An enhanced fault tolerant control against current sensor failures in induction motor drive by applying space vector
In this paper, an enhanced active
fault-tolerant control (FTC) is proposed to solve
a current sensor failure in the induction motor
drive (IMD) using two current sensors. The
proposed FTC method applies only one observer
to diagnose the faults and recongure the
control signals by the space stator current. The
diagnosis function is made up of a comparison
algorithm between the measured current space
vector and the estimated space vector. Then,
incorrect feedback stator currents are replaced
by the estimated values in the reconguration
function. The amplitude of a healthy measured
current is applied to adjusted the accuracy of
estimated current signals. The IMD uses the
eld-oriented control (FOC) technique to control
the speed and torque. The eectiveness in stabilizing the IMD system when a current sensor
error occurs is veried by various simulations
in the Matlab-Simulink environment.
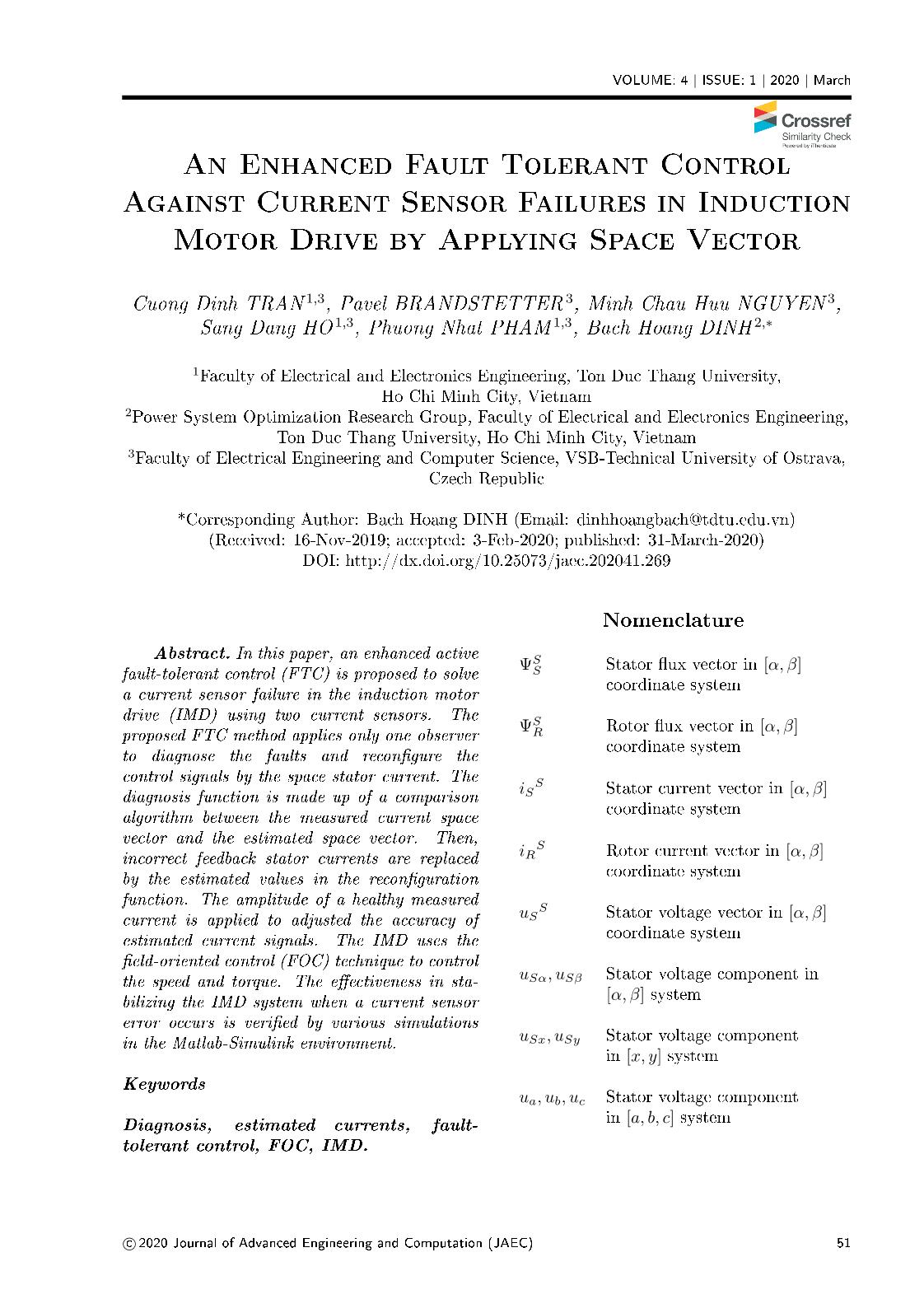
Trang 1
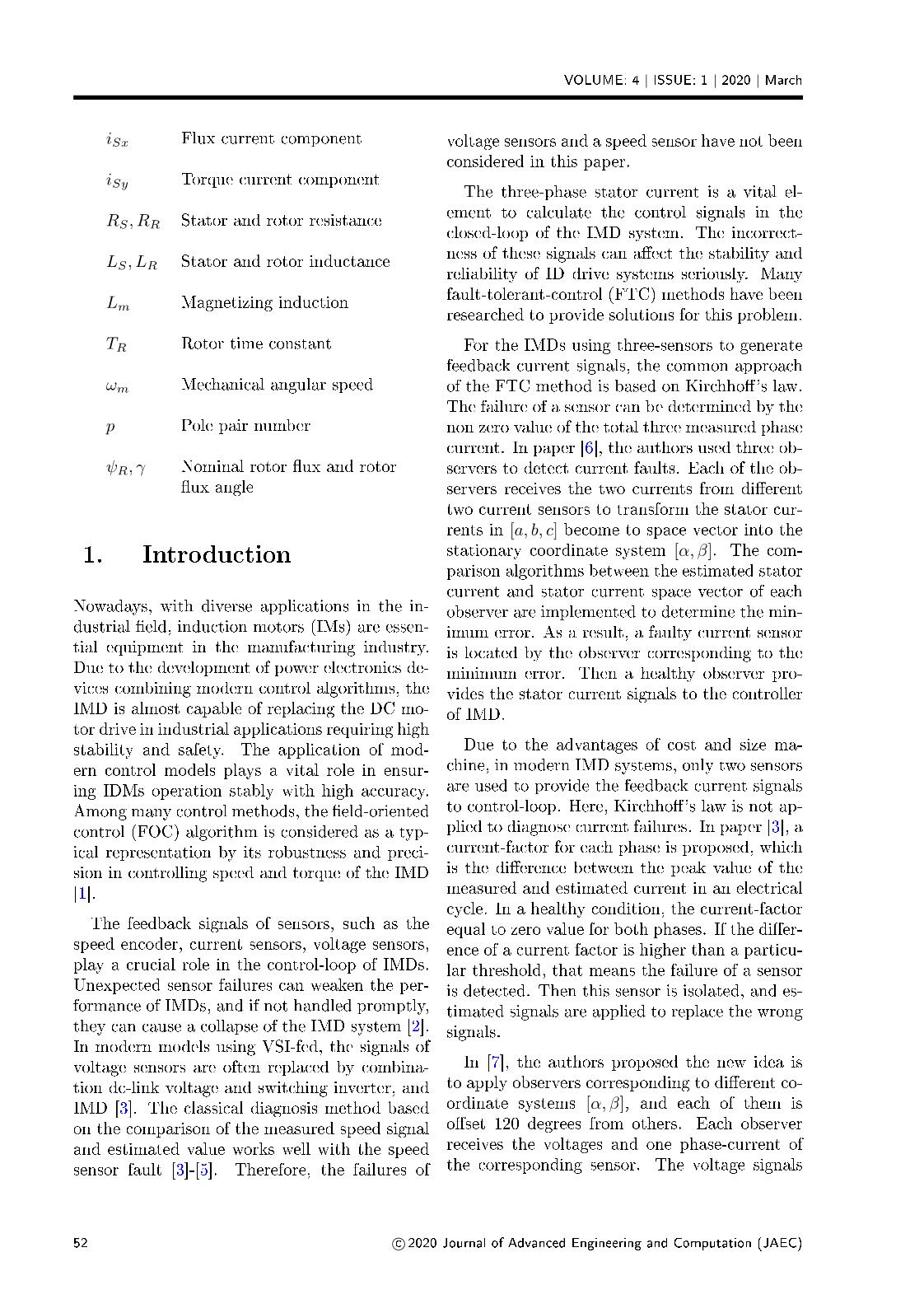
Trang 2
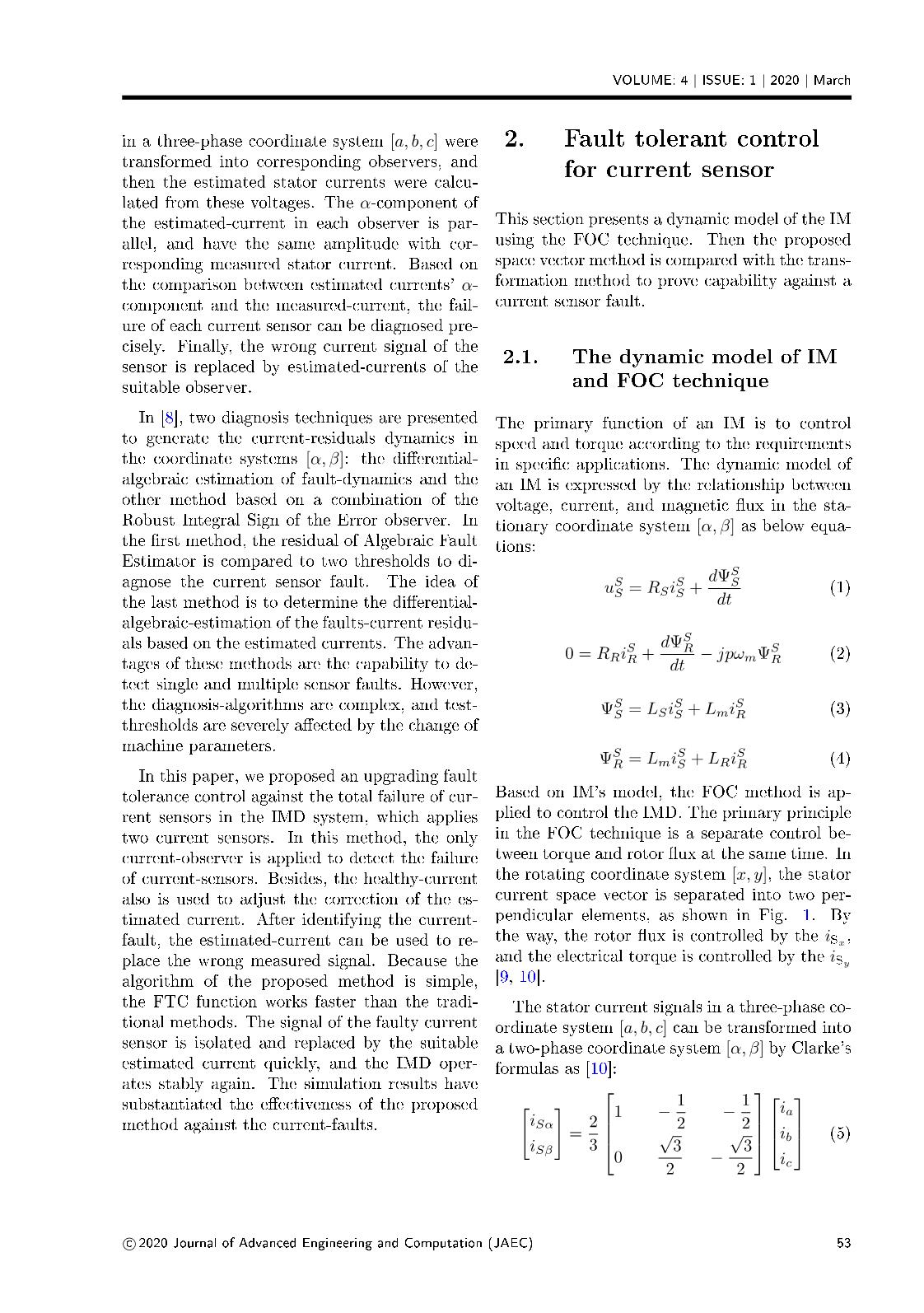
Trang 3
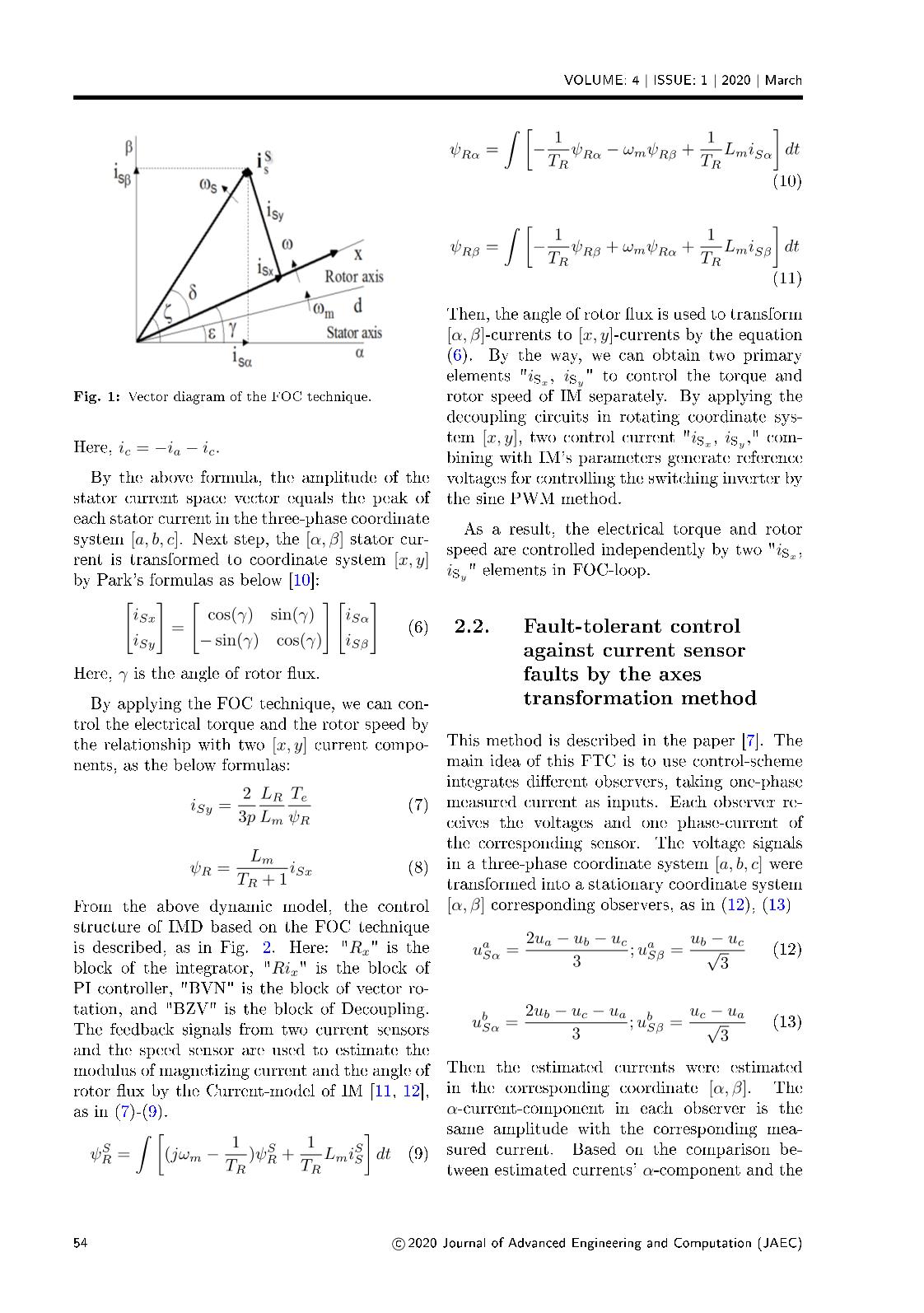
Trang 4
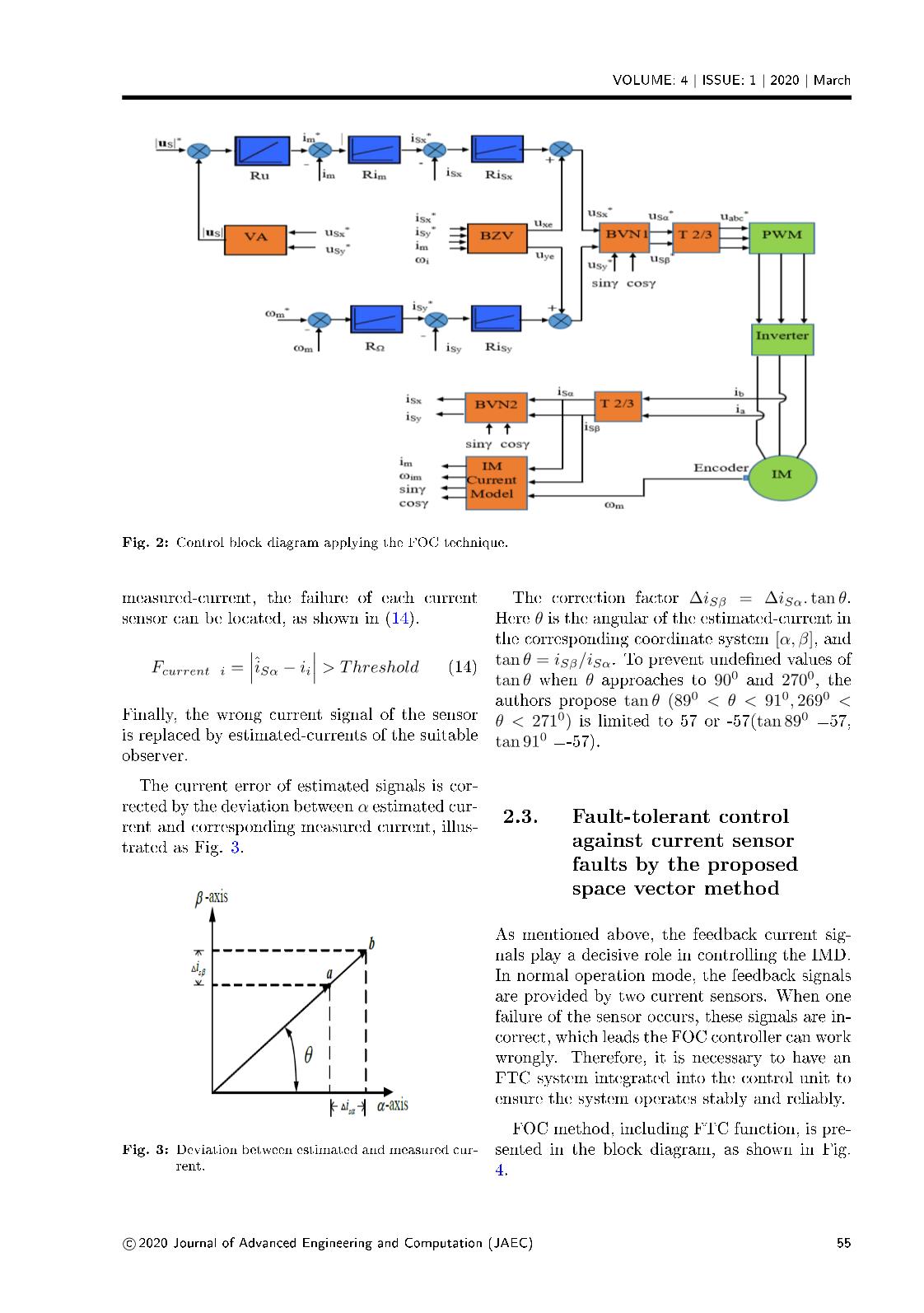
Trang 5
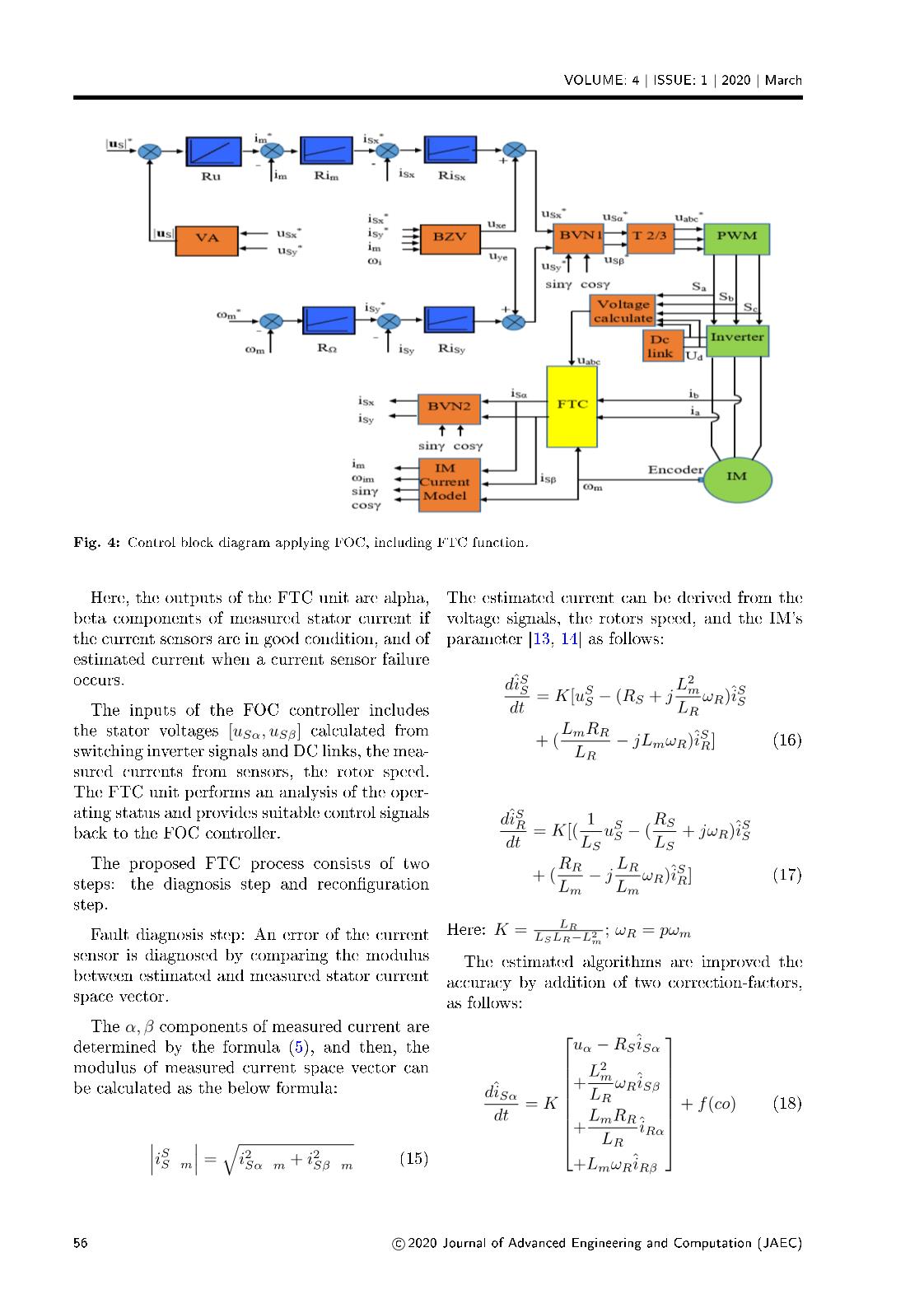
Trang 6

Trang 7
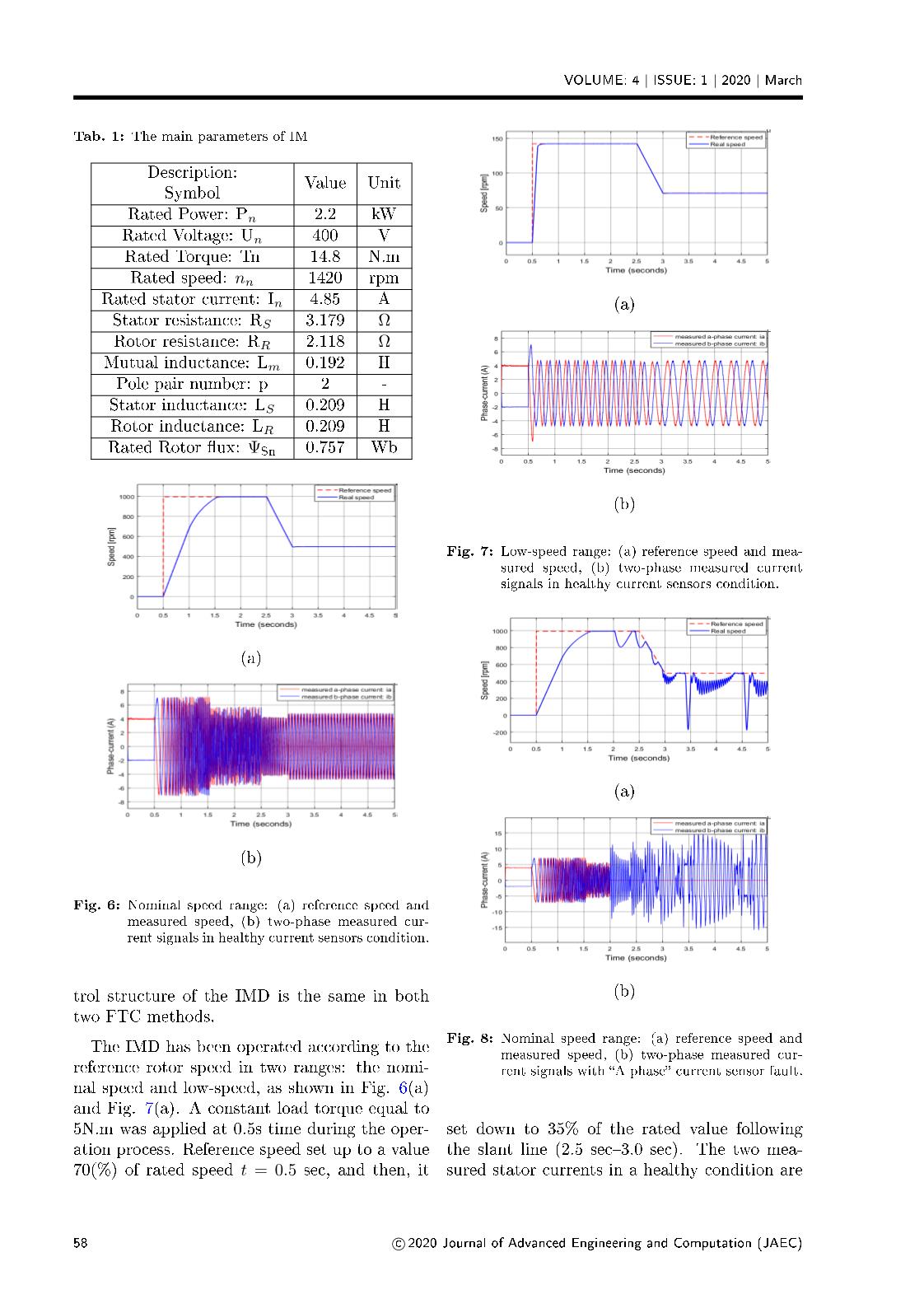
Trang 8
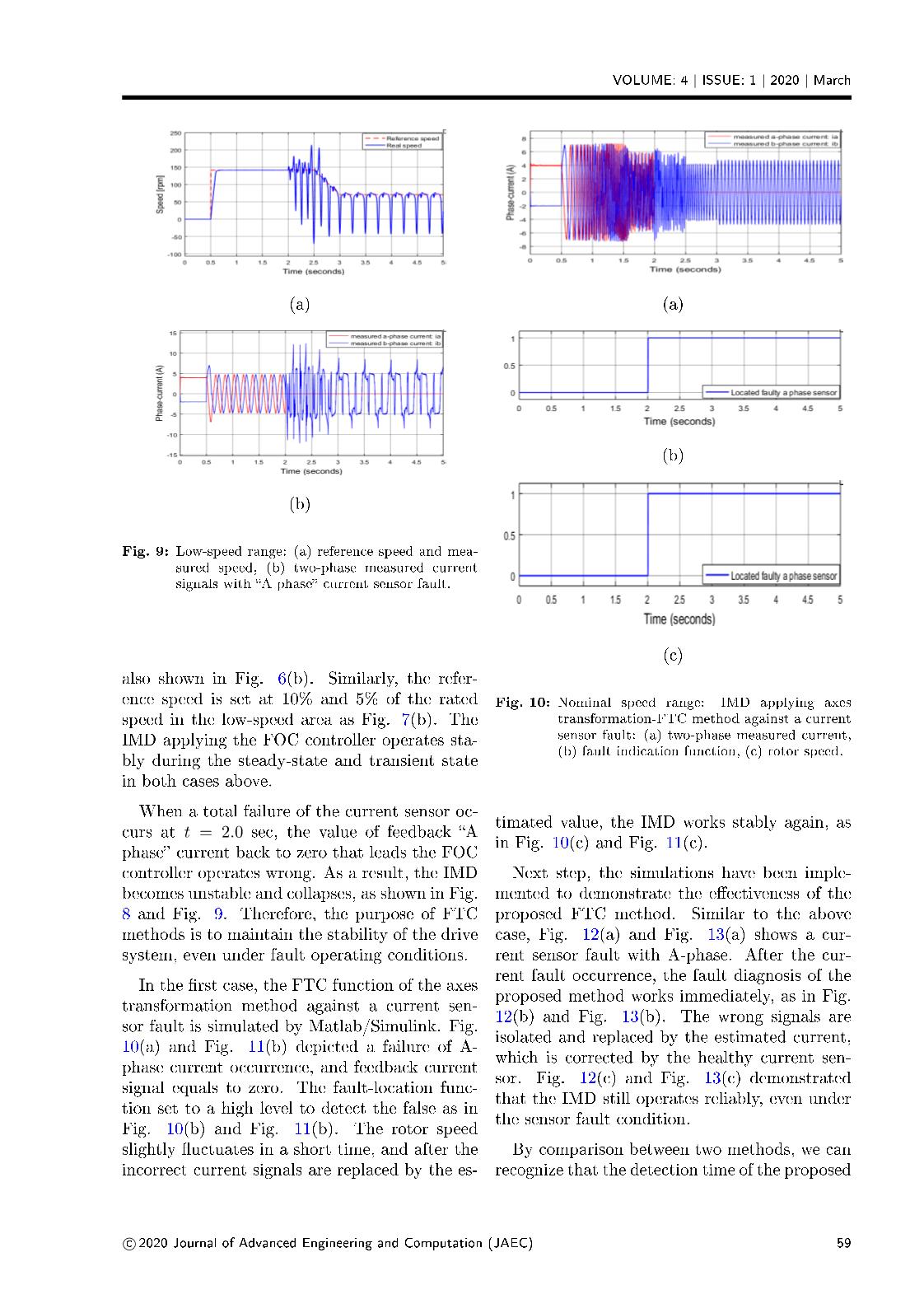
Trang 9
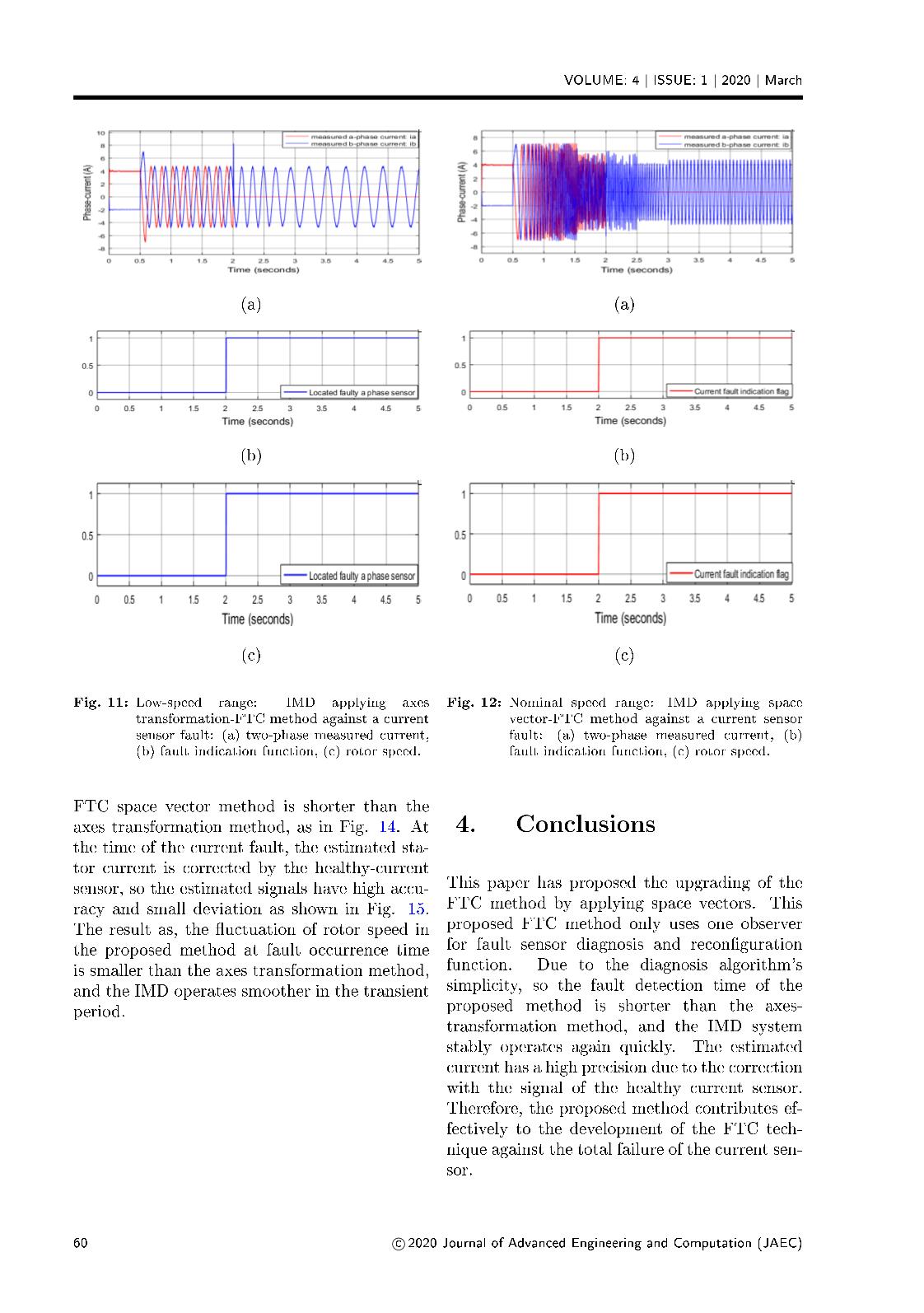
Trang 10
Tải về để xem bản đầy đủ
Tóm tắt nội dung tài liệu: An enhanced fault tolerant control against current sensor failures in induction motor drive by applying space vector
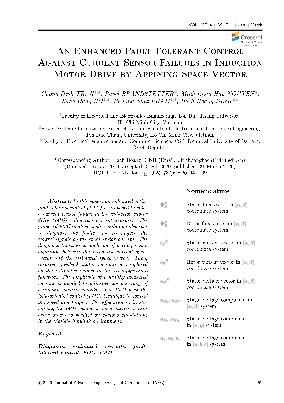
f measured and the estimated current space vec- tor, as follows: IF : ∣∣∣∣∣∣iSS_m∣∣∣− ∣∣∣ˆiSS∣∣∣∣∣∣ > Tthreshold THEN : Fcurrent = 1;ELSE : Fcurrent = 0. (24) T threshold : is a maximum difference between the amplitude of measured current space vector and magnitude of the estimated current space vector. In this paper, T threshold is proposed as a 10(%) value of rated