80 106 cm2 obtained at
applied CD of 10 A/dm2 which shows the best performance of the coating. The variation in
coating performance is explained by microstructure details, specifically phases, compositions of
oxide-layers, and micro-pores and cracks.
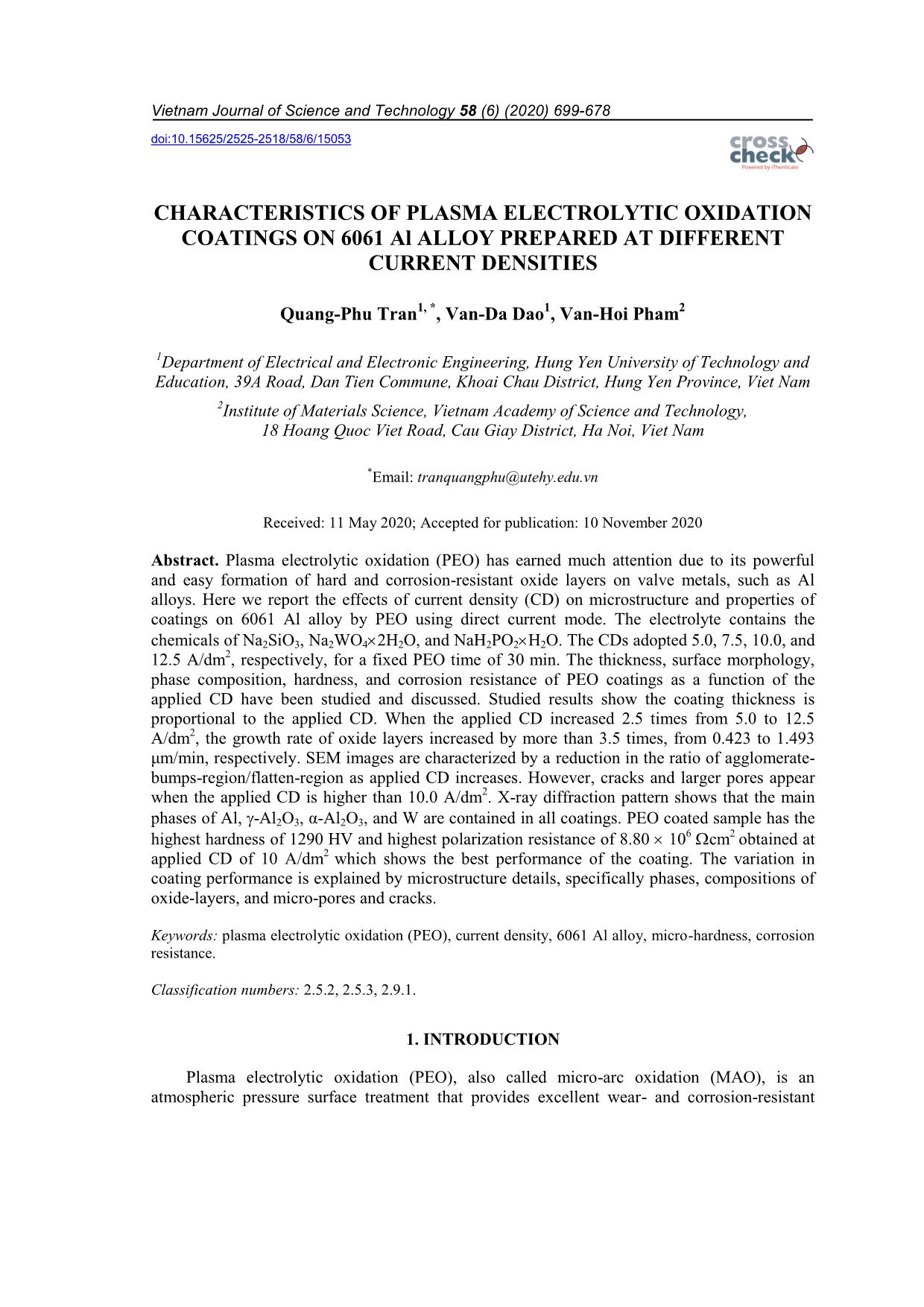
Trang 1
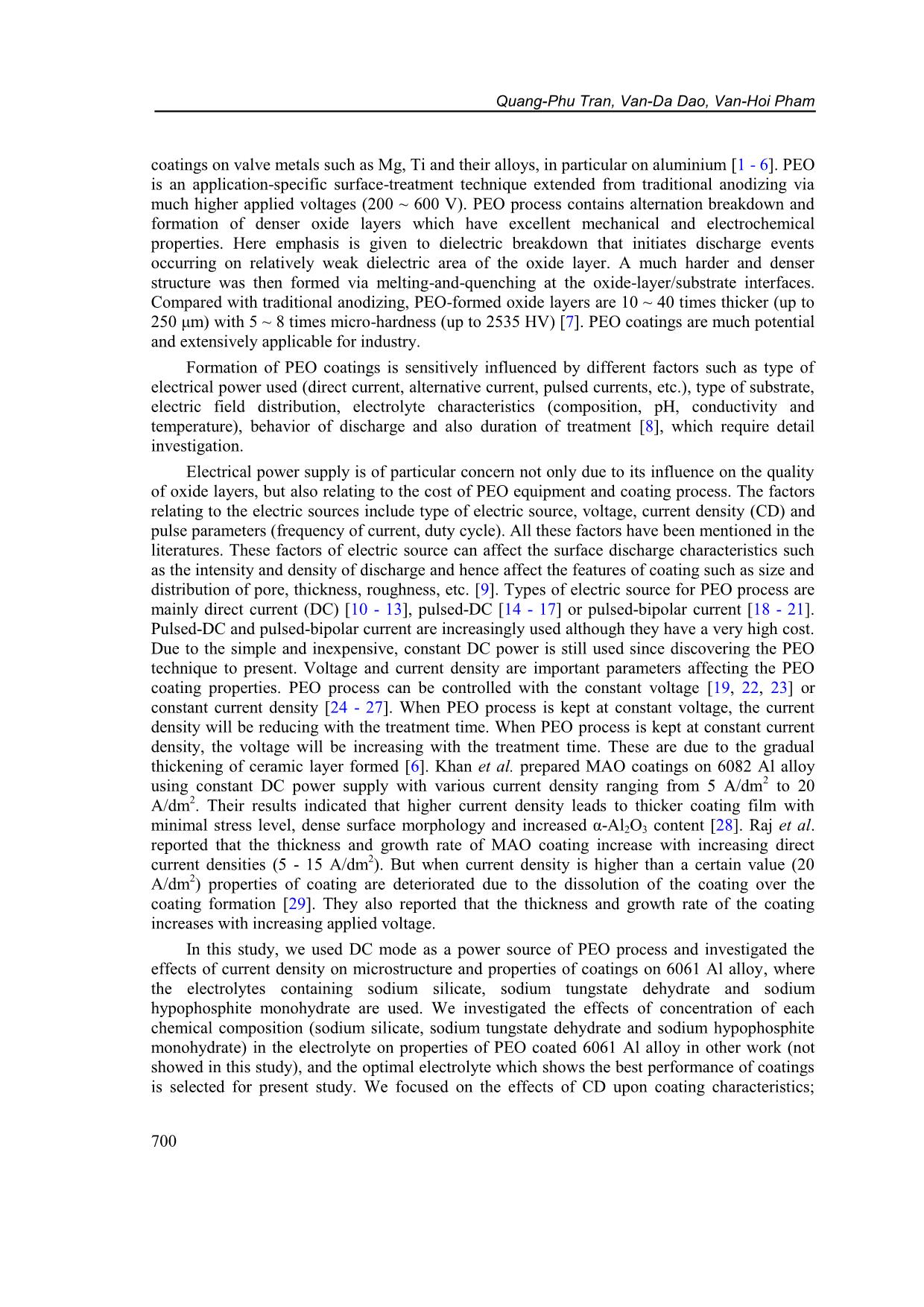
Trang 2
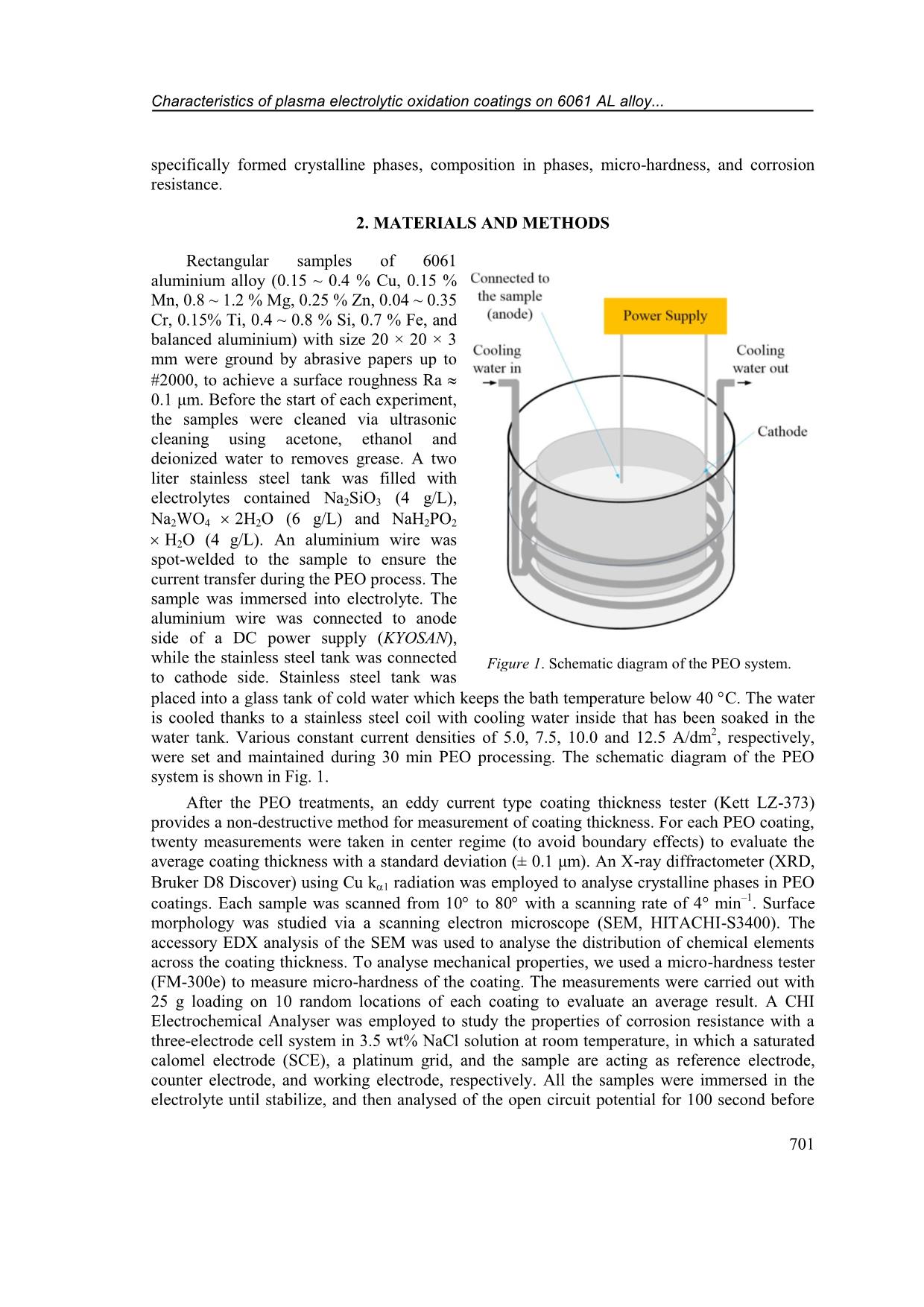
Trang 3
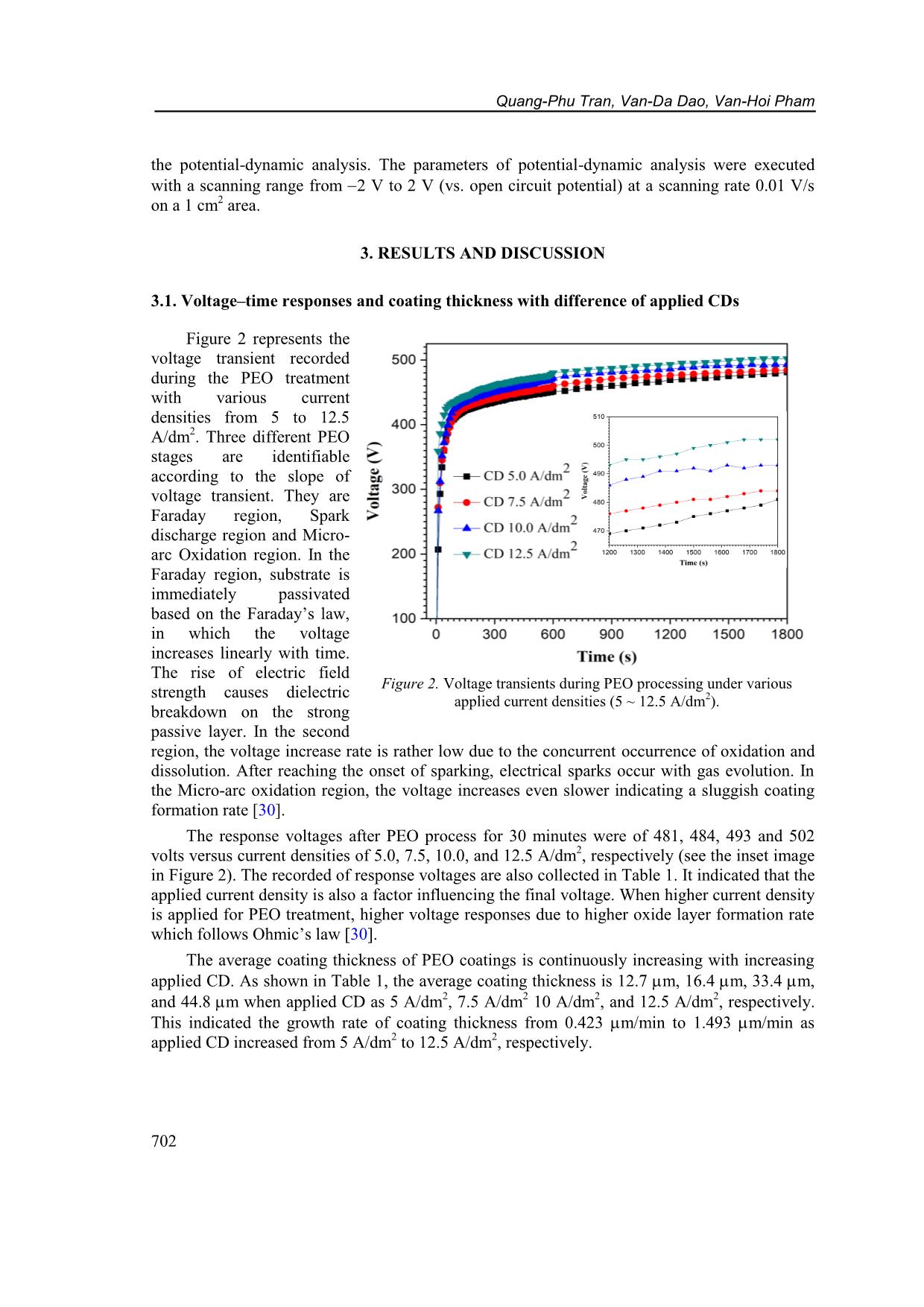
Trang 4
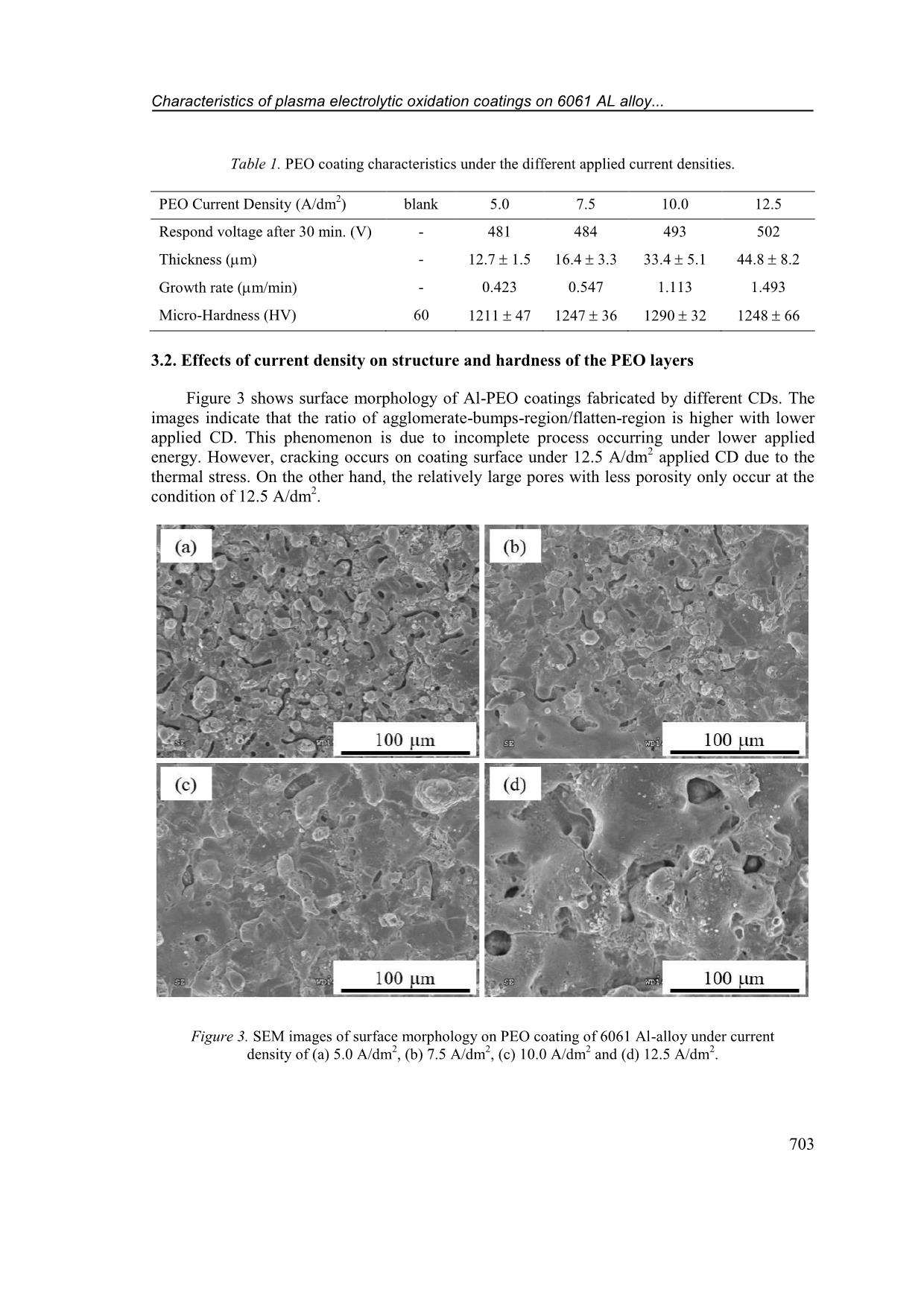
Trang 5
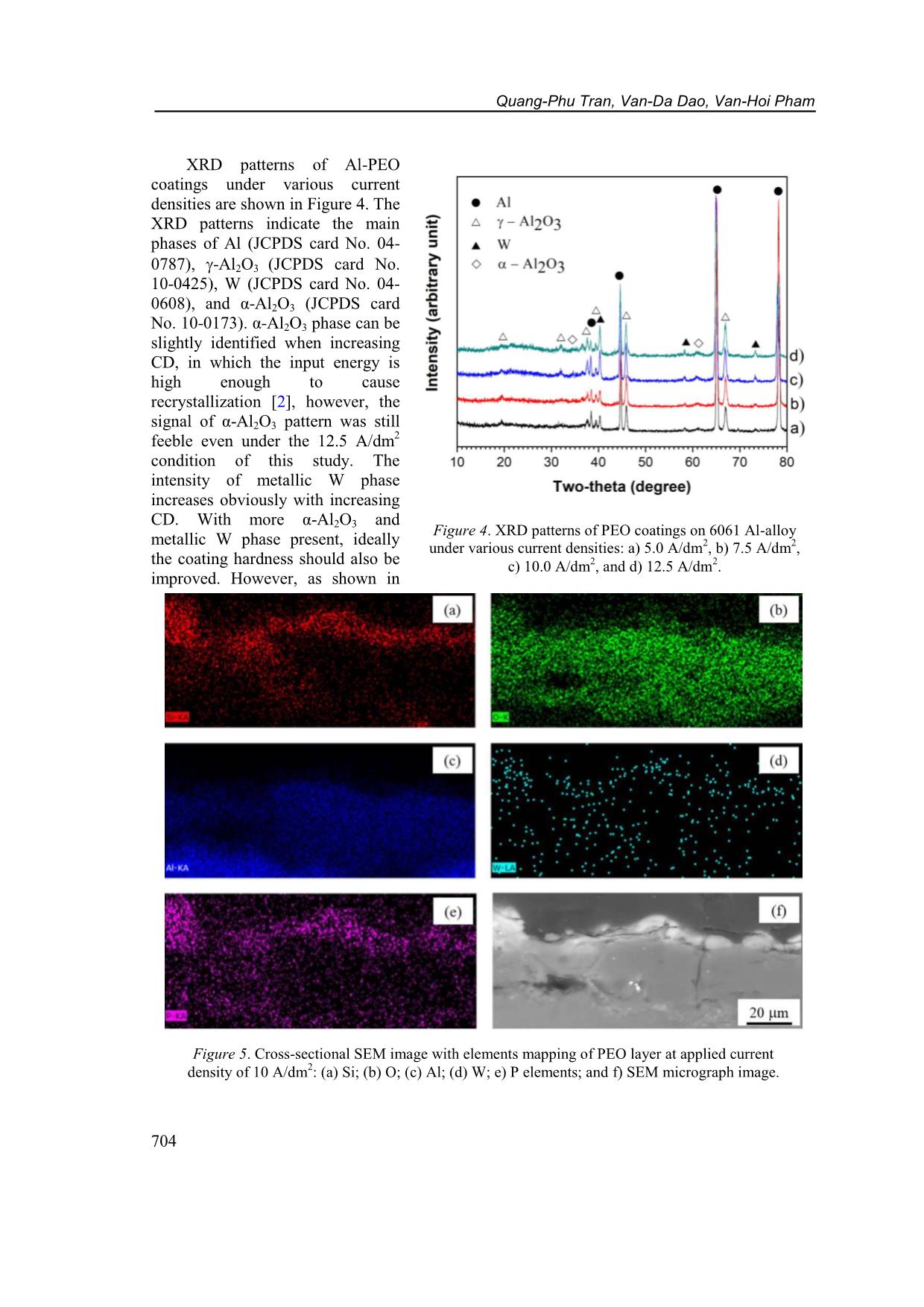
Trang 6
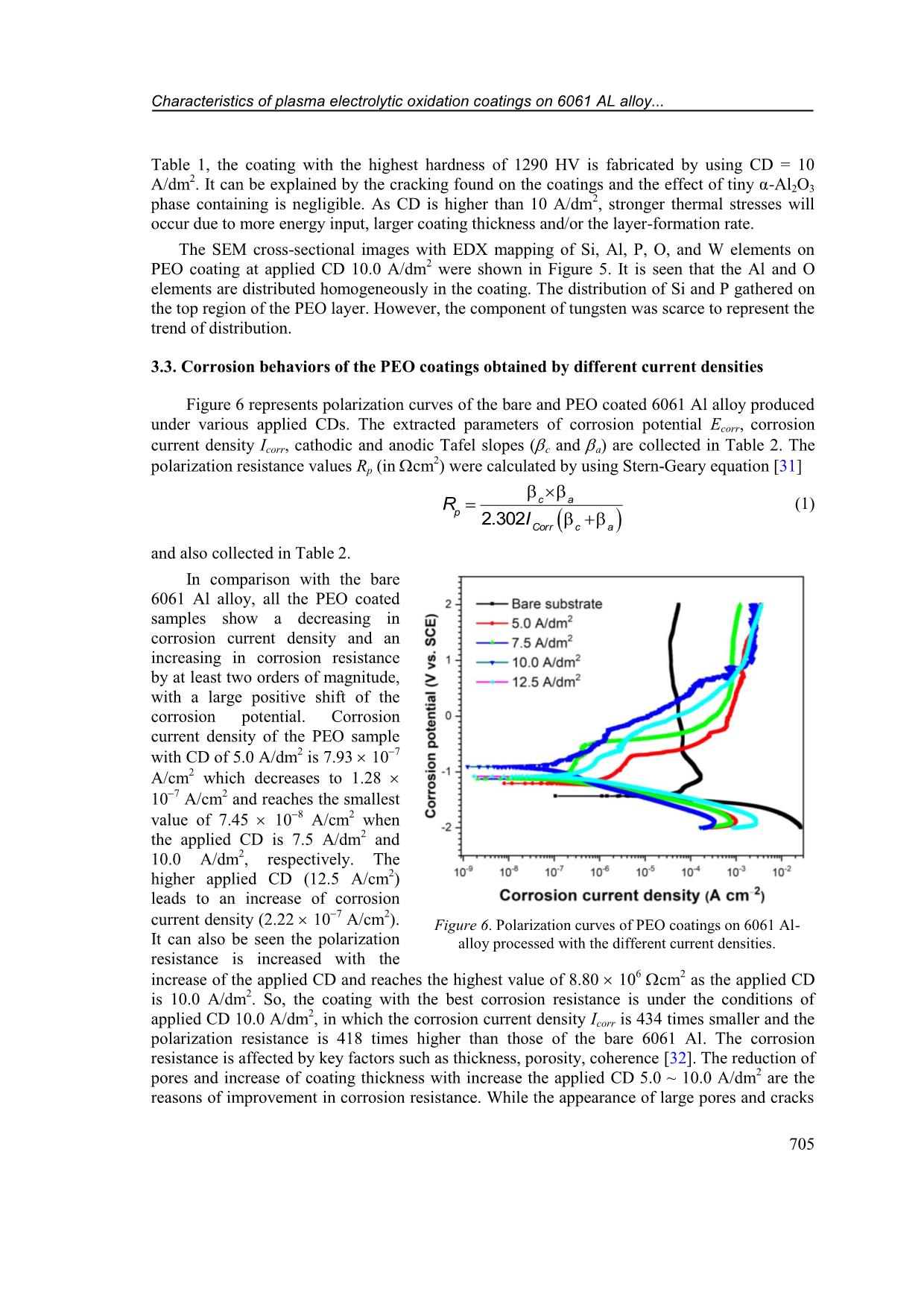
Trang 7
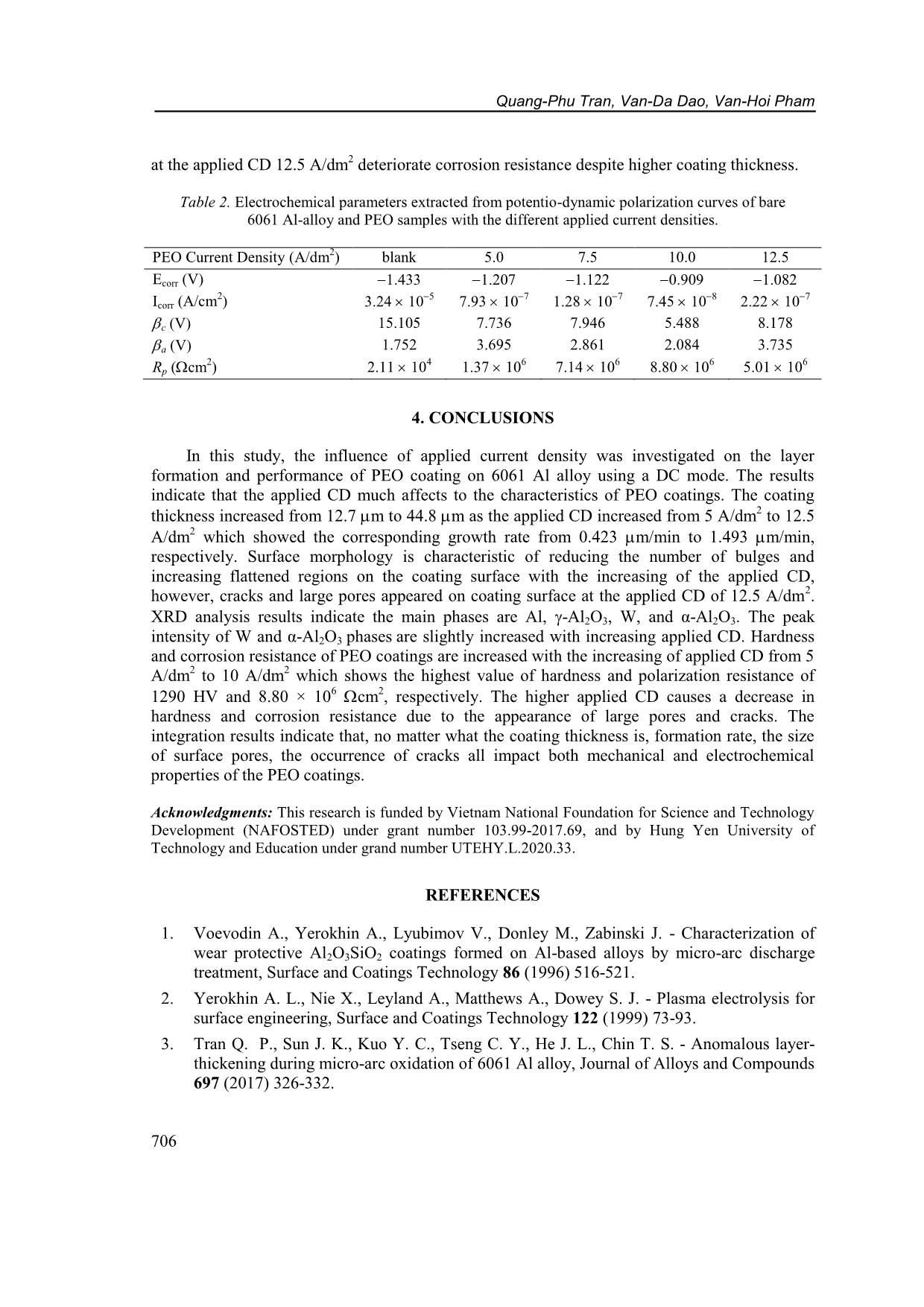
Trang 8
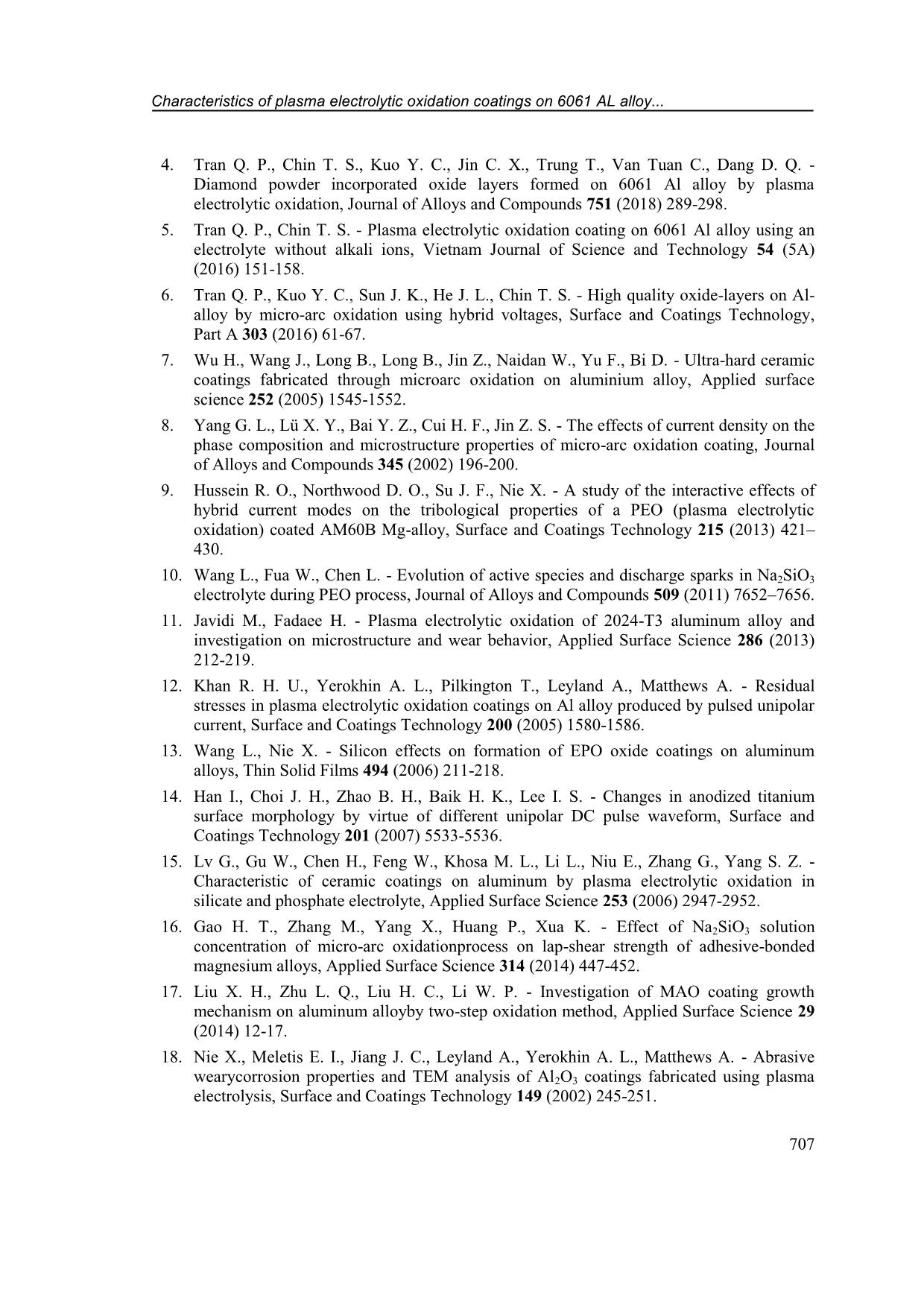
Trang 9
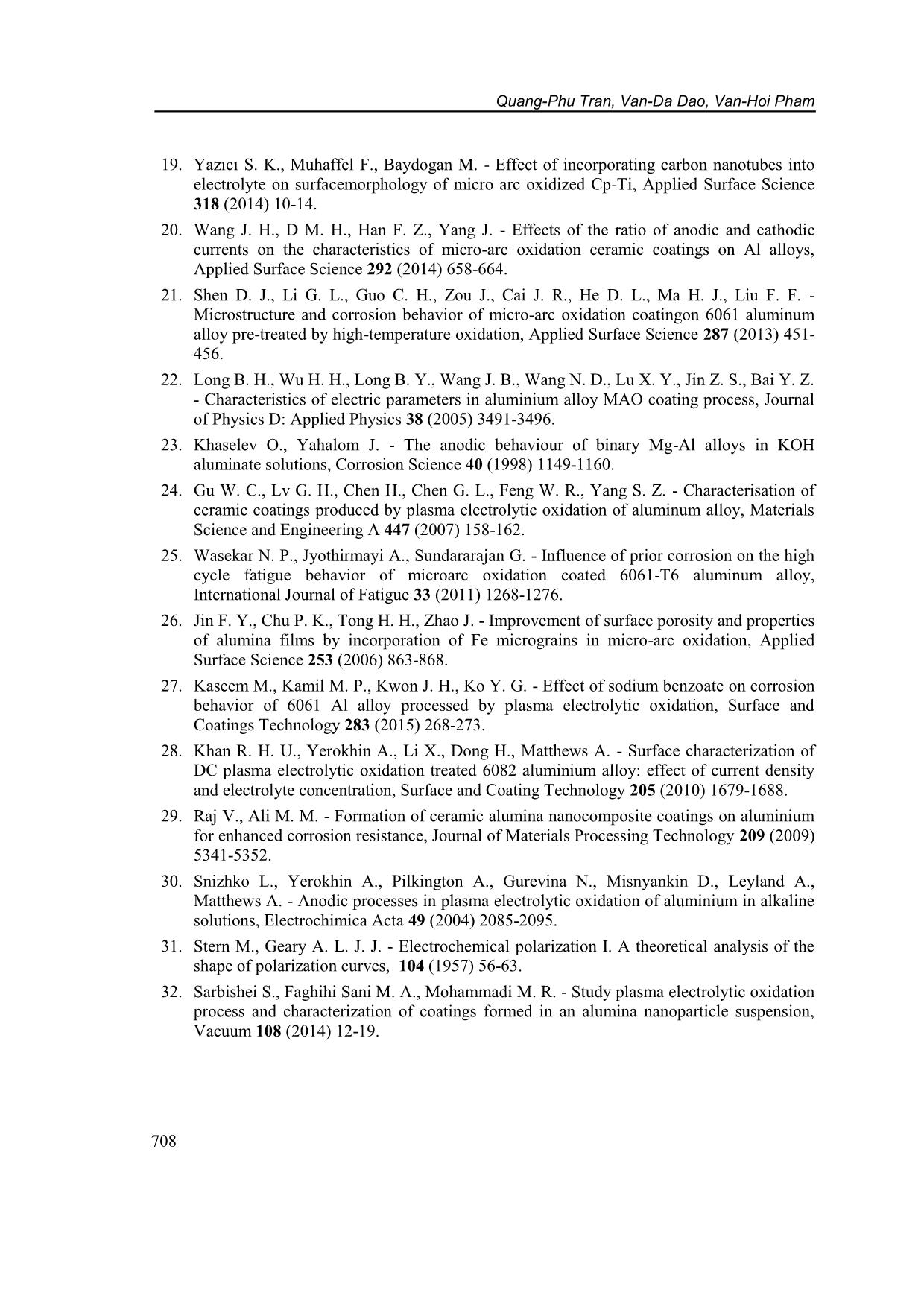
Trang 10
Tóm tắt nội dung tài liệu: Characteristics of plasma electrolytic oxidation coatings on 6061 al alloy prepared at different current densities
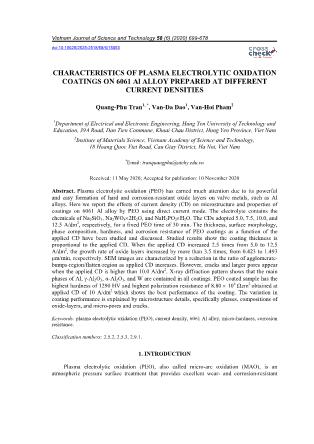
CD increased from 5 A/dm 2 to 12.5 A/dm 2 , respectively. Figure 2. Voltage transients during PEO processing under various applied current densities (5 ~ 12.5 A/dm 2 ). Characteristics of plasma electrolytic oxidation coatings on 6061 AL alloy... 703 Table 1. PEO coating characteristics under the different applied current densities. PEO Current Density (A/dm 2 ) blank 5.0 7.5 10.0 12.5 Respond voltage after 30 min. (V) - 481 484 493 502 Thickness (m) - 12.7 1.5 16.4 3.3 33.4 5.1 44.8 8.2 Growth rate (m/min) - 0.423 0.547 1.113 1.493 Micro-Hardness (HV) 60 1211 47 1247 36 1290 32 1248 66 3.2. Effects of current density on structure and hardness of the PEO layers Figure 3 shows surface morphology of Al-PEO coatings fabricated by different CDs. The images indicate that the ratio of agglomerate-bumps-region/flatten-region is higher with lower applied CD. This phenomenon is due to incomplete process occurring under lower applied energy. However, cracking occurs on coating surface under 12.5 A/dm 