current. Reconfiguration step: after the total-current- failure is detected, the FTC controller isolates the wrong feedback signals of current sensors, and replace them by the estimated current signs. As a result, the IMD operates stably with the estimated current signals, which are corrected by the remain healthy current sensor. Finally, the FTC unit determines the fault state and provides the feedback current to the FOC controller as the flowchart in Fig. 5: Fig. 5: Flowchart of FTC unit's function. 3. Simulation results In this part, simulations in Matlab/Simulink have been implemented and compared between the axes transformation method and space vec- tor method. Here, the model induction motor with machine parameters listed in Tab. 1. The simulations have been implemented at the normal reference speed zone. The IMD is controlled by the FOC technique in both healthy sensor conditions and false conditions. The con- c© 2020 Journal of Advanced Engineering and Computation (JAEC) 57 VOLUME: 4 | ISSUE: 1 | 2020 | March Tab. 1: The main parameters of IM Description: Symbol Value Unit Rated Power: Pn 2.2 kW Rated Voltage: Un 400 V Rated Torque: Tn 14.8 N.m Rated speed: nn 1420 rpm Rated stator current: In 4.85 A Stator resistance: RS 3.179 Ω Rotor resistance: RR 2.118 Ω Mutual inductance: Lm 0.192 H Pole pair number: p 2 - Stator inductance: LS 0.209 H Rotor inductance: LR 0.209 H Rated Rotor flux: Ψ Sn 0.757 Wb (a) (b) Fig. 6: Nominal speed range: (a) reference speed and measured speed, (b) two-phase measured cur- rent signals in healthy current sensors condition. trol structure of the IMD is the same in both two FTC methods. The IMD has been operated according to the reference rotor speed in two ranges: the nomi- nal speed and low-speed, as shown in Fig. 6(a) and Fig. 7(a). A constant load torque equal to 5N.m was applied at 0.5s time during the oper- ation process. Reference speed set up to a value 70(%) of rated speed t = 0.5 sec, and then, it (a) (b) Fig. 7: Low-speed range: (a) reference speed and mea- sured