2 applied CD due to the thermal stress. On the other hand, the relatively large pores with less porosity only occur at the condition of 12.5 A/dm 2 . Figure 3. SEM images of surface morphology on PEO coating of 6061 Al-alloy under current density of (a) 5.0 A/dm 2 , (b) 7.5 A/dm 2 , (c) 10.0 A/dm 2 and (d) 12.5 A/dm 2 . Quang-Phu Tran, Van-Da Dao, Van-Hoi Pham 704 Figure 4. XRD patterns of PEO coatings on 6061 Al-alloy under various current densities: a) 5.0 A/dm 2 , b) 7.5 A/dm 2 , c) 10.0 A/dm 2 , and d) 12.5 A/dm 2 . XRD patterns of Al-PEO coatings under various current densities are shown in Figure 4. The XRD patterns indicate the main phases of Al (JCPDS card No. 04- 0787), -Al2O3 (JCPDS card No. 10-0425), W (JCPDS card No. 04- 0608), and α-Al2O3 (JCPDS card No. 10-0173). α-Al2O3 phase can be slightly identified when increasing CD, in which the input energy is high enough to cause recrystallization [2], however, the signal of α-Al2O3 pattern was still feeble even under the 12.5 A/dm 2 condition of this study. The intensity of metallic W phase increases obviously with increasing CD. With more α-Al2O3 and metallic W phase present, ideally the coating hardness should also be improved. However, as shown in Figure 5. Cross-sectional SEM image with elements mapping of PEO layer at applied current density of 10 A/dm 2 : (a) Si; (b) O; (c) Al; (d) W; e) P elements; and f) SEM micrograph image. Characteristics of plasma electrolytic oxidation coatings on 6061 AL alloy... 705 Table 1, the coating with the highest hardness of 1290 HV is fabricated by using CD = 10 A/dm 2. It can be explained by the cracking found on the coatings and the effect of tiny α-Al2O3 phase containing is negligible. As CD is higher than 10 A/dm 2 , stronger thermal stresses will occur due to more energy input, larger coating thickness and/or the layer-formation rate. The SEM cross-sectional images with EDX mapping of Si, Al, P, O, and W elements on PEO coating at applied CD 10.0 A/dm 2 were shown in Figure 5. It is seen that the Al and O elements are distributed homogeneously in the coating. The distribution of Si and P gathered on the top region of the PEO layer. However, the component of tungsten was scarce to represent the trend of distribution. 3.3. Corrosion behaviors of the PEO coatings obtained by different current densities Figure 6 represents polarization curves of the bare and PEO coated 6061 Al alloy produced under various applied CDs. The extracted parameters of corrosion potential Ecorr, corrosion current density Icorr, cathodic and anodic Tafel slopes (c and a) are collected in Table 2. The polarization resistance values Rp (in cm 2 ) were calculated by using Stern-Geary equation [31] 2.302 c a p Corr c a R I (1) and also collected in Table 2. In comparison with the bare 6061 Al alloy, all the PEO coated samples show a decreasing in corrosion current density and an increasing in corrosion resistance by at least two orders of magnitude, with a large positive shift of the corrosion potential. Corrosion current density of the PEO sample with CD of 5.0 A/dm 2 is 7.93 10 7 A/cm 2 which decreases to 1.28 10 7 A/cm 2 and reaches the smallest value of 7.45 10 8 A/cm2 when the applied CD is 7.5 A/dm 2 and 10.0 A/dm 2 , respectively. The higher applied CD (12.5 A/cm 2 ) leads to an increase of corrosion current density (2.22 10 7 A/cm2). It can also be seen the polarization resistance is increased with the increase of the applied CD and reaches the highest value of 8.80 106 cm2 as the applied CD is 10.0 A/dm 2 . So, the coating with the best corrosion resistance is under the conditions of applied CD 10.0 A/dm 2 , in which the corrosion current density Icorr is 434 times smaller and the polarization resistance is 418 times higher than those of the bare 6061 Al. The corrosion resistance is affected by key factors