speed, (b) two-phase measured current signals in healthy current sensors condition. (a) (b) Fig. 8: Nominal speed range: (a) reference speed and measured speed, (b) two-phase measured cur- rent signals with A phase current sensor fault. set down to 35% of the rated value following the slant line (2.5 sec3.0 sec). The two mea- sured stator currents in a healthy condition are 58 c© 2020 Journal of Advanced Engineering and Computation (JAEC) VOLUME: 4 | ISSUE: 1 | 2020 | March (a) (b) Fig. 9: Low-speed range: (a) reference speed and mea- sured speed, (b) two-phase measured current signals with A phase current sensor fault. also shown in Fig. 6(b). Similarly, the refer- ence speed is set at 10% and 5% of the rated speed in the low-speed area as Fig. 7(b). The IMD applying the FOC controller operates sta- bly during the steady-state and transient state in both cases above. When a total failure of the current sensor oc- curs at t = 2.0 sec, the value of feedback A phase current back to zero that leads the FOC controller operates wrong. As a result, the IMD becomes unstable and collapses, as shown in Fig. 8 and Fig. 9. Therefore, the purpose of FTC methods is to maintain the stability of the drive system, even under fault operating conditions. In the first case, the FTC function of the axes transformation method against a current sen- sor fault is simulated by Matlab/Simulink. Fig. 10(a) and Fig. 11(b) depicted a failure of A- phase current occurrence, and feedback current signal equals to zero. The fault-location func- tion set to a high level to detect the false as in Fig. 10(b) and Fig. 11(b). The rotor speed slightly fluctuates in a short time, and after the incorrect current signals are replaced by the es- (a) (b) (c) Fig. 10: Nominal speed range: IMD applying axes transformation-FTC method against a current sensor fault: (a) two-phase measured current, (b) fault indication function, (c) rotor speed. timated value, the IMD works stably again, as in Fig. 10(c) and Fig. 11(c). Next step, the simulations have been