such as thickness, porosity, coherence [32]. The reduction of pores and increase of coating thickness with increase the applied CD 5.0 ~ 10.0 A/dm 2 are the reasons of improvement in corrosion resistance. While the appearance of large pores and cracks Figure 6. Polarization curves of PEO coatings on 6061 Al- alloy processed with the different current densities. Quang-Phu Tran, Van-Da Dao, Van-Hoi Pham 706 at the applied CD 12.5 A/dm 2 deteriorate corrosion resistance despite higher coating thickness. Table 2. Electrochemical parameters extracted from potentio-dynamic polarization curves of bare 6061 Al-alloy and PEO samples with the different applied current densities. PEO Current Density (A/dm 2 ) blank 5.0 7.5 10.0 12.5 Ecorr (V) 1.433 1.207 1.122 0.909 1.082 Icorr (A/cm 2 ) 3.24 10 5 7.93 10 7 1.28 10 7 7.45 10 8 2.22 10 7 c (V) 15.105 7.736 7.946 5.488 8.178 a (V) 1.752 3.695 2.861 2.084 3.735 Rp (cm 2 ) 2.11 104 1.37 106 7.14 106 8.80 106 5.01 106 4. CONCLUSIONS In this study, the influence of applied current density was investigated on the layer formation and performance of PEO coating on 6061 Al alloy using a DC mode. The results indicate that the applied CD much affects to the characteristics of PEO coatings. The coating thickness increased from 12.7 m to 44.8 m as the applied CD increased from 5 A/dm2 to 12.5 A/dm 2 which showed the corresponding growth rate from 0.423 m/min to 1.493 m/min, respectively. Surface morphology is characteristic of reducing the number of bulges and increasing flattened regions on the coating surface with the increasing of the applied CD, however, cracks and large pores appeared on coating surface at the applied CD of 12.5 A/dm 2 . XRD analysis results indicate the main phases are Al, -Al2O3, W, and α-Al2O3. The peak intensity of W and α-Al2O3 phases are slightly increased with increasing applied CD. Hardness and corrosion resistance of PEO coatings are increased with the increasing of applied CD from 5 A/dm 2 to 10 A/dm 2 which shows the highest value of hardness and polarization resistance of 1290 HV and 8.80 × 10 6 cm2, respectively. The higher applied CD causes a decrease in hardness and corrosion resistance due to the appearance of large pores and cracks. The integration results indicate that, no matter what the coating thickness is, formation rate, the size of surface pores, the occurrence of cracks all impact both mechanical and electrochemical properties of the PEO coatings. Acknowledgments: This research is funded by Vietnam National Foundation for Science and Technology Development (NAFOSTED) under grant number 103.99-2017.69, and by Hung Yen University of Technology and Education under grand number UTEHY.L.2020.33. REFERENCES 1. Voevodin A., Yerokhin A., Lyubimov V., Donley M., Zabinski J. - Characterization of wear protective Al2O3SiO2 coatings formed on Al-based alloys by micro-arc discharge treatment, Surface and Coatings Technology 86 (1996) 516-521. 2. Yerokhin A. L., Nie X., Leyland A., Matthews A., Dowey S. J. - Plasma electrolysis for surface engineering, Surface and Coatings Technology 122 (1999) 73-93. 3. Tran Q. P., Sun J. K., Kuo Y. C., Tseng C. Y., He J. L., Chin T. S. - Anomalous layer- thickening during micro-arc oxidation of 6061 Al alloy, Journal of Alloys and Compounds 697 (2017) 326-332. Characteristics of plasma electrolytic oxidation coatings on 6061 AL alloy... 707 4. Tran Q. P., Chin T. S., Kuo Y. C., Jin C. X., Trung T., Van Tuan C., Dang D. Q. - Diamond powder incorporated oxide layers formed on 6061 Al alloy by plasma electrolytic oxidation, Journal of Alloys and Compounds 751 (2018) 289-298. 5. Tran Q. P., Chin T. S. - Plasma electrolytic oxidation coating on 6061 Al alloy using an electrolyte without alkali ions, Vietnam Journal of Science and Technology 54 (5A) (2016) 151-158. 