imple- mented to demonstrate the effectiveness of the proposed FTC method. Similar to the above case, Fig. 12(a) and Fig. 13(a) shows a cur- rent sensor fault with A-phase. After the cur- rent fault occurrence, the fault diagnosis of the proposed method works immediately, as in Fig. 12(b) and Fig. 13(b). The wrong signals are isolated and replaced by the estimated current, which is corrected by the healthy current sen- sor. Fig. 12(c) and Fig. 13(c) demonstrated that the IMD still operates reliably, even under the sensor fault condition. By comparison between two methods, we can recognize that the detection time of the proposed c© 2020 Journal of Advanced Engineering and Computation (JAEC) 59 VOLUME: 4 | ISSUE: 1 | 2020 | March (a) (b) (c) Fig. 11: Low-speed range: IMD applying axes transformation-FTC method against a current sensor fault: (a) two-phase measured current, (b) fault indication function, (c) rotor speed. FTC space vector method is shorter than the axes transformation method, as in Fig. 14. At the time of the current fault, the estimated sta- tor current is corrected by the healthy-current sensor, so the estimated signals have high accu- racy and small deviation as shown in Fig. 15. The result as, the fluctuation of rotor speed in the proposed method at fault occurrence time is smaller than the axes transformation method, and the IMD operates smoother in the transient period. (a) (b) (c) Fig. 12: Nominal speed range: IMD applying space vector-FTC method against a current sensor fault: (a) two-phase measured current, (b) fault indication function, (c) rotor speed. 4. Conclusions This paper has proposed the upgrading of the FTC method by applying space vectors. This proposed FTC method only uses one observer for fault sensor diagnosis and reconfiguration function. Due to the diagnosis algorithm's simplicity, so the fault detection time of the proposed method is shorter than the axes- transformation method, and the IMD system stably operates again quickly. The estimated current has a high precision due