6. Tran Q. P., Kuo Y. C., Sun J. K., He J. L., Chin T. S. - High quality oxide-layers on Al- alloy by micro-arc oxidation using hybrid voltages, Surface and Coatings Technology, Part A 303 (2016) 61-67. 7. Wu H., Wang J., Long B., Long B., Jin Z., Naidan W., Yu F., Bi D. - Ultra-hard ceramic coatings fabricated through microarc oxidation on aluminium alloy, Applied surface science 252 (2005) 1545-1552. 8. Yang G. L., Lü X. Y., Bai Y. Z., Cui H. F., Jin Z. S. - The effects of current density on the phase composition and microstructure properties of micro-arc oxidation coating, Journal of Alloys and Compounds 345 (2002) 196-200. 9. Hussein R. O., Northwood D. O., Su J. F., Nie X. - A study of the interactive effects of hybrid current modes on the tribological properties of a PEO (plasma electrolytic oxidation) coated AM60B Mg-alloy, Surface and Coatings Technology 215 (2013) 421– 430. 10. Wang L., Fua W., Chen L. - Evolution of active species and discharge sparks in Na2SiO3 electrolyte during PEO process, Journal of Alloys and Compounds 509 (2011) 7652–7656. 11. Javidi M., Fadaee H. - Plasma electrolytic oxidation of 2024-T3 aluminum alloy and investigation on microstructure and wear behavior, Applied Surface Science 286 (2013) 212-219. 12. Khan R. H. U., Yerokhin A. L., Pilkington T., Leyland A., Matthews A. - Residual stresses in plasma electrolytic oxidation coatings on Al alloy produced by pulsed unipolar current, Surface and Coatings Technology 200 (2005) 1580-1586. 13. Wang L., Nie X. - Silicon effects on formation of EPO oxide coatings on aluminum alloys, Thin Solid Films 494 (2006) 211-218. 14. Han I., Choi J. H., Zhao B. H., Baik H. K., Lee I. S. - Changes in anodized titanium surface morphology by virtue of different unipolar DC pulse waveform, Surface and Coatings Technology 201 (2007) 5533-5536. 