to the correction with the signal of the healthy current sensor. Therefore, the proposed method contributes ef- fectively to the development of the FTC tech- nique against the total failure of the current sen- sor. 60 c© 2020 Journal of Advanced Engineering and Computation (JAEC) VOLUME: 4 | ISSUE: 1 | 2020 | March (a) (b) (c) Fig. 13: Low-speed range: IMD applying space vector- FTC method against a current sensor fault: (a) two-phase measured current, (b) fault indica- tion function, (c) rotor speed. Acknowledgement This research is funded by Graduate Schol- arship for Master and Doctoral Programs of Ton Duc Thang University, website: This work was supported by Project reg. no. SP2020/128 - Research and development of sophisticated con- trol methods for the area of electric controlled drives of VSB-Technical University of Ostrava, 2020. (a) (b) Fig. 14: Comparison of detection time between the axes transformation-FTC and space vector- FTC method in (a) nominal speed range and (b) low-speed range. (a) (b) Fig. 15: The deviation between the estimated current and measured current of the healthy sensor in (a) nominal speed range and (b) low-speed range. References [1] Regaya, C. B., Farhani, F., Zaafouri, A., & Chaari, A. (2018). A novel adaptive control method for induction motor based on Back- stepping approach using dSpace DS 1104 control board. Mechanical Systems and Sig- nal Processing, 100, 466-481. [2] Liu, Y., Stettenbenz, M., & Bazzi, A. M. (2018). Smooth Fault-Tolerant Control of c© 2020 Journal of Advanced Engineering and Computation (JAEC) 61 VOLUME: 4 | ISSUE: 1 | 2020 | March Induction Motor Drives with Sensor Fail- ures. IEEE Transactions on Power Elec- tronics, 34(4), 3544-3552. [3] Najafabadi, T. A., Salmasi, F. R., & Jabehdar-Maralani, P. (2010). Detection and isolation of speed-, DC-link voltage-, and current-sensor faults based on an adap- tive observer in induction-motor drives. IEEE Transactions on Industrial Electron- ics, 58(5), 1662-1672. [4] Klimkowski, K., & Dybkowski, M. (2016). A fault tolerant control structure for an induction motor drive system. automatika, 57(3), 638-647. [5] Chakraborty, C., & Verma, V. (2014). Speed and current sensor fault detec- tion and isolation technique for induc- tion motor drive using axes transformation. IEEE Transactions on Industrial Electron- ics, 62(3), 1943-1954. [6] Baghli, L., Poure, P., & Rezzoug, A. (2005, September). Sensor fault detection for fault tolerant vector controlled induction ma- chine. In 2005 European Conference on Power Electronics and Applications (pp. 10- pp). IEEE. [7] Yu, Y., Zhao, Y., Wang, B., Huang, X., & Xu, D. (2017). Current sensor fault di- agnosis and tolerant control for VSI-based induction motor drives. IEEE Transactions on Power Electronics, 33(5), 4238-4248. [8] Rkhissi-Kammoun, Y., Ghommam, J., Boukhnifer, M., & Mnif, F. (2019). Two current sensor fault detection and isolation schemes for induction motor drives using al- gebraic estimation approach. Mathematics and Computers in Simulation, 157, 39-62. [9] Kohlrusz, G., & Fodor, D. (2011). Compar- ison of scalar and vector control strategies of induction motors. Hungarian Journal of Industry and Chemistry, 39(2), 265-270. [10] Melentjev, S., Belahcen, A., Kallaste, A., & Vaimann, T. (2014, October). Overview of control methods of reluctance machines with sensors and sensorless. In 2014 55th In- ternational Scientific Conference on Power and Electrical Engineering of Riga Tech- nical University (RTUCON) (pp. 26-29). IEEE. [11] Brandstetter, P., & Kuchar, M. (2015, May). Rotor flux estimation using voltage model of induction motor. In 2015 16th In- ternational Scientific Conference on Elec- tric Power Engineering (EPE) (pp. 246- 250). IEEE. [12] Brand²tetter, P. (2012). Sensorless control of induction motor using modified MRAS. In International Review of Electrical Engi- neering (I.R.E.E), 7(3), 4404-4411. [13] Tran, C. D., Brandstetter, P., Ho, S. D., Tran, T. C., Nguyen, M. C. H., Phan, H. X., & Dinh, B. H. (2018, September). Im- proving Fault Tolerant Control to the one