15. Lv G., Gu W., Chen H., Feng W., Khosa M. L., Li L., Niu E., Zhang G., Yang S. Z. - Characteristic of ceramic coatings on aluminum by plasma electrolytic oxidation in silicate and phosphate electrolyte, Applied Surface Science 253 (2006) 2947-2952. 16. Gao H. T., Zhang M., Yang X., Huang P., Xua K. - Effect of Na2SiO3 solution concentration of micro-arc oxidationprocess on lap-shear strength of adhesive-bonded magnesium alloys, Applied Surface Science 314 (2014) 447-452. 17. Liu X. H., Zhu L. Q., Liu H. C., Li W. P. - Investigation of MAO coating growth mechanism on aluminum alloyby two-step oxidation method, Applied Surface Science 29 (2014) 12-17. 18. Nie X., Meletis E. I., Jiang J. C., Leyland A., Yerokhin A. L., Matthews A. - Abrasive wearycorrosion properties and TEM analysis of Al2O3 coatings fabricated using plasma electrolysis, Surface and Coatings Technology 149 (2002) 245-251. Quang-Phu Tran, Van-Da Dao, Van-Hoi Pham 708 19. Yazıcı S. K., Muhaffel F., Baydogan M. - Effect of incorporating carbon nanotubes into electrolyte on surfacemorphology of micro arc oxidized Cp-Ti, Applied Surface Science 318 (2014) 10-14. 20. Wang J. H., D M. H., Han F. Z., Yang J. - Effects of the ratio of anodic and cathodic currents on the characteristics of micro-arc oxidation ceramic coatings on Al alloys, Applied Surface Science 292 (2014) 658-664. 21. Shen D. J., Li G. L., Guo C. H., Zou J., Cai J. R., He D. L., Ma H. J., Liu F. F. - Microstructure and corrosion behavior of micro-arc oxidation coatingon 6061 aluminum alloy pre-treated by high-temperature oxidation, Applied Surface Science 287 (2013) 451- 456. 22. Long B. H., Wu H. H., Long B. Y., Wang J. B., Wang N. D., Lu X. Y., Jin Z. S., Bai Y. Z. - Characteristics of electric parameters in aluminium alloy MAO coating process, Journal of Physics D: Applied Physics 38 (2005) 3491-3496. 23. Khaselev O., Yahalom J. - The anodic behaviour of binary Mg-Al alloys in KOH aluminate solutions, Corrosion Science 40 (1998) 1149-1160. 