current sensor failures for induction motor drives. In International Conference on Ad- vanced Engineering Theory and Applica- tions (pp. 789-798). Springer, Cham. [14] Tran, C. D., Brandstetter, P., Dinh, B. H., Ho, S. D., & Nguyen, M. H. C. (2018). Current-Sensorless Method for Speed Con- trol of Induction Motor Based on Hysteresis Pulse Width Modulation Technique. Jour- nal of Advanced Engineering and Compu- tation, 2(4), 271-280. About Authors Cuong Dinh TRAN was born in Ho Chi Minh, Vietnam. He graduated from the Viet- nam National University - Ho Chi Minh City - University of Technology. He received his B.E. and M.E. degrees in electrical electronics power engineering in 2005 and 2008, respec- tively. Now, he is teaching at the department of electrical and electronics engineering, Ton Duc Thang University, Ho Chi Minh city, Vietnam. His research interests include modern control methods of electrical drives, automatic control system, intelligent control system, operation and control power system. 62 c© 2020 Journal of Advanced Engineering and Computation (JAEC) VOLUME: 4 | ISSUE: 1 | 2020 | March Pavel BRANDSTETTER was born in Ostrava, Czech Republic, 1955, 1 June. He received the M.Sc. and Ph.D. degrees in Electrical Engineering from Brno University of Technology, Czech Republic, in 1979 and 1987, respectively. He is currently full professor in Electrical Machines, Apparatus and Drives and dean of Faculty of Electrical Engineering and Computer Science at VSBTechnical University of Ostrava. His current research interests are applied electronics and modern control methods of electrical drives. Since 2000 he has performed research in field of modern control methods for AC motors, for example sensorless control, applications of artificial intelligence in control of AC drives. Minh Chau Huu NGUYEN was born in Binh Duong, Vietnam. He graduated from the Military Technical Academy, Vietnam. He received his M.E. degrees in Automation engi- neering in 2012. Now, he is researching at the Faculty of Electrical Engineering & Computer Science, VSB Technical University of Ostrava, Czech Republic. His research interests include an automatic control system, intelligent control system and electrical machine, apparatus and drives. Sang Dang HO received his B.Eng. and M.Eng degrees in Electrical Engineering from Ho Chi Minh University of Technology, Ho Chi Minh city, Vietnam in 2001 and 2008, respectively. Now, he is teaching at department of electrical and electronics engineering, Ton Duc Thang university, Ho Chi Minh city, Viet- nam. His research interests include optimization of power system and electric machines control. Phuong Nhat PHAM was born in Tien Giang, Vietnam. He graduated from the University of Technical Education Ho Chi Minh City, Viet Nam. He received MSc. degrees in Electrical Equipment, Network and Power Station in 2006. Now, he is teaching at the department of electrical and electronics engi- neering, Ton Duc Thang University, Ho Chi Minh City, Vietnam. His research interests include Evolutionary algorithm, intelligent con- trol system, operation and control power system. Bach Hoang DINH received the Ph.D degree in Electrical Engineering from Heriot- Watt University, Edinburgh, United Kingdom in 2009. He received the B.E. and the M.E. degrees in Electrical Engineering from Vietnam National University - Hochiminh City in 1995 and 1998, respectively. Bach Dinh is currently the head of Electrical Engineering Department, Faculty of Electrical-Electronic Engineering at Ton Duc Thang University. His research interests are intelligent and optimal control, computer vision, robotics, power electronics, SCADA and industrial communication net- works. He is a member of the IEEE Industrial Electronics Society. "This is an Open Access article distributed under the terms of the Creative Commons Attribution License, which permits unrestricted use, distribution, and reproduction in any medium provided the original work is properly cited (CC BY 4.0)." 63
File đính kèm:
an_enhanced_fault_tolerant_control_against_current_sensor_fa.pdf