24. Gu W. C., Lv G. H., Chen H., Chen G. L., Feng W. R., Yang S. Z. - Characterisation of ceramic coatings produced by plasma electrolytic oxidation of aluminum alloy, Materials Science and Engineering A 447 (2007) 158-162. 25. Wasekar N. P., Jyothirmayi A., Sundararajan G. - Influence of prior corrosion on the high cycle fatigue behavior of microarc oxidation coated 6061-T6 aluminum alloy, International Journal of Fatigue 33 (2011) 1268-1276. 26. Jin F. Y., Chu P. K., Tong H. H., Zhao J. - Improvement of surface porosity and properties of alumina films by incorporation of Fe micrograins in micro-arc oxidation, Applied Surface Science 253 (2006) 863-868. 27. Kaseem M., Kamil M. P., Kwon J. H., Ko Y. G. - Effect of sodium benzoate on corrosion behavior of 6061 Al alloy processed by plasma electrolytic oxidation, Surface and Coatings Technology 283 (2015) 268-273. 28. Khan R. H. U., Yerokhin A., Li X., Dong H., Matthews A. - Surface characterization of DC plasma electrolytic oxidation treated 6082 aluminium alloy: effect of current density and electrolyte concentration, Surface and Coating Technology 205 (2010) 1679-1688. 29. Raj V., Ali M. M. - Formation of ceramic alumina nanocomposite coatings on aluminium for enhanced corrosion resistance, Journal of Materials Processing Technology 209 (2009) 5341-5352. 30. Snizhko L., Yerokhin A., Pilkington A., Gurevina N., Misnyankin D., Leyland A., Matthews A. - Anodic processes in plasma electrolytic oxidation of aluminium in alkaline solutions, Electrochimica Acta 49 (2004) 2085-2095. 31. Stern M., Geary A. L. J. J. - Electrochemical polarization I. A theoretical analysis of the shape of polarization curves, 104 (1957) 56-63. 32. Sarbishei S., Faghihi Sani M. A., Mohammadi M. R. - Study plasma electrolytic oxidation process and characterization of coatings formed in an alumina nanoparticle suspension, Vacuum 108 (2014) 12-19.
File đính kèm:
characteristics_of_plasma_electrolytic_oxidation